Kategoriat
Geomachine
Adopting digital tools for ground investigation is easy with Geomachine’s guidance. You don’t need to understand the technology or speak in complex terms. All you need to know is the direction in which you want to develop your operations.
“In the ground investigation industry, things have been done the same way for years, using familiar methods,” says Pasi Majakangas, who designs digital services for Geomachine. “Learning something new alongside your regular work can seem like a burden, so often, people prefer to stick with familiar practices. But what if embracing new solutions was made easy, and it turned out to be a smart and effortless investment from a business development perspective?”
Two ways to adopt
The core of Geomachine’s digital product family, the GMTracker data-logger, is automatically included with the purchase of a new machine. The data-logger can also be added to a machine already in use on-site.
Since digital tools are still relatively new in the ground investigation industry, discussions about their adoption are always led by the customer’s workflows, challenges, and needs, rather than product features. “Some of our customers know exactly what smart features they want from their new machine, and these are added to their GMTracker during the machine’s production phase. Other times, the customer might not have a clear vision of the best solutions for their specific operations. In those cases, we ask the right questions and determine the goals they have for the machine and their business development.”
The customer may also have identified pain points in their operations that they need solutions for. “If the areas that need improvement are already known, we focus on how our digital tools can help resolve these issues. If the goal is simply to get more out of their machines and processes, we’ll explain what’s possible with our digital services.”
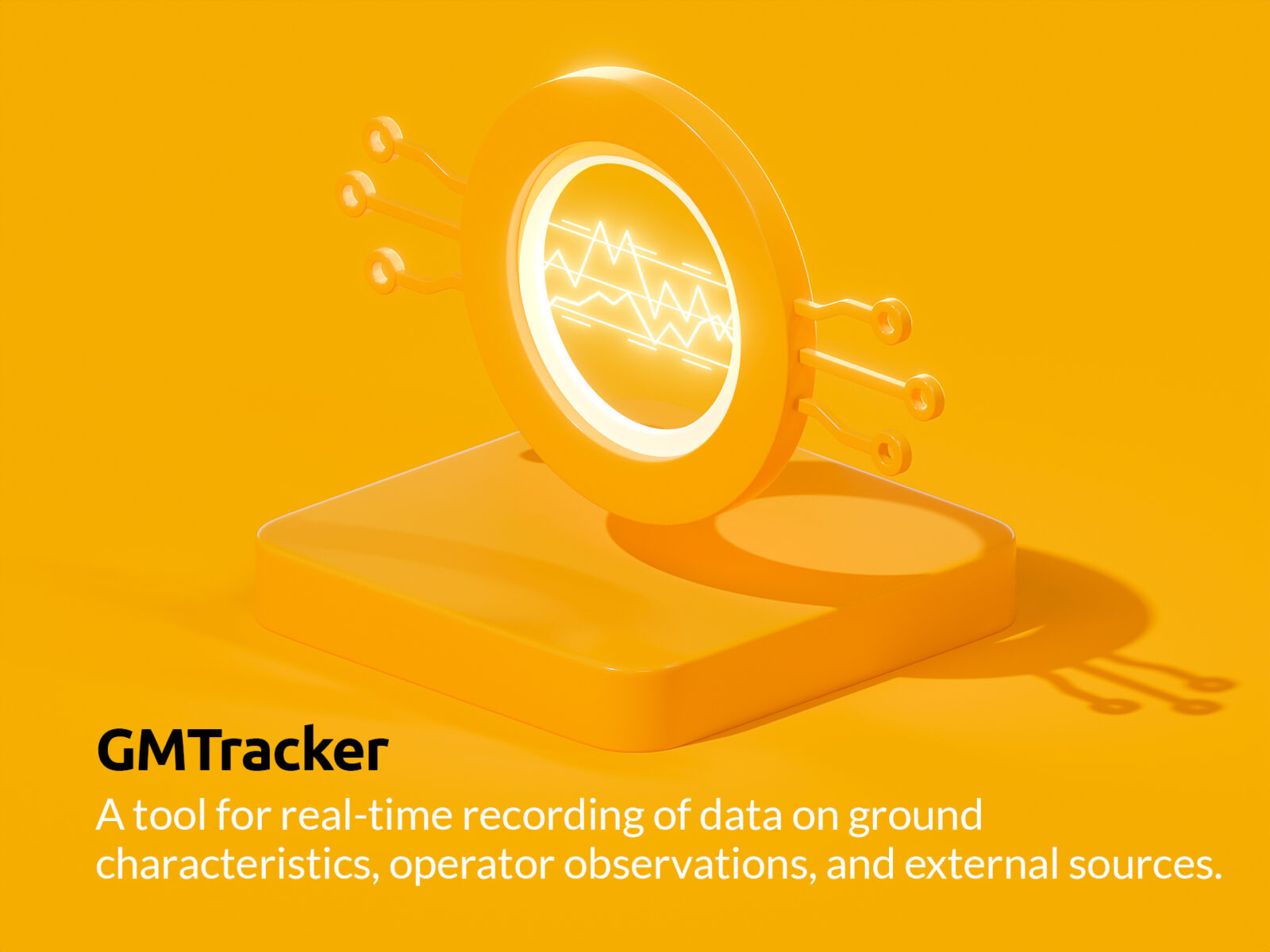
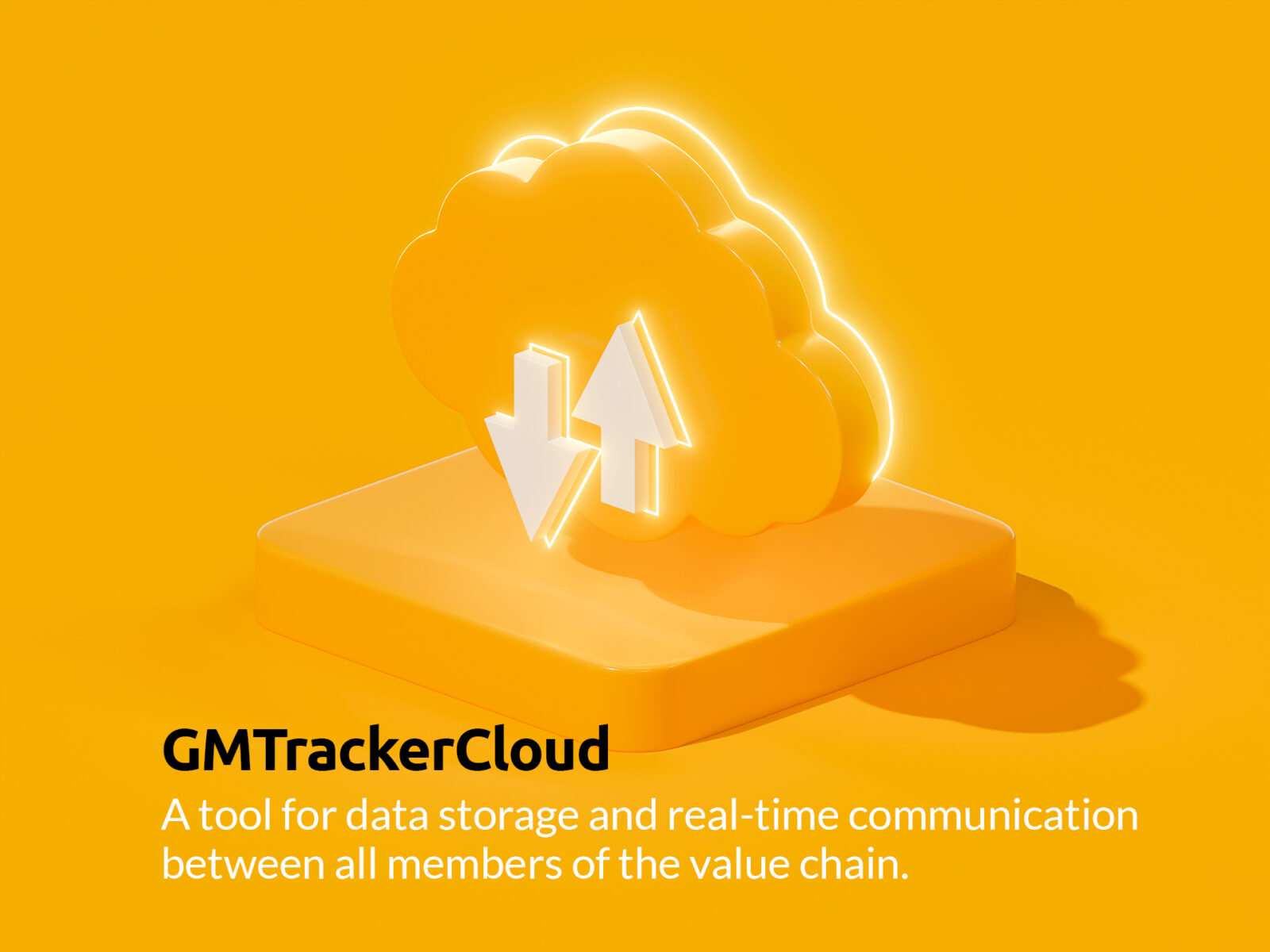
Real-life examples
Pasi Majakangas shares that one issue may be long downtime due to maintenance queues, leading to slow and unprofitable project completion. “In such cases, we suggest adopting GMCare. It opens a two-way connection between the operator, machine maintenance manager, and service partner. The software gives the service partner a real-time view of the equipment’s condition, enabling preventive actions to reduce machine failures. GMCare also digitizes and standardizes maintenance documentation, storing it centrally in one place. The software uses machine learning to continuously build a knowledge base, making future machine maintenance more individualized and predictive.”
Another issue might be keeping the machine documentation up to date. “In that case, we suggest using GMFleet. This ensures all relevant equipment information is always available in real-time and kept up to date. GMFleet contains all the information related to the machine, including technical documentation and lifecycle data. It also provides easy access to information about the machine’s technical capabilities.”
A customer might also struggle with communication issues that slow down project progress. “In such cases, we recommend using GMSiteOps. It streamlines project management and resource allocation, automating related tasks. It digitalizes the project manager’s workspace and integrates it into the project’s value chain. GMSiteOps improves process transparency, real-time data, quality, and safety, while helping to transform the data collected from processes into business-driving actions.”
So, how to move forward?
If you’re interested in improving your business, the right place to start the conversation is with Geomachine’s Sales Manager, Alex Lindholm. “You can email or call Alex. He will arrange a meeting with you to review your business and needs. After the meeting, you’ll receive a proposal for the digital features that can help you reach your goals. If you’re integrating digital tools into an existing machine, the software installation will typically take 1–3 working days. It’s important to consider this when planning your project schedules.”
For those buying a new machine, the process is even easier. “Digital services are always offered with a new machine purchase, allowing you to share your operational optimization goals with our sales team. When the machine leaves the factory, it will already have all the intelligence you wanted pre-programmed.”
According to Pasi Majakangas, there’s no need to fear digital services. “Our product family is easy to understand and use, and our customers who already use the tools agree. If you want to boost your productivity and improve the quality of the data you collect, don’t hesitate to contact us. We’ll tell you which of our tools best suit your needs and how to get them up and running quickly.”
Interested? Contact Geomachine!
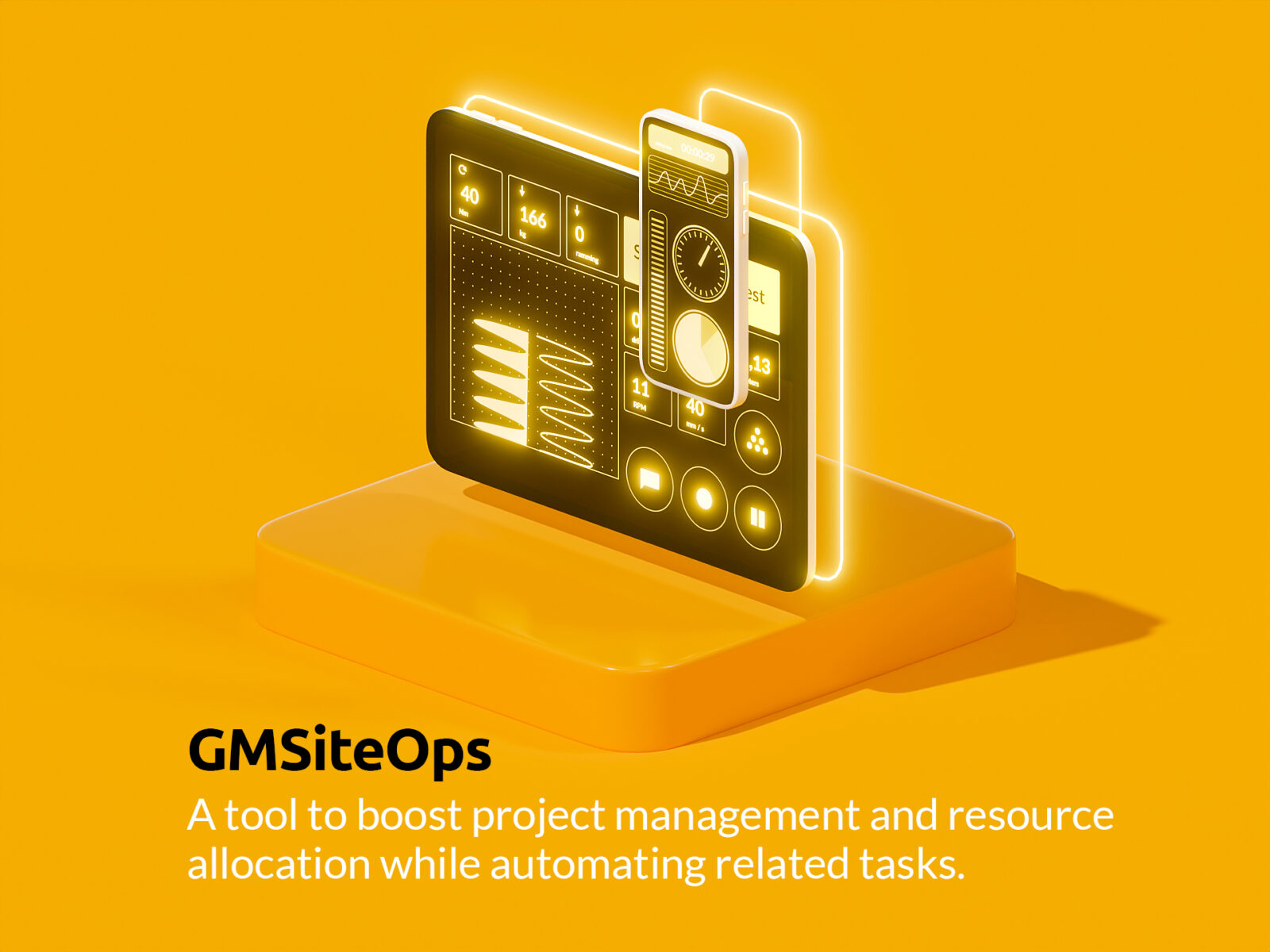
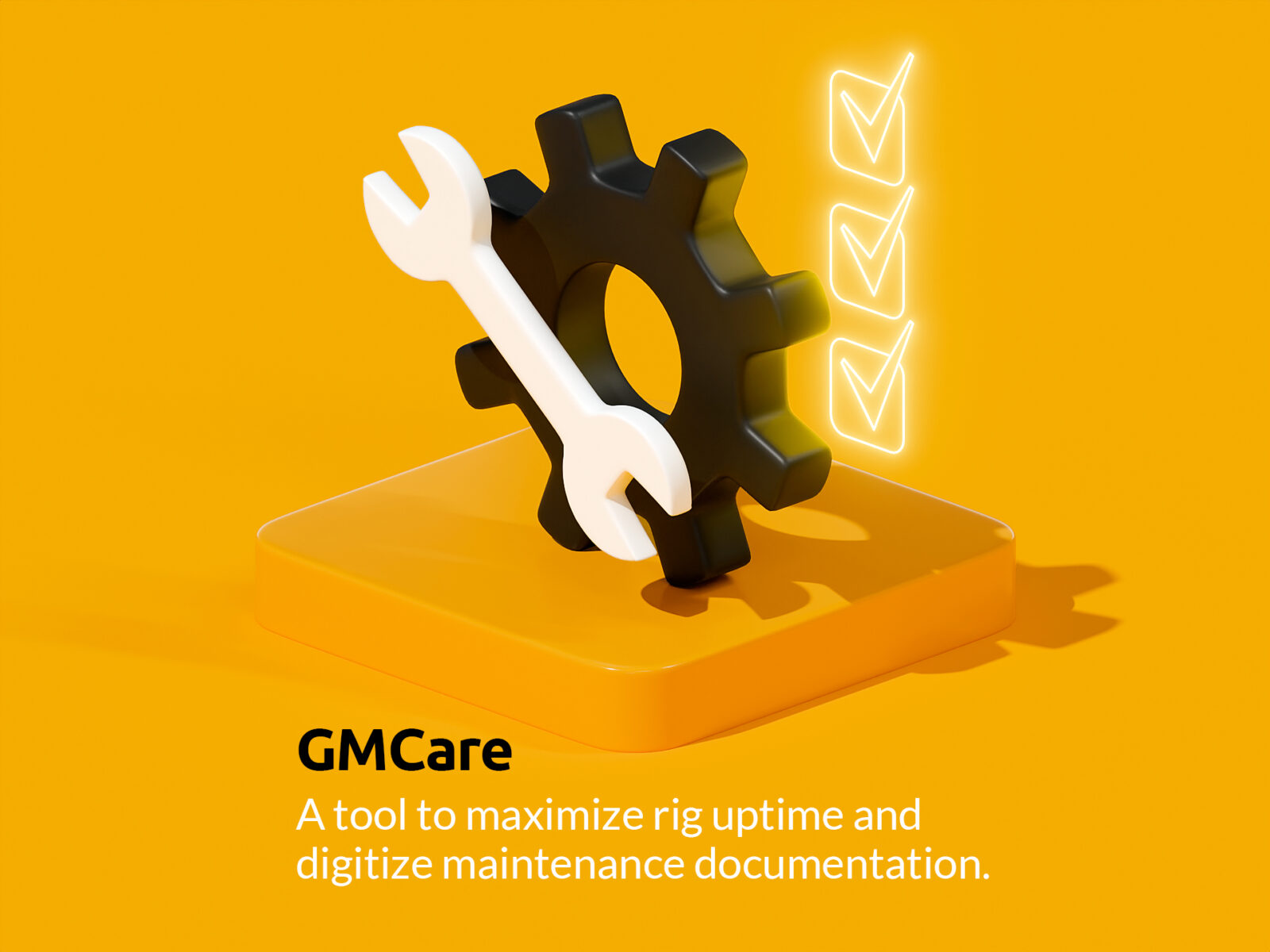
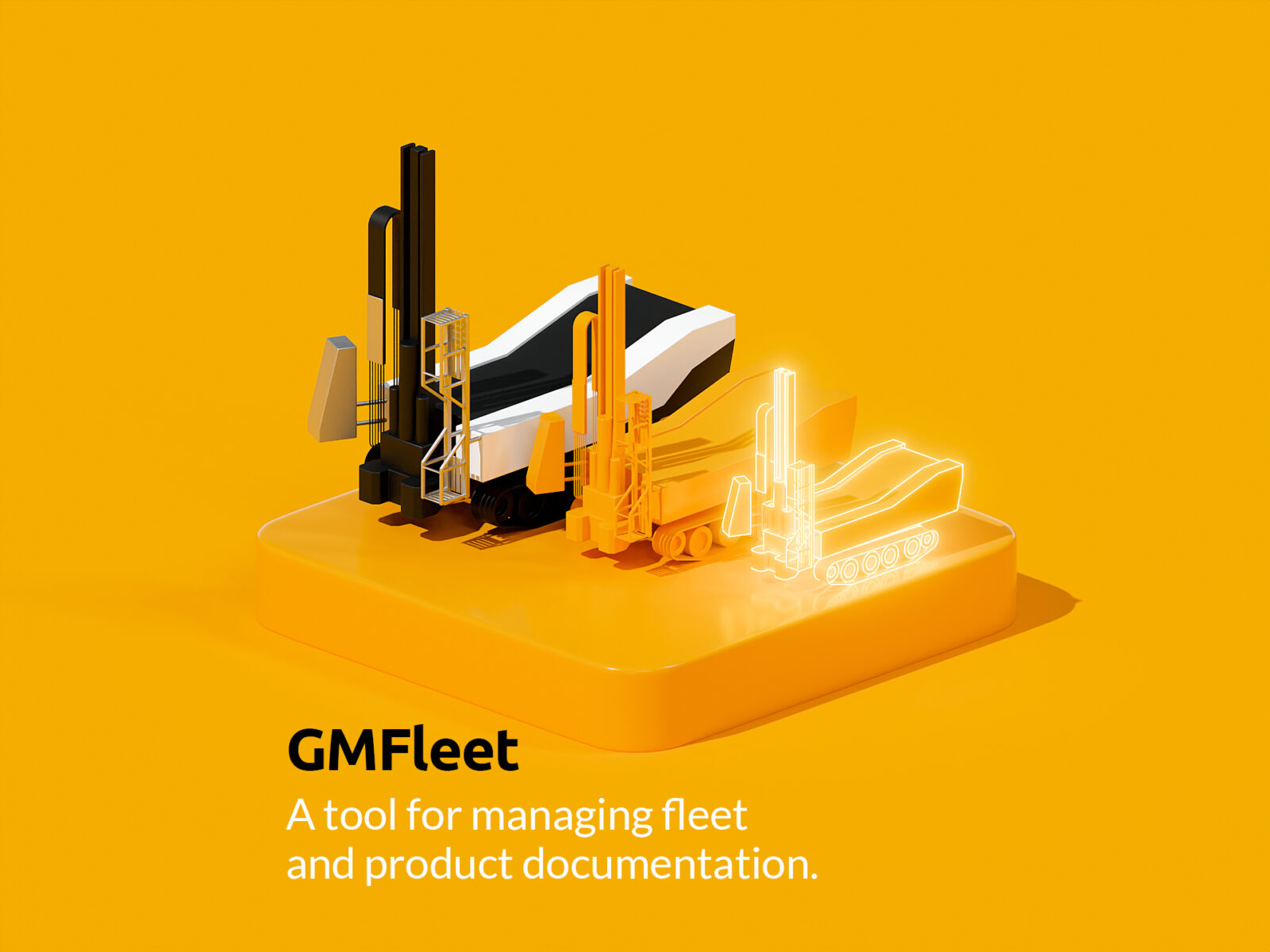
Geomachine
Geomachine aims to make ground investigation as efficient, profitable, and high-quality as possible. That’s why it develops cutting-edge digital innovations that will lead the industry into a new and smarter era.
Continuous development is deeply embedded in Geomachine’s DNA. In recent years, the company has focused particularly on digital innovations in its product development to enable companies in the ground investigation industry to conduct their business more intelligently and profitably.
“In the ground investigation industry, traditional methods have often been used, resulting in many manual workflows and fragmentation in the value chain,” says Pasi Majakangas, who designs digital services for Geomachine. “Four years ago, we initiated the development process for digital products with the aim of tackling these challenges.”
Geomachine’s digital product family currently includes four innovative tools. “The heart of our product family is the GMTracker data-logger. It is an extremely smart tool that provides full visibility into the investigation processes and gives an overview of the performance of the equipment used. In its StandAlone version, GMTracker works locally as an operator tool, and in its Cloud version, it creates a real-time, two-way connection between all project stakeholders. The Cloud version can also be extended with modules such as GMCare, which enhances machine maintenance and servicing, GMSiteOps for optimizing project management and planning, and GMFleet, the equipment registry.”
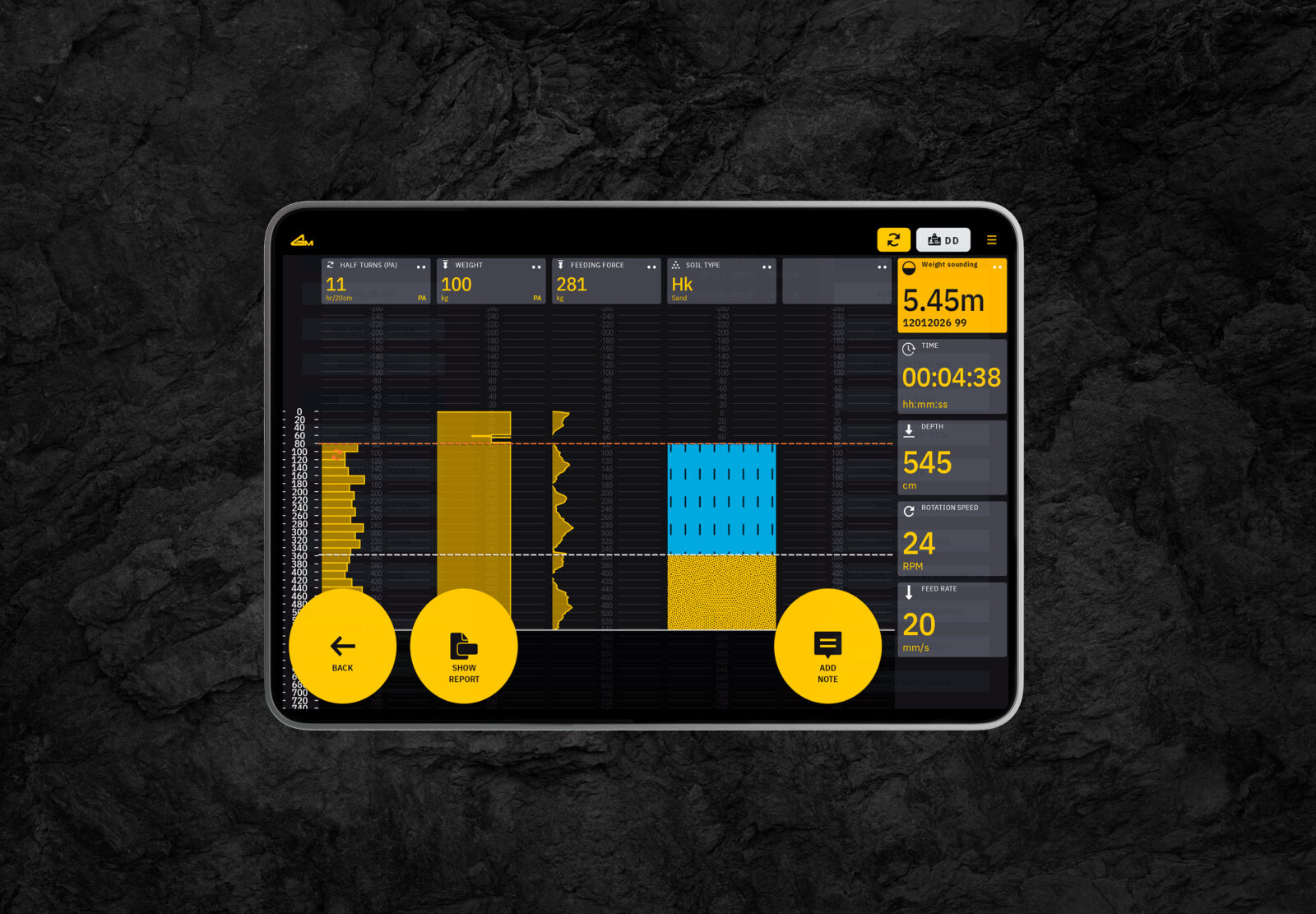
Step by step forward
As with all of Geomachine’s product development projects, the planning and development of the digital product family involved strong customer collaboration. “In the development of the GMTracker data-logger, we received invaluable support and insights from our long-time customer, Aluetaito Oy. They were involved in the project from the very beginning, and through iterative work, we developed the data-logger to the point where it could be launched to the market.”
The first version of the GMTracker data-logger was made for research methods used in Finland, and later versions were developed for Sweden and Norway. “From a product development perspective, the initial challenge was that there was considerable variation in the needs and practices of companies in the ground investigation industry. A single software solution for everyone was not an option at that point, so the product had to be configured individually for each customer’s specific needs. We focused heavily on customization in our product development. Today, customizing GMTrackerCloud to meet the unique needs of customers can be done with just a few clicks.”
Once the first version of GMTracker and its project management features were up and running, the product development moved forward. “In the next phase, we began considering solutions to enhance machine maintenance and servicing and improve equipment management transparency. These challenges were addressed with the development of the GMCare and GMFleet tools.”
Toolbox expands as needed
According to Pasi Majakangas, no other digital product family like Geomachine’s is currently available on the market. “Until now, individual tools could be purchased from various providers. However, this has resulted in customers having to manage a system architecture that could become messy and difficult to handle. Each program had to be learned separately, and integrating them could require a lot of effort. Managing the whole is now much smarter and easier when all the essential tools can be obtained from one provider.”
One of the strengths of Geomachine’s digital product family is its scalability. “Our products adapt to the needs of the user. You don’t have to purchase the entire extensive toolbox at once; it can be expanded as needed.”
Once all the innovative features of GMTrackerCloud are activated, it provides solutions for the efficient and data-driven execution of the key tasks in ground investigation projects. The transparency of supply chains immediately increases project efficiency, reduces equipment downtime, improves fleet management, and reduces the amount of manual, unnecessary work. In the long term, projects become more productive continuously, as machine learning makes maintenance and servicing operations more predictive. Data on operations and equipment performance constantly increases, helping to make the overall operation more profitable over time.
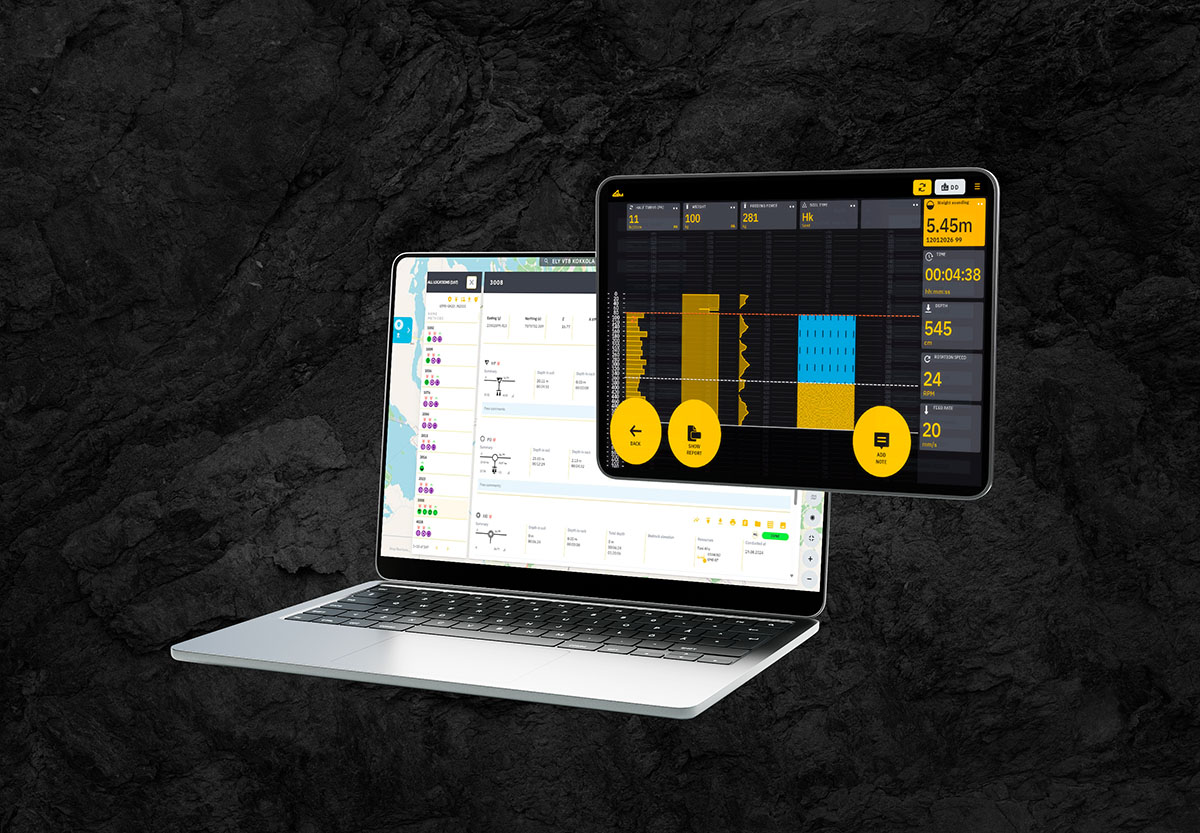
Continuously smarter and more versatile
Pasi Majakangas says that the development of the digital product family is still ongoing. “In the future, our product family will include even more analytics and 3D visualization features. With these, for example, risk assessments and quality assurance on work sites will be done even more efficiently. The drill rig will learn to identify ground characteristics and automatically suggest them to the driller. Additionally, it will take care of its own maintenance and identify its own issues. This way, maintenance can be performed as soon as the machine starts to show signs of failure, even before an actual breakdown occurs.”
Geomachine’s digital tools are currently in use by leading companies in the ground investigation industry in Finland, Sweden, Norway, and Iceland. “Every ground investigation company that understands that project productivity requires transparency across the value chain can benefit from our innovations. We want to enable our customers to focus on the right things. Do more with less – that’s what we want to offer our customers in a nutshell.”
Interested? Contact Geomachine!
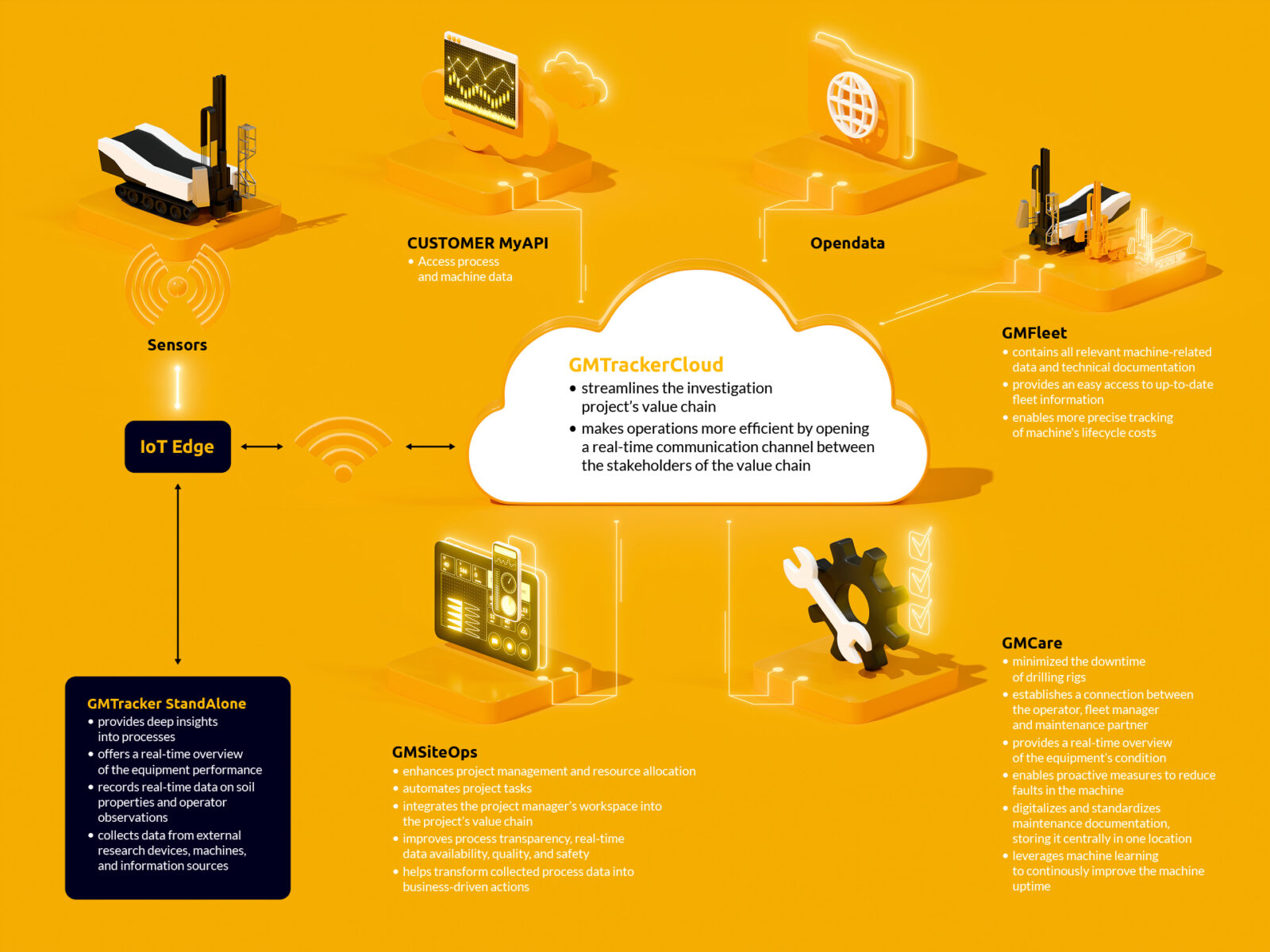
GMTracker
Information about the geotechnical field equipment used in ground investigations must be documented in the investigation report. Thanks to a new feature in the GMTracker data-logger, data on equipment is now transferred to the investigation report without manual effort.
The equipment required for ground investigations include, for example, CPT cones, vane shear devices, and sampling tools. These details must also be recorded in the work report for the investigation.
The new feature added to the GMTracker data-logger enables the maintenance and automatic adding of equipment data in work reports. The equipment registry contains information on the device’s identifier, model, type, and calibration, depending on the device. GMTracker is the only data-logger on the market whose registry also includes sampling tubes. Thanks to this new feature, equipment data is always accurately recorded in reports.
In the future, equipment management will also be integrated into the Cloud version of the GMTracker data-logger. Once data can be stored in the cloud, all stakeholders requiring equipment information will gain a comprehensive view of the devices used by the investigation company, their age, condition, and calibration status.
Managing specialized equipment through GMTrackerCloud will not only enhance reporting but also streamline the execution of investigation projects. It will help project management allocate sampling tasks to specific investigation vehicles without needing to transfer equipment from other sites. In the future, calibration values for equipment will also be manageable via GMTrackerCloud.
Interested? Take contact!
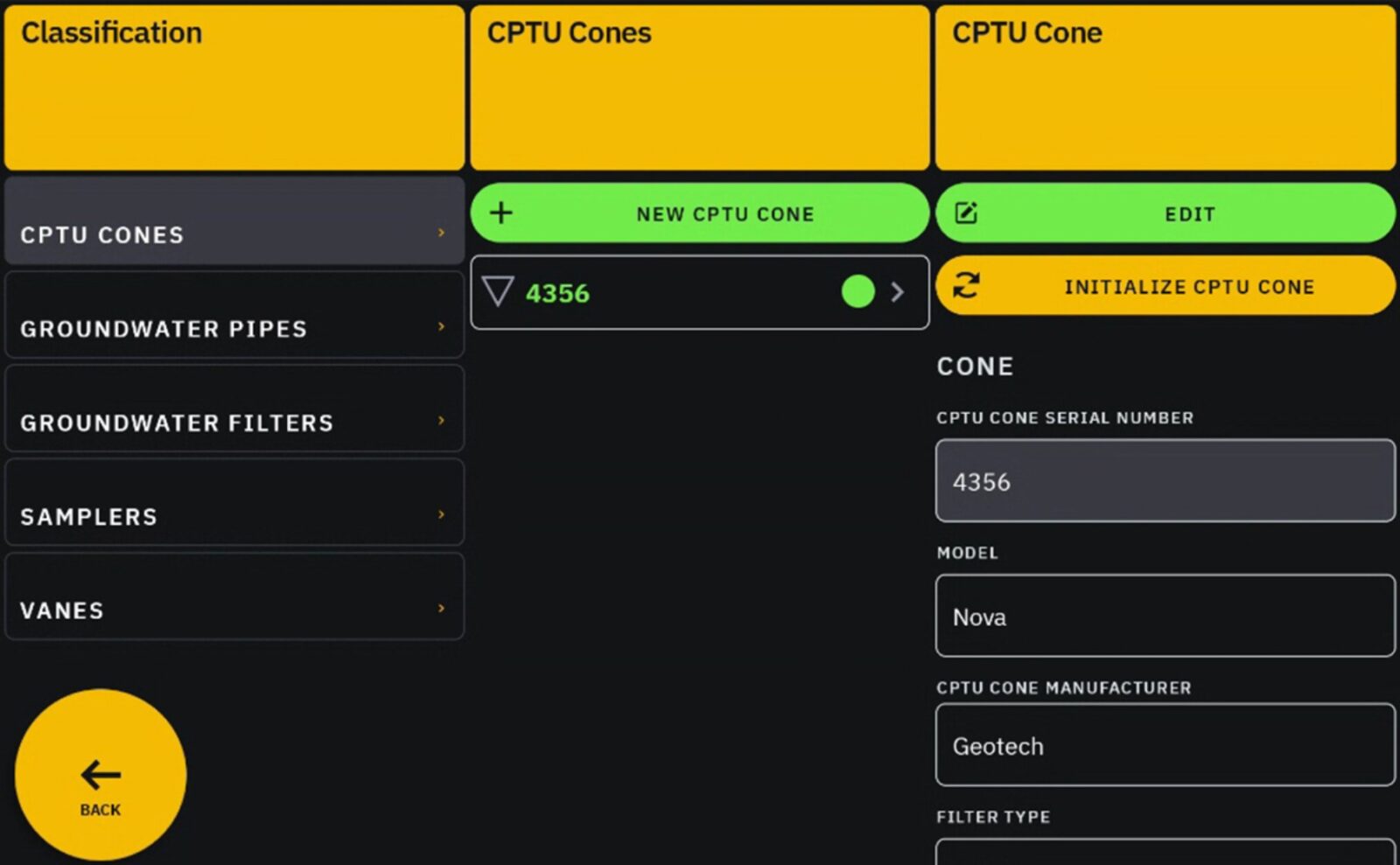
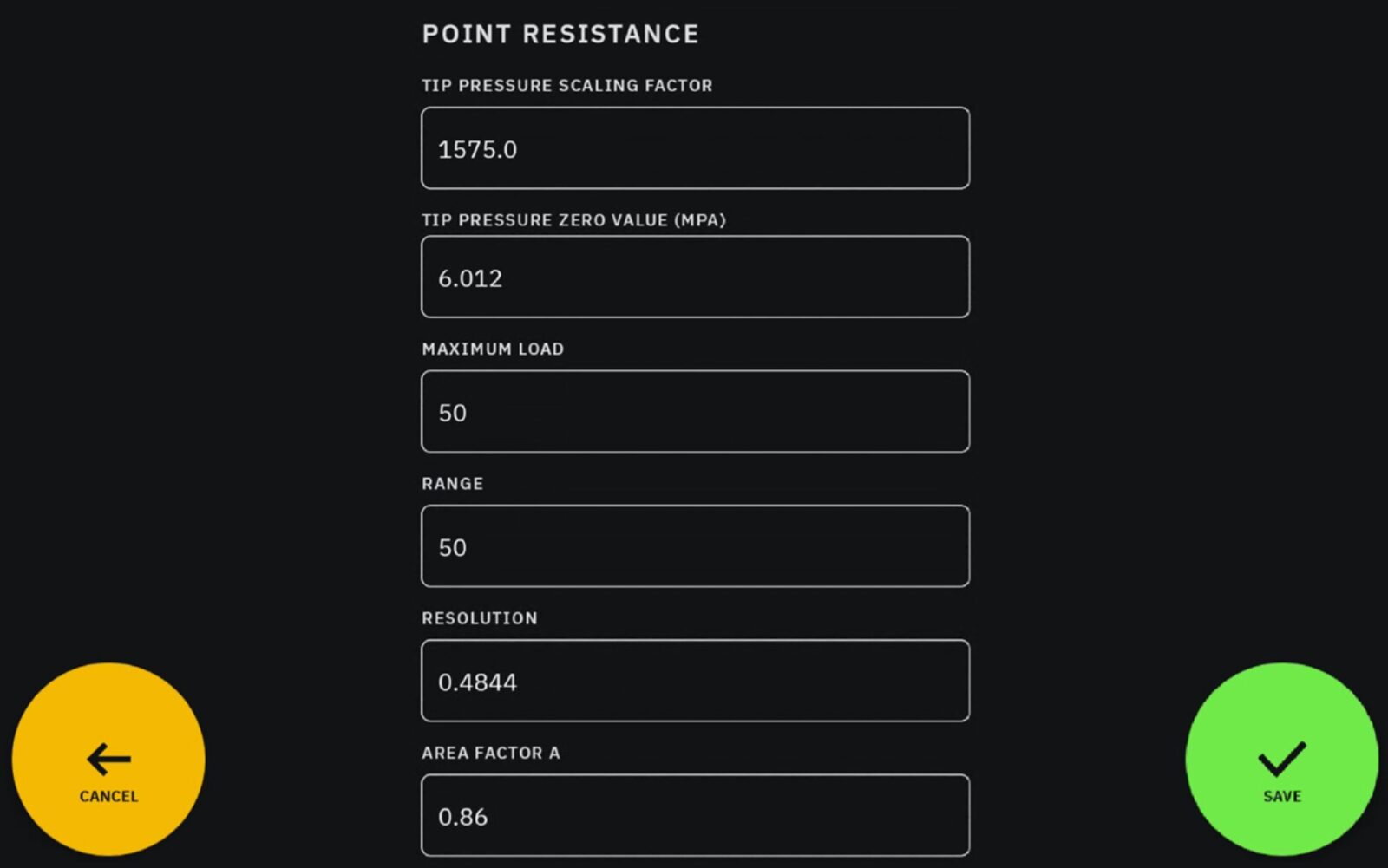
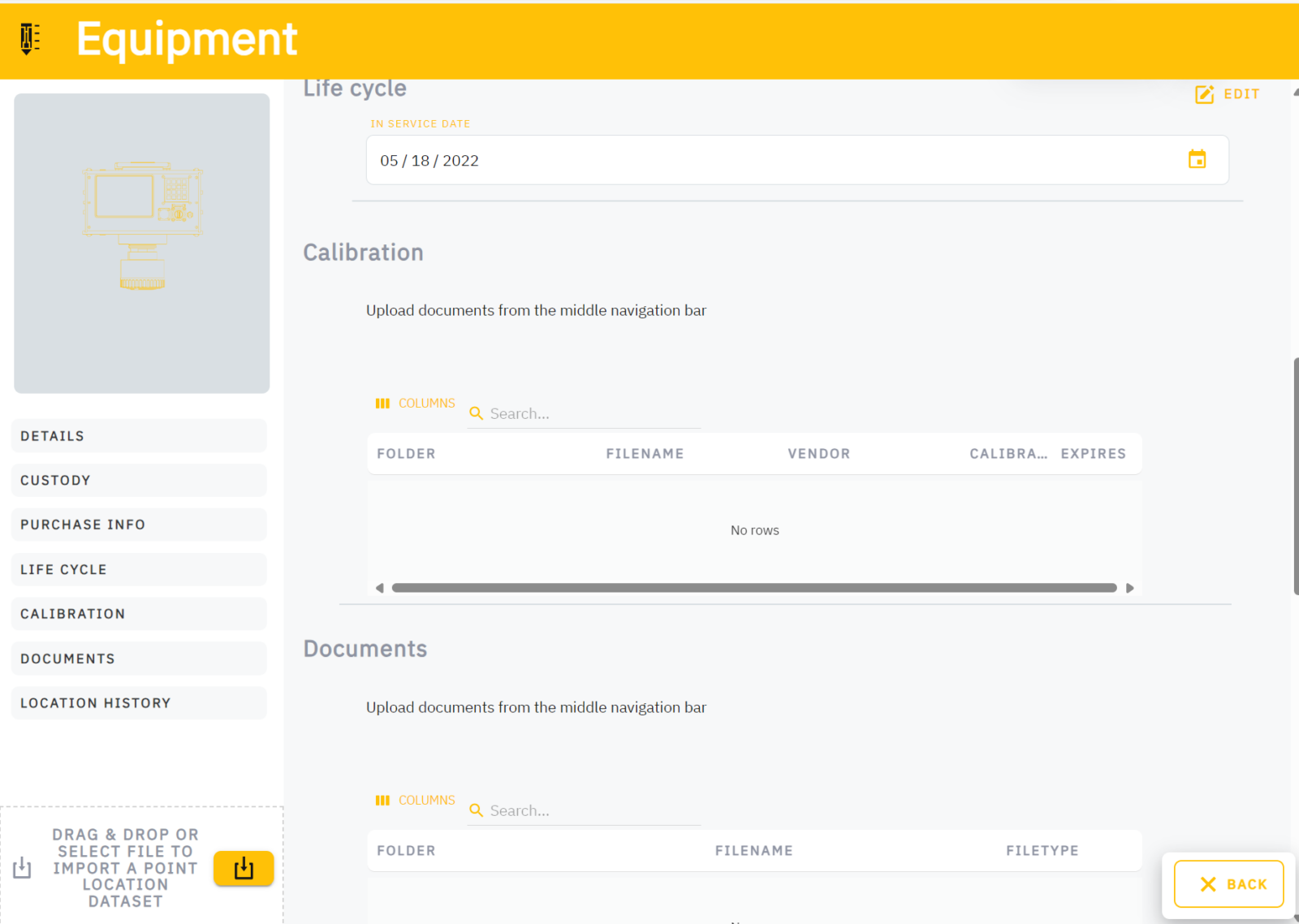
GMTracker
A new intelligent feature has been added to the GMTracker data-logger’s Cloud-version. The digital safety inspection streamlines the process of ensuring occupational safety measures are met, making it easier to comply with safety and quality requirements.
Before starting a soil investigation or well-drilling work, a commissioning inspection must be performed on the drilling rig at the site. For longer-term projects, daily or weekly inspections are also required. The GMTracker data-logger now serves as a tool to efficiently carry out these procedures as well.
Thanks to the new feature in the GMTracker data-logger, the safety inspection process can now be conducted in a standardized, digital format, eliminating time-consuming paperwork. The Cloud version of the data-logger enables real-time reporting of inspection results and any detected discrepancies to all relevant stakeholders. This feature ensures that the inspection history of the equipment, including records of any failed inspection tasks, is securely stored. Inspection task lists are fully customizable to meet user needs.
By digitizing site inspections, Geomachine emphasizes that working safety is just as important as its efficiency, quality, and environmental sustainability. This feature aims to familiarize operators with safe work practices and integrate risk assessment into routine operations. It also ensures that information about working conditions and the safe operational status of machines is always accessible to external inspectors, such as authorities, when required.
International standards ISO9001 and ISO14001 require Geomachine to operate in accordance with the highest quality standards. However, our aim is not only to meet these requirements but also to exceed them whenever possible. Adding the digital safety inspection feature to the GMTracker data-logger is one example of this commitment.
Interested? Contact us!
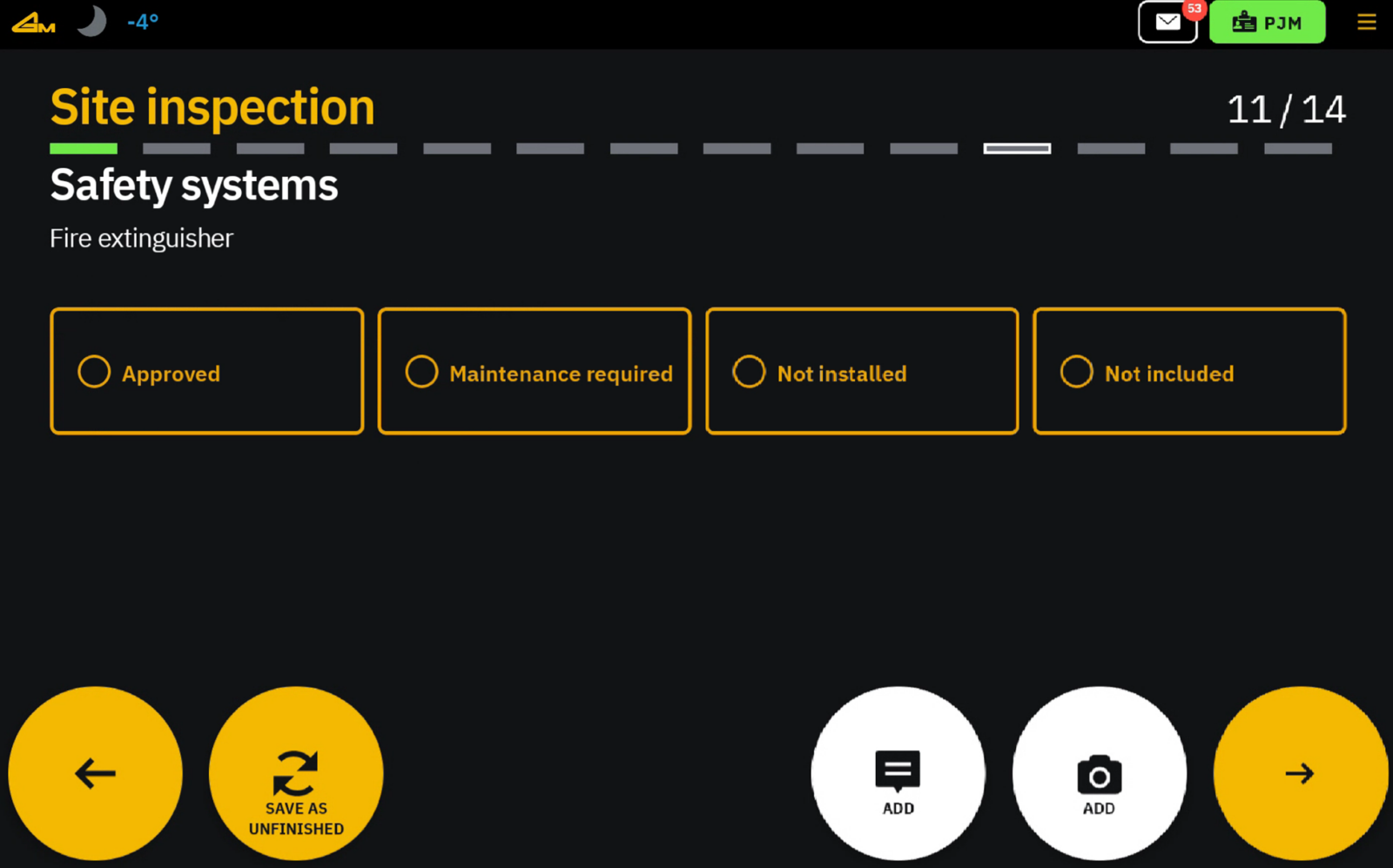
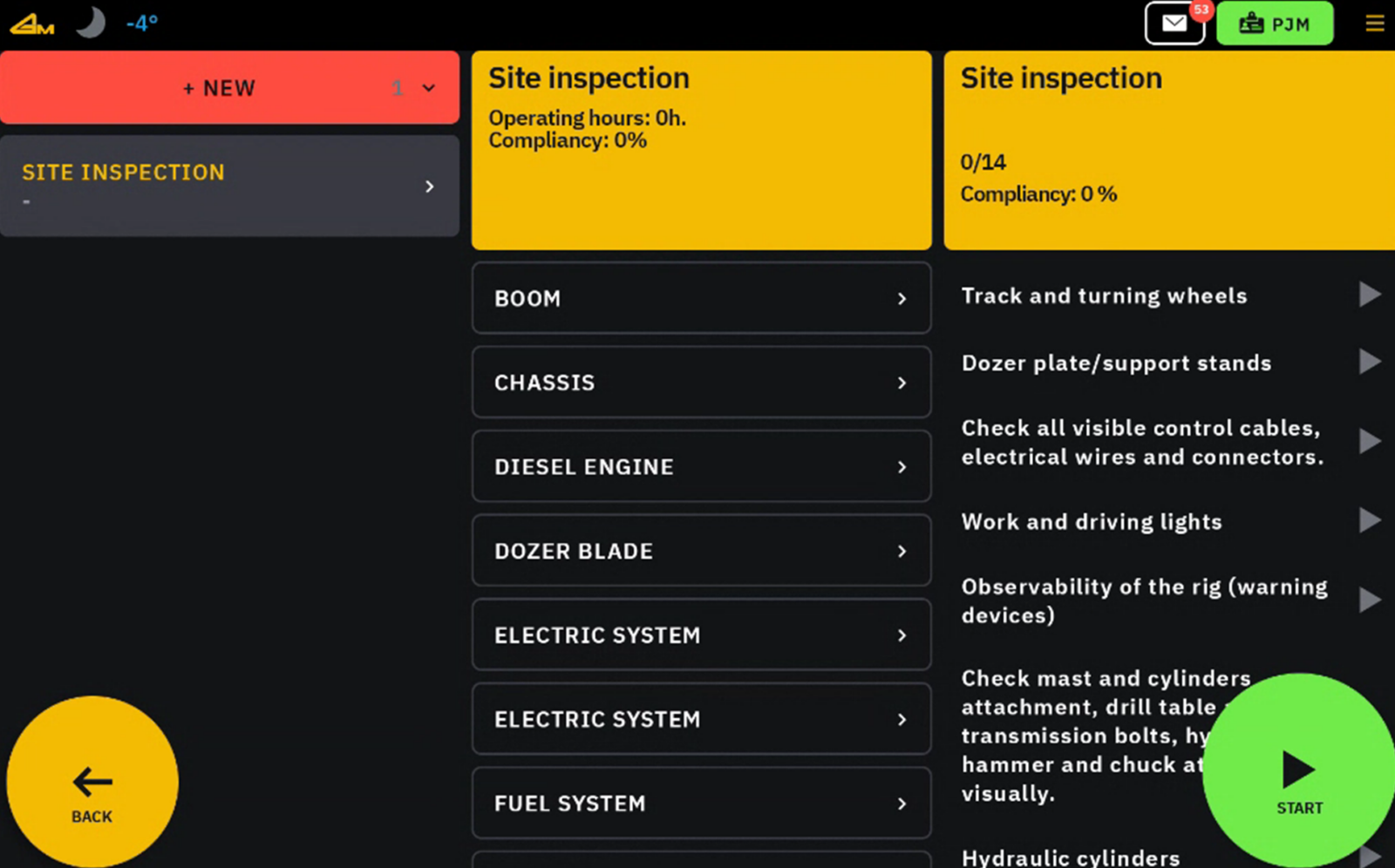
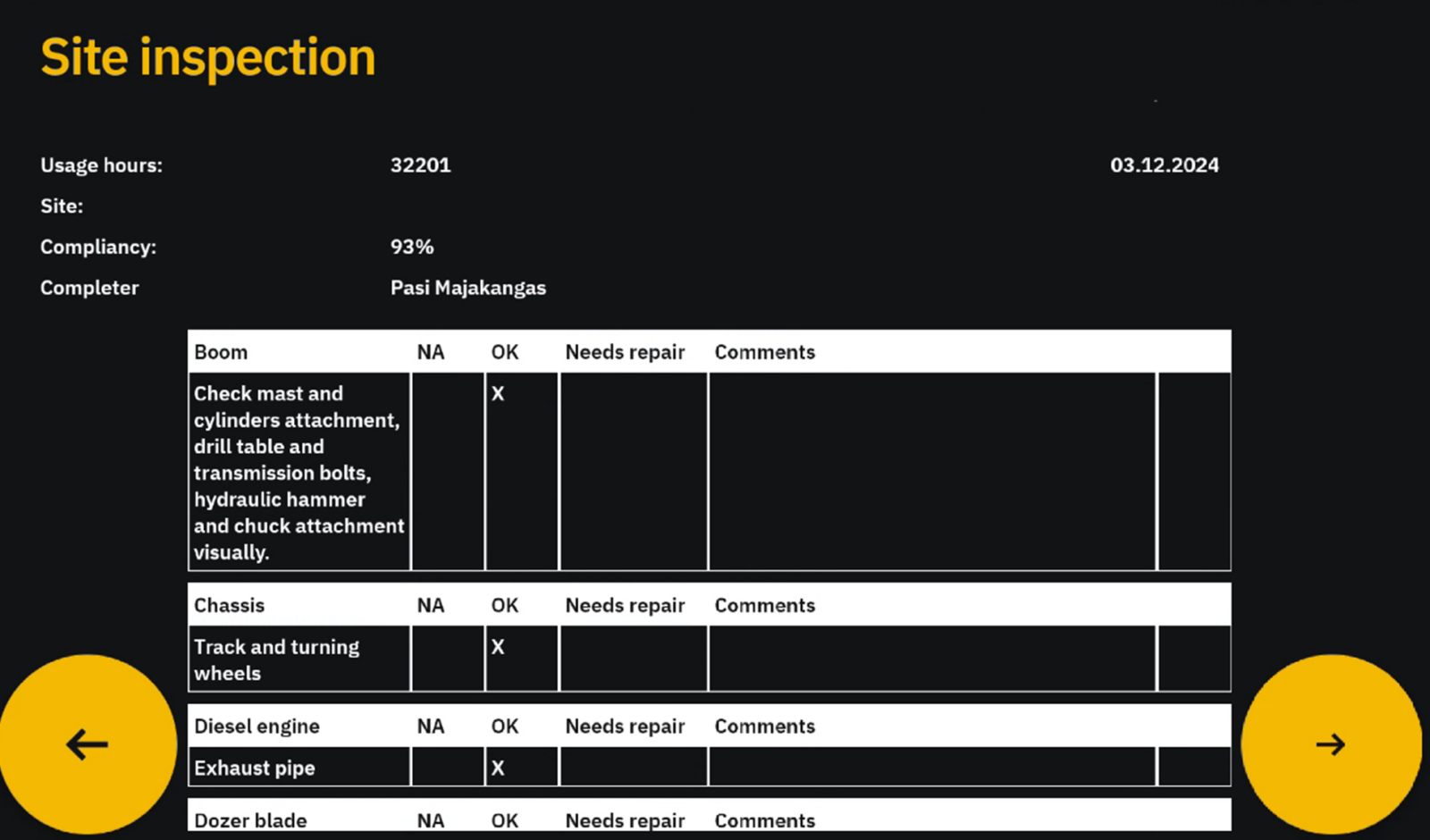
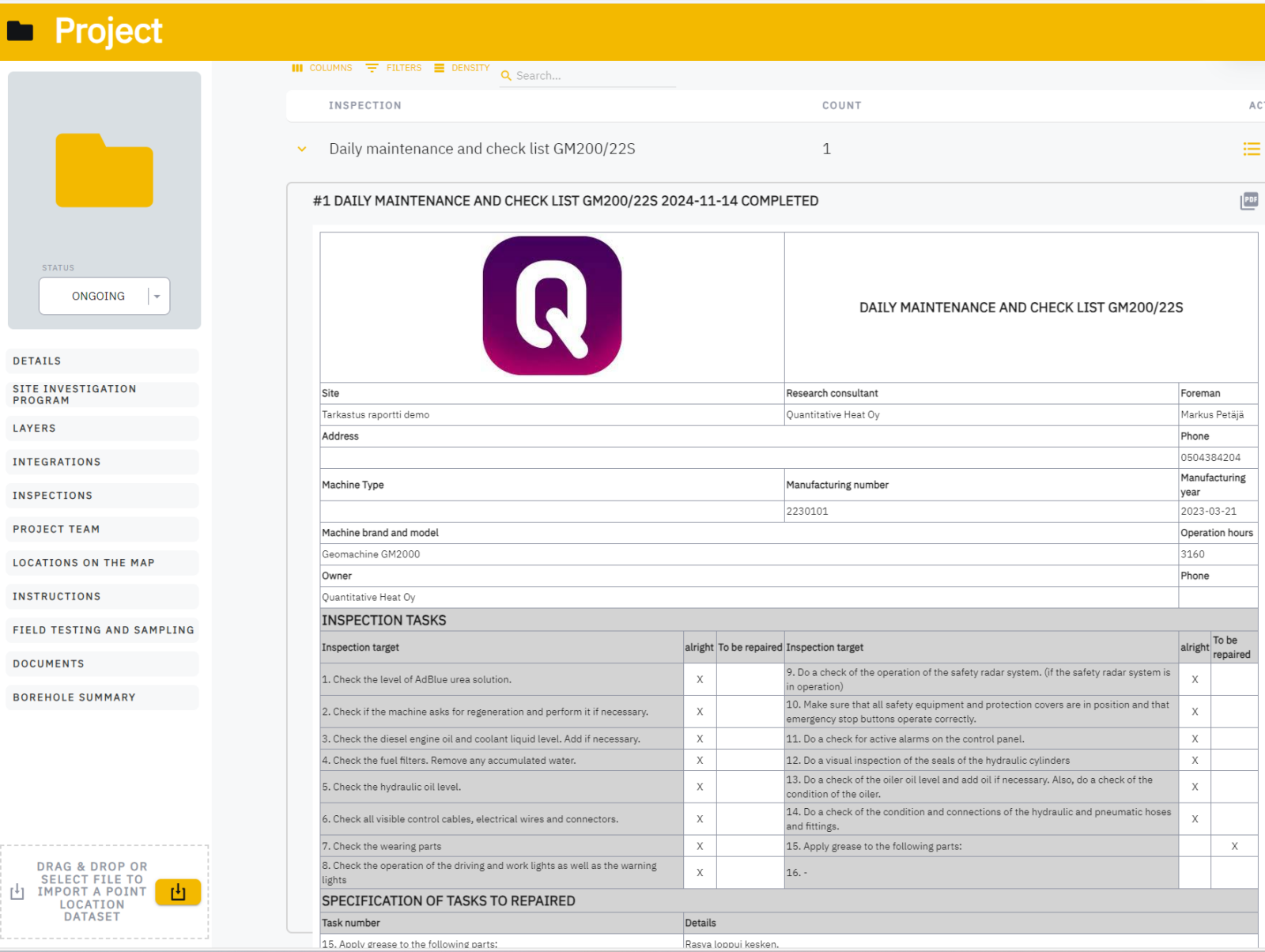
GMTracker
Weather conditions can impact the results of geotechnical investigations, which is why they are documented in the project’s work report. Geomachine has enhanced its GMTracker data-logger with a new feature that records weather data during investigations, allowing this information to be easily integrated into reports.
Geomachine’s GMTracker data-logger is now smarter than ever, thanks to its new weather-tracking feature. This functionality significantly streamlines the work of project managers, as weather information can now be directly copied into the report from geotechnical investigation data. This means that there’s no need to retrieve it separately from a weather service during the report preparation phase anymore.
Using this feature in the GMTracker is straightforward. With the device’s location tracking enabled, the data-logger automatically fetches weather data from a weather service and includes it in the investigation report. Recorded data includes temperature, dew point, precipitation, and wind speed during the investigation.
Geomachine’s GMTracker is currently the only geotechnical data-logger on the market equipped with a weather tracking feature.
Interested? Get in touch!
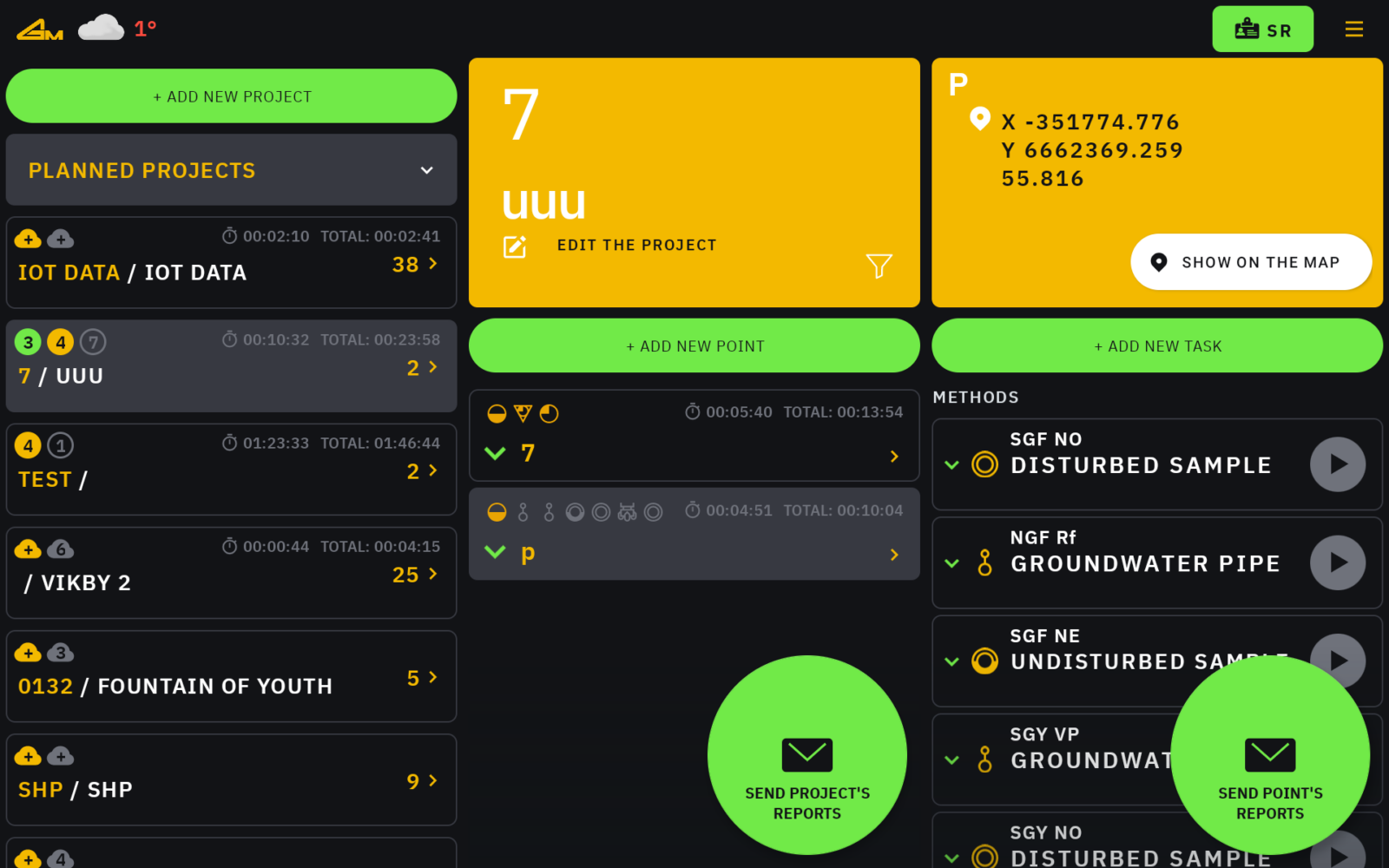
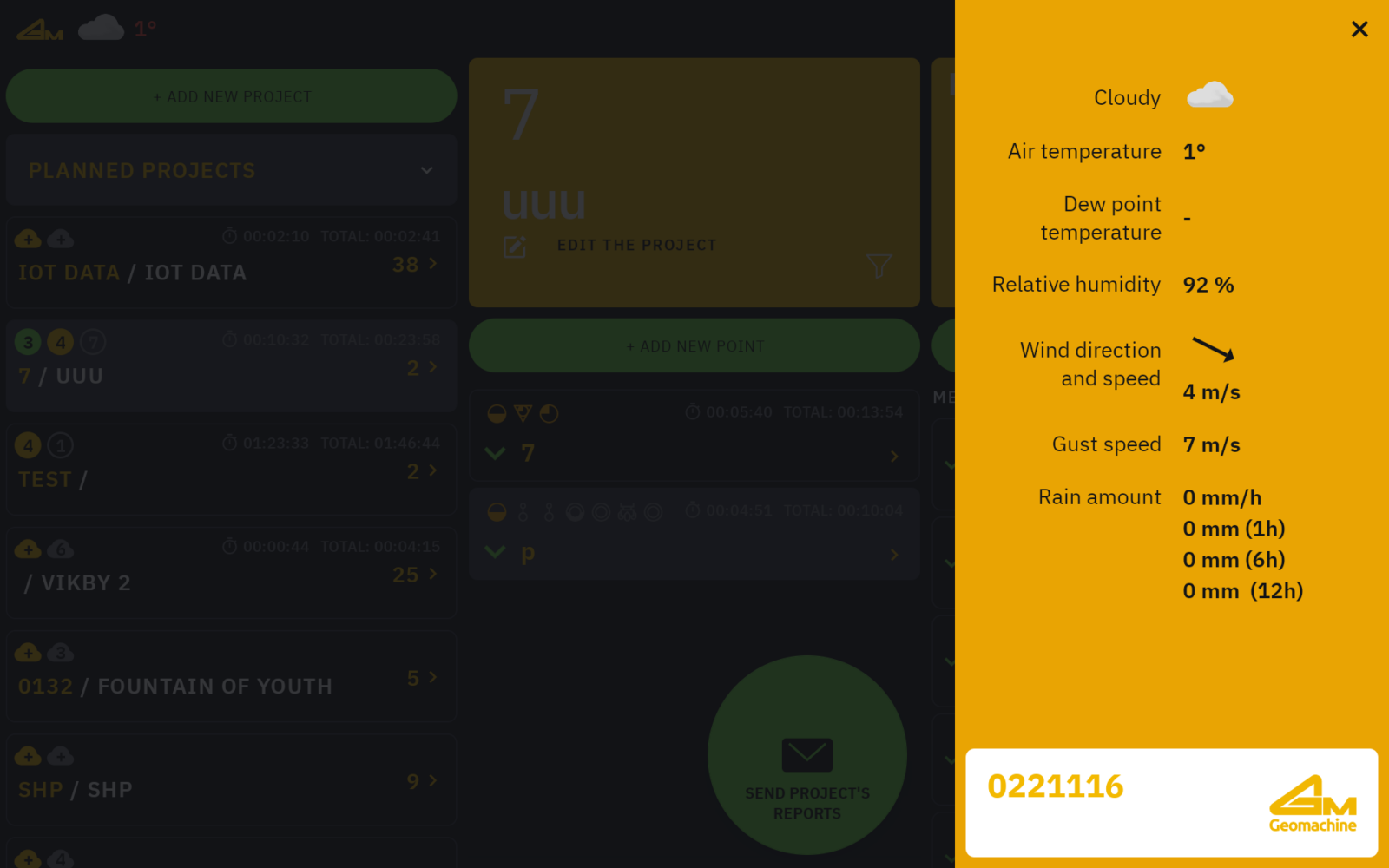
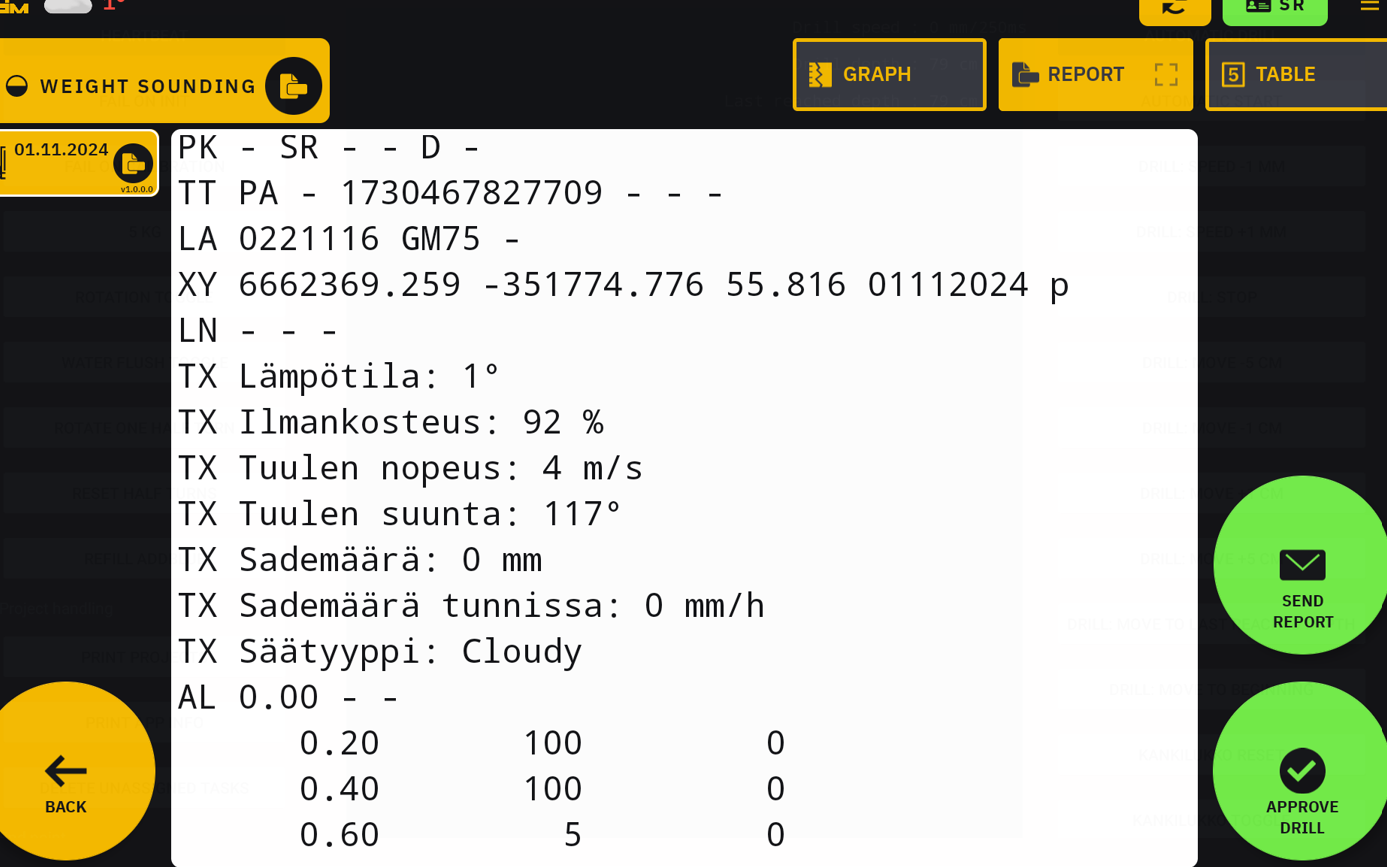
Vegagerðin
Vegagerðin is an Icelandic state-owned company responsible for managing the country’s roads and infrastructure. The company has recently adopted Geomachine’s GMTrackerCloud service, which enables it to conduct geotechnical investigations in the most intelligent way possible.
Thanks to the GMTrackerCloud service, geotechnical projects can now be carried out more efficiently. The service enables the data-logging, storage, processing, and real-time availability of data for all members of the value chain. “GMTrackerCloud makes the data supply chain smarter,” says Pasi Majakangas, Head of Digital Products at Geomachine. “It reduces the amount of manual work, and the data is always effortlessly accessible to everyone who needs it.”
According to Sverrir Sverrisson, Project Manager at Vegagerðin, GMTrackerCloud is now used by all stakeholders involved in geotechnical projects in Iceland. “Geotechnical engineers upload their drilling plans to Geomachine’s cloud and allocate tasks to the drilling rigs. The field investigator performs the investigations as requested and uploads the data to the cloud service. Geotechnical engineers receive the data in real time from the cloud and can utilize it in their work without delay.”
The activation of the GMTrackerCloud service also eases the workload of field investigators in other ways. “We have implemented a Bluetooth-enabled CPTu solution. This allows the transfer of investigation data wirelessly from the CPTu probe to the GMTracker data-logger. Additionally, we use DGPS positioning, which ensures that the precise location of the investigation point is measured and also saved to the cloud in real time.”
Since Vegagerðin is the sole organization conducting geotechnical investigations in Iceland, the adoption of the GMTrackerCloud service means that the entire country’s investigations are now carried out in a more efficient, high-quality, and intelligent manner.
Interested? Contact us!

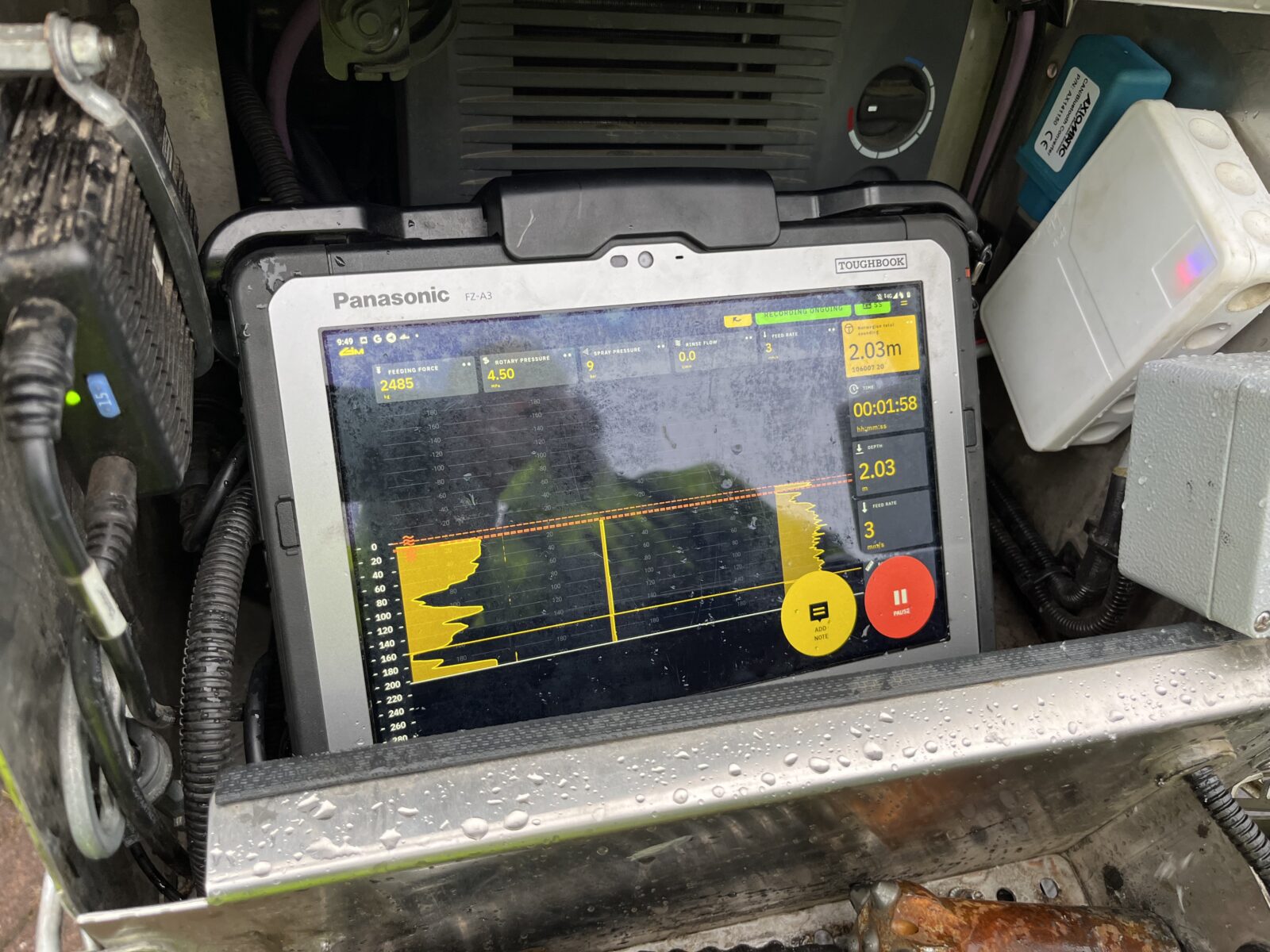
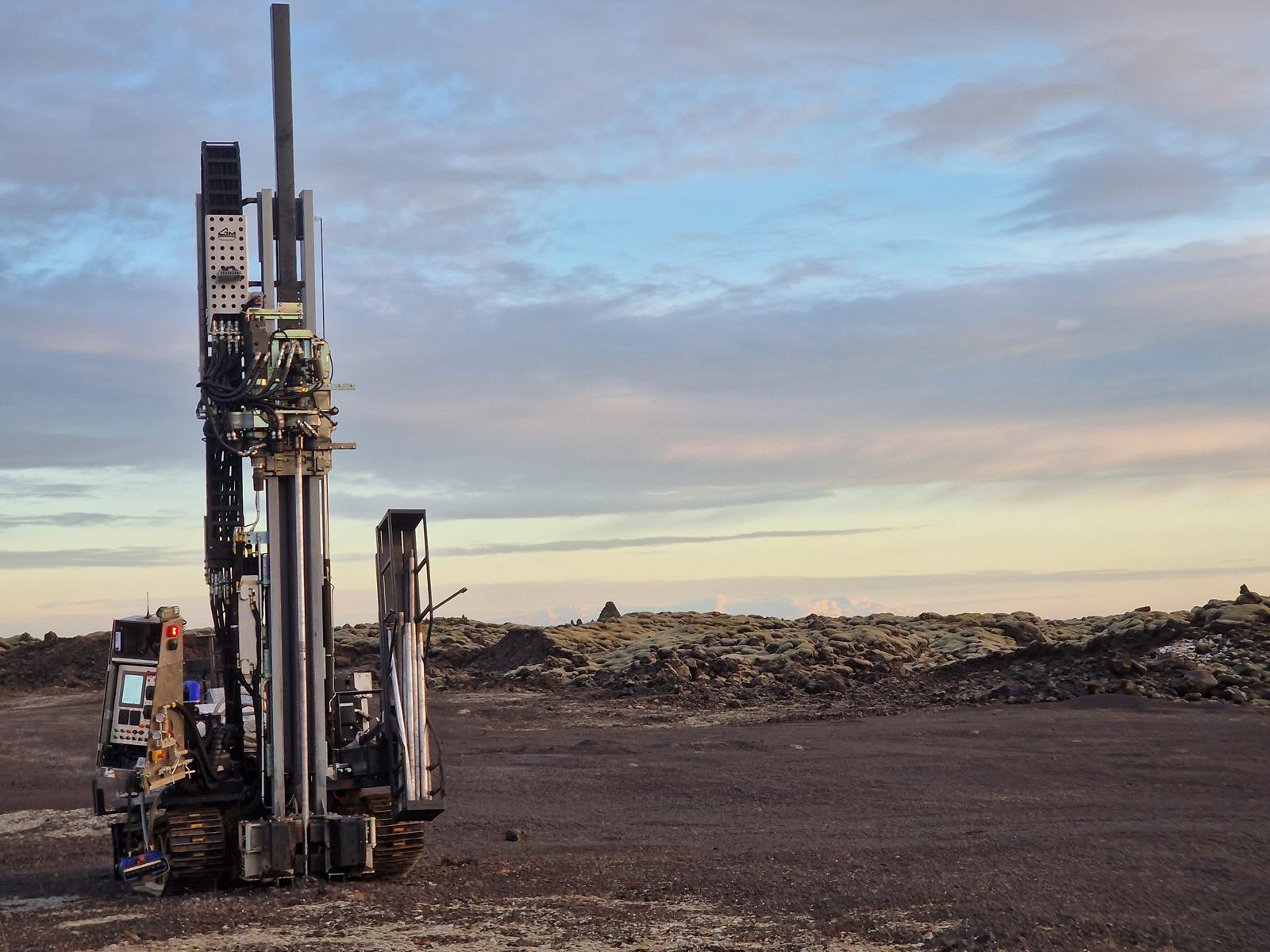
GMCare
Geomachine provides its customers with digital services to enhance the efficiency of drilling rigs. The Norwegian company Norconsult Boreteknikk AS aims to improve the utilization and potential of its fleet by implementing Geomachine’s GMCare service.
GMCare is a comprehensive tool for real-time machine analysis. It offers clearly visualized information on machine usage, productivity, safety, and operational condition. This data helps prioritize daily machine-related activities, predict maintenance needs, reduce manual work, minimize unexpected downtime, and thus maximize the productive usage of the equipment.
Norconsult Boreteknikk AS is implementing the GMCare service in all their drilling rigs regardless of the brand. The goal of adopting the service is to automate recurring maintenance processes, reduce the amount of manual maintenance work, continuously monitor the real-time operational condition of the machines, and ensure that this information always reaches the right person at the right time.
The training for using the service will be held in September, and the first user experiences will be shared in October. The GMCare service is also used by Norconsult’s maintenance partner, PTO Teknikk AS, which further streamlines the maintenance of the drilling rigs.
Interested? Contact us!
CPTu analytics
CPTu testing has been added as an investigation method to the GMTracker data-logger. This new feature makes GMTracker a perfect tool for producing high-quality data from all the most common ground investigation methods.
Geomachine has now added also CPTu testing to the GMTracker data-logger. CPTu drilling analytics is produced with Geotech Nova CPTu equipment, which works reliably in various research environments. During the investigations, the equipment provides information on, for example, tip resistance, casing friction, pore pressure, drilling angle and, as an option, also the temperature of the research environment. The real-time data transfer feature enables the driller to know what is happening below the surface at all times as the work progresses.
This additional feature makes the driller’s working day even smoother, more efficient and more productive, as all investigation methods can now be conveniently analyzed with the same data-logger.
Interested? Contact us!
DGPS smart antenna
In our opinion, the product is only functional when it genuinely improves work performance. That’s why Geomachine has added a feature to its GMTracker data-logger, thanks to which the drill hole can now be precisely located with the DGPS smart antenna. This makes GMTracker an even more accurate tool for ground investigation data management.
In the ground investigation process, the consultant must add the exact level and height coordinates to the investigation data before handing it over to the next stage of the process.
This is now even easier, as integration with a smart antenna has been added to the GMTracker data-logger. The coordinates located by the antenna can be added as part of the project data already in the field, which makes the work smoother. The integration is now implemented via Bluetooth with the Novatron Xsite Rover antenna, but in the future it’s also possible with similar devices from other manufacturers.
This new feature means faster and more error-free data management for our customers, i.e. a clear added value to the ground investigation data storage process.
Interested? Contact us!
Scanreco
Geomachine is constantly developing new features for its products so that working at the investigation site can be more productive and efficient. One such is the integration between the GMTracker data-logger and the Scanreco radio remote controller.
When changing the rod, the machine operator must remember to acknowledge the change with the physical button on the side of the machine, so that the measurement of the depth of investigation works correctly.
To facilitate this function, we have now built an integration between the GMTracker, which stores the investigation data, and the Scanreco radio controller, which is used to remotely control the machine.
The integration brings added value to the ground investigation data logging process by streamlining it and reducing the risk of errors in the process. Practical work also becomes safer when the rod change can be confirmed by remote control.
Interested? Contact us!