GM2000 drilling rig in full action
25.09.2024
GM2000
The GM2000 geothermal well drilling rig has been in action at the Lounavoima Waste-to-Energy plant in Salo, Finland for quite some time now. So, it’s the perfect moment to assess how the rig has been performing on-site in real life.
“We are now in a situation where the third well, drilled with the GM2000 rig, is completed at a depth of 2000 meters,” says QHeat operator Hannu Ylitalo. “In total, there is four wells finished now, as we drilled the first one with another brand’s rig.”
Hannu Ylitalo has been involved in the Lounavoima project since the drilling of the first 2000-meter deep well began. “The first well was drilled at the Lounavoima site in 2021. It was 1600 meters deep. After that, we started using the Geomachine GM2000 rig for the drilling.”
The first one makes adjustments
The GM2000 rig is the first in the world specifically designed for drilling geothermal wells at a depth of 2000 meters. At the Lounavoima site, it was understood that pioneering this technology would require learning new skills and likely adjusting the rig to achieve optimal drilling efficiency. “I knew in advance that since this was the first machine of its model series, we as its first users, would be part of its product development process.”
Hannu Ylitalo was there when the new rig was put into operation. “I was involved in the commissioning of the GM2000 rig. Its transfer to the drilling site was easy, and setting up the booms was straightforward. At first, we made many adjustments, but gradually the drilling process started to streamline.”
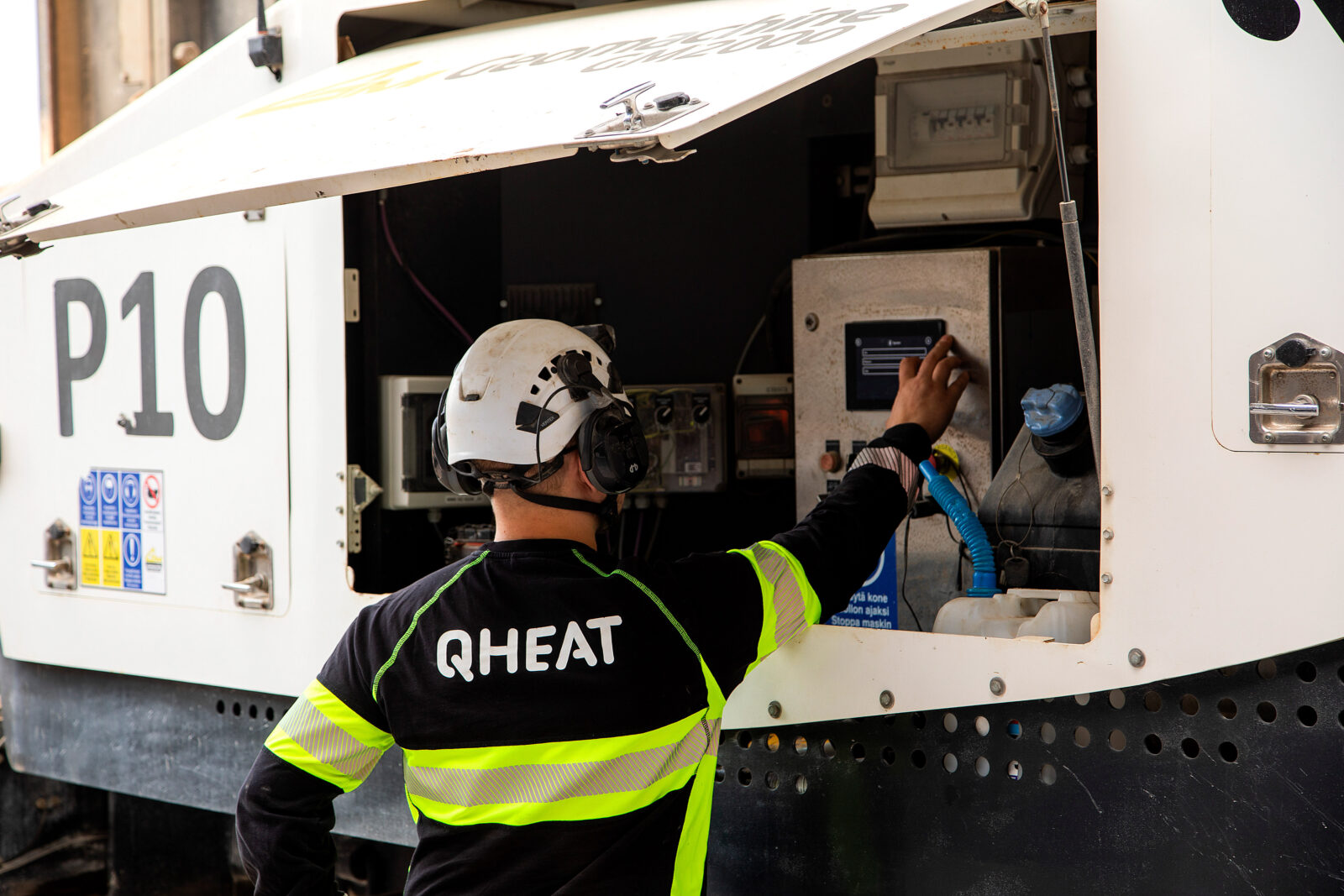
Success is a combination of many factors
The progress of the drilling process is largely dependent on what is found beneath the surface. “In our case, the bedrock is such that the rock material turns into fine powder during drilling. If water enters the well, the rock material turns into sludge and adheres to the walls of the well. When the borehole becomes narrow due to this, the air pressure in the well starts to rise, making drilling difficult without adjusting the machine. The collapse of the well walls also naturally slows down the drilling process.”
According to Hannu Ylitalo, the GM2000 rig has one feature that stands out in anticipating what happens beneath the surface. “Geomachine’s GMTracker data-logger is an invaluable tool for the driller, as it makes visible what cannot be seen with the eye and the ear cannot hear. By being aware of the bedrock conditions during drilling, regardless of the drilling depth, the machine can be adjusted in advance to suit the conditions. This way, equipment damage can be avoided, for example. Without the data-logger, drilling would be practically blind and hit-or-miss.”
Comfort and safety in work
In addition to the GMTracker, Hannu Ylitalo wants to highlight two other features of the GM2000 rig. “The remote control of the machine significantly enhances comfort and safety while working. The rig can be operated from a site cabin, which is especially nice when working in poor weather conditions. Another really good feature relates to rod handling. The opening and tightening of rod connections have been made easy with a hydraulic clamp and a sliding rod holder. The compressed air released when opening connections is directed to the back of the machine through silencers. This greatly increases the smoothness and safety of the work, as there can be up to 80 bar of pressure inside the drill rod.”
According to Hannu Ylitalo, the physical workload when drilling with the GM2000 rig has significantly decreased. “This machine is really pleasant to use. The only area where we still do some physical work is in handling the rods. However, it is known that in the future, this will also be eliminated for the operators, as an automatic rod handling system will be available for the GM2000 rig.”
Pioneering collaboration
Even though drilling at the early stages of the Lounavoima project involved a lot of new learning, working as a pioneer in a renewable energy project has been a rewarding experience for Hannu Ylitalo. “We are constantly learning new things, and it’s gratifying to see that drilling is becoming smoother all the time. Currently, the challenges that arise are related to the bedrock, not so much the drilling rig itself. And these challenges can never be completely anticipated in advance.”
The collaboration with Geomachine has been a key aspect of learning new things and streamlining the process. “It has been important that we have had the necessary support available at all times. We have received answers to our questions quickly, and through collaboration, we have gradually learned more about the drilling process, allowing us to drill wells more smoothly and with quicker turnaround times.”
Interested? Contact Geomachine!
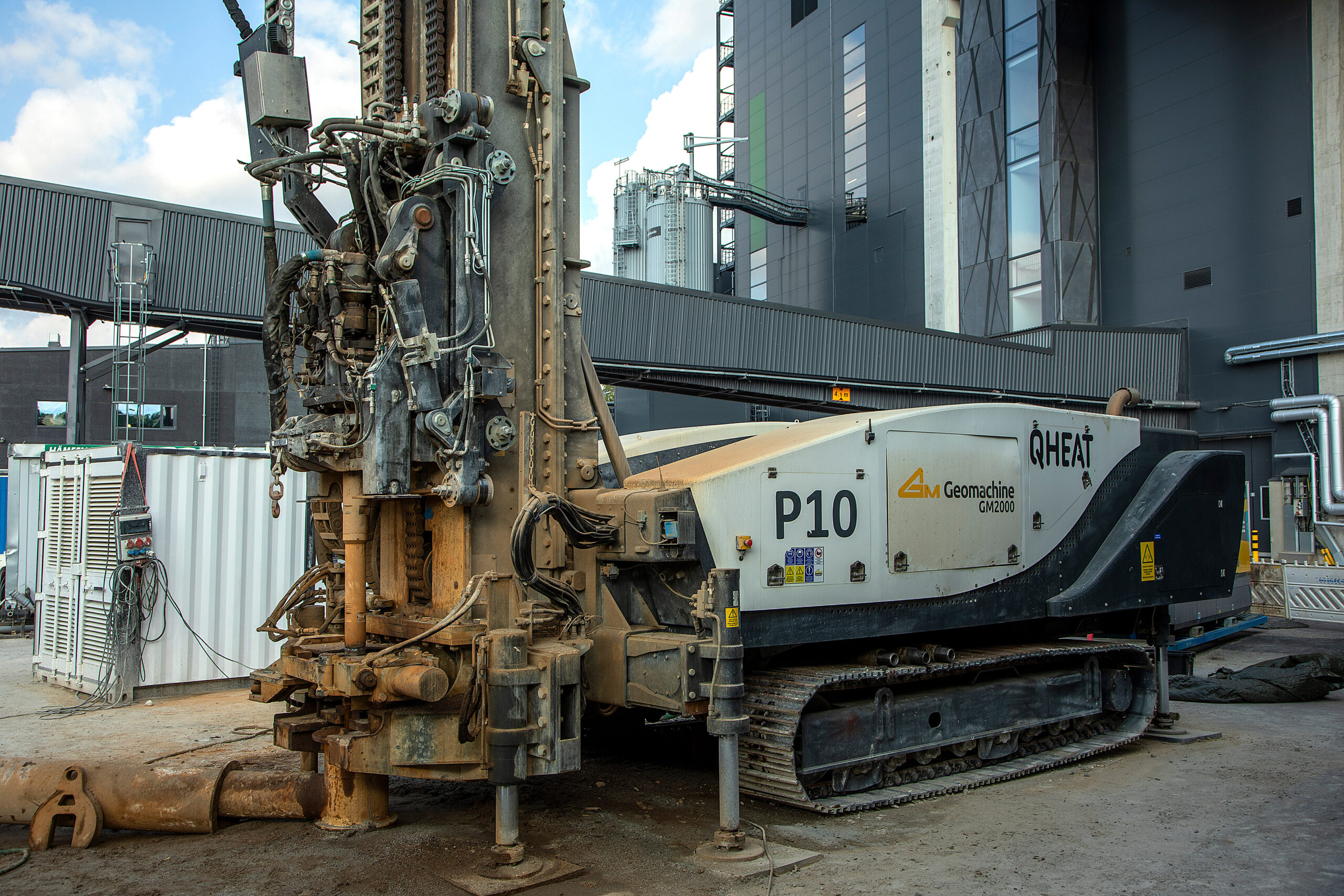