Deep customer insight drives Geomachine’s product development
13.12.2024
Geomachine
Geomachine is a company deeply committed to product development. At the core of every innovation lies a profound understanding of customer needs, the unresolved challenges within the industry, and the future directions of the field.
The guiding principle of Geomachine’s product development is to create solutions that genuinely meet its customers’ needs. To deepen its customer insight, Geomachine engages in close discussions with professionals in the geotechnical investigation and well-drilling sectors. This collaborative approach was pivotal also in developing the GM2000 drilling rig, designed specifically for deep geothermal well drilling.
To dive into the world of geothermal wells, Geomachine collaborated with consultant Jukka Ahonen. Ahonen’s expertise spans various drilling and piling methods, from anchoring to rotary drilling and quarry techniques ranging from precision holes for dimension stone to large-scale hammer drilling and shaft sinking.
“I have been involved in numerous mining projects, hydroelectric construction sites, and challenging foundation reinforcement projects around the world,” begins Jukka Ahonen. “In the well-drilling industry, I have worked for decades both in Finland and abroad, particularly in the Middle East, North America, and South America. My comprehensive understanding of the field has been built through hands-on experience, research, and especially through collaboration with local drilling professionals, who are the true experts in the field.”
The changing landscape of well drilling
According to Ahonen, the well-drilling industry has undergone significant changes in recent years. “Households have become more urbanized, and people now live in areas where municipalities provide water supply and wastewater infrastructure. Private households no longer find it worthwhile to maintain their own wells, making the drilling of traditional water wells for households increasingly rare. In contrast, vacation homes and farms, especially dairy farms, continue to invest in drilled well water.”
Global trends also influence the well-drilling sector, with the increasing demand for renewable energy being a major driver. As a result, the focus has shifted significantly towards drilling geothermal wells. “Today, 70–80% of new buildings rely on geothermal energy for heating. Geothermal wells have also been adopted as a heating solution for large new construction projects, such as halls, shopping centers, and factories.”
In densely built urban areas, one major challenge in utilizing geothermal energy has been the limited availability of land. “Previously, to meet the energy needs of a large property it has been necessary to drill for example 150 shallow wells. In densely built areas, this has naturally been challenging, if not impossible. Therefore, there has been a real need for deeper wells.”
Currently, a 2,000-meter-deep geothermal well is considered the most economically viable option, and thanks to QHeat and Geomachine, cost-efficient drilling to such depths is now possible. “The overall cost-effectiveness of a well is not only influenced by the drilling costs but also on how efficiently heat can be extracted from the well without losses. QHeat and Geomachine have successfully addressed this challenge.”
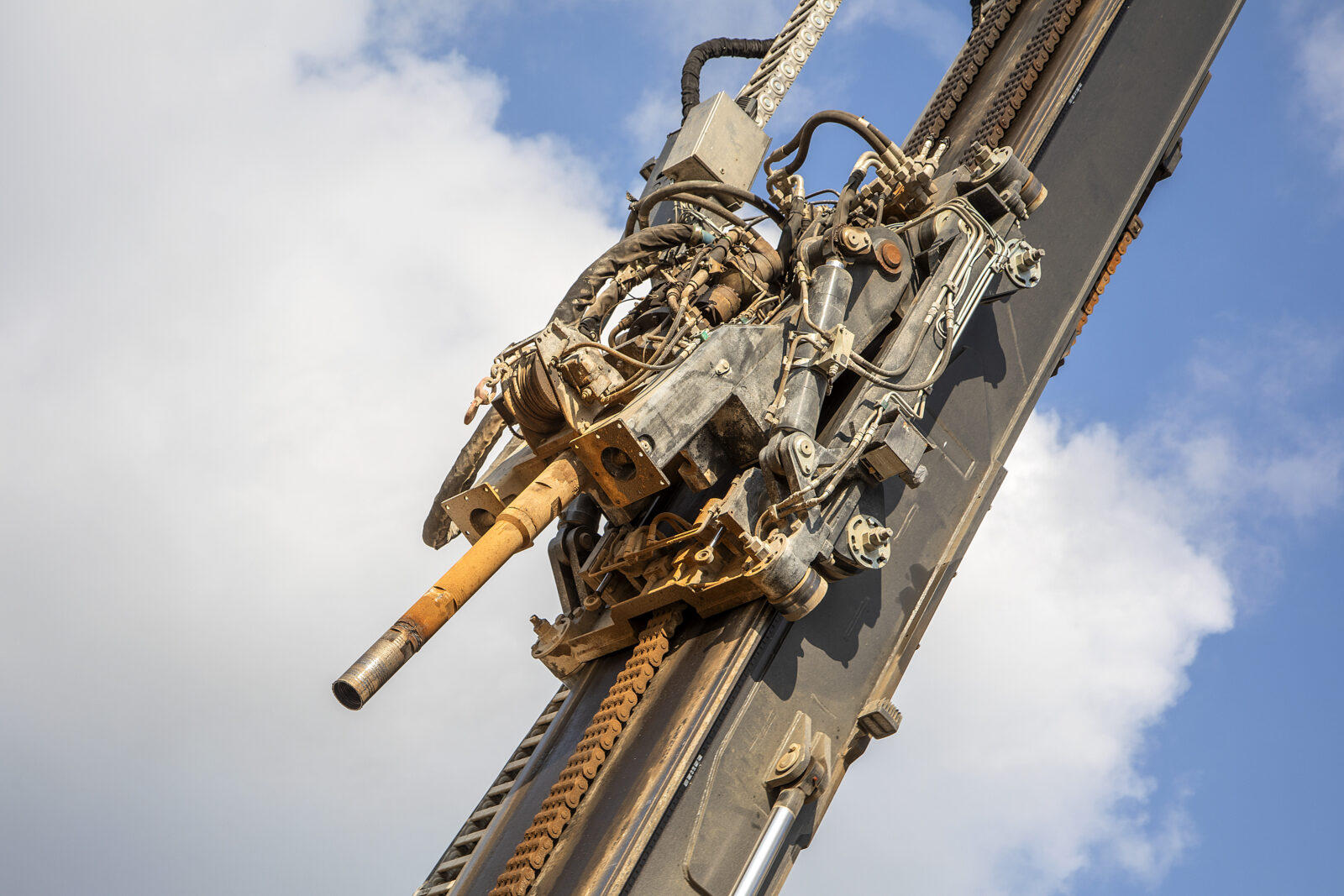
Unique challenges of deep geothermal well drilling
The Scandinavian bedrock is a slab of granite and other deep-rock types, hundreds of kilometers thick. Ahonen notes that in this ancient, folded, and layered bedrock, drilling conditions vary significantly as the depth increases. “Even in hard bedrock, there are fault zones, and within the first 500 meters, there is usually a lot of groundwater. Faults and high water inflow can cause the well walls to collapse. In the GM2000 solution, this challenge is mitigated by reinforcing the well walls with a casing for the first 500 meters. Besides preserving the well’s structure, wall reinforcement also serves another critical purpose: it acts as a surface water barrier, preventing unwanted substances from entering the groundwater.”
Water present in the bedrock also affects the drilling process. “Within the first 500 meters, encountered water can be under high pressure, ranging from 40 to 50 bar depending on rock fractures. This means the compressors used in drilling need to handle higher pressures than before. The GM2000 solution ensures a stable air supply by enhancing compressor performance with a dedicated high-pressure booster.”
To maximize cost-efficiency, it is essential to drill continuously without interruptions. “When drilling stops at the end of a shift, the well begins to fill with water. This means the well must first be emptied before drilling can resume. Developing faster methods for well-emptying is one area of future product development. Another focus is creating quieter drilling methods, which would enable 24/7 drilling without noise disturbances.”
Drilling brings up significant amounts of groundwater, which must also be managed. “The solids content in the groundwater must not exceed 300 mg/l. The water must either be transported off-site or treated before being discharged into the sewage system. Developing advanced water treatment systems is another key focus for deep-well drilling product development.”
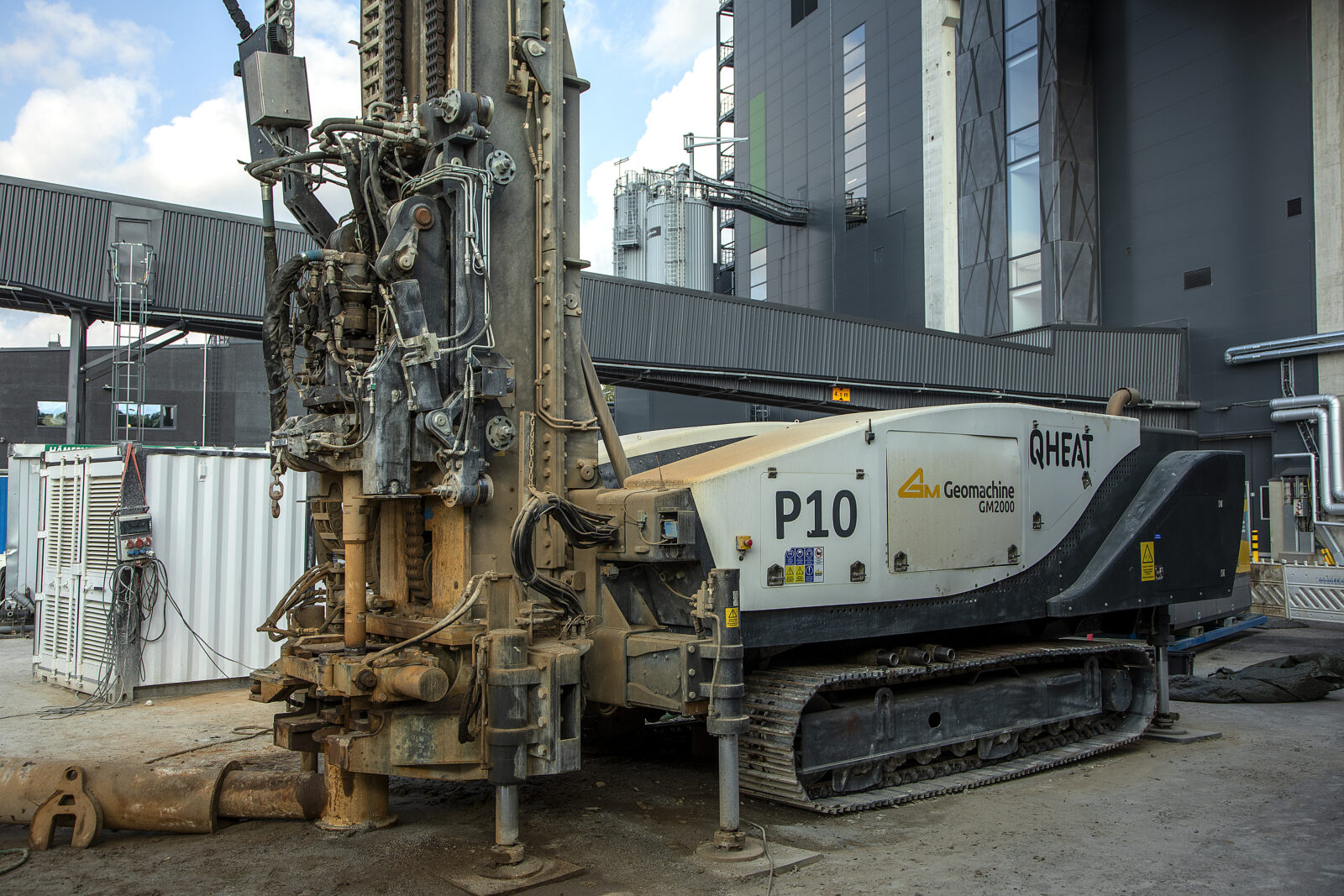
Increasing demand for renewable energy
Geothermal energy is highly likely to grow in popularity in the future. “The drive for energy self-sufficiency is intensifying. In Sweden, for example, interest in property-specific geothermal wells has surged due to the volatility of electricity prices.”
One of the challenges for the future is how to drill wells in confined environments, such as from within existing buildings. “In Canada, for example, there have already been attempts to develop new drilling and collector solutions for such scenarios.”
To make geothermal energy accessible for a wide range of properties, it’s essential to consider which well solution best suits each case—depth isn’t always the key factor. “Shallow wells are suitable for areas with fractured, water-rich bedrock, while deep wells are a good solution when the bedrock is homogeneous and relatively dry.”
Ahonen believes that drilling deep geothermal wells will continue to become more efficient. “Drilling to depths of 300–400 meters was still a significant challenge twenty years ago, but today it has become routine. Progress has been remarkable and will continue. Thanks to QHeat and Geomachine, we now have a solution that makes deep drilling cost-effective and replicable. The results achieved at the Salo Waste-to-Energy plant are very promising and suggest great potential for the future.”
Interested? Contact Geomachine!
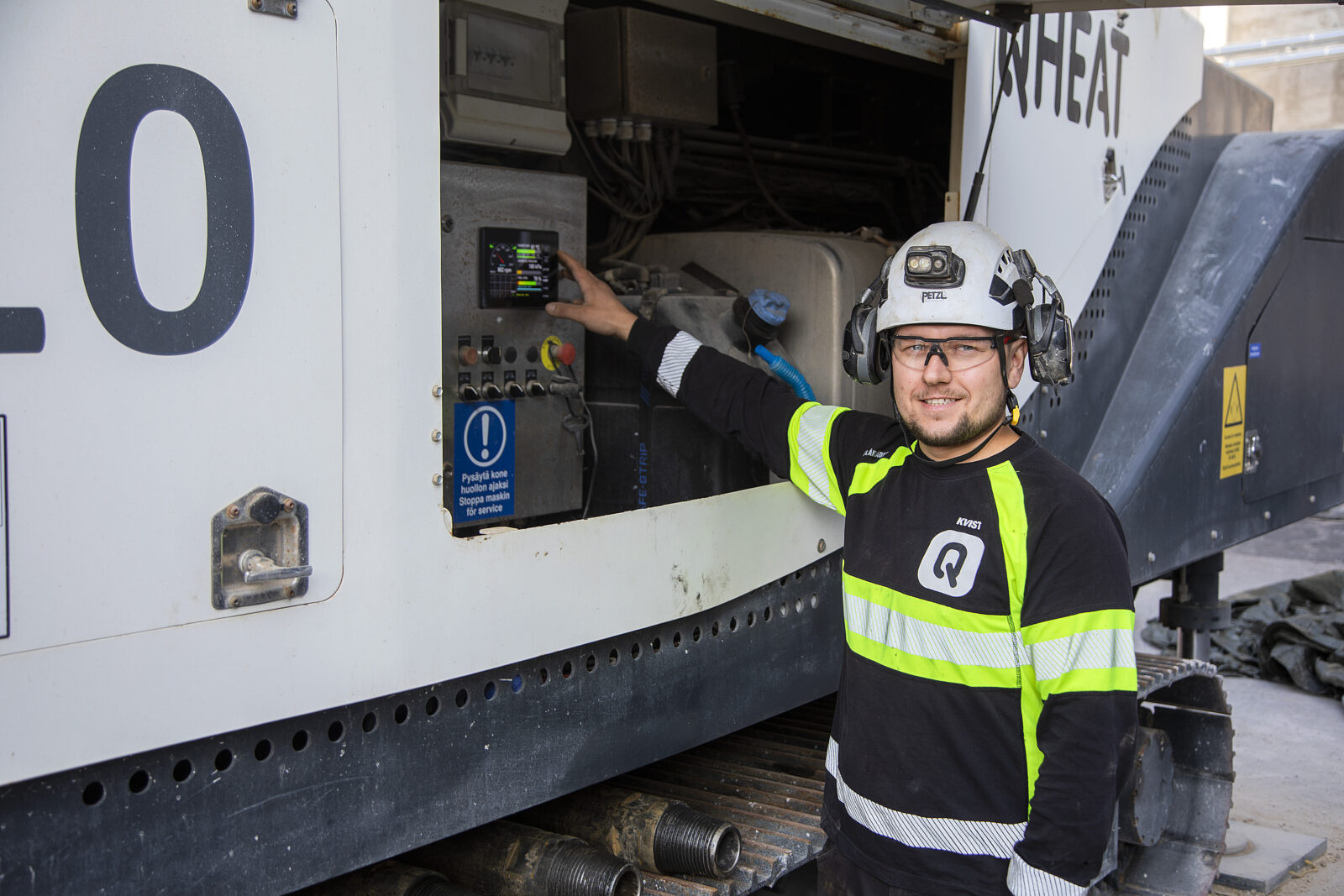