Kategoriat
Geomachine
Updating the equipment used in geotechnical investigations becomes relevant for every industry player from time to time. Whether it’s a facelift or a complete renewal, the process is clear and seamless under Geomachine’s guidance.
“The geotechnical investigation industry in the Nordic region is relatively small,” begins Alexander Packalén, Geomachine’s Chief Operating Officer. “It’s a highly specialized field where industry professionals often know each other. That’s why the companies reaching out to us for their equipment needs are frequently already familiar to us.”
Regardless of whether the customer is a long-time partner or a new acquaintance, the discussion always starts by aligning with their needs. “Most of our customers are well-informed and have a clear idea—down to the model—of the machine that best suits their requirements. However, sometimes they only have a general idea of the intended use. In such cases, we explore the situation in more detail, and based on these discussions, we determine the best approach for moving forward with the procurement process.”
The needs of all stakeholders are considered
When a customer first contacts Geomachine about acquiring a machine, their primary concern is usually the cost. “When the time comes to make a purchase, it’s naturally important to understand the budget scale. Once the investment range is clear, the customer can proceed with internal decision-making within their organization.”
The next step involves diving into the details. “We arrange a meeting for a thorough needs assessment. In addition to the decision-maker, we also welcome the machine operators to this discussion. A skilled driller typically has a strong opinion on the features their tool must have. By mapping out these requirements during the design phase, we can ensure a cost-effective production process, avoiding unnecessary modifications later when the machine is already nearing completion.”
Should you upgrade or replace?
According to Alexander Packalén, the goal is always to find the best solution tailored to each customer’s needs. “We provide calculations for our customers to assess whether upgrading their existing equipment or investing in a new machine would be more cost-effective in their specific case. This analysis is especially crucial for companies continuously striving for better profitability.
Sometimes, an upgrade isn’t enough. Companies positioning themselves as industry pioneers and preparing for future changes in their business environment often choose to acquire an entirely new machine. “The geotechnical investigation industry is subject to increasingly stringent regulations, particularly regarding emissions standards. If a company aims to operate in densely built urban areas or participate in public tenders, acquiring a new machine is often the smartest choice. Even if an old machine has been upgraded with smart technology, a new boom, or other modern features, it won’t be competitive if its diesel engine exceeds emission limits.”
The geotechnical investigation sector is constantly evolving. “We closely monitor industry developments and regulatory changes. While no one can predict the future with certainty, we can at least provide well-informed insights based on our expertise.”
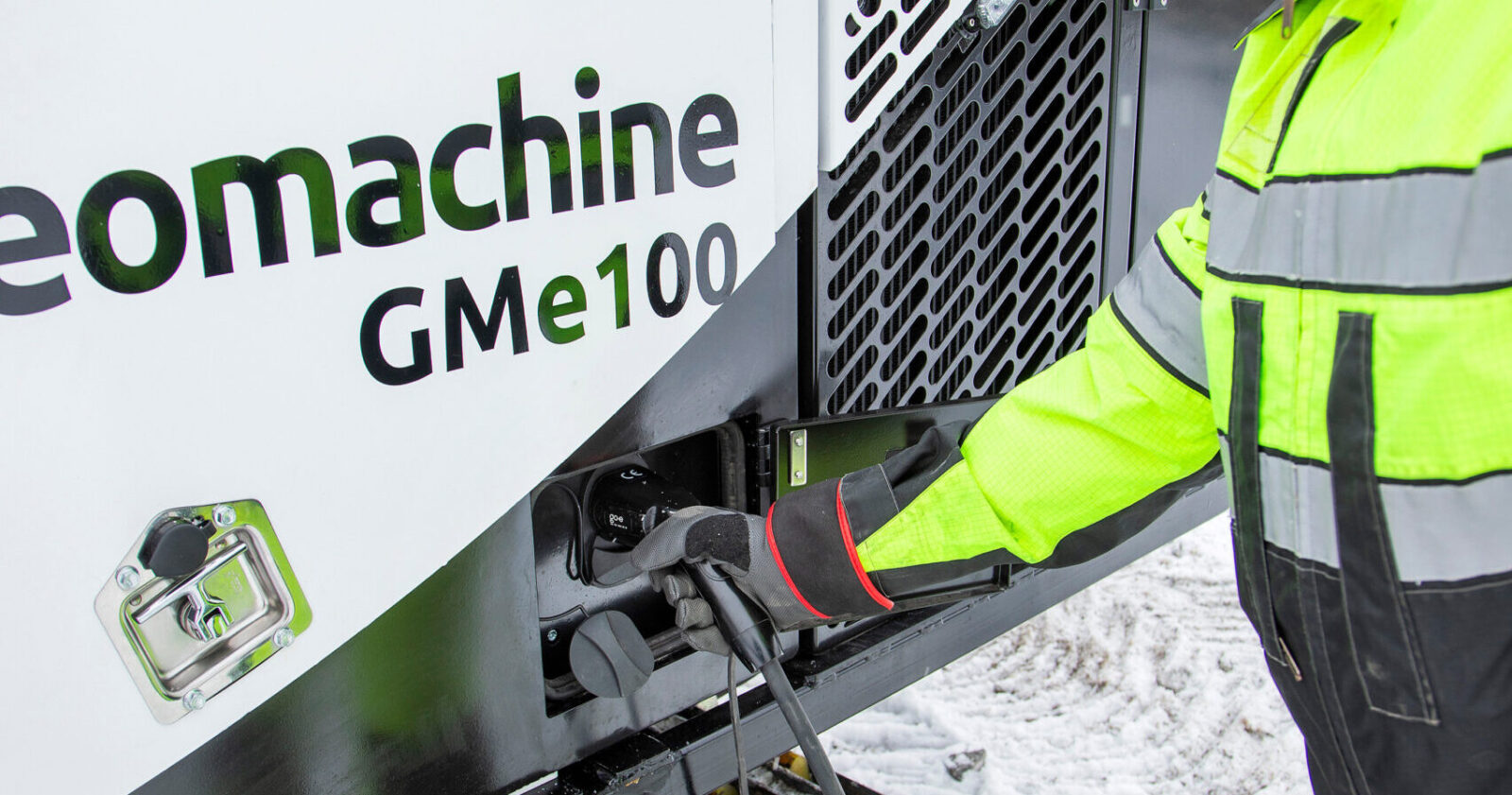
Start the conversation when the need arises
When it’s time to update or renew equipment, Alexander Packalén encourages reaching out to Geomachine without hesitation. “Our Sales Manager, Alex Lindholm, is the right person to contact by phone or email. He initiates the discussions and assembles the Geomachine team to drive the procurement process forward. Depending on the case, machine production times range from a few months to a year. That’s why it’s best to start the conversation as soon as a new purchase is on the horizon—ensuring that the machine is ready for use exactly when needed.”
Regardless of the level of preparedness or prior knowledge about equipment procurement, Geomachine is always a valuable partner. “We have been in the geotechnical investigation field for several decades and have learned to listen closely to our customers’ needs. We guide the procurement process in close collaboration with our clients, from the initial needs assessment to the moment the machine rolls off our production line. Customer satisfaction is always our priority, and we are known for this in the industry. That’s why we are the right partner for professionals who want to work with the best tools on the market and continuously improve their business success.”
Interested? Contact Geomachine!
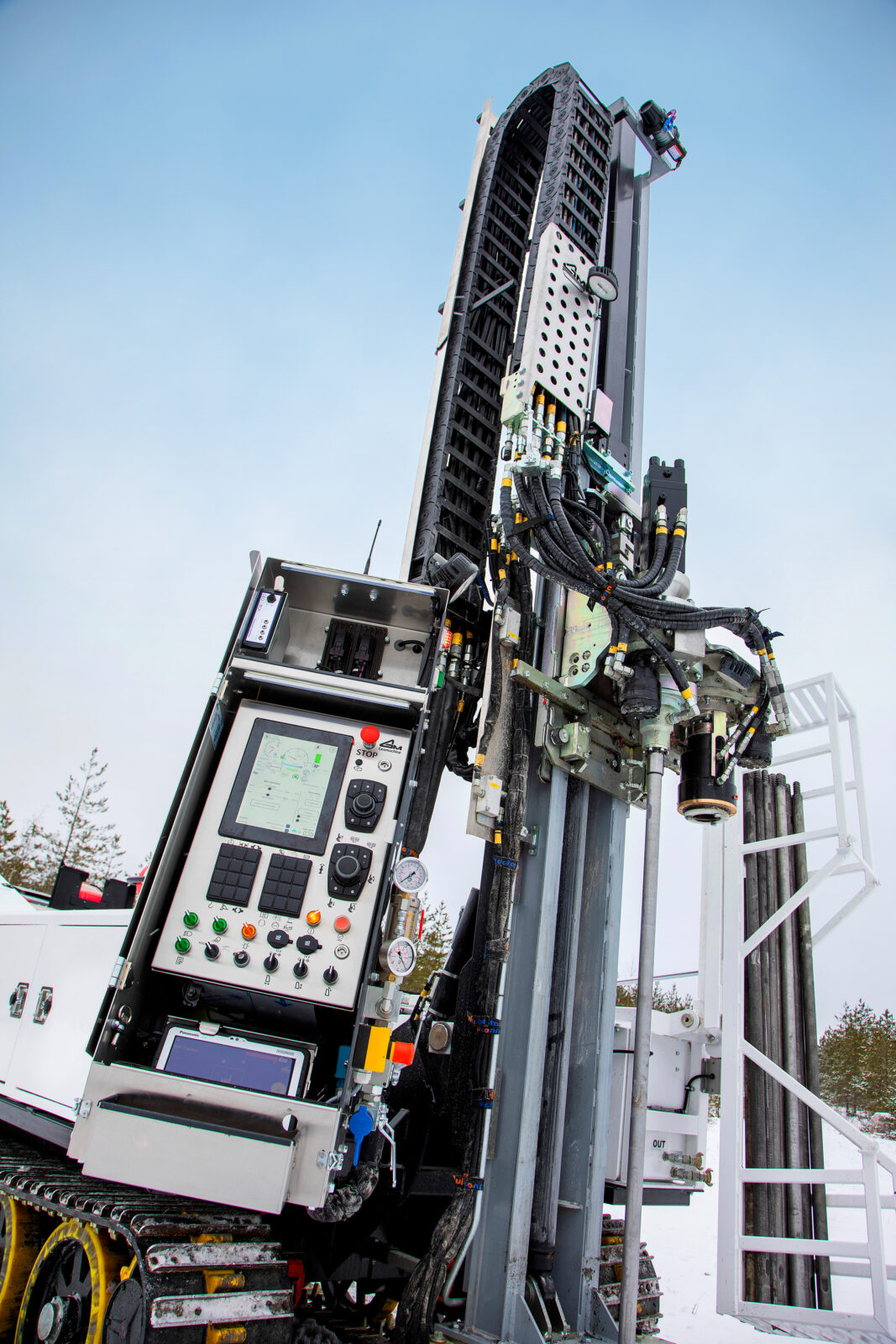
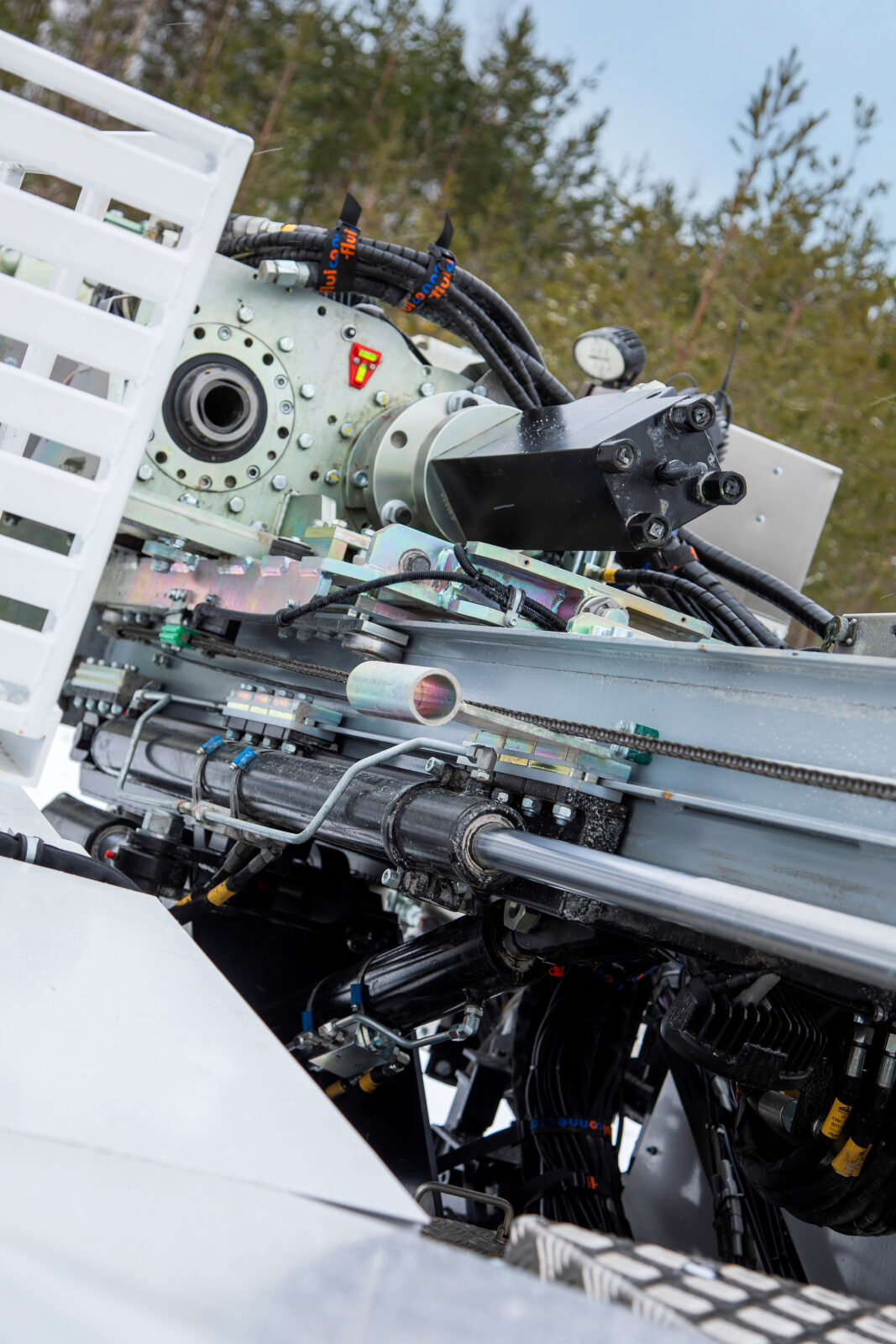
Geomachine
The emission class requirements for machines used in ground investigation are becoming increasingly stringent, and the pressure to work in an environmentally friendly manner is growing. Geomachine’s response to this challenge is the fully electric GMe100 drill rig.
The emissions of diesel-powered work machines have begun to be restricted, especially in densely built urban areas. For example, in Oslo, their use is no longer permitted. Efforts to reduce emissions are also evident in public tenders organized by cities, where emission class requirements are stricter than before, even if emissions are not yet legally regulated in the tendering area.
In the world of ground investigation, just like in technological development in general today, the trend is towards electrification. New product innovations are continually being introduced under this theme. Geomachine is also actively developing products to meet changes and expectations in its operating environment. The latest example of this is the fully electric GMe100 ground investigation rig.
New product innovations are created in collaboration with customers
Geomachine’s Chief Technology Officer, Vesa-Matti Salminen, explains that the GMe100 ground investigation rig was developed based on market needs. “When the requirement for zero-emission operation was enforced in Oslo, Norway, our distributor operating there contacted us. Following discussions and market research, we began developing an electrically powered drill rig in 2023.”
The GMe100 drill rig was built on the existing diesel-powered GM100 platform. It retains the same functionalities and usability as its diesel-powered twin. The machine’s operations remain hydraulic, but power generation in this rig is fully electric.
The length of Geomachine’s product development process varies depending on whether it involves a completely new product innovation or the further development of an existing product. The journey of the GMe100 drill rig from the drawing board to machine delivery took about two years.
When developing a completely new innovation, the product development process does not end at the time of delivery. “Although the machine is ready at delivery, close collaboration with the customer continues in the support phase,” says Geomachine’s Head of Engineering, Juha Sandholm. “We collect customer feedback on the real-world functionality of the machine to make further refinements if needed. Customers who invest in new innovations are industry pioneers. They understand that a finished product can still be refined after deployment and are keen to participate in this stage of product development.”
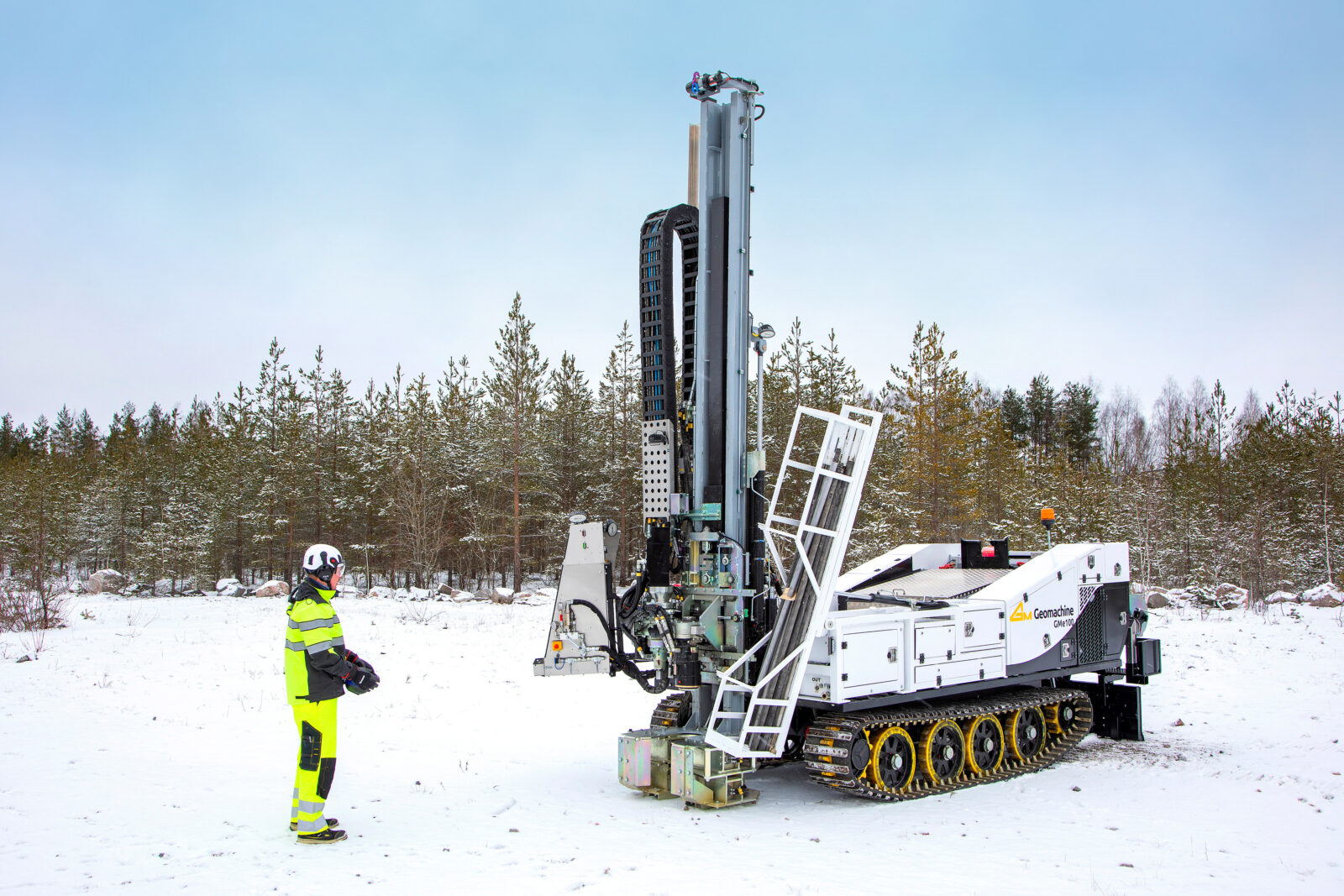
An electrically powered option for ground investigation
The GMe100 ground investigation rig is suitable for all the same investigation methods as its diesel-powered twin. These include dynamic probing, weight sounding, percussion drilling, casing drilling, spt and dspt testing, cpt and cpt-u testing, and pore pressure drilling. Additionally, it is suitable for groundwater pipe installation and sampling from both hard and soft grounds.
The GMe100 rig is powered by a battery-operated electric motor. Compressed air is supplied via an electric compressor. “During product development, we realized that using an electric compressor improves the efficiency of the fully electric machine, allowing for longer operation on a single battery charge,” says Juha Sandholm. “With a dedicated motor for the compressor, we were able to reduce the size of the machine’s main powertrain motor.”
The battery life of the rig varies depending on the investigation method used, and its capacity can be increased with an additional battery pack if necessary.
Like Geomachine’s equipment in general, the GMe100 is highly intelligent. It features an IQAN control system and GMTracker data logging software. A Cloud version of the logging software is also available, enhancing workflow efficiency, machine maintenance, and project management by connecting all stakeholders in the project’s value chain in real time.
Usability was another key focus in designing the GMe100 rig. This machine includes more storage space than before for the operator’s tools and essential liquids.
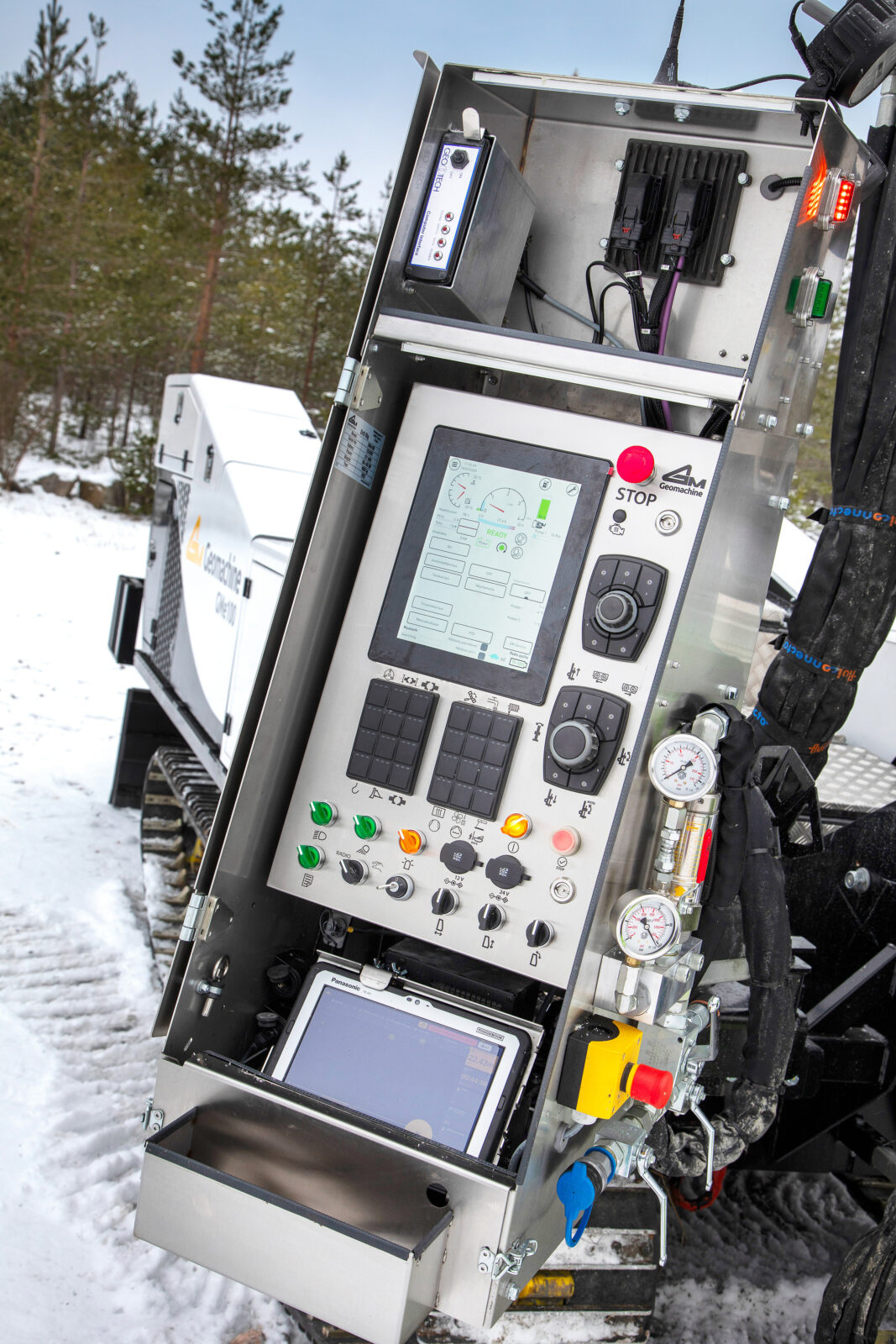
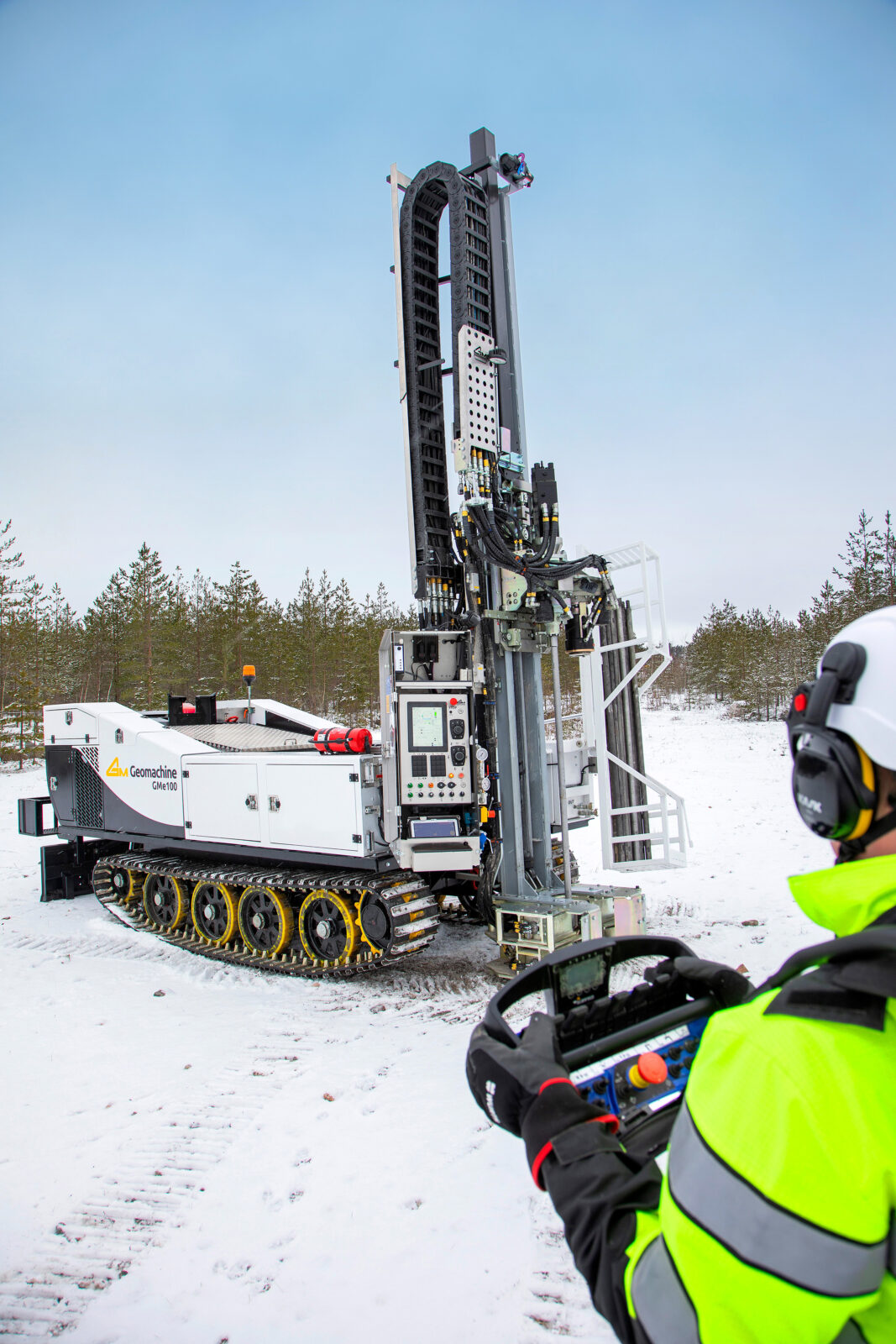
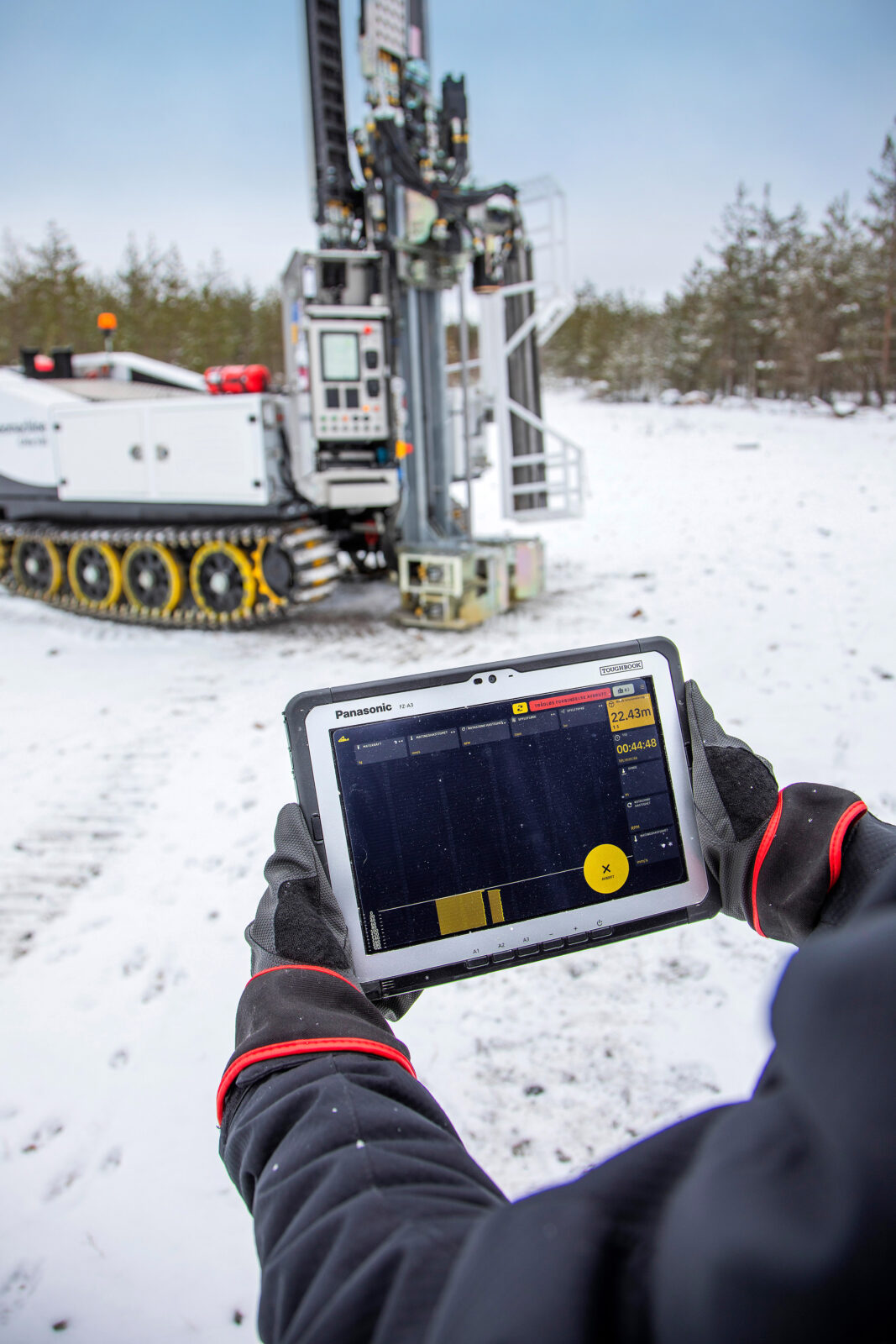
Key principles of product development
Vesa-Matti Salminen explains that Geomachine adheres to specific requirements in product development, ensuring that every product meets the highest standards. “We strive for quality in everything we do; our machines must be durable and perform at their best. Our products must also be easy to use. That’s why we aim for minimal differences in usability between models. Workplace safety is another crucial factor, and we continuously develop new solutions to enhance it.”
Geomachine’s customers share a commitment to working with the most reliable and user-friendly machines on the market. But that’s not all. “Our customers also highly value efficient and high-quality customer support. It’s important for them to get assistance from a familiar service representative who knows the machine’s history and features inside out.”
The GMe100 is a product innovation that Geomachine is extremely proud of. “Drawing on our extensive experience, we have successfully built a machine that enables ground investigation with exceptional quality and efficiency—now also in a more environmentally friendly and emission-free manner, meeting today’s demands.”
Interested? Contact Geomachine!
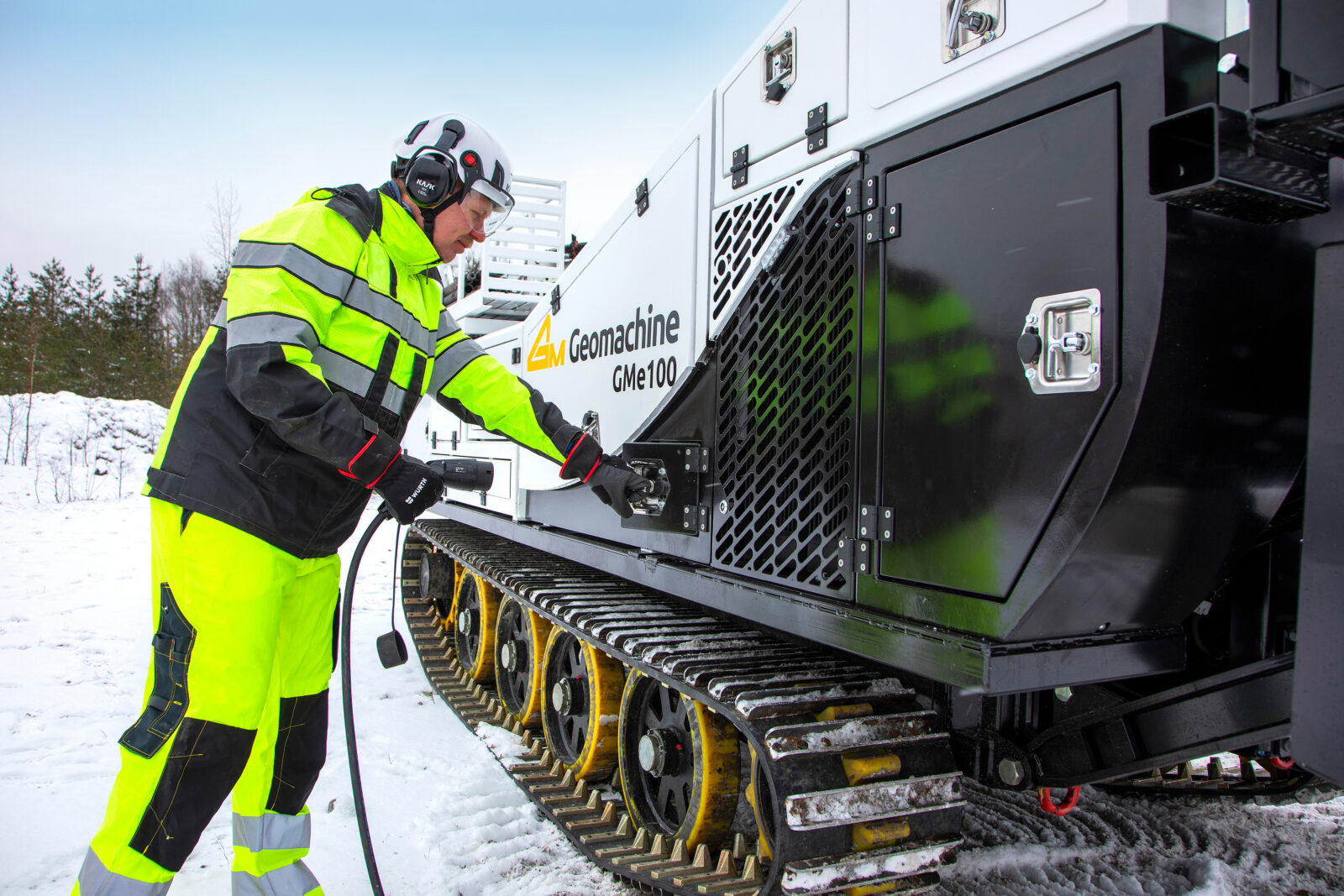
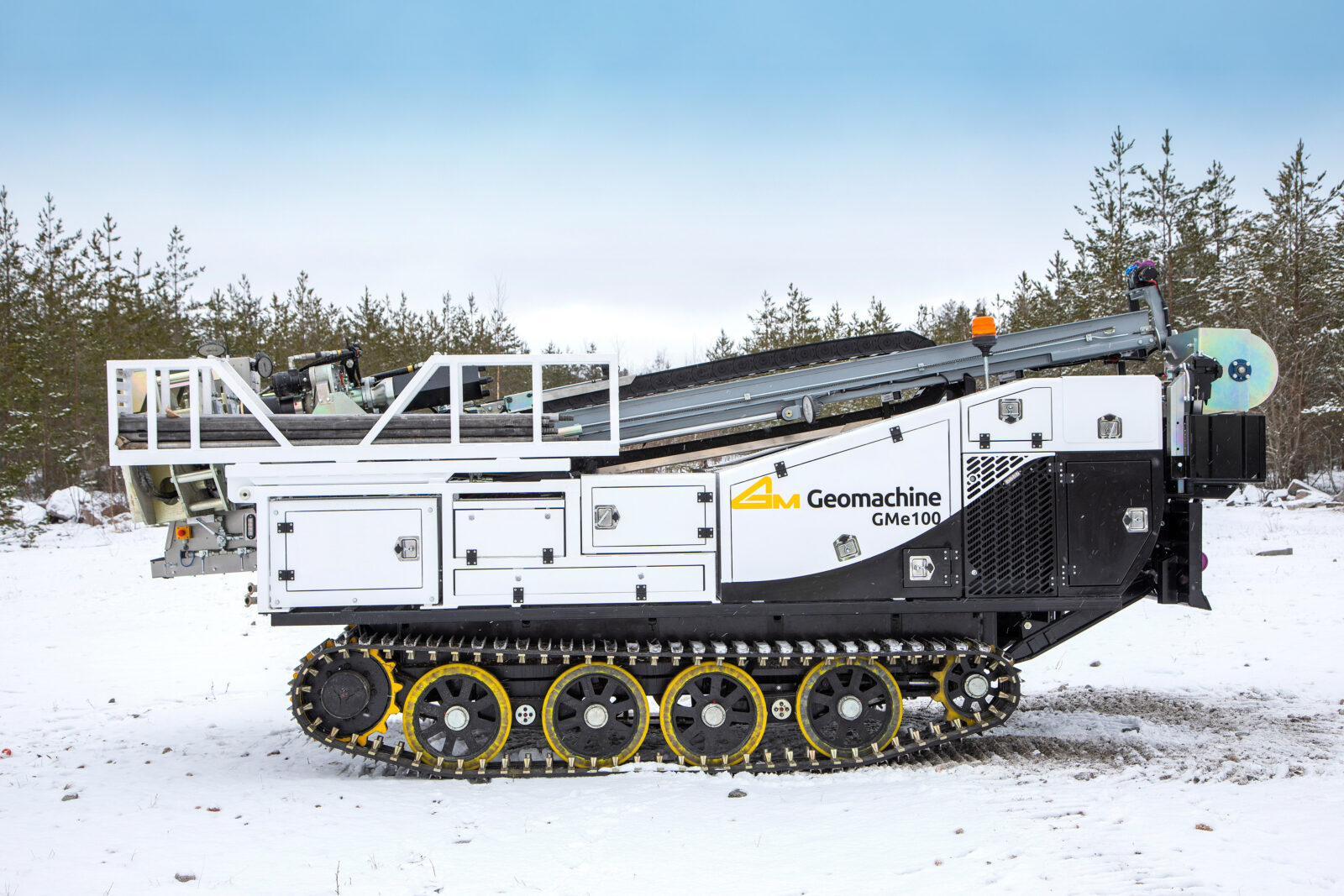
GMTracker
Information about the geotechnical field equipment used in ground investigations must be documented in the investigation report. Thanks to a new feature in the GMTracker data-logger, data on equipment is now transferred to the investigation report without manual effort.
The equipment required for ground investigations include, for example, CPT cones, vane shear devices, and sampling tools. These details must also be recorded in the work report for the investigation.
The new feature added to the GMTracker data-logger enables the maintenance and automatic adding of equipment data in work reports. The equipment registry contains information on the device’s identifier, model, type, and calibration, depending on the device. GMTracker is the only data-logger on the market whose registry also includes sampling tubes. Thanks to this new feature, equipment data is always accurately recorded in reports.
In the future, equipment management will also be integrated into the Cloud version of the GMTracker data-logger. Once data can be stored in the cloud, all stakeholders requiring equipment information will gain a comprehensive view of the devices used by the investigation company, their age, condition, and calibration status.
Managing specialized equipment through GMTrackerCloud will not only enhance reporting but also streamline the execution of investigation projects. It will help project management allocate sampling tasks to specific investigation vehicles without needing to transfer equipment from other sites. In the future, calibration values for equipment will also be manageable via GMTrackerCloud.
Interested? Take contact!
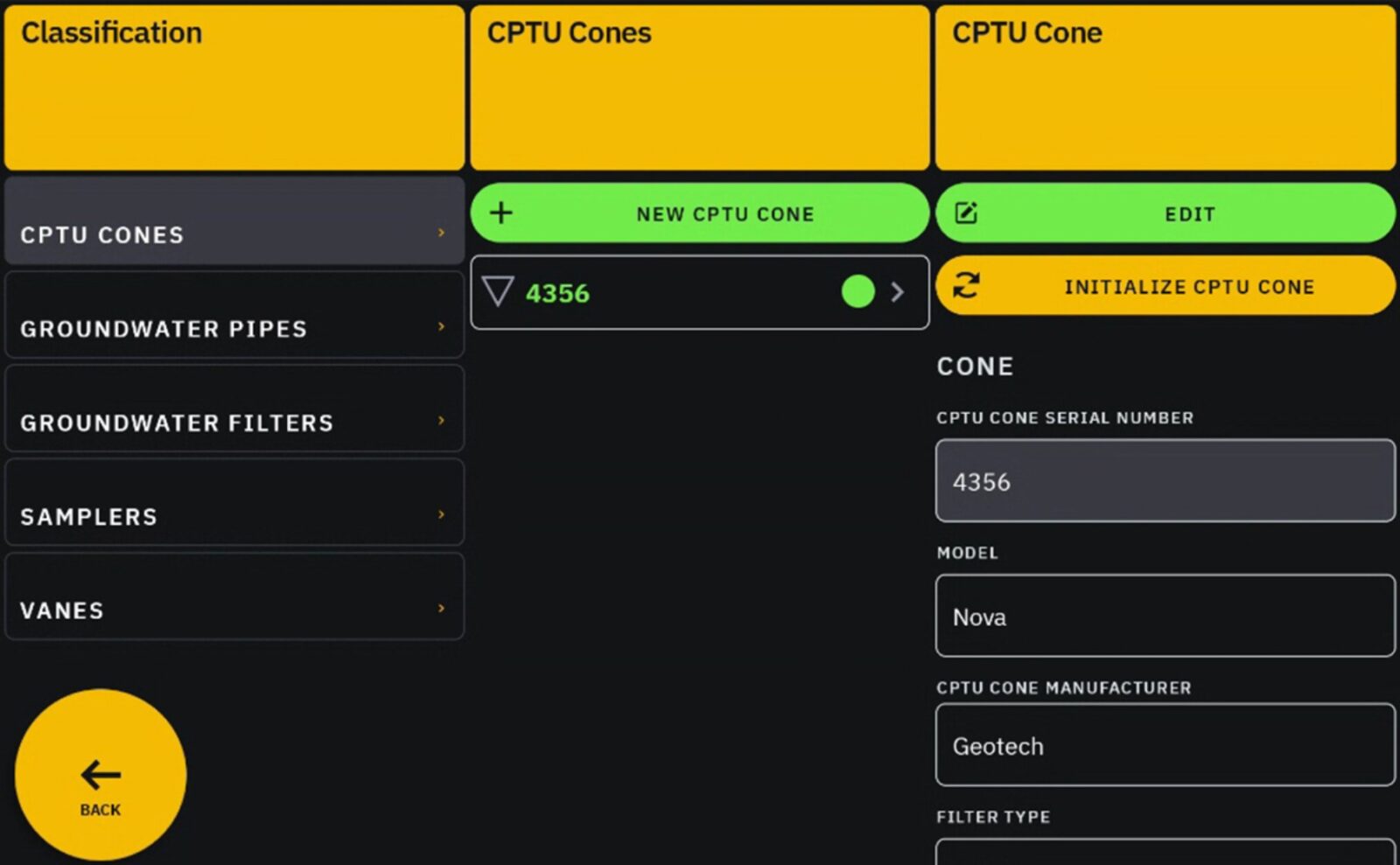
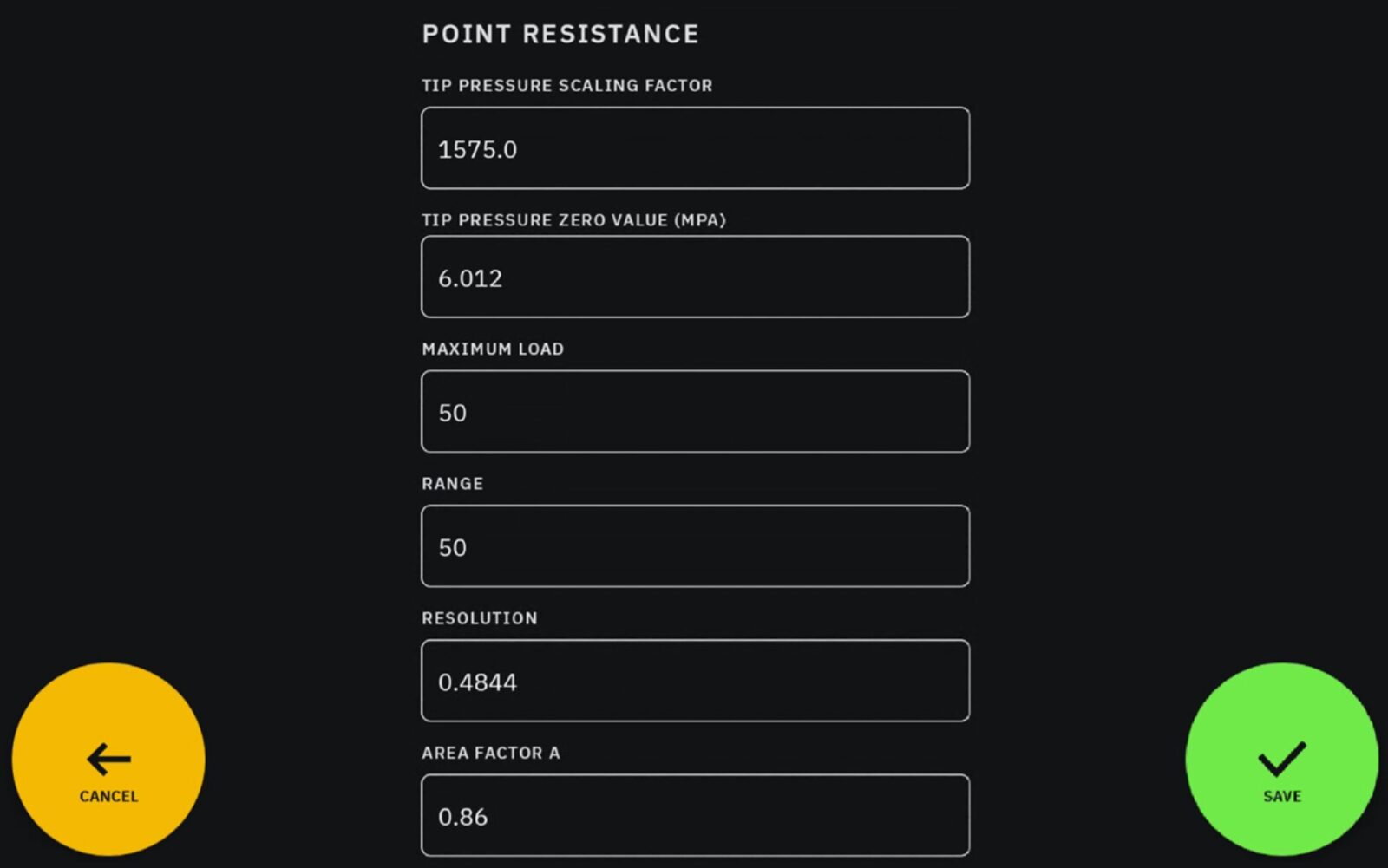
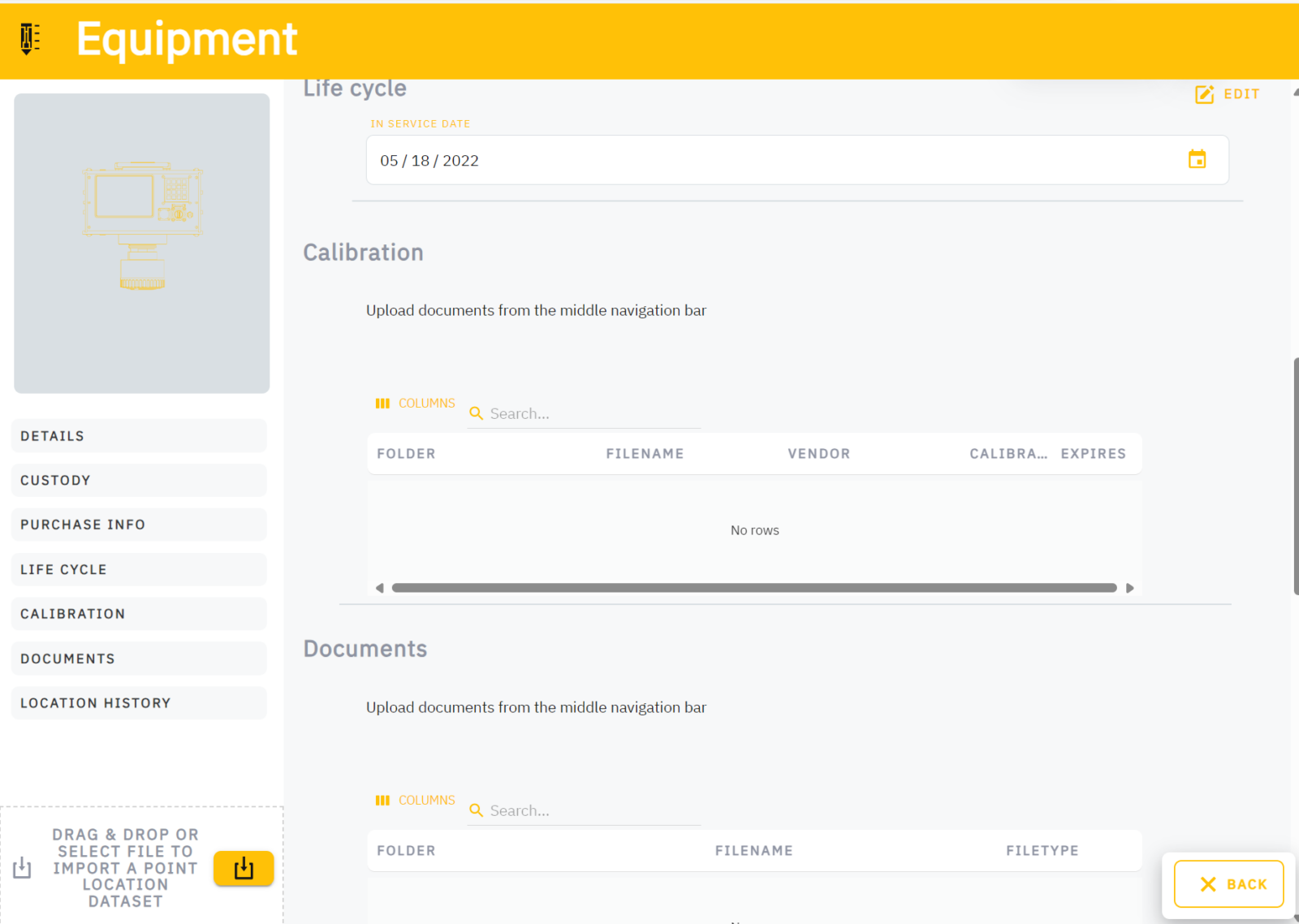
GMTracker
Weather conditions can impact the results of geotechnical investigations, which is why they are documented in the project’s work report. Geomachine has enhanced its GMTracker data-logger with a new feature that records weather data during investigations, allowing this information to be easily integrated into reports.
Geomachine’s GMTracker data-logger is now smarter than ever, thanks to its new weather-tracking feature. This functionality significantly streamlines the work of project managers, as weather information can now be directly copied into the report from geotechnical investigation data. This means that there’s no need to retrieve it separately from a weather service during the report preparation phase anymore.
Using this feature in the GMTracker is straightforward. With the device’s location tracking enabled, the data-logger automatically fetches weather data from a weather service and includes it in the investigation report. Recorded data includes temperature, dew point, precipitation, and wind speed during the investigation.
Geomachine’s GMTracker is currently the only geotechnical data-logger on the market equipped with a weather tracking feature.
Interested? Get in touch!
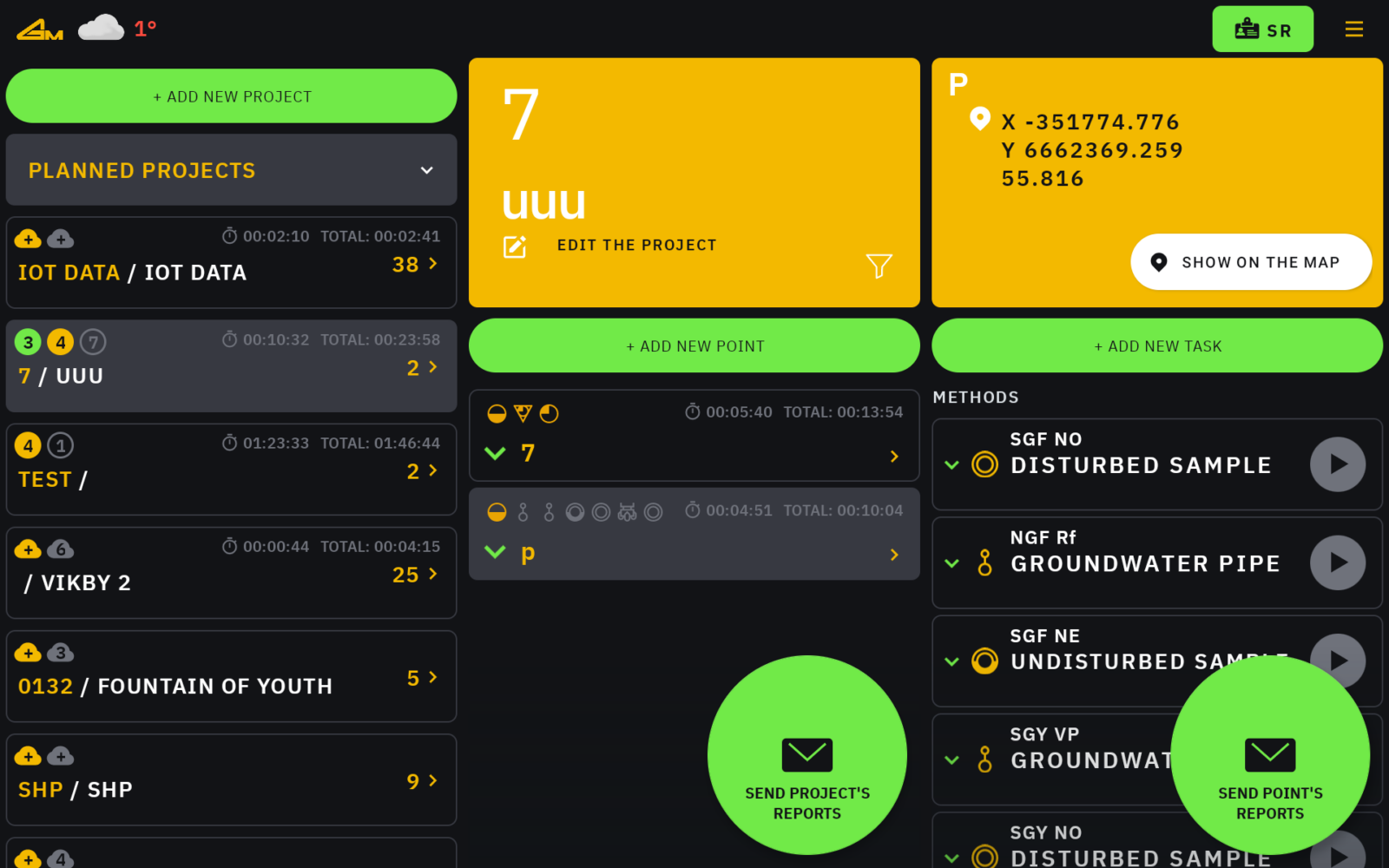
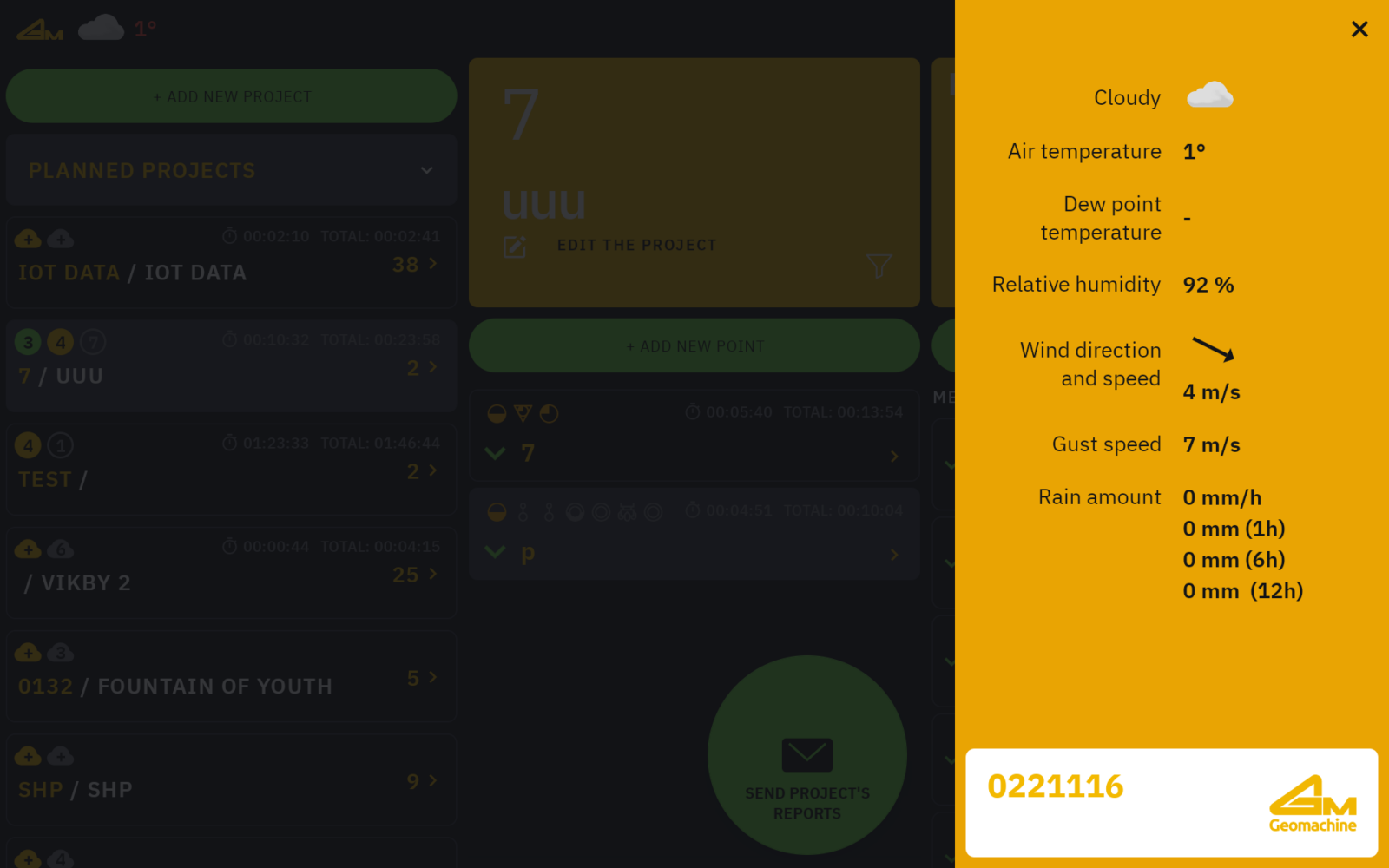
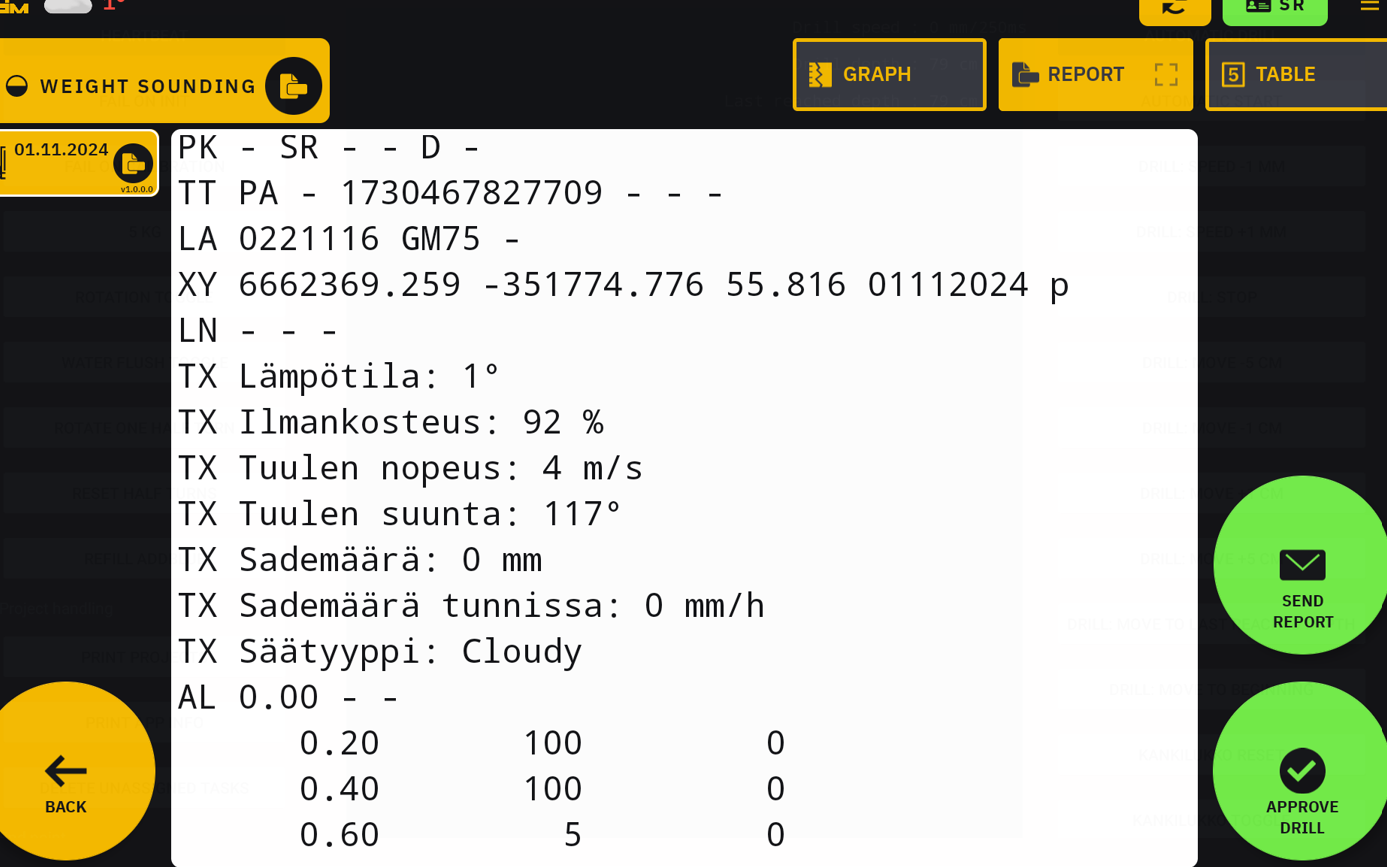
Vegagerðin
Vegagerðin is an Icelandic state-owned company responsible for managing the country’s roads and infrastructure. The company has recently adopted Geomachine’s GMTrackerCloud service, which enables it to conduct geotechnical investigations in the most intelligent way possible.
Thanks to the GMTrackerCloud service, geotechnical projects can now be carried out more efficiently. The service enables the data-logging, storage, processing, and real-time availability of data for all members of the value chain. “GMTrackerCloud makes the data supply chain smarter,” says Pasi Majakangas, Head of Digital Products at Geomachine. “It reduces the amount of manual work, and the data is always effortlessly accessible to everyone who needs it.”
According to Sverrir Sverrisson, Project Manager at Vegagerðin, GMTrackerCloud is now used by all stakeholders involved in geotechnical projects in Iceland. “Geotechnical engineers upload their drilling plans to Geomachine’s cloud and allocate tasks to the drilling rigs. The field investigator performs the investigations as requested and uploads the data to the cloud service. Geotechnical engineers receive the data in real time from the cloud and can utilize it in their work without delay.”
The activation of the GMTrackerCloud service also eases the workload of field investigators in other ways. “We have implemented a Bluetooth-enabled CPTu solution. This allows the transfer of investigation data wirelessly from the CPTu probe to the GMTracker data-logger. Additionally, we use DGPS positioning, which ensures that the precise location of the investigation point is measured and also saved to the cloud in real time.”
Since Vegagerðin is the sole organization conducting geotechnical investigations in Iceland, the adoption of the GMTrackerCloud service means that the entire country’s investigations are now carried out in a more efficient, high-quality, and intelligent manner.
Interested? Contact us!

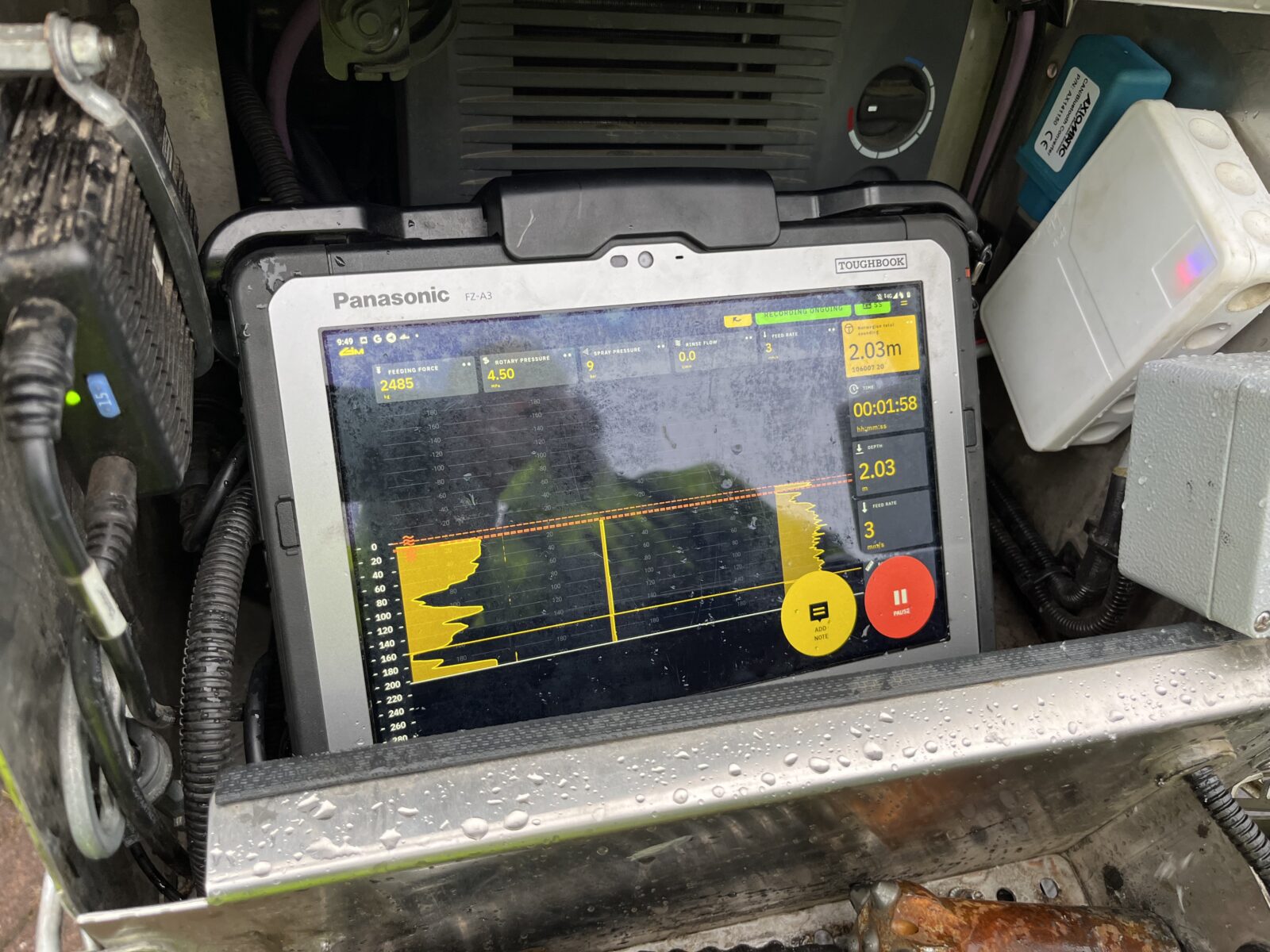
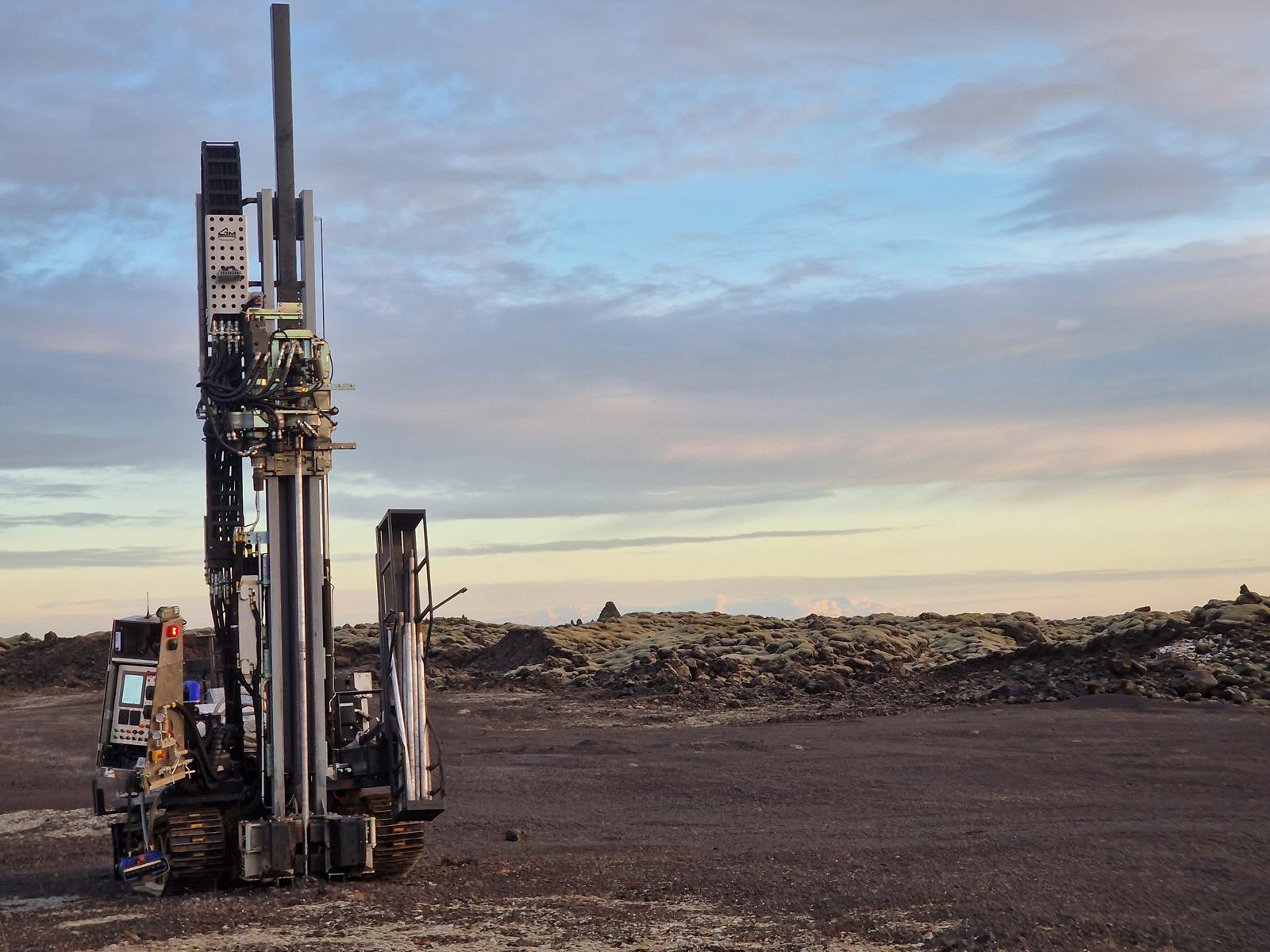
Der Geothermie Kongress
In October 2024 Geomachine participated in Der Geothermie Kongress event in Potsdam, Germany. During the three-day event, congress attendees were presented with a comprehensive lecture series on various topics related to geothermal technology, one of them being Geomachine’s GM2000 drilling solution.
“We joined the event at the suggestion of our new German distributor, BODO,” says Ari Kuhalampi, Geomachine’s Product Line Director. “It turned out to be a good decision, as deep geothermal drilling is currently a hot topic worldwide. In Europe, DTH drilling technology is still relatively unknown, so Geomachine’s presentation on the subject was met with great interest at the event.”
The congress attracted approximately 600 visitors over three days, with 110 presentations given. “Geomachine’s presentation focused on showcasing the unique benefits of the GM2000 solution. In our presentation we put emphasis on the fact that drilling requires only a small land area nowadays and opened up the GM2000’s sectored drilling process. In addition we presented our GMTrackerCloud service, which makes the drilling process intelligent and this way also enhances it’s efficiency.”
In many parts of central and southern Europe, the soil is soft. This means that deep well drilling in these regions requires combining multiple drilling technologies. “When drilling through soft soil layers, appropriate methods must be used, such as reinforcing the well walls. Once through the soft soil, Geomachine’s solution allows drilling to continue as the ground turns to rock at greater depths. Different technologies are not mutually exclusive but rather complementary.”
Geomachine’s presentation piqued the interest of professionals in the well-drilling sector from Germany, Austria, and Switzerland. “There was particular interest in how drilling has progressed with the GM2000 solution at the waste-to-energy plant in Salo, Finland. Additionally, questions were raised about daily drilling progress and drilling costs. Now that we have concrete evidence of how efficiently and replicably deep wells can be drilled today, it’s easy to explain it clearly to all those interested in the topic.”
News of Geomachine’s GM2000 solution had already reached many congress attendees before the event. “We have been actively producing content related to deep well drilling for our website and social media channels lately. These efforts have clearly been noticed and received with interest. This encourages us to continue sharing information on the topic. It strongly seems that our solution is attracting significant interest and meets a real need.”
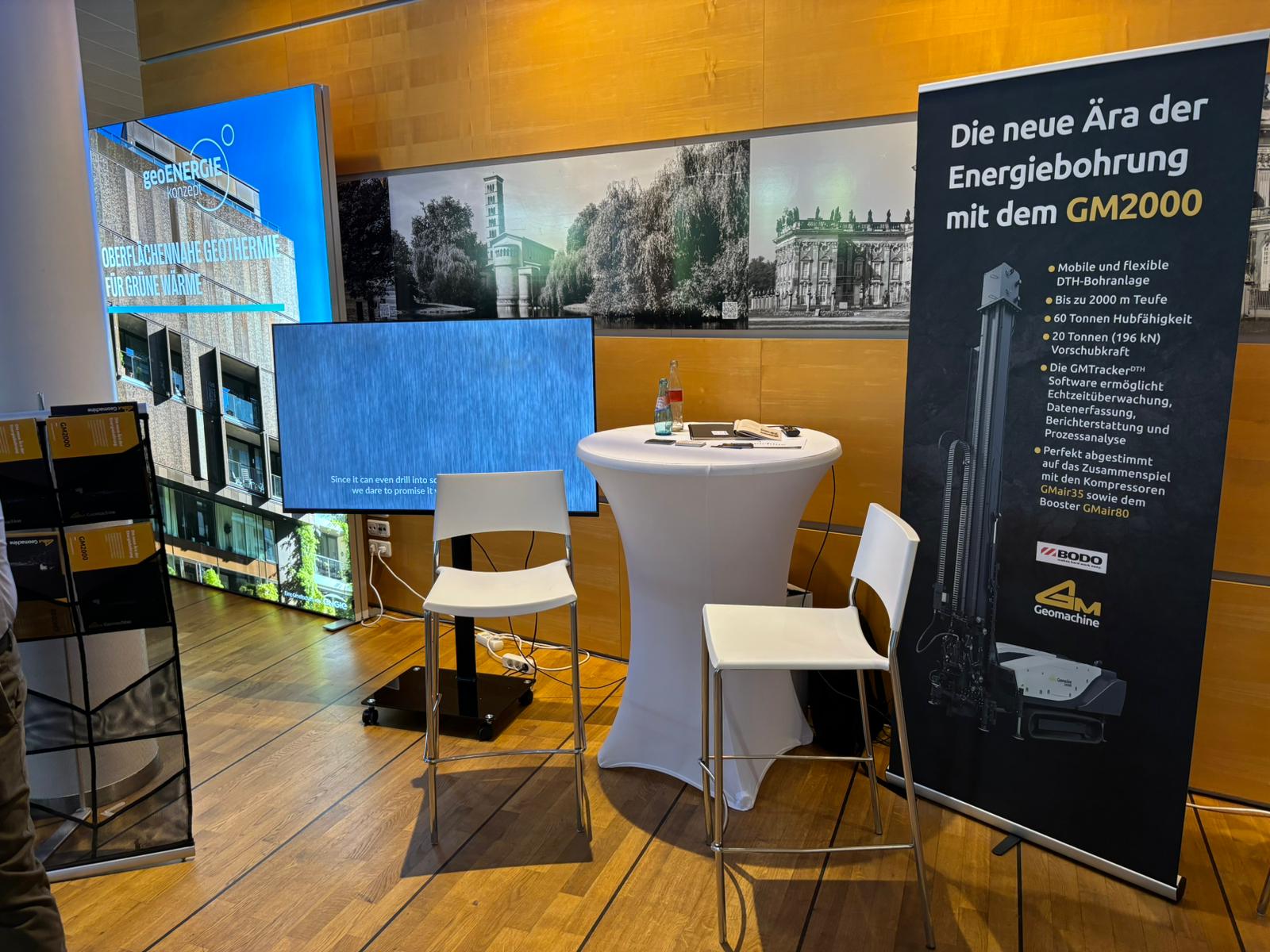
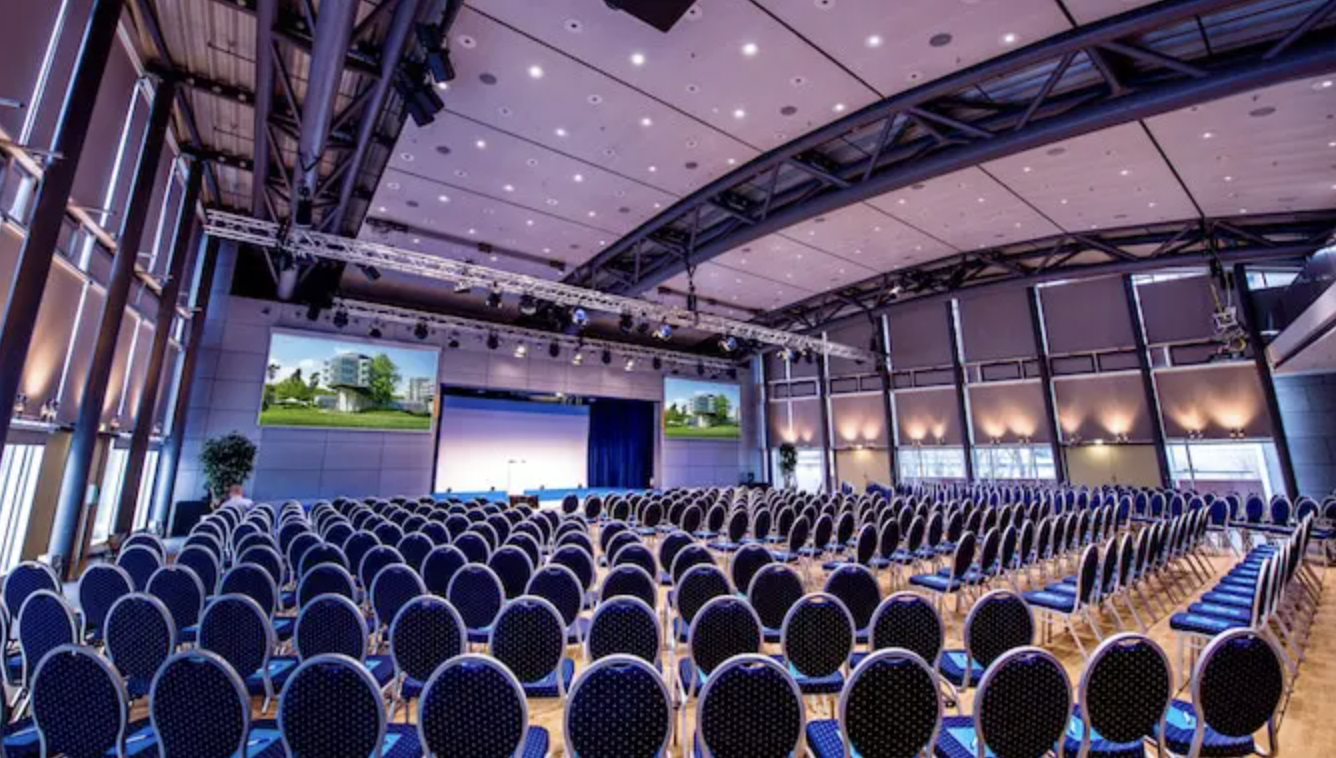
Geoenergidagen
Geomachine wants to actively engage in the discussion on renewable energy. For this reason, it often participates in the events that are organized on this topic worldwide.
“In the beginning of October 2024 we participated in the Geoenergidagen event, held in Nynäshamn, Sweden,” says Ari Kuhalampi, Product Line Director at Geomachine. “The two-day event brought together some of the most prominent players in the geoenergy sector from around Sweden and the Nordic countries.”
Geomachine focused on highlighting the unique features of the GM2000 drilling solution during its presentation. “Drilling geothermal wells has truly become replicable and cost-effective thanks to our GM2000 solution. The required area for drilling is minimal, just a 30m x 40m space is enough. The equipment is easy to set-up and transport. The actual drilling, machine control, and drilling progress monitoring are made possible with the GMTracker data-logger.”
According to Ari Kuhalampi, the efficiency of the drilling process and, therefore, the timely completion of the well is based on the phased drilling process. “In the first phase, the attention is paid to surface layer, then the water, and in the final phase, drilling is carried out to the target depth using data collected by the GMTracker data-logger. Using the latest IoT and cloud technologies this information can also be saved and shared in real-time with everyone who needs it.”
According to Ari Kuhalampi, another factor contributing to the cost-effectiveness of the drilling process is how the machines are maintained. “At Geoenergidagen, we also introduced Geomachine’s GMCare maintenance service, which helps shift from reactive to predictive maintenance of drilling equipment. When the necessary maintenance can be done systematically and by communicating efficiently with the service, the utilization rate and productivity of the machines can be maximized.”
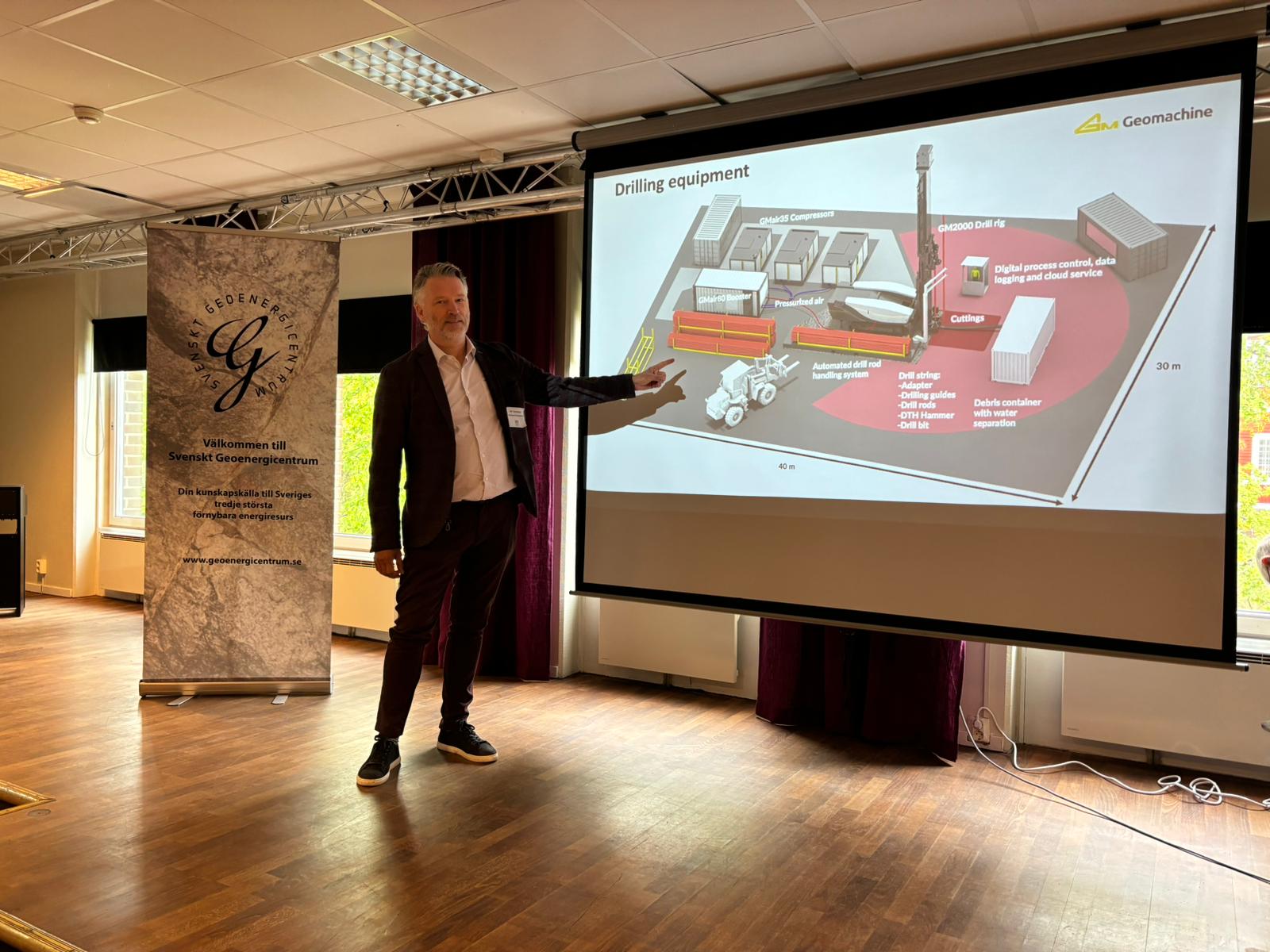
Documentation
When considering the development of work machinery, good product documentation is often not the most glamorous or trendy aspect to focus on. However, easy access to information can significantly improve the user experience, operational efficiency, and safety of the machine. Documentation also serves as the backbone of communication between the machine’s user and manufacturer, thereby enhancing not only the operation of the machine but also speeding up the resolution of any issues.
At Geomachine, over the course of a year-long project, we have elevated our user, maintenance, and spare parts documentation to a new level. We began with the development projects of new products, including the GM2000 geothermal drilling rig, the GM22S stabilization rig, and the GMair35 compressor. At the same time, we have also focused on the documentation for ground investigation rigs, and the updated documentation package is now included with all machines delivered from the beginning of this year.
We have thoroughly reviewed the user manuals with an emphasis on safe and efficient operation. The manuals are organized into clear sections at a main level, such as safety, operation, and transportation. The manuals include step-by-step instructions for operating the machine, as well as general and case-specific safety precautions. We have also invested in illustrative visual materials to make the information as easy to understand as possible.
The maintenance instructions are based on years of experience, proven maintenance practices, and the requirements specified by the suppliers of the machine’s various components. Special attention has been paid to daily and frequently recurring maintenance tasks. For example, lubrication points are clearly illustrated with images.
Spare parts manuals are created individually for each machine unit according to a new process, ensuring that the specific differences between machines are taken into account and that the correct parts can be quickly and easily found for each machine. The manuals aim to include the machine’s structure as comprehensively as possible, so that the appropriate part or assembly can be located effortlessly.
The updated documentation is delivered with the machines and is also available in Geomachine’s cloud service, where it is always easily accessible to the customer.
Interested? Contact Geomachine!
GM2000
The GM2000 geothermal well drilling rig has been in action at the Lounavoima Waste-to-Energy plant in Salo, Finland for quite some time now. So, it’s the perfect moment to assess how the rig has been performing on-site in real life.
“We are now in a situation where the third well, drilled with the GM2000 rig, is completed at a depth of 2000 meters,” says QHeat operator Hannu Ylitalo. “In total, there is four wells finished now, as we drilled the first one with another brand’s rig.”
Hannu Ylitalo has been involved in the Lounavoima project since the drilling of the first 2000-meter deep well began. “The first well was drilled at the Lounavoima site in 2021. It was 1600 meters deep. After that, we started using the Geomachine GM2000 rig for the drilling.”
The first one makes adjustments
The GM2000 rig is the first in the world specifically designed for drilling geothermal wells at a depth of 2000 meters. At the Lounavoima site, it was understood that pioneering this technology would require learning new skills and likely adjusting the rig to achieve optimal drilling efficiency. “I knew in advance that since this was the first machine of its model series, we as its first users, would be part of its product development process.”
Hannu Ylitalo was there when the new rig was put into operation. “I was involved in the commissioning of the GM2000 rig. Its transfer to the drilling site was easy, and setting up the booms was straightforward. At first, we made many adjustments, but gradually the drilling process started to streamline.”
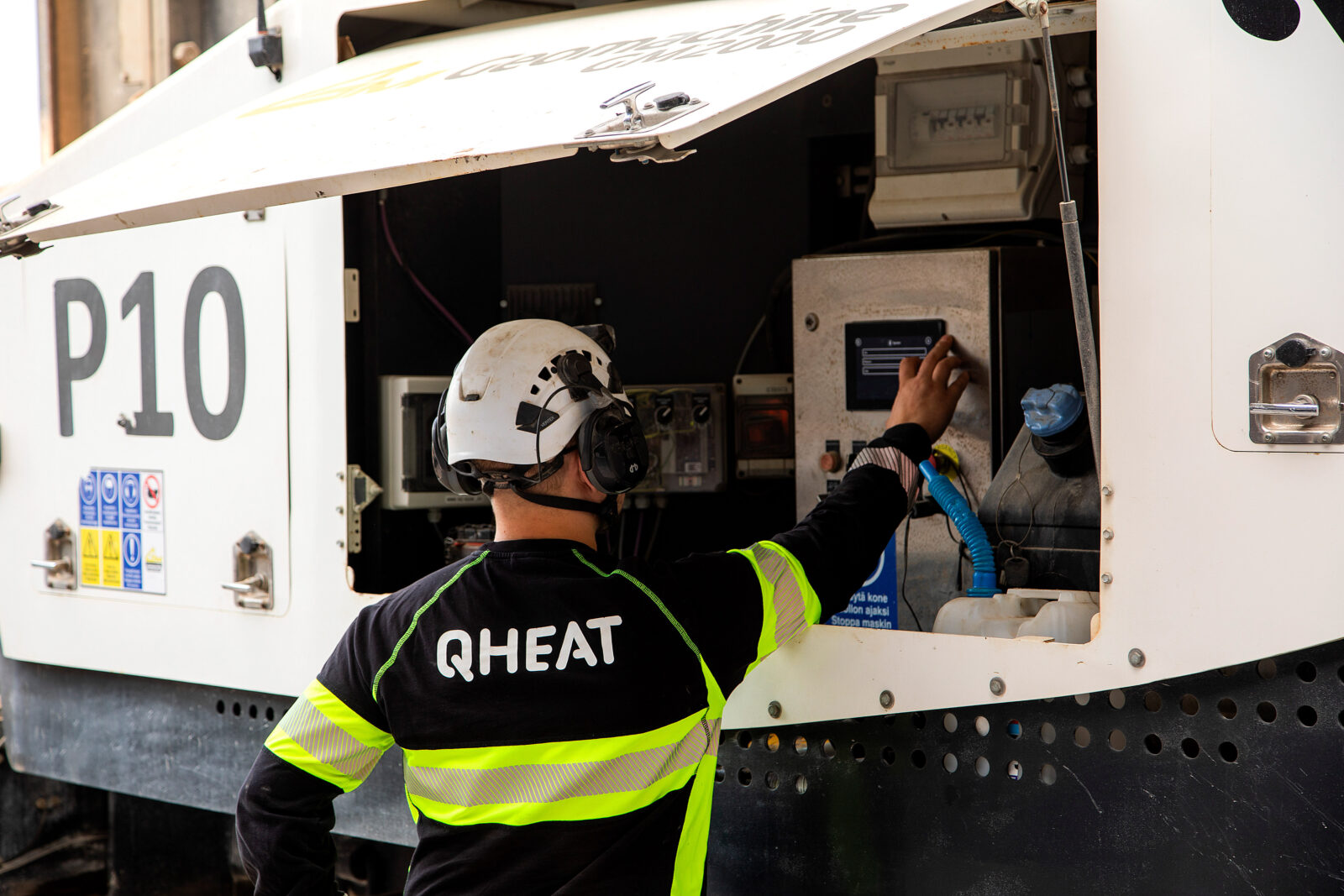
Success is a combination of many factors
The progress of the drilling process is largely dependent on what is found beneath the surface. “In our case, the bedrock is such that the rock material turns into fine powder during drilling. If water enters the well, the rock material turns into sludge and adheres to the walls of the well. When the borehole becomes narrow due to this, the air pressure in the well starts to rise, making drilling difficult without adjusting the machine. The collapse of the well walls also naturally slows down the drilling process.”
According to Hannu Ylitalo, the GM2000 rig has one feature that stands out in anticipating what happens beneath the surface. “Geomachine’s GMTracker data-logger is an invaluable tool for the driller, as it makes visible what cannot be seen with the eye and the ear cannot hear. By being aware of the bedrock conditions during drilling, regardless of the drilling depth, the machine can be adjusted in advance to suit the conditions. This way, equipment damage can be avoided, for example. Without the data-logger, drilling would be practically blind and hit-or-miss.”
Comfort and safety in work
In addition to the GMTracker, Hannu Ylitalo wants to highlight two other features of the GM2000 rig. “The remote control of the machine significantly enhances comfort and safety while working. The rig can be operated from a site cabin, which is especially nice when working in poor weather conditions. Another really good feature relates to rod handling. The opening and tightening of rod connections have been made easy with a hydraulic clamp and a sliding rod holder. The compressed air released when opening connections is directed to the back of the machine through silencers. This greatly increases the smoothness and safety of the work, as there can be up to 80 bar of pressure inside the drill rod.”
According to Hannu Ylitalo, the physical workload when drilling with the GM2000 rig has significantly decreased. “This machine is really pleasant to use. The only area where we still do some physical work is in handling the rods. However, it is known that in the future, this will also be eliminated for the operators, as an automatic rod handling system will be available for the GM2000 rig.”
Pioneering collaboration
Even though drilling at the early stages of the Lounavoima project involved a lot of new learning, working as a pioneer in a renewable energy project has been a rewarding experience for Hannu Ylitalo. “We are constantly learning new things, and it’s gratifying to see that drilling is becoming smoother all the time. Currently, the challenges that arise are related to the bedrock, not so much the drilling rig itself. And these challenges can never be completely anticipated in advance.”
The collaboration with Geomachine has been a key aspect of learning new things and streamlining the process. “It has been important that we have had the necessary support available at all times. We have received answers to our questions quickly, and through collaboration, we have gradually learned more about the drilling process, allowing us to drill wells more smoothly and with quicker turnaround times.”
Interested? Contact Geomachine!
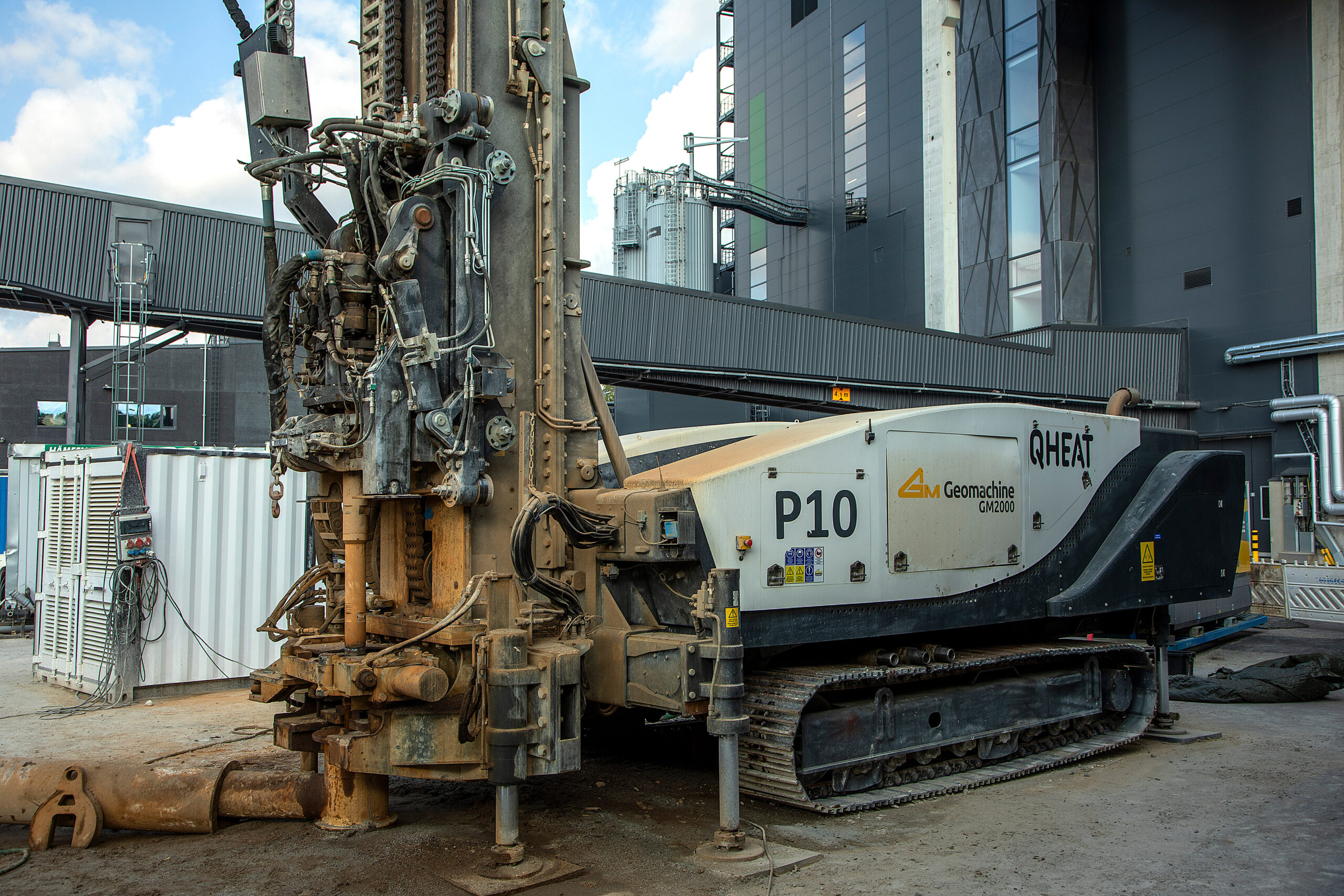
GM2000
Lounavoima’s Waste-to-Energy plant in Salo, Finland wants to improve the utilization of the waste and the excess heat. This is being done by storing the heat in wells drilled to a depth of 2000 meters.
“Increasing the waste utilization rate and storing excess heat were on Lounavoima’s agenda already in 2018 when I joined the company,” begins Petri Onikki, CEO of Lounavoima and Salo District Heating. “It was known that the plant produced excess heat, and various possibilities for utilizing this heat were already being explored.”
While investigating the implementation options for the project, Lounavoima also explored the new well-drilling technology developed by QHeat. “This solution seemed most suitable for us, and once we received an investment grant from the Ministry of Economic Affairs and Employment, the project really got going in 2021.”
Pioneer recognizes the risks
When something is done for the first time in the world, it must be accepted that not everything can be known in advance. “There were many uncertainties associated with drilling a 2000-meter-deep well. We started to drill with Geomachine’s GM2000 drilling rig, which was the first machine specifically designed for drilling wells of this depth. We knew that once we’d start using it, adjustments and configurations would inevitably be needed. Another risk when going underground is, of course, that you can never fully predict what you might encounter there.”
Despite the uncertainties, it was decided to proceed with the project. “We moved forward by minimizing risks as effectively as possible. We drilled the first well purely with the mindset that it was a demo well. Based on the data and calculations we gathered from the drilling process, we could then plan the drilling of the next wells.”
Decisions regarding the scope of the project were made as it progressed. “Once we had completed and partially brought three wells into production, it was easy for us to decide to drill the next three. We’ve always been aware that we are pioneers in this project, so we’ve approached it with caution. We’ve continued the project based on the results we’ve obtained during the work process. This approach has proven to be very effective.”
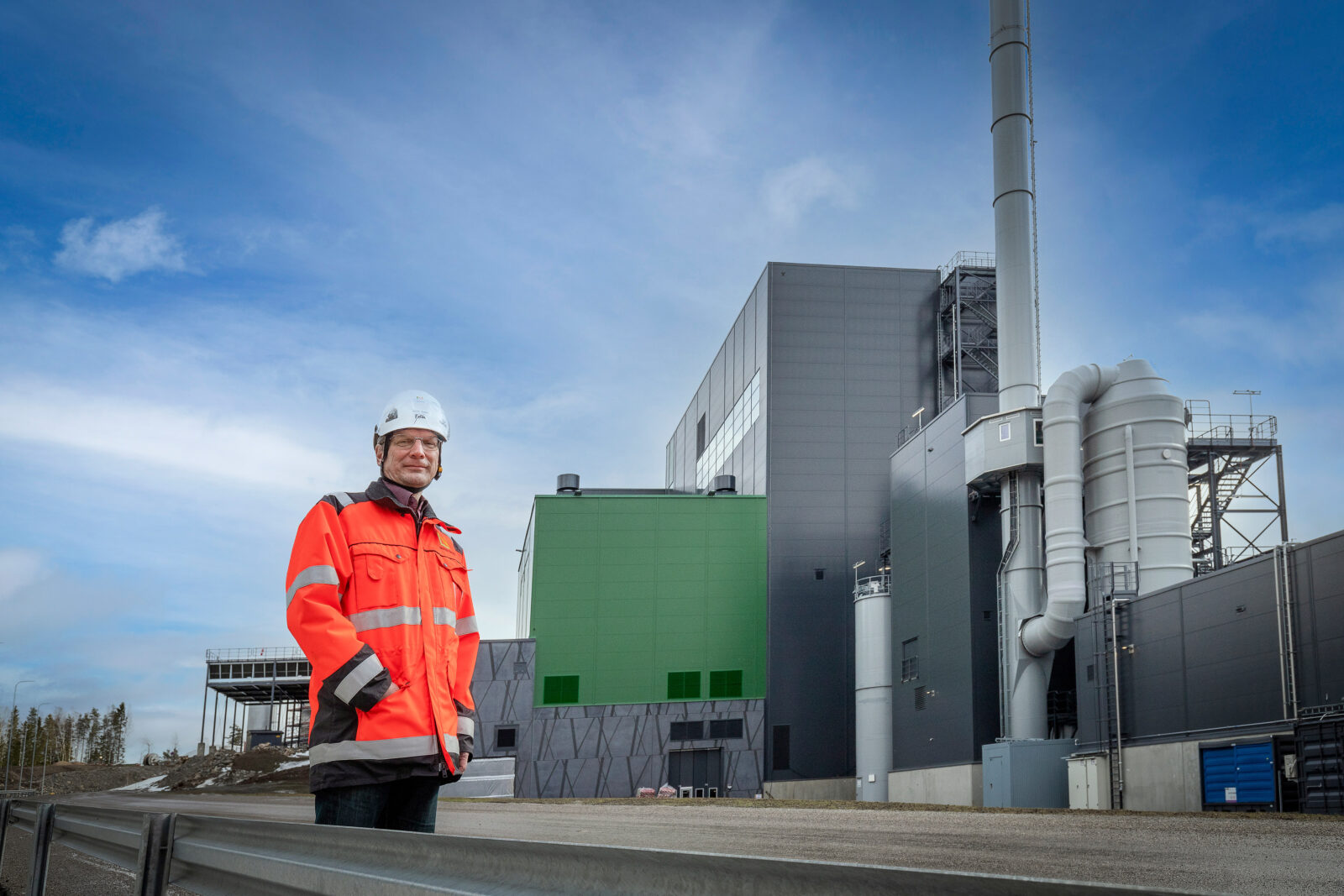
On track towards the goal
Lounavoima’s project has progressed as expected, and soon the fourth 2000-meter-deep well will be operational. “As we’ve gained more drilling experience with the GM2000 rig, the drilling time has shortened. In this project, every party involved has learned something new along the way and will undoubtedly benefit from this knowledge in the future.”
The project is well on its way, with only two wells left to drill. Once all six wells are operational, it is possible to start reaping the benefits. “Naturally, we expect the project to start paying for itself in terms of our business figures. We also hope it will have a positive impact on our district heating customers. In a situation where rising costs are constantly pressuring the energy sector, we hope that utilizing excess heat will help us keep our pricing competitive. Perhaps we’ll soon be able to offer a solution to district heating customers who want to source all their energy from environmentally friendly excess heat.”
A sustainable and smart heating solution for tomorrow
Lounavoima’s project is unique, as apparently nothing like it has been implemented elsewhere in the world before. “This project will surely serve as an inspiring example for all countries with high energy demands due to cold climates. In addition to storing excess heat, deep wells can naturally serve as an inexhaustible source of energy. Now that we’ve seen that drilling wells to 2000 meters is practically feasible, interest in this topic will surely grow.”
The numbers also support the use of geothermal wells. “Once we complete our energy storage system consisting of six wells, we will be able to heat 700 single-family homes annually with the excess heat stored in them. Utilizing the full potential of these wells will also have a direct impact on our carbon dioxide emissions, which will decrease by 2000–3000 tons annually. This is a very significant number for the Salo area, as opportunities for reducing emissions are quite limited.”
Boldly moving forward
The district heating industry is constantly seeking new solutions for transitioning from fossil fuels to renewables. Both nationally and at the EU level, there is increasing pressure to adopt greener alternatives. Public discourse also increasingly demands better consideration for the environment.
Petri Onikki encourages the energy sector to boldly explore and adopt the possibilities of geothermal energy. “I believe that the geothermal well project is worth considering for all energy companies looking to operate more environmentally friendly, cost-effectively, and competitively in the eyes of consumers. At Lounavoima, we have tested the functionality of this technology as pioneers, and we know that drilling 2000-meter-deep wells is feasible today with standardized and smart costs. Now that the solution has been proven to work in practice, it’s easier also for others to implement it in their own businesses.”
Interested? Contact Geomachine!
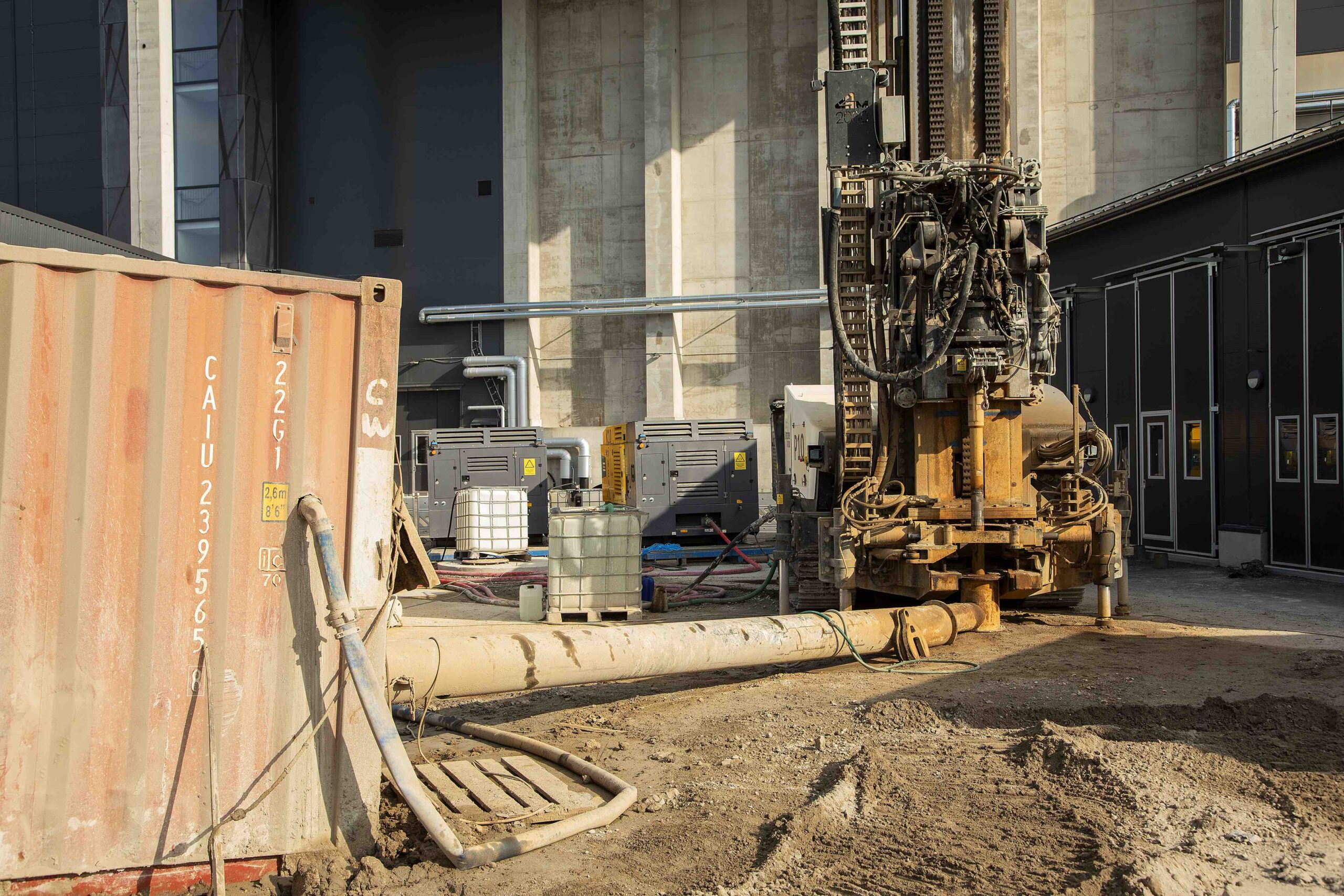