Kategoriat
Geomachine
Geomachine is a company deeply committed to product development. At the core of every innovation lies a profound understanding of customer needs, the unresolved challenges within the industry, and the future directions of the field.
The guiding principle of Geomachine’s product development is to create solutions that genuinely meet its customers’ needs. To deepen its customer insight, Geomachine engages in close discussions with professionals in the geotechnical investigation and well-drilling sectors. This collaborative approach was pivotal also in developing the GM2000 drilling rig, designed specifically for deep geothermal well drilling.
To dive into the world of geothermal wells, Geomachine collaborated with consultant Jukka Ahonen. Ahonen’s expertise spans various drilling and piling methods, from anchoring to rotary drilling and quarry techniques ranging from precision holes for dimension stone to large-scale hammer drilling and shaft sinking.
“I have been involved in numerous mining projects, hydroelectric construction sites, and challenging foundation reinforcement projects around the world,” begins Jukka Ahonen. “In the well-drilling industry, I have worked for decades both in Finland and abroad, particularly in the Middle East, North America, and South America. My comprehensive understanding of the field has been built through hands-on experience, research, and especially through collaboration with local drilling professionals, who are the true experts in the field.”
The changing landscape of well drilling
According to Ahonen, the well-drilling industry has undergone significant changes in recent years. “Households have become more urbanized, and people now live in areas where municipalities provide water supply and wastewater infrastructure. Private households no longer find it worthwhile to maintain their own wells, making the drilling of traditional water wells for households increasingly rare. In contrast, vacation homes and farms, especially dairy farms, continue to invest in drilled well water.”
Global trends also influence the well-drilling sector, with the increasing demand for renewable energy being a major driver. As a result, the focus has shifted significantly towards drilling geothermal wells. “Today, 70–80% of new buildings rely on geothermal energy for heating. Geothermal wells have also been adopted as a heating solution for large new construction projects, such as halls, shopping centers, and factories.”
In densely built urban areas, one major challenge in utilizing geothermal energy has been the limited availability of land. “Previously, to meet the energy needs of a large property it has been necessary to drill for example 150 shallow wells. In densely built areas, this has naturally been challenging, if not impossible. Therefore, there has been a real need for deeper wells.”
Currently, a 2,000-meter-deep geothermal well is considered the most economically viable option, and thanks to QHeat and Geomachine, cost-efficient drilling to such depths is now possible. “The overall cost-effectiveness of a well is not only influenced by the drilling costs but also on how efficiently heat can be extracted from the well without losses. QHeat and Geomachine have successfully addressed this challenge.”
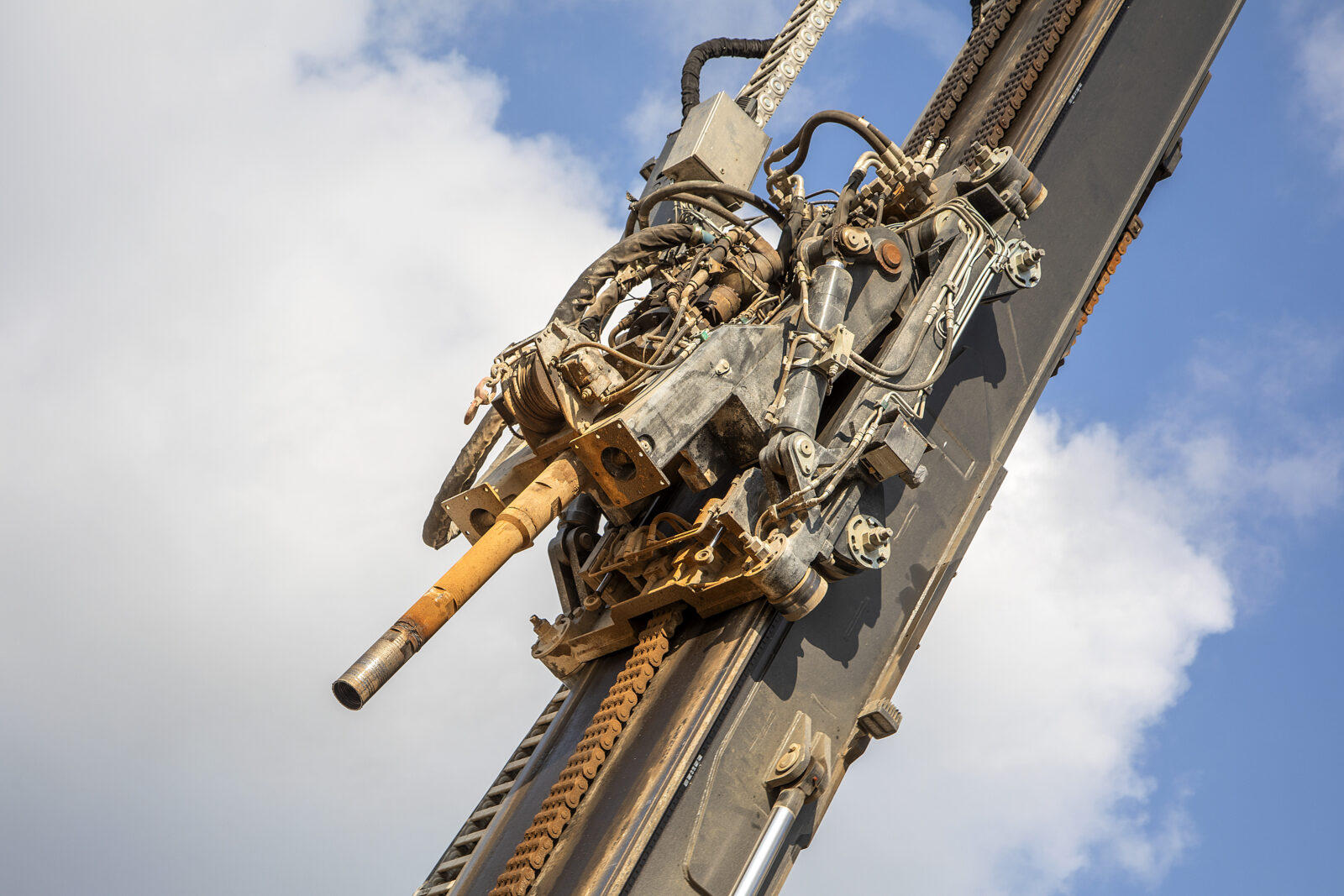
Unique challenges of deep geothermal well drilling
The Scandinavian bedrock is a slab of granite and other deep-rock types, hundreds of kilometers thick. Ahonen notes that in this ancient, folded, and layered bedrock, drilling conditions vary significantly as the depth increases. “Even in hard bedrock, there are fault zones, and within the first 500 meters, there is usually a lot of groundwater. Faults and high water inflow can cause the well walls to collapse. In the GM2000 solution, this challenge is mitigated by reinforcing the well walls with a casing for the first 500 meters. Besides preserving the well’s structure, wall reinforcement also serves another critical purpose: it acts as a surface water barrier, preventing unwanted substances from entering the groundwater.”
Water present in the bedrock also affects the drilling process. “Within the first 500 meters, encountered water can be under high pressure, ranging from 40 to 50 bar depending on rock fractures. This means the compressors used in drilling need to handle higher pressures than before. The GM2000 solution ensures a stable air supply by enhancing compressor performance with a dedicated high-pressure booster.”
To maximize cost-efficiency, it is essential to drill continuously without interruptions. “When drilling stops at the end of a shift, the well begins to fill with water. This means the well must first be emptied before drilling can resume. Developing faster methods for well-emptying is one area of future product development. Another focus is creating quieter drilling methods, which would enable 24/7 drilling without noise disturbances.”
Drilling brings up significant amounts of groundwater, which must also be managed. “The solids content in the groundwater must not exceed 300 mg/l. The water must either be transported off-site or treated before being discharged into the sewage system. Developing advanced water treatment systems is another key focus for deep-well drilling product development.”
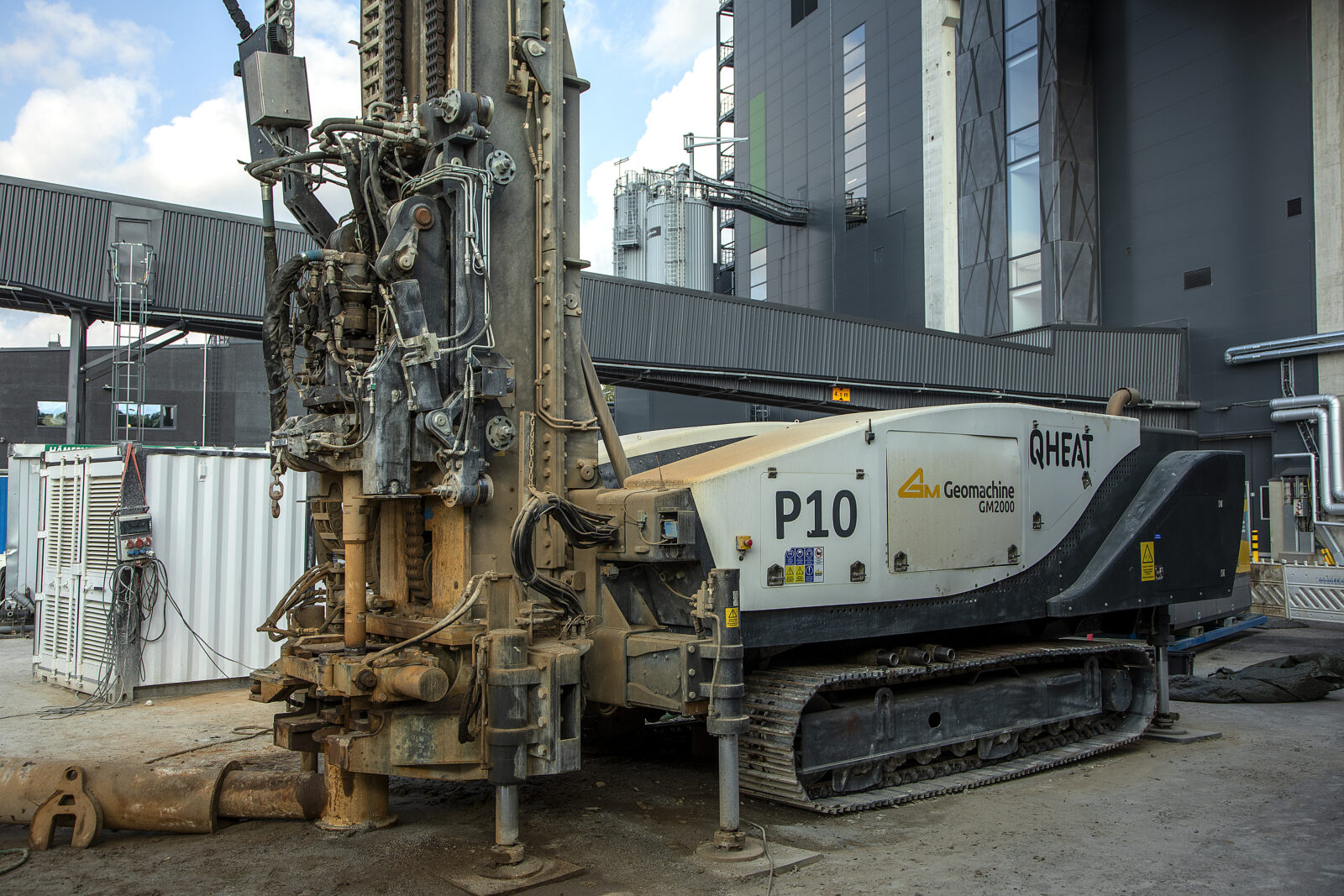
Increasing demand for renewable energy
Geothermal energy is highly likely to grow in popularity in the future. “The drive for energy self-sufficiency is intensifying. In Sweden, for example, interest in property-specific geothermal wells has surged due to the volatility of electricity prices.”
One of the challenges for the future is how to drill wells in confined environments, such as from within existing buildings. “In Canada, for example, there have already been attempts to develop new drilling and collector solutions for such scenarios.”
To make geothermal energy accessible for a wide range of properties, it’s essential to consider which well solution best suits each case—depth isn’t always the key factor. “Shallow wells are suitable for areas with fractured, water-rich bedrock, while deep wells are a good solution when the bedrock is homogeneous and relatively dry.”
Ahonen believes that drilling deep geothermal wells will continue to become more efficient. “Drilling to depths of 300–400 meters was still a significant challenge twenty years ago, but today it has become routine. Progress has been remarkable and will continue. Thanks to QHeat and Geomachine, we now have a solution that makes deep drilling cost-effective and replicable. The results achieved at the Salo Waste-to-Energy plant are very promising and suggest great potential for the future.”
Interested? Contact Geomachine!
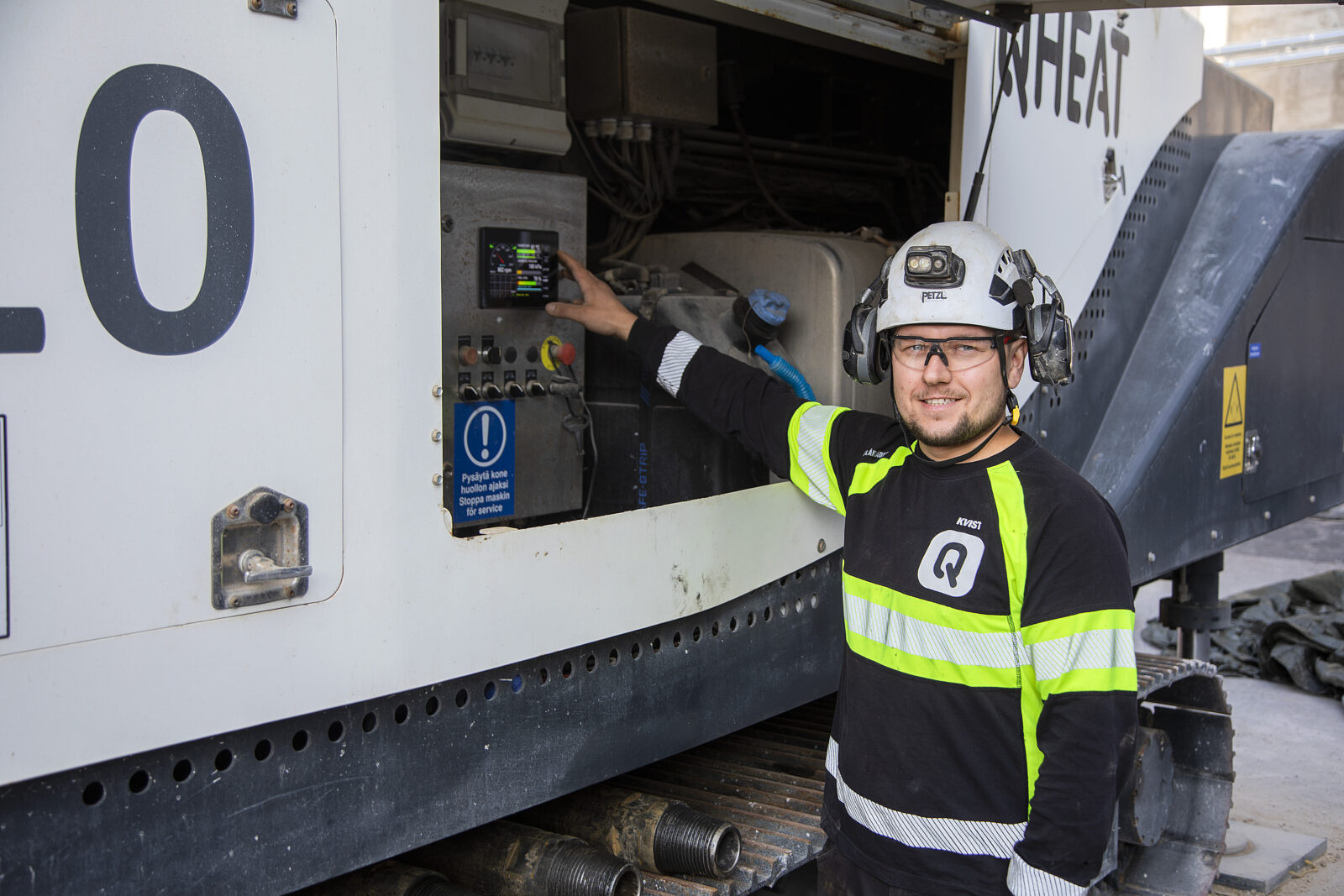
Geoenergidagen
Geomachine wants to actively engage in the discussion on renewable energy. For this reason, it often participates in the events that are organized on this topic worldwide.
“In the beginning of October 2024 we participated in the Geoenergidagen event, held in Nynäshamn, Sweden,” says Ari Kuhalampi, Product Line Director at Geomachine. “The two-day event brought together some of the most prominent players in the geoenergy sector from around Sweden and the Nordic countries.”
Geomachine focused on highlighting the unique features of the GM2000 drilling solution during its presentation. “Drilling geothermal wells has truly become replicable and cost-effective thanks to our GM2000 solution. The required area for drilling is minimal, just a 30m x 40m space is enough. The equipment is easy to set-up and transport. The actual drilling, machine control, and drilling progress monitoring are made possible with the GMTracker data-logger.”
According to Ari Kuhalampi, the efficiency of the drilling process and, therefore, the timely completion of the well is based on the phased drilling process. “In the first phase, the attention is paid to surface layer, then the water, and in the final phase, drilling is carried out to the target depth using data collected by the GMTracker data-logger. Using the latest IoT and cloud technologies this information can also be saved and shared in real-time with everyone who needs it.”
According to Ari Kuhalampi, another factor contributing to the cost-effectiveness of the drilling process is how the machines are maintained. “At Geoenergidagen, we also introduced Geomachine’s GMCare maintenance service, which helps shift from reactive to predictive maintenance of drilling equipment. When the necessary maintenance can be done systematically and by communicating efficiently with the service, the utilization rate and productivity of the machines can be maximized.”
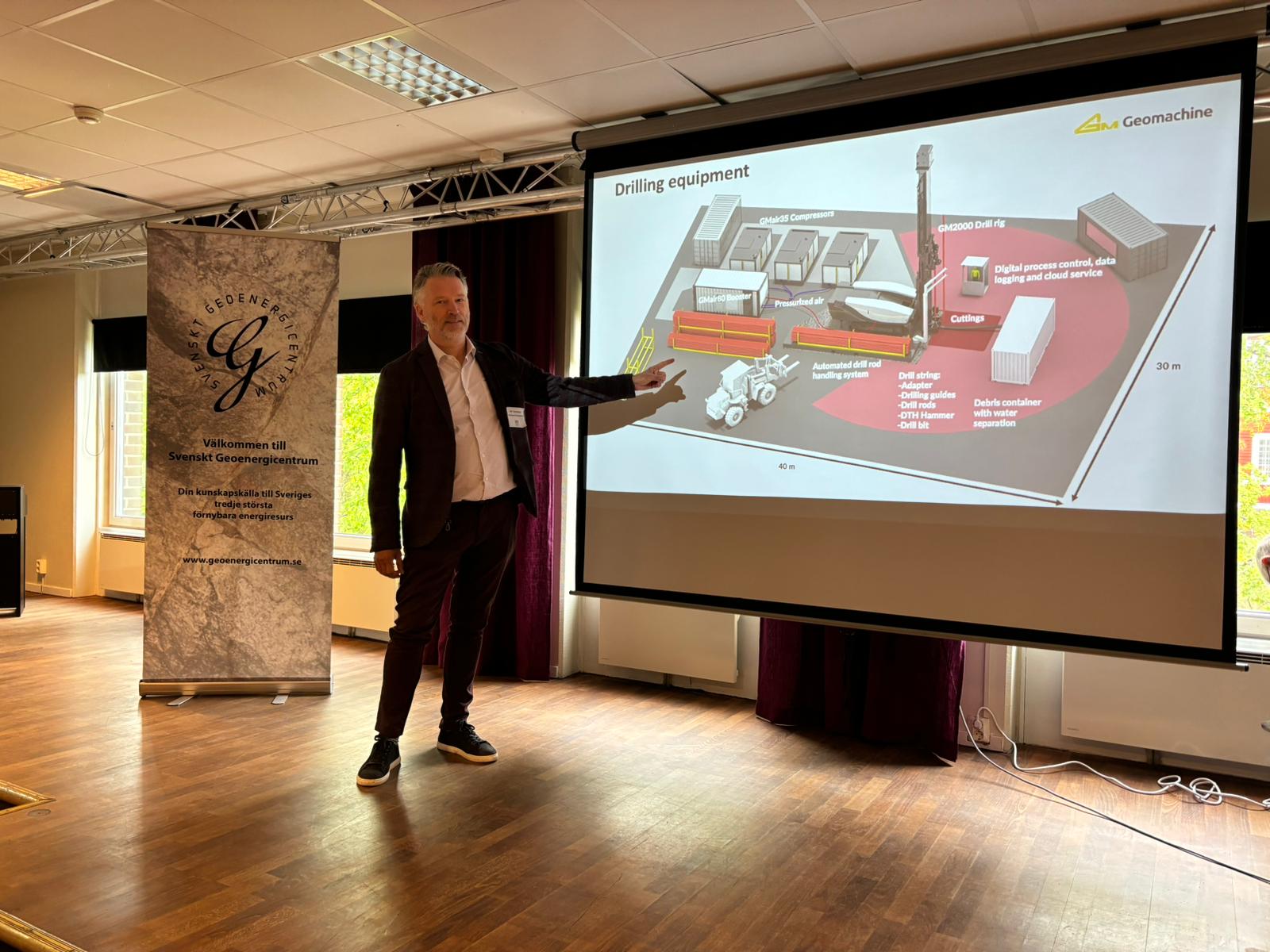
GM2000
The GM2000 geothermal well drilling rig has been in action at the Lounavoima Waste-to-Energy plant in Salo, Finland for quite some time now. So, it’s the perfect moment to assess how the rig has been performing on-site in real life.
“We are now in a situation where the third well, drilled with the GM2000 rig, is completed at a depth of 2000 meters,” says QHeat operator Hannu Ylitalo. “In total, there is four wells finished now, as we drilled the first one with another brand’s rig.”
Hannu Ylitalo has been involved in the Lounavoima project since the drilling of the first 2000-meter deep well began. “The first well was drilled at the Lounavoima site in 2021. It was 1600 meters deep. After that, we started using the Geomachine GM2000 rig for the drilling.”
The first one makes adjustments
The GM2000 rig is the first in the world specifically designed for drilling geothermal wells at a depth of 2000 meters. At the Lounavoima site, it was understood that pioneering this technology would require learning new skills and likely adjusting the rig to achieve optimal drilling efficiency. “I knew in advance that since this was the first machine of its model series, we as its first users, would be part of its product development process.”
Hannu Ylitalo was there when the new rig was put into operation. “I was involved in the commissioning of the GM2000 rig. Its transfer to the drilling site was easy, and setting up the booms was straightforward. At first, we made many adjustments, but gradually the drilling process started to streamline.”
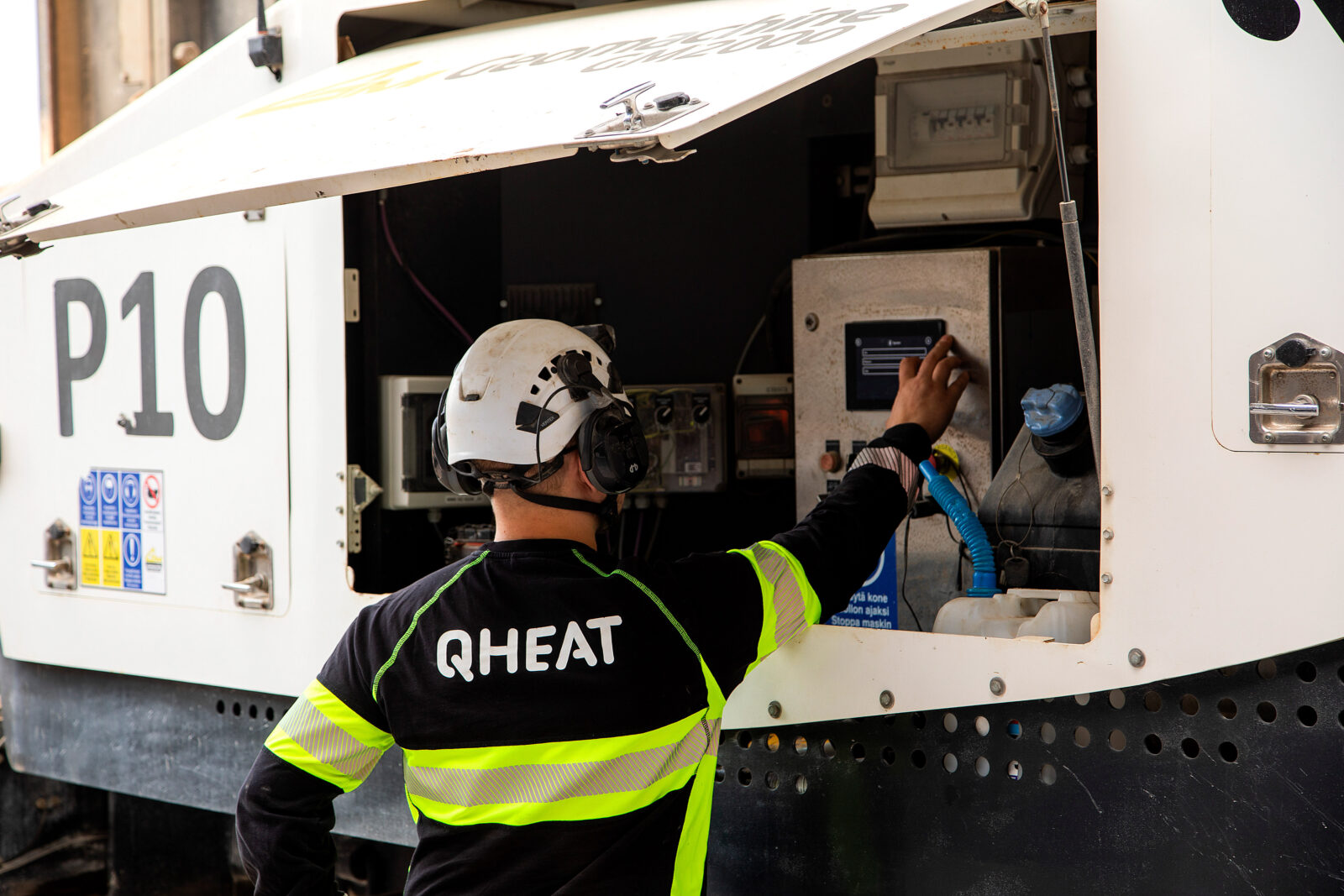
Success is a combination of many factors
The progress of the drilling process is largely dependent on what is found beneath the surface. “In our case, the bedrock is such that the rock material turns into fine powder during drilling. If water enters the well, the rock material turns into sludge and adheres to the walls of the well. When the borehole becomes narrow due to this, the air pressure in the well starts to rise, making drilling difficult without adjusting the machine. The collapse of the well walls also naturally slows down the drilling process.”
According to Hannu Ylitalo, the GM2000 rig has one feature that stands out in anticipating what happens beneath the surface. “Geomachine’s GMTracker data-logger is an invaluable tool for the driller, as it makes visible what cannot be seen with the eye and the ear cannot hear. By being aware of the bedrock conditions during drilling, regardless of the drilling depth, the machine can be adjusted in advance to suit the conditions. This way, equipment damage can be avoided, for example. Without the data-logger, drilling would be practically blind and hit-or-miss.”
Comfort and safety in work
In addition to the GMTracker, Hannu Ylitalo wants to highlight two other features of the GM2000 rig. “The remote control of the machine significantly enhances comfort and safety while working. The rig can be operated from a site cabin, which is especially nice when working in poor weather conditions. Another really good feature relates to rod handling. The opening and tightening of rod connections have been made easy with a hydraulic clamp and a sliding rod holder. The compressed air released when opening connections is directed to the back of the machine through silencers. This greatly increases the smoothness and safety of the work, as there can be up to 80 bar of pressure inside the drill rod.”
According to Hannu Ylitalo, the physical workload when drilling with the GM2000 rig has significantly decreased. “This machine is really pleasant to use. The only area where we still do some physical work is in handling the rods. However, it is known that in the future, this will also be eliminated for the operators, as an automatic rod handling system will be available for the GM2000 rig.”
Pioneering collaboration
Even though drilling at the early stages of the Lounavoima project involved a lot of new learning, working as a pioneer in a renewable energy project has been a rewarding experience for Hannu Ylitalo. “We are constantly learning new things, and it’s gratifying to see that drilling is becoming smoother all the time. Currently, the challenges that arise are related to the bedrock, not so much the drilling rig itself. And these challenges can never be completely anticipated in advance.”
The collaboration with Geomachine has been a key aspect of learning new things and streamlining the process. “It has been important that we have had the necessary support available at all times. We have received answers to our questions quickly, and through collaboration, we have gradually learned more about the drilling process, allowing us to drill wells more smoothly and with quicker turnaround times.”
Interested? Contact Geomachine!
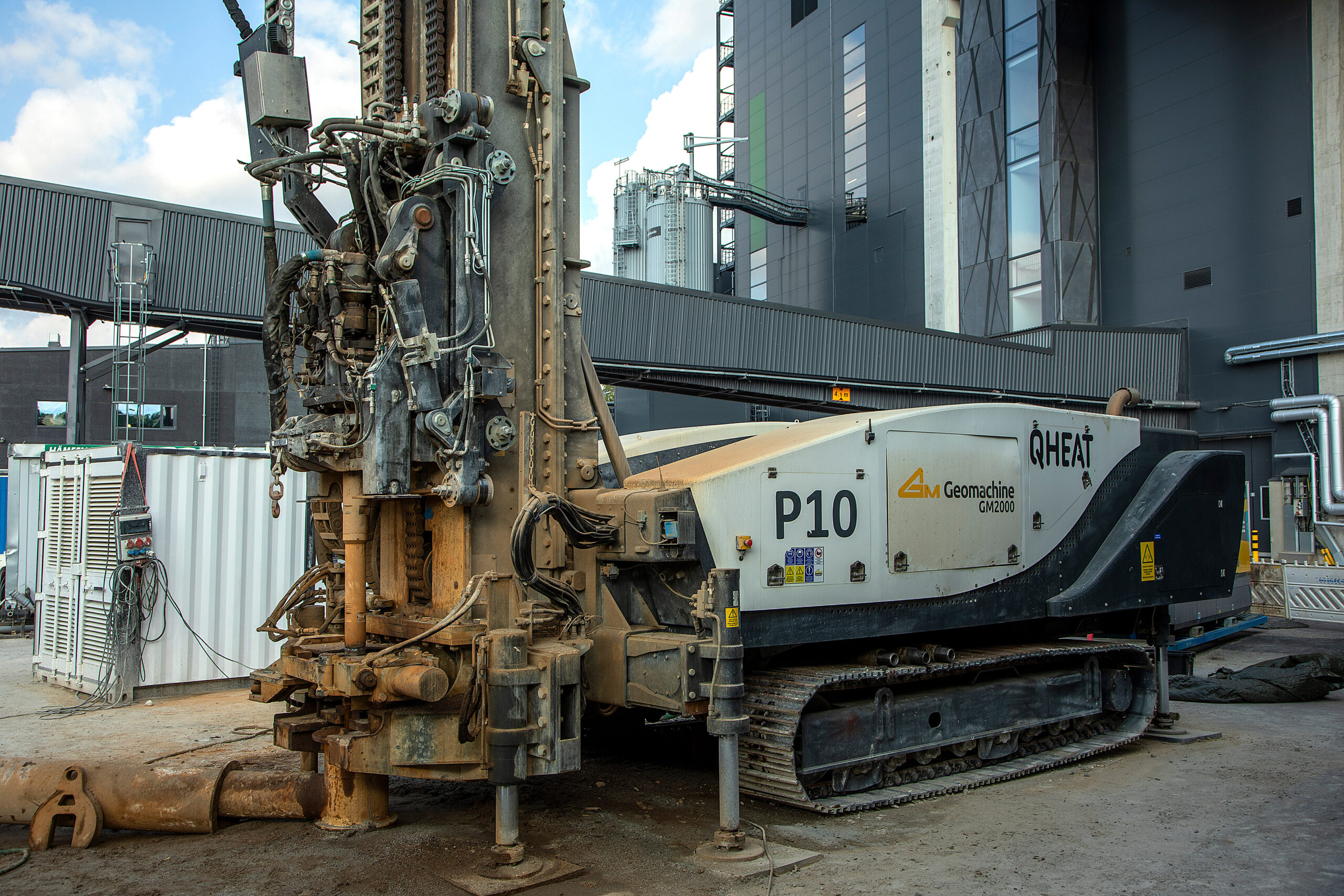
GM2000
Lounavoima’s Waste-to-Energy plant in Salo, Finland wants to improve the utilization of the waste and the excess heat. This is being done by storing the heat in wells drilled to a depth of 2000 meters.
“Increasing the waste utilization rate and storing excess heat were on Lounavoima’s agenda already in 2018 when I joined the company,” begins Petri Onikki, CEO of Lounavoima and Salo District Heating. “It was known that the plant produced excess heat, and various possibilities for utilizing this heat were already being explored.”
While investigating the implementation options for the project, Lounavoima also explored the new well-drilling technology developed by QHeat. “This solution seemed most suitable for us, and once we received an investment grant from the Ministry of Economic Affairs and Employment, the project really got going in 2021.”
Pioneer recognizes the risks
When something is done for the first time in the world, it must be accepted that not everything can be known in advance. “There were many uncertainties associated with drilling a 2000-meter-deep well. We started to drill with Geomachine’s GM2000 drilling rig, which was the first machine specifically designed for drilling wells of this depth. We knew that once we’d start using it, adjustments and configurations would inevitably be needed. Another risk when going underground is, of course, that you can never fully predict what you might encounter there.”
Despite the uncertainties, it was decided to proceed with the project. “We moved forward by minimizing risks as effectively as possible. We drilled the first well purely with the mindset that it was a demo well. Based on the data and calculations we gathered from the drilling process, we could then plan the drilling of the next wells.”
Decisions regarding the scope of the project were made as it progressed. “Once we had completed and partially brought three wells into production, it was easy for us to decide to drill the next three. We’ve always been aware that we are pioneers in this project, so we’ve approached it with caution. We’ve continued the project based on the results we’ve obtained during the work process. This approach has proven to be very effective.”
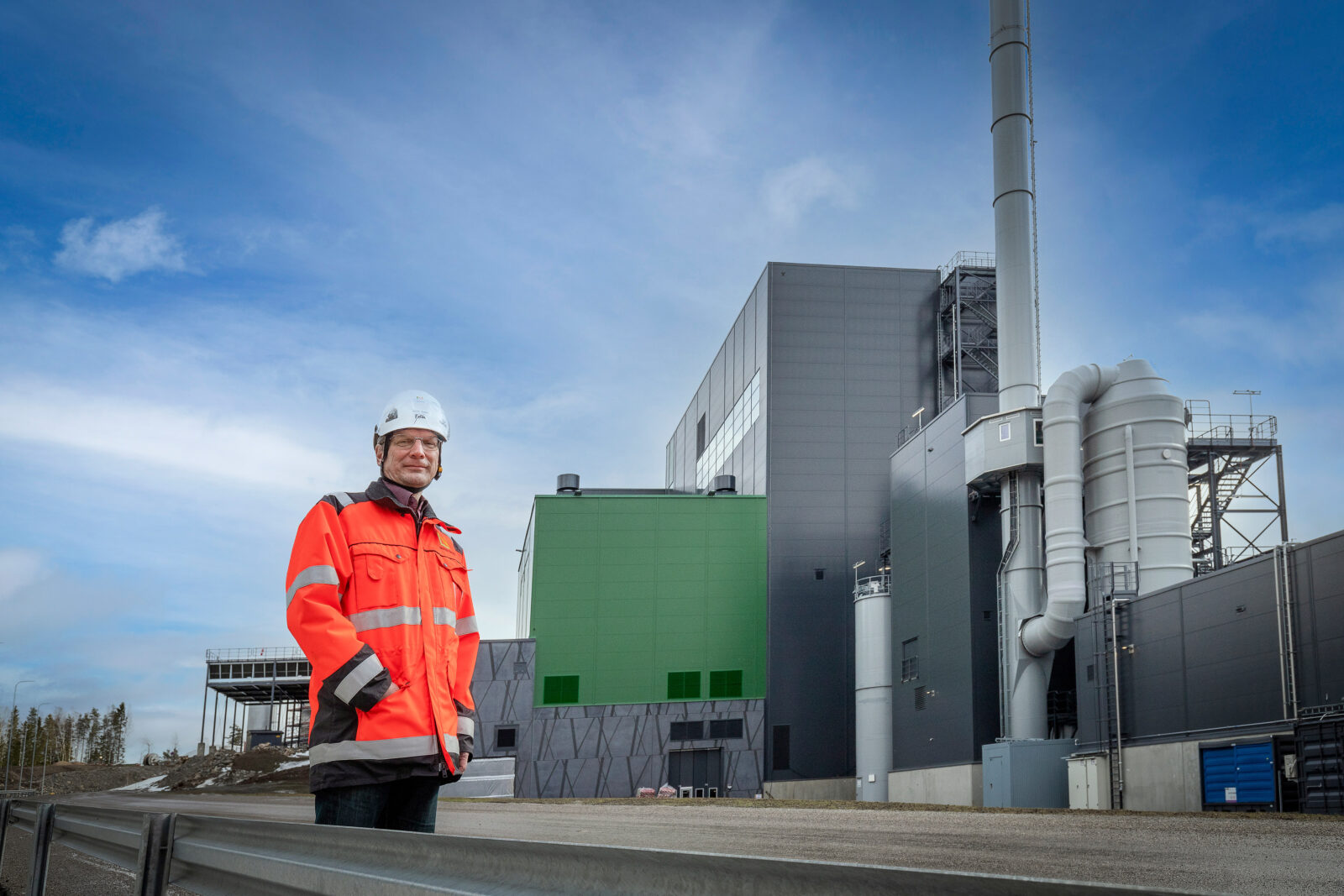
On track towards the goal
Lounavoima’s project has progressed as expected, and soon the fourth 2000-meter-deep well will be operational. “As we’ve gained more drilling experience with the GM2000 rig, the drilling time has shortened. In this project, every party involved has learned something new along the way and will undoubtedly benefit from this knowledge in the future.”
The project is well on its way, with only two wells left to drill. Once all six wells are operational, it is possible to start reaping the benefits. “Naturally, we expect the project to start paying for itself in terms of our business figures. We also hope it will have a positive impact on our district heating customers. In a situation where rising costs are constantly pressuring the energy sector, we hope that utilizing excess heat will help us keep our pricing competitive. Perhaps we’ll soon be able to offer a solution to district heating customers who want to source all their energy from environmentally friendly excess heat.”
A sustainable and smart heating solution for tomorrow
Lounavoima’s project is unique, as apparently nothing like it has been implemented elsewhere in the world before. “This project will surely serve as an inspiring example for all countries with high energy demands due to cold climates. In addition to storing excess heat, deep wells can naturally serve as an inexhaustible source of energy. Now that we’ve seen that drilling wells to 2000 meters is practically feasible, interest in this topic will surely grow.”
The numbers also support the use of geothermal wells. “Once we complete our energy storage system consisting of six wells, we will be able to heat 700 single-family homes annually with the excess heat stored in them. Utilizing the full potential of these wells will also have a direct impact on our carbon dioxide emissions, which will decrease by 2000–3000 tons annually. This is a very significant number for the Salo area, as opportunities for reducing emissions are quite limited.”
Boldly moving forward
The district heating industry is constantly seeking new solutions for transitioning from fossil fuels to renewables. Both nationally and at the EU level, there is increasing pressure to adopt greener alternatives. Public discourse also increasingly demands better consideration for the environment.
Petri Onikki encourages the energy sector to boldly explore and adopt the possibilities of geothermal energy. “I believe that the geothermal well project is worth considering for all energy companies looking to operate more environmentally friendly, cost-effectively, and competitively in the eyes of consumers. At Lounavoima, we have tested the functionality of this technology as pioneers, and we know that drilling 2000-meter-deep wells is feasible today with standardized and smart costs. Now that the solution has been proven to work in practice, it’s easier also for others to implement it in their own businesses.”
Interested? Contact Geomachine!
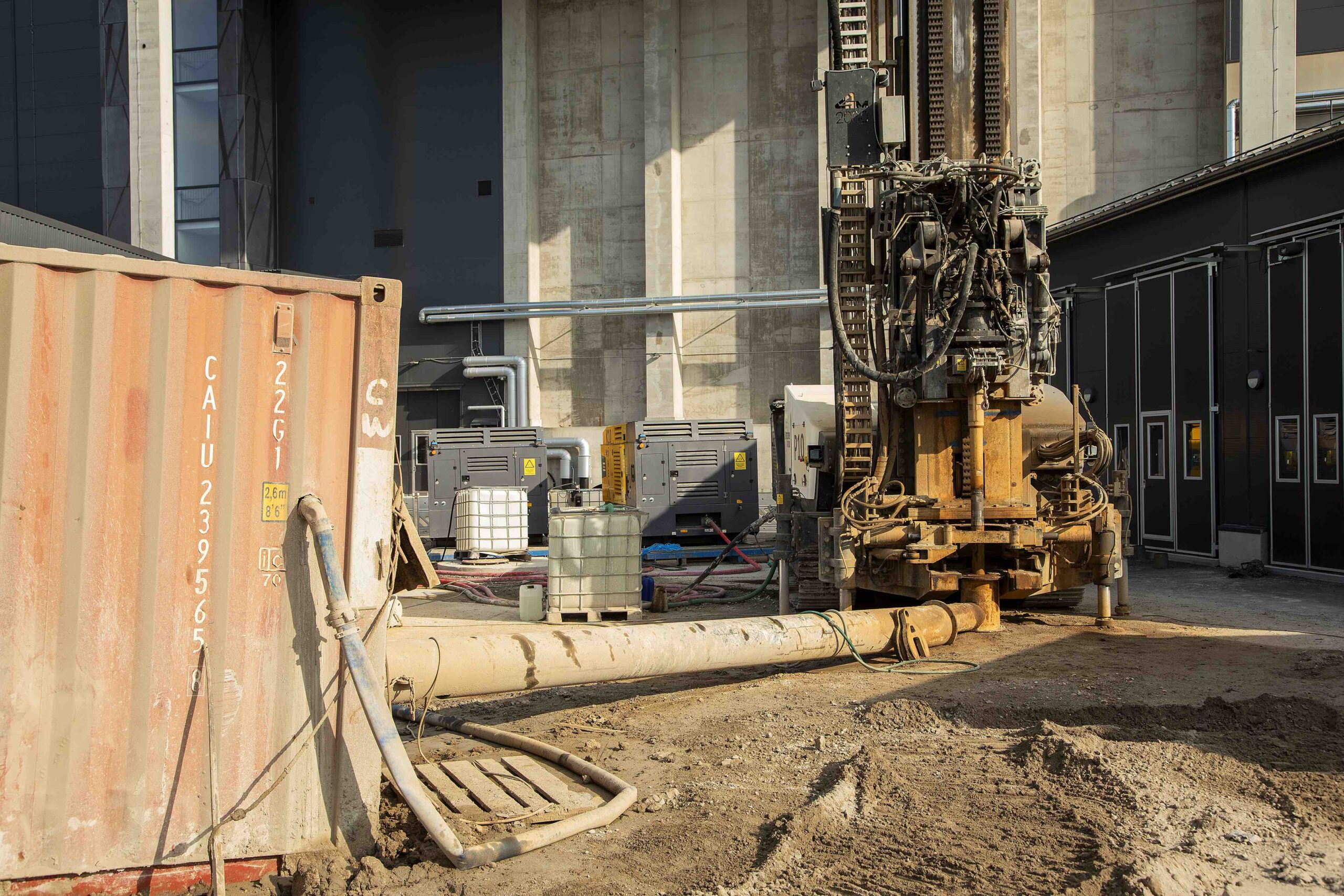
GM2000
The technology company QHeat has developed a solution that makes geothermal energy more accessible to those who need it. Wells drilled to a depth of 2000 meters can now be used not only as an inexhaustible source of energy but also as energy storage in a cost-effective way.
“For decades, the oil and gas sector has been drilling down to kilometers of depth,” explains Erika Salmenvaara, CEO of QHeat. “There’s nothing particularly new about drilling deep wells, but what is new is how we can now extract geothermal heat cost-efficiently from these wells.”
Between 2016 and 2020, a well-drilling project was underway in Espoo, Finland but it was ultimately discontinued. “The project in Espoo drilled to a depth of about 6 kilometers. Our company’s founder, Rami Niemi, was involved and realized that the method used at the time was not economically viable. To smartly extract energy from bedrock that was compressed during the ice ages, a new type of solution needed to be developed.”
2000 meters is enough with the right technology
QHeat realized that drilling to a depth of 2000 meters was sufficient to achieve an optimal input-output ratio. “The deeper you drill, the greater the well’s heat production potential becomes, but the drilling costs also increase. When comparing the costs and the value of heat production at different depths, the best cost-efficiency ratio is found at 2000 meters.”
QHeat’s solution collects heat in a completely new way. “Our innovation is based on creating a coaxial flow in the well. An insulated central pipe is installed in the well, allowing energy to be brought from the depths to the surface without heat loss. Previously, the deeper the well was drilled, the greater the heat loss became.”
Installing the central pipe in the geothermal well also offers another excellent benefit. “By reversing the flow direction of the well, it can be turned into a heat storage unit, releasing energy when needed.”
By drilling to 2000 meters, heat production can also be brought closer to its end users. “Traditionally, heat energy has been produced by burning fossil fuels in centralized heat production plants, far from the end user. Deep geothermal is suitable for the needs of a decentralized district heating network, as it can be produced and stored close to those who need it.”

Impressive also in terms of facts
To convert different forms of energy into heating energy, heat pumps are required, and their efficiency varies depending on the energy source used. Heat pump efficiency is measured by the COP (Coefficient of Performance). It indicates how many units of heat energy a heat pump can produce with one unit of electricity. “In district heating networks using air-to-water heat pumps, the COP is 2.5,” says Erika Salmenvaara. “If the energy source is a geothermal well 200–300 meters deep, the pump’s efficiency is 3.5. By using our technology and a 2000-meter deep well, we can achieve a COP of up to 4.5. This means that despite the initial investment, a deep well is the most cost-effective energy source.”
Drilling deep geothermal wells is also smart beyond just economic factors. “A 2000-meter deep well produces emission-free, clean energy. It takes up 97% less land area than traditional wells, making it possible to implement in densely built urban environments. Overall economic efficiency is also improved as the well serves as both an inexhaustible energy source and an energy storage unit.”
Geothermal energy’s positive effects are also societal. “This energy form improves the country’s energy production self-sufficiency. It shortens the energy production supply chain and ensures its responsibility.”
Multiple applications, many beneficiaries
The most significant beneficiaries of deep well drilling are those who generate waste heat. “For example, deep energy storage is a smart solution for waste incineration plants. When the waste heat produced by the plant is stored in the well, it can be released into the district heating network when consumption is high.”
Storing waste heat would also benefit cities aiming for energy circularity. “Urban planning should make better use of waste heat by storing it in deep geothermal wells. Energy could be retrieved from the wells when demand for heat is highest.”
Real estate investors also benefit from geothermal energy. “If you’re looking to increase the value of your property, self-sufficient, clean energy is one of the most important investments. There is a lot of research showing that utilizing self-sufficient renewable energy positively impacts property value. Current knowledge suggests it can increase the value by up to 10%.”
Development continues, with the user’s benefit at the core
QHeat’s development of geothermal technology continues. “So far, we’ve mainly focused on the properties and costs of well components. In the future, our product development will focus on the intelligent control of the technology and enabling market integration.”
The energy market of tomorrow requires even more flexibility. “The solution to the need for flexibility is the smarter use of energy through deep geothermal wells. Energy can be produced stably from bedrock, as geothermal energy is not dependent on weather conditions. By storing energy in deep wells, it can be released for use when needed.”
Procrastination benefits no one
Erika Salmenvaara reminds us that the right time to start a geothermal energy project is today. “Climate change is a growing concern, and the situation needs to be addressed in a timely manner. Energy users should understand that if the goal is to operate carbon neutrally by 2030, investments aimed at that goal need to be made now.”
If you’re interested in geothermal energy, it’s worth contacting QHeat or Geomachine. “Share your thoughts with us. Let’s determine together what would be the most sensible way for you to adopt this energy form. We will carry out the project with the help of our network and also assist in securing funding and maintaining the well. By starting the project now, you could benefit from a deep geothermal well in about a year.”
Interested? Contact Geomachine or QHeat!
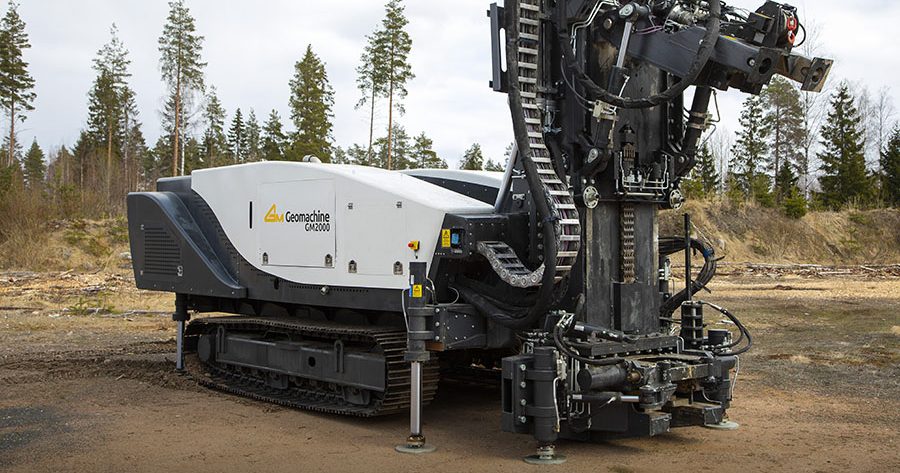
Lounavoima
In Salo, Finland, heat is stored in 2,000-meter-deep geothermal wells drilled with the Geomachine GM2000 geothermal drilling rig. This is the first time that such deep geothermal wells are in operational use in the Nordic countries. Lounavoima has also begun the construction of three new geothermal wells already.
A geothermal heat well storage has been commissioned at Lounavoima’s Waste-to-Energy (WtE) plant at the Lounapuisto circular economy park in Salo, Finland. The test run results for the first well have been good, and a decision has been made to construct three additional wells. Upon completion of the project, the WtE plant will have six geothermal heat wells with a combined output of 6MW. Waste heat produced by the WtE plant is stored in the geothermal heat wells and used for district heating in the winter.
Read Lounavoima’s press release on the subject here.
The news about the commissioning of the geothermal wells was also noted by other Finnish media (content in Finnish):
Interested? Contact us!
GM2000
With the GM2000 drilling rig, it is now possible to drill a geothermal well to a depth of more than two kilometers – quickly, replicably and at competitive costs.
More energy from a smaller land area
An energy field consisting of traditional 300-meter-deep geothermal wells requires a lot of land, and is therefore not suitable for densely built-up areas, large sites, or the needs of district heating networks.
One 2000 meters deep geothermal well produces more than 60 times more energy than a traditional shallow well. It only needs 1% of the land area required to build an energy field. A deep geothermal well provides heat a long time without losing its production capacity.
In deep wells, the losses in the coaxial heat exchange system are small and the heat transfer from the soil to the geothermal system is efficient. Only water is used in the system.
Deep well is also an energy storage
By changing the flow direction in the well, the geothermal well can be used for cooling properties and storing energy in the bedrock. This makes it possible to utilize the waste heat produced in the summer when the energy consumption increases in the winter.
Efficient and reliable drilling
The GM2000 drilling rig enables efficient and repeatable drilling to a depth of two kilometers in hard granite. The measurement and control technology used in soil investigation, has now been brought to well drilling, making it possible to control the process even in deep wells.
Find out more here.
Clean energy
Geothermal energy is renewable energy and is available continuously regardless of weather conditions. It produces carbon dioxide emissions up to 150–300 kg/MWh* less annually compared to oil or district heating. The CO2 emission reduction of one deep geothermal well is 257,000 kg per year, which corresponds to the emission reduction potential of more than 10,000 solar panels**.
Geothermal wells meet the criteria of the EU taxonomy and are a socially responsible alternative, as they do not have landscape or noise effects on their surroundings.
Self-sufficiency in energy production
A deep geothermal well can be an independent energy source. Well can also be a part of district heating network reducing network’s carbon dioxide emissions and improving the energy efficiency of the system. On a larger scale, the utilization of deep geothermal wells increases the energy self-sufficiency of the whole country.
Interested? Take contact!
*Statistics Finland 2023
** Calculated with the average emission factor of Finnish electricity production
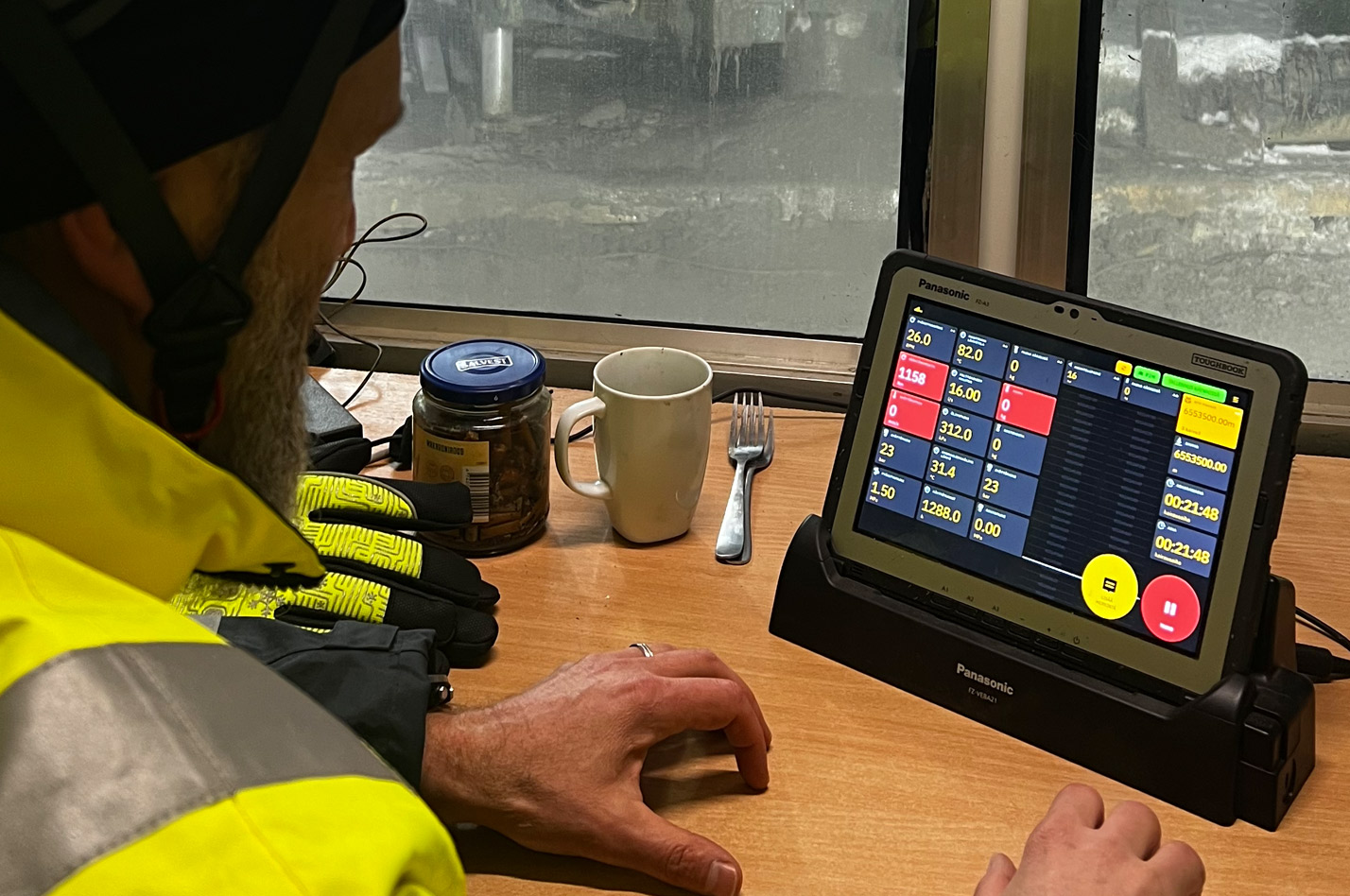
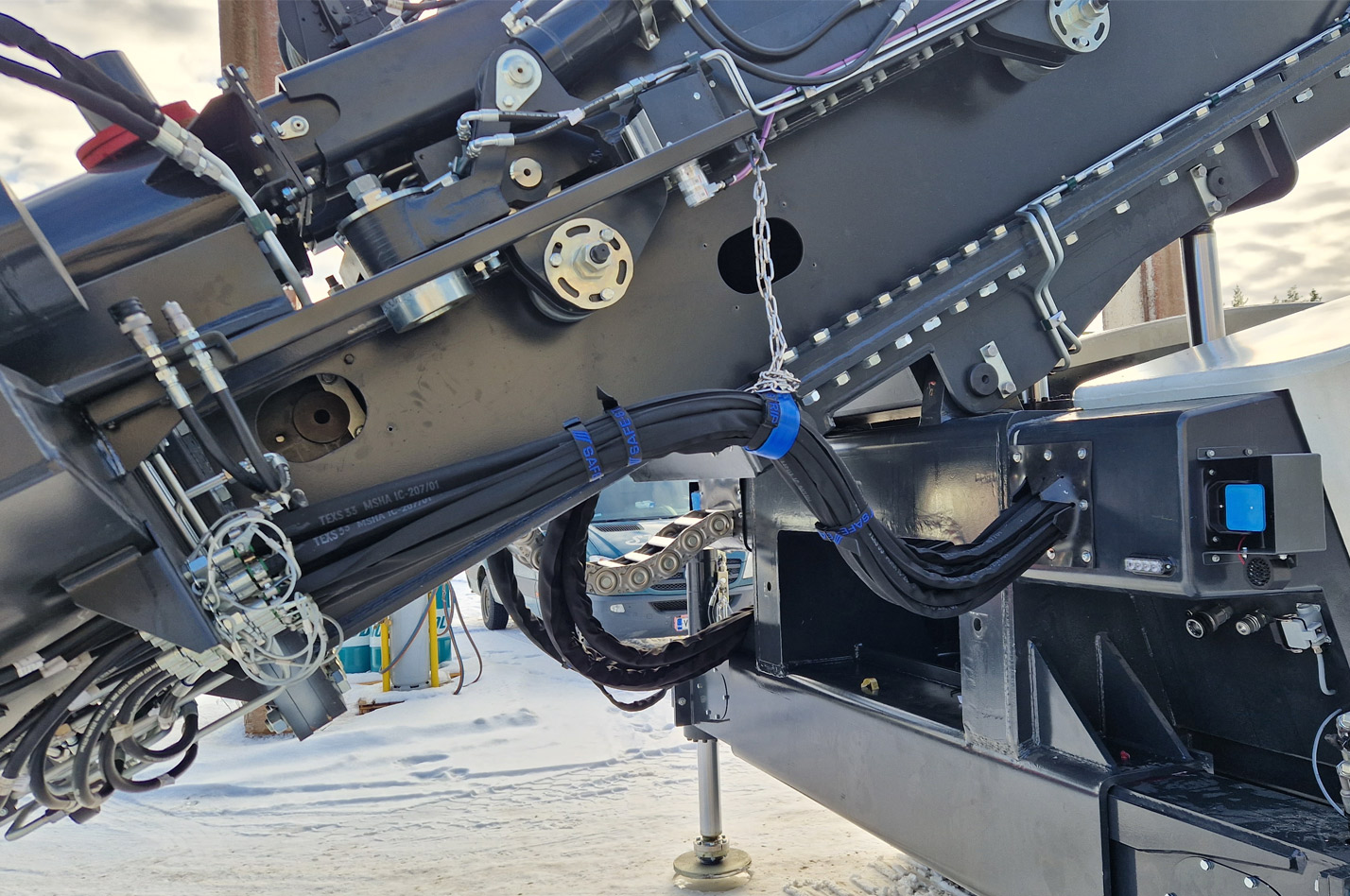
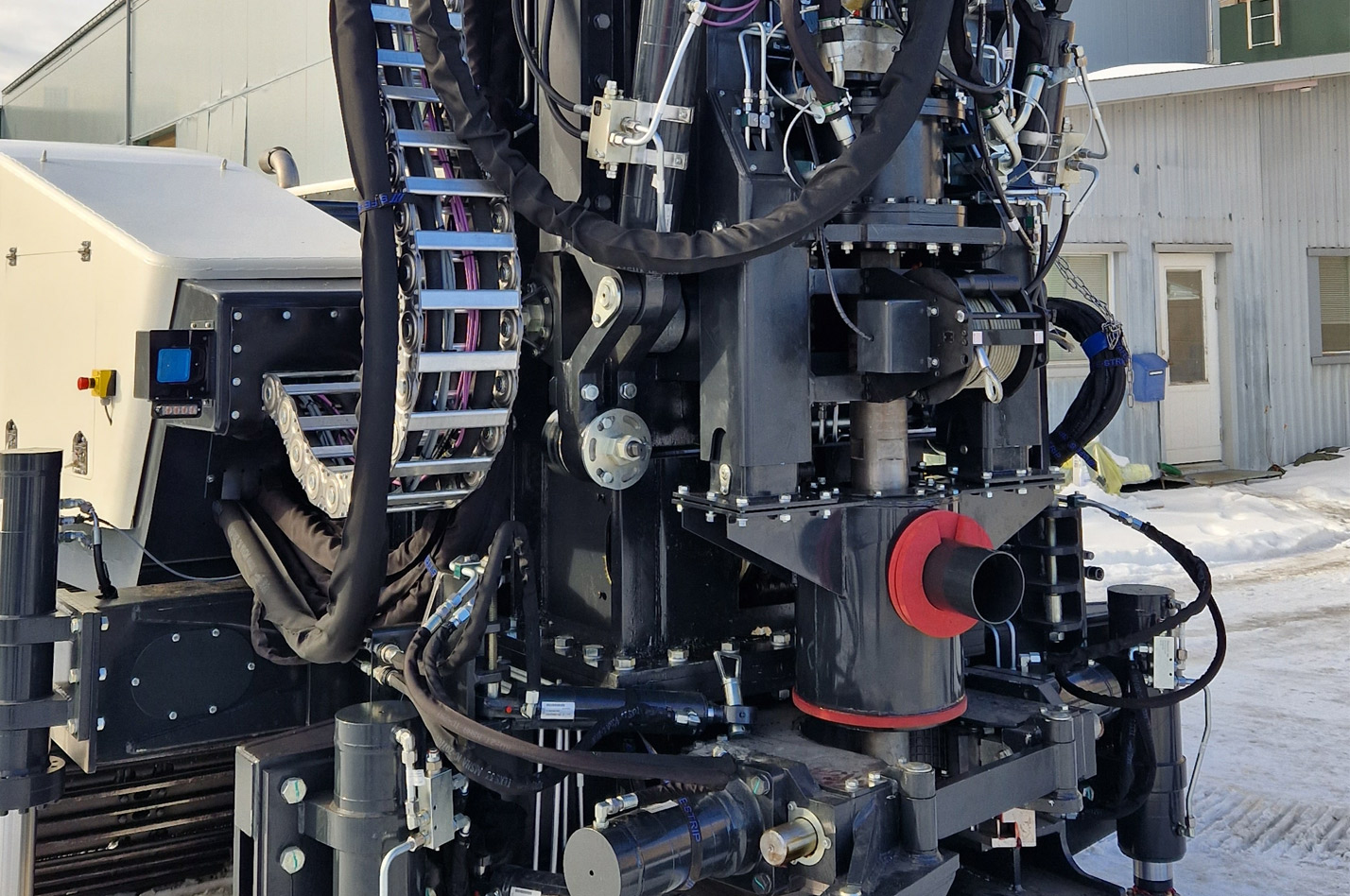
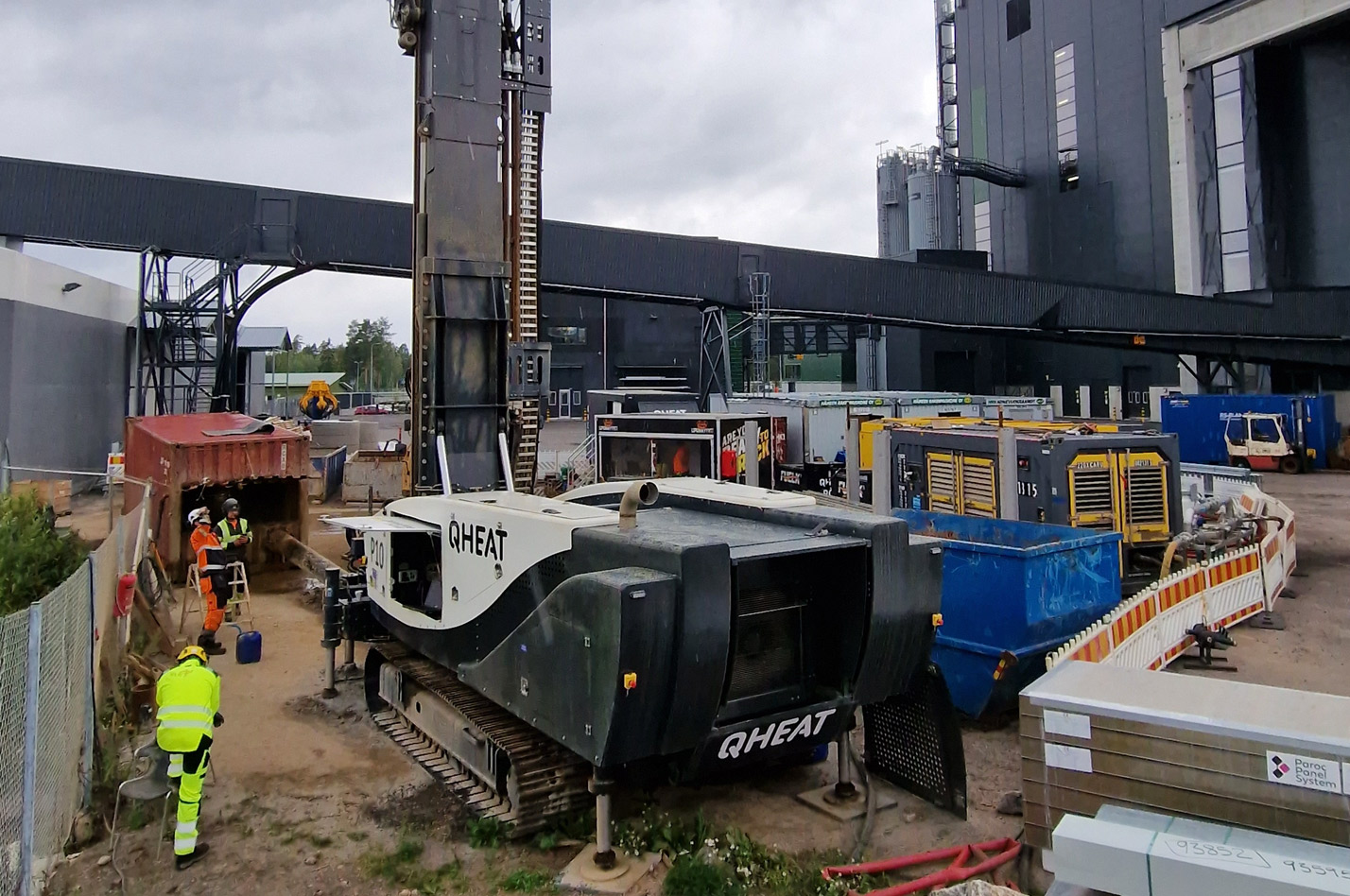
Geomachine | QHeat | Lounavoima
The world’s first 2,000-meter-deep geothermal well drilled for the use of Waste-to-Energy (WtE) plant has been completed at Waste-to-Energy company Lounavoima’s plant in Salo, Finland. The operation of the well is based on the geothermal well solution developed by Quantitative Heat Oy (QHeat) and it was drilled with a GM2000 drill rig developed by Geomachine Oy.
“Geothermal heat is an environmentally friendly and sustainable solution to the world’s growing energy needs,” says Samuli Salmela, CEO of Geomachine Oy. “Since there will be less land available for geothermal wells in the future, the wells must be drilled deeper. One geothermal well drilled to 2,000 meters produces the same amount of energy as some dozens of traditional energy wells, and it is also suitable for heat storage and cooling. Therefore, the solution developed now is suitable e.g. for use on larger construction sites and district heating networks.”
The world’s first GM2000 well drilling rig has been commissioned in Salo, Finland by WtE company Lounavoima’s order. “The operation of the plant generates energy for the district heating network evenly,” QHeat CEO Erika Salmenvaara says. “In the network, however, the heat consumption load changes all the time, so when the consumption is at a low level, the plant has produced excess heat. This energy can now be stored in deep geothermal wells and released from there later as consumption increases. A similar solution has not been used at a waste-to-energy plant before, so we are now the first in the world to implement the project in such an environment. Over the next few years, a total of six wells will be drilled for the Lounavoima waste-to-energy plant.”
In the past, QHeat’s record depth for drilling geothermal wells has been 1,600 meters. The fact that drilling can now be carried out with Geomachine’s GM2000 drilling rig up to 2,000 meters and even beyond, takes the utilization of geothermal energy to a whole new level. “The drilling depth has been increased by a third, which means that the energy production of the well increases more than 60 %. Annually, 950 megawatt-hours were obtained from a 1,500-meter-deep well, and now we obtain 1,530 megawatt-hours from a 2,000-meter deep well,” says Erika Salmenvaara. The numbers are even higher if the energy output of a 2,000-meter-deep well is compared to a traditional 300-meter-deep geothermal well. “Compared to a traditional well, we can now capture up to 60 times more energy from one well than before.”
Geomachine’s geothermal well drilling solution is optimized for down-the-hole drilling in hard Scandinavian rock. Its product development has focused on the overall economy of drilling, the fast drilling progress enabled by DTH technology, automatic recording of drilling data, real-time analysis of the drilling process, and working safety. In addition to the GM2000 well drilling rig, the overall solution includes needed air compressors, drilling accessories and an intelligent control and data logging system for optimizing the drilling process. The solution is also available with electric powerline, which enables a reduction in emissions. The rig’s easy mobility and ramp up also contribute to the overall economic efficiency of drilling. “Thanks to our solution, the driller can monitor the drilling parameters in real time, even though the drilling itself takes place at a depth of hundreds of meters. This reduces equipment breakdowns, speeds up drilling and makes it cost-effective,” says Samuli Salmela, CEO of Geomachine Oy.
The relative share of geothermal heat as the main heat source for buildings has been
growing since the beginning of the 2000s. In the future, the GM2000 solution will especially benefit large real estate sites where the concept can be used as a regional energy source. From one well, there is enough energy to heat even more than three hundred, A energy class 70 m2 apartments.
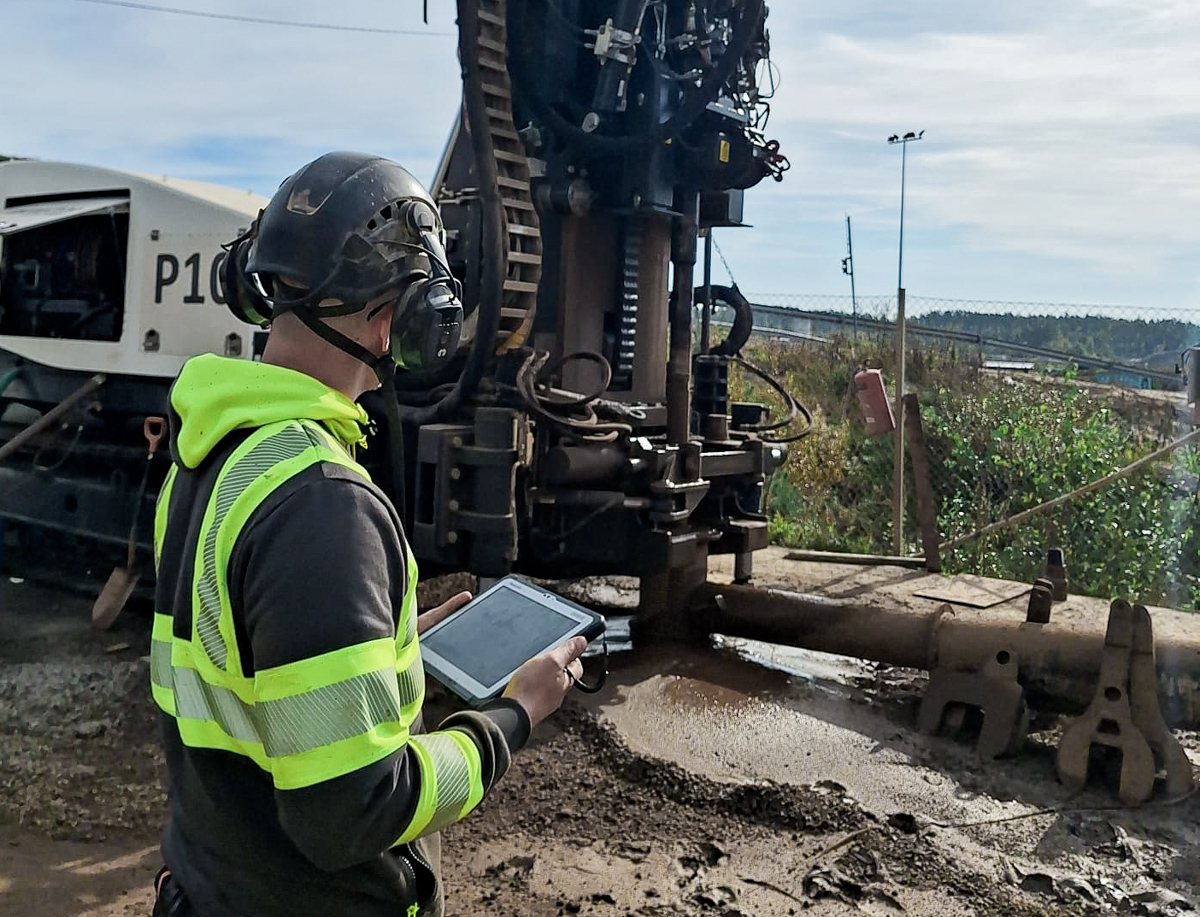
QHeat
Thanks to the new geothermal solution introduced in March 2023, geothermal heat is now being captured from depths exceeding 2000 metres. The developer behind this solution is the technology company QHeat. Well drilling is carried out using Geomachine’s GM2000 technology.
“Deep drilling has been a practice in the oil and gas sector for a long time,” begins Erika Salmenvaara, CEO of QHeat. “However, in traditional geothermal drilling, the depth has only been around 300 metres. With our newly developed geothermal well solution, we are now able to utilise geothermal energy from up to 2000 metres deep, and possibly even deeper in the future. This represents a significant leap in the utilisation of geoenergy.”
QHeat’s new geothermal solution is patented globally. “We will also take our innovation abroad. Energy consumption is continuously increasing, and there is a growing demand for renewable energy sources. Geothermal energy holds immense market potential in Europe, North America, and Asia.”
GM2000 takes centre stage in drilling
The drilling of wells is performed using Geomachine developed GM2000 well drilling technology. In addition to the well drilling rig, the complete solution includes a compressed air system and an intelligent control and recording system for optimising the drilling process. This solution is the first of its kind in the world. “When we started looking for a practical implementer for our innovation a few years ago, we realised that there was no expertise in deep geothermal well drilling in Finland. Geomachine has decades of experience in ground investigation and down-the-hole hammer drilling, so we engaged in discussions about refining our concept with them. It became clear that they had the expertise needed to develop the drilling rig.”
In designing the GM2000 well drilling rig, special attention has been given to overall cost-effectiveness, automatic data recording, real-time analysis of the drilling process, and work safety. “The adoption of the GM2000 solution has brought various benefits. Drillers’ job satisfaction has improved because they now have a modern tool at their disposal. Work is safer, and drillers are no longer exposed to emissions as the rig can be controlled remotely. Due to the rig’s data-driven control, the driller knows what is happening in the hole at all times. Overall, work has become safer and of higher quality.”
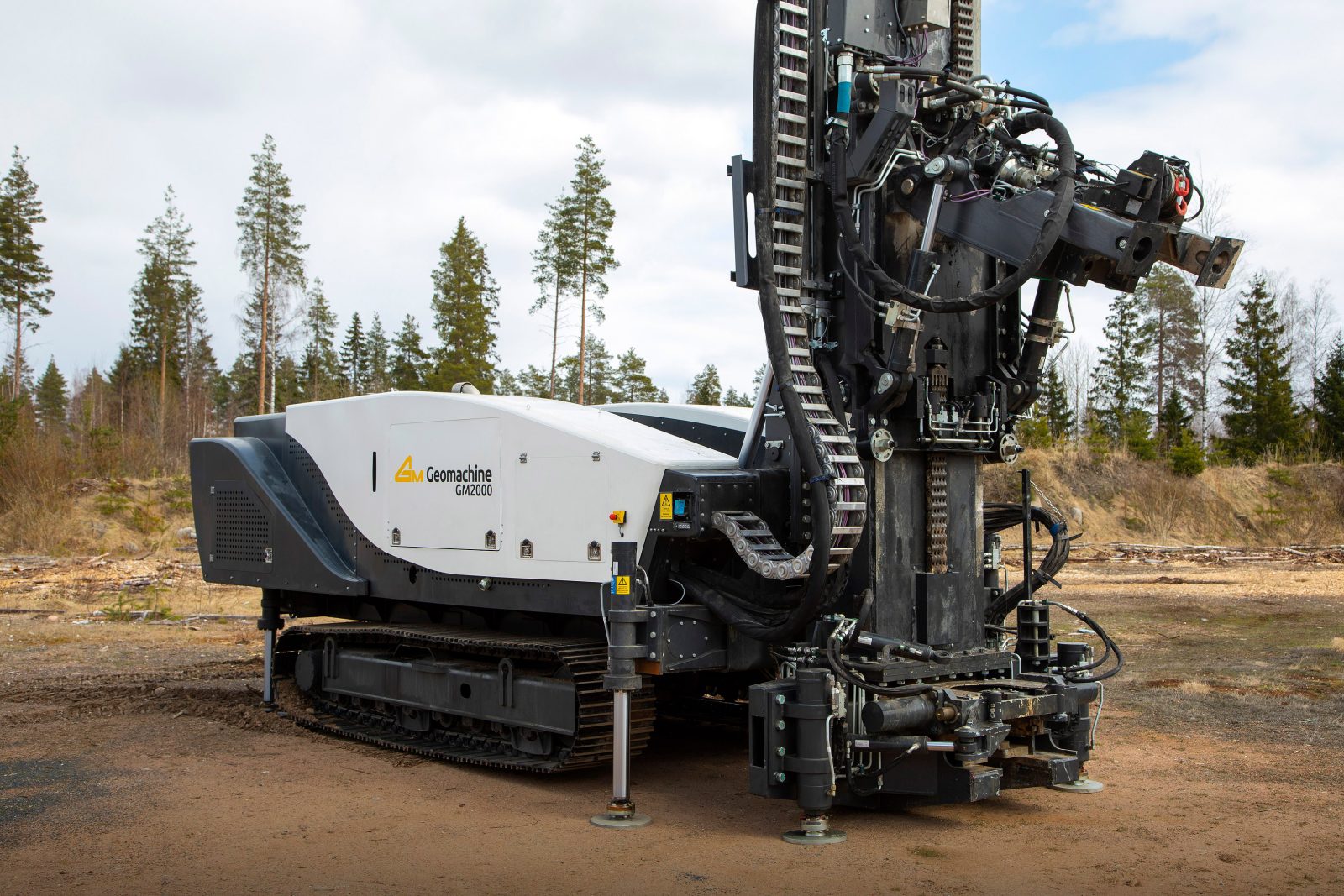
In action at a waste incineration plant
The world’s first GM2000 well drilling rig was put into operation in March 2023 at the request of Lounavoima, a waste incineration plant in Salo, Finland. “Our customer specifically required the use of this solution for their site. In addition to greater drilling depth, safety during work was important to our customer.”
At the Lounavoima waste incineration plant, deep geothermal wells are primarily used for heat storage. “The plant generates a steady stream of energy for the district heating network. However, the heat demand on the network constantly varies. During periods of low consumption, the plant has generated excess heat. This excess heat can now be stored in deep geothermal wells and later released when demand increases. This solution was not previously used at waste incineration plants, so we are implementing it here as the first in the world.”
The Lounavoima project began in 2021 with a different drilling rig, and now it continues with Geomachine’s GM2000 solution. “The plan is to drill two more geothermal wells this year, totaling three wells at the site. Overall, the goal is to create a heat storage consisting of six wells.”

Clear numbers tell the story
Before the introduction of the GM2000 well drilling rig, the record drilling depth for geothermal wells was 1600 metres. The ability to now drill to 2000 metres, and potentially even deeper in the future, takes the utilisation of geothermal energy to a whole new level. “The drilling depth has been increased by a third, which means that now we can capture 60% more energy than before. From a 1500-metre deep well, we obtained 950 megawatt-hours annually, and from a 2000-metre deep well, we can now obtain 1530 megawatt-hours. This is a remarkable improvement!”
The numbers are even more impressive when comparing the energy output of a 2000-metre deep well to a traditional 300-metre deep geothermal well. “Compared to a traditional well, we can now capture over 60 times more energy from a single well.”
In the future, the GM2000 solution will benefit especially large real estate properties where the solution can be used as a regional energy source. The energy from a single well is sufficient to heat even 300 energy class A apartments size of 70 m².
“In the future, we will market our solution especially to large property owners, professional real estate investors, construction companies, district heating producers, and district heating companies. The target must be large enough to optimally benefit from our solution.”
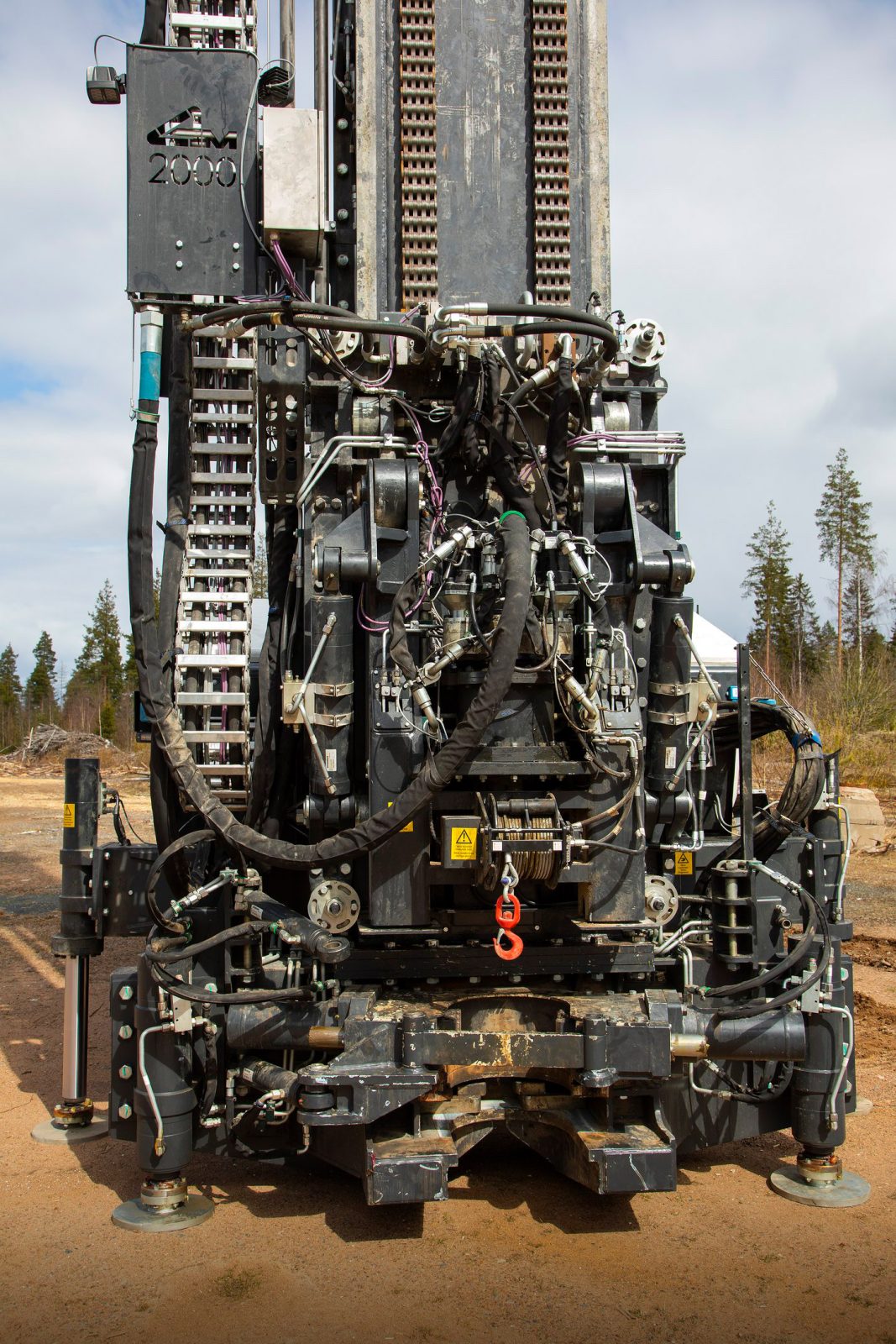
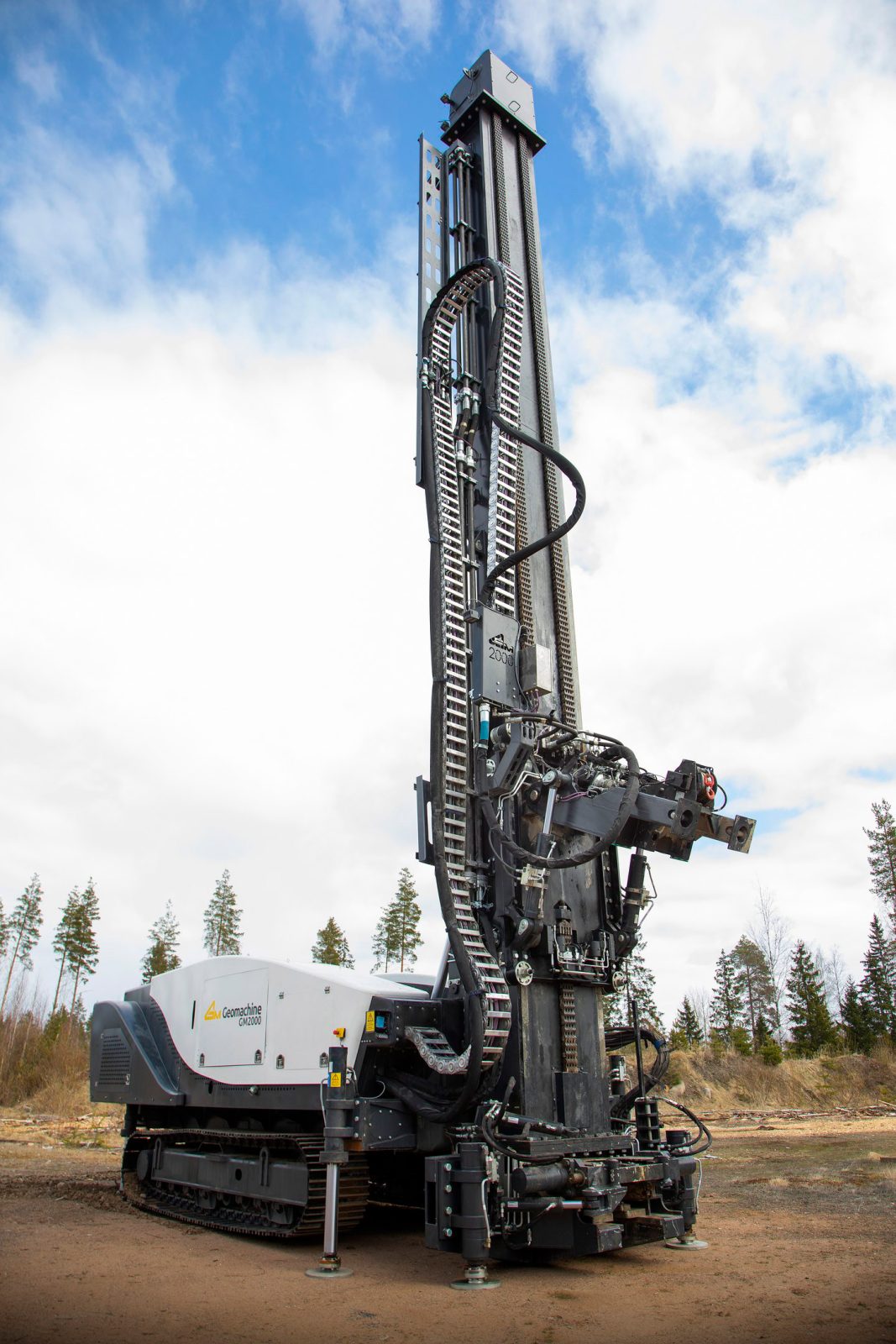
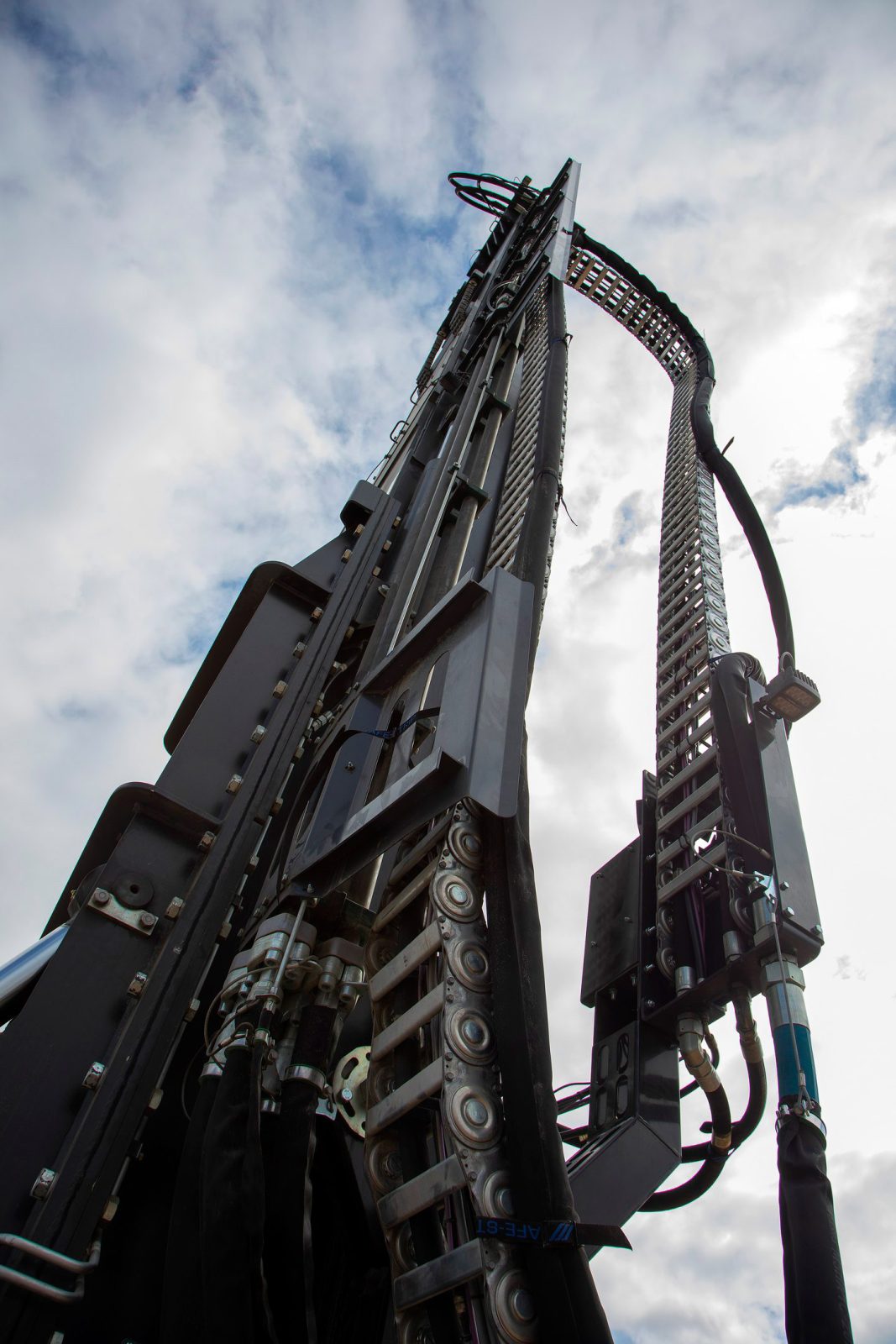
Authentic collaboration
According to Erika Salmenvaara, the collaboration with Geomachine is an excellent example of how combining forces can lead to an excellent outcome. “Our mission is to assist our customers on their carbon neutrality journey, particularly in heating. Our product is clean heating energy. Geomachine, on the other hand, offers the solution for practically implementing our mission. Even though we operate in different industries, we have found true synergy in achieving a common good.”
Both QHeat and Geomachine benefit from this collaboration in growing their respective businesses. “For us, collaboration enables us to sell our innovation as a tangible product to those who need it. Geomachine, on the other hand, adds a new solution to their product portfolio, expanding their offerings from ground investigation to geothermal energy drilling.”
Read more about GM2000 solution here.
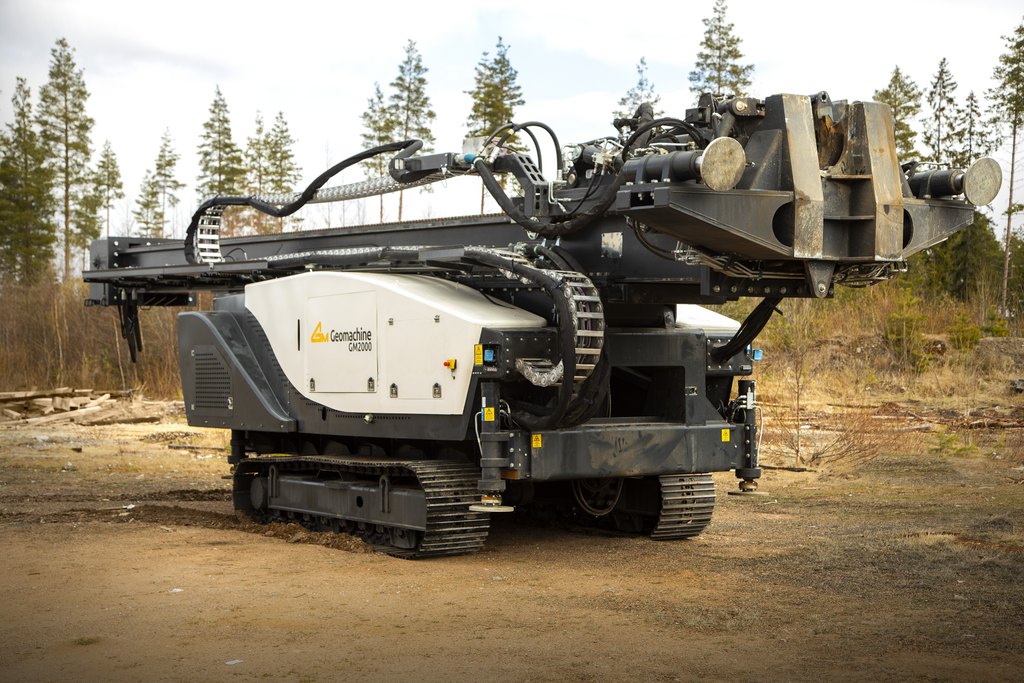