Kategoriat
Aluetaito Oy
At Aluetaito Oy, the most important aspect of ground investigations is capturing data with the highest possible quality and delivering it swiftly along the project value chain. This commitment has led to a partnership with Geomachine that has lasted over a decade.
Aluetaito provides clients with infrastructure design and investigation services, as well as field surveys and measurements. The service portfolio also includes, among other things, architectural design, BIM modelling, target cost estimates, and zoning for urban and shore areas. The company serves clients primarily within a 200–300 km radius of its headquarters in Lapua and its branch in Rauma.
“When it comes to ground investigations, our mission as a company is clear,” says CEO Juha Porre. “We provide our clients with investigations that are definitely done correctly and in accordance with the investigation programme. We ensure the highest quality of results and complete them on schedule.”
Efficient work made possible by robust tools
At Aluetaito, investigations are carried out with the best available equipment. “We know that if standards are set high, drill operators must be given the best possible conditions to meet them. That means investigation tools and working conditions must support success.”
Currently, Aluetaito uses Geomachine’s GM25, GM50, GM75, and GM8 drill-rig models. “For lighter drilling tasks, we use GM25 and GM50. The GM75 is a great all-rounder, capable of a wide variety of investigations from a single platform. Its compact size also makes it easy to transport between sites. We chose the GM8 as another multi-purpose rig due to its excellent terrain mobility—it has wheels instead of tracks, making it ideal for challenging terrain.”
According to Juha Porre, one key strength of Geomachine’s rigs is their consistent operational logic. “When drill operators use multiple models, it’s beneficial for the machines to function in a similar way. Once they learn one model’s drive, control, and usability, they don’t need to relearn each time they switch to another model. Naturally, this improves both efficiency and quality or work.”
Data at the heart of everything
The final product of a ground investigation is the investigation report—the information about what’s beneath the surface. If this data cannot be captured in high quality, the whole investigation is undermined. “We want to be known as a company whose investigation reports are trustworthy. The reports must always be of the highest possible quality and executed exactly according to the investigation programmes. We’re also known for delivering reports on schedule. Naturally, not all surprises can be foreseen—but when, for example, weather conditions don’t delay work, our reports are produced on time.”
The quality of an investigation report depends heavily on how data is captured. “Geomachine’s technological development of drill-rigs in recent years has been impressive, and today they are incredibly intelligent tools. A concrete example is the GMTracker data-logger designed for collecting ground investigation data.”
Aluetaito was involved in the development of GMTracker and knows its features well. The data-logger—used for about four years—has radically changed their practice. “Project management is now much smoother, as project leaders can distribute investigation programmes to multiple rigs simultaneously. On site, drill operators can view task-specific investigations via the logger and mark them as completed. Not only is data automatically stored in GMTracker, but operators can also add their own observations in it. Manual data entry has become unnecessary now that the level of automation is so high.”
The data-logger has become a popular tool among drill operators. “Since learning how to use the logger, I don’t believe anyone would ever give it up. It’s been an enormous help to operators in their daily work.”
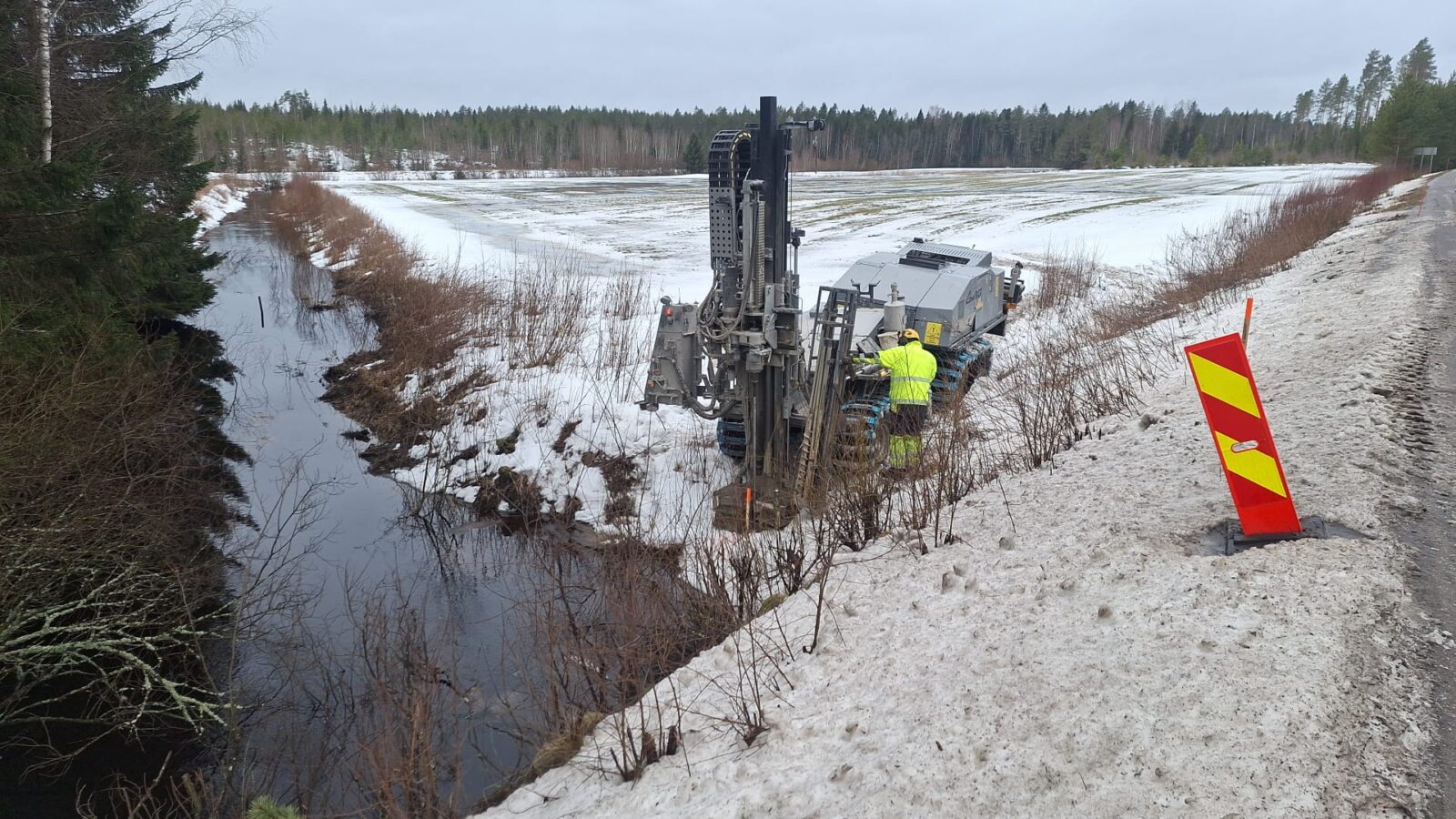
Transparent data flow and increasingly higher utilisation
Thanks to GMTracker’s Cloud version, investigation data is transmitted instantly from the site to everyone who needs it. “Not only can our project management team monitor progress in real time, but our clients also have immediate access to the information. They’ve praised us, noting that they can follow the investigation status without delay and download data as soon as it’s available.”
The Cloud functionality also allows Aluetaito to use the GMCare maintenance service. “We want to maximise the utilisation of our machines, and GMCare is an effective tool for this. At the moment, we mainly use it to document commissioning inspections carried out on site, but in the future it could also help us enhance interaction between the machine operator and maintenance. GMCare uses machine learning, which will enable machines in the future to inform us when maintenance is required.”
For those who want to focus on what matters
Today, a wide range of tools are available to enhance efficiency in ground investigation, and Juha Porre believes companies should definitely take advantage of them. “There are various companies in our sector, each with different operating principles. Our principle is that since the core of ground investigation lies in carrying out investigations correctly and to high quality, that is how we choose to operate. Our strategy for achieving this is to provide our drill operators with the most modern and highest-quality tools available. This is also an investment in the future, as excellent work is the best marketing for an investigation company and a driver of business growth.”
Geomachine’s tools help users focus on what’s essential in investigation work, and are therefore ideal for those whose quality standards and goals are high. “Behind a company’s success is usually the understanding that focusing on the right things is important. Focus improves both work quality and results, which in turn benefits customer satisfaction and drives business.”
Interested? Contact Geomachine!
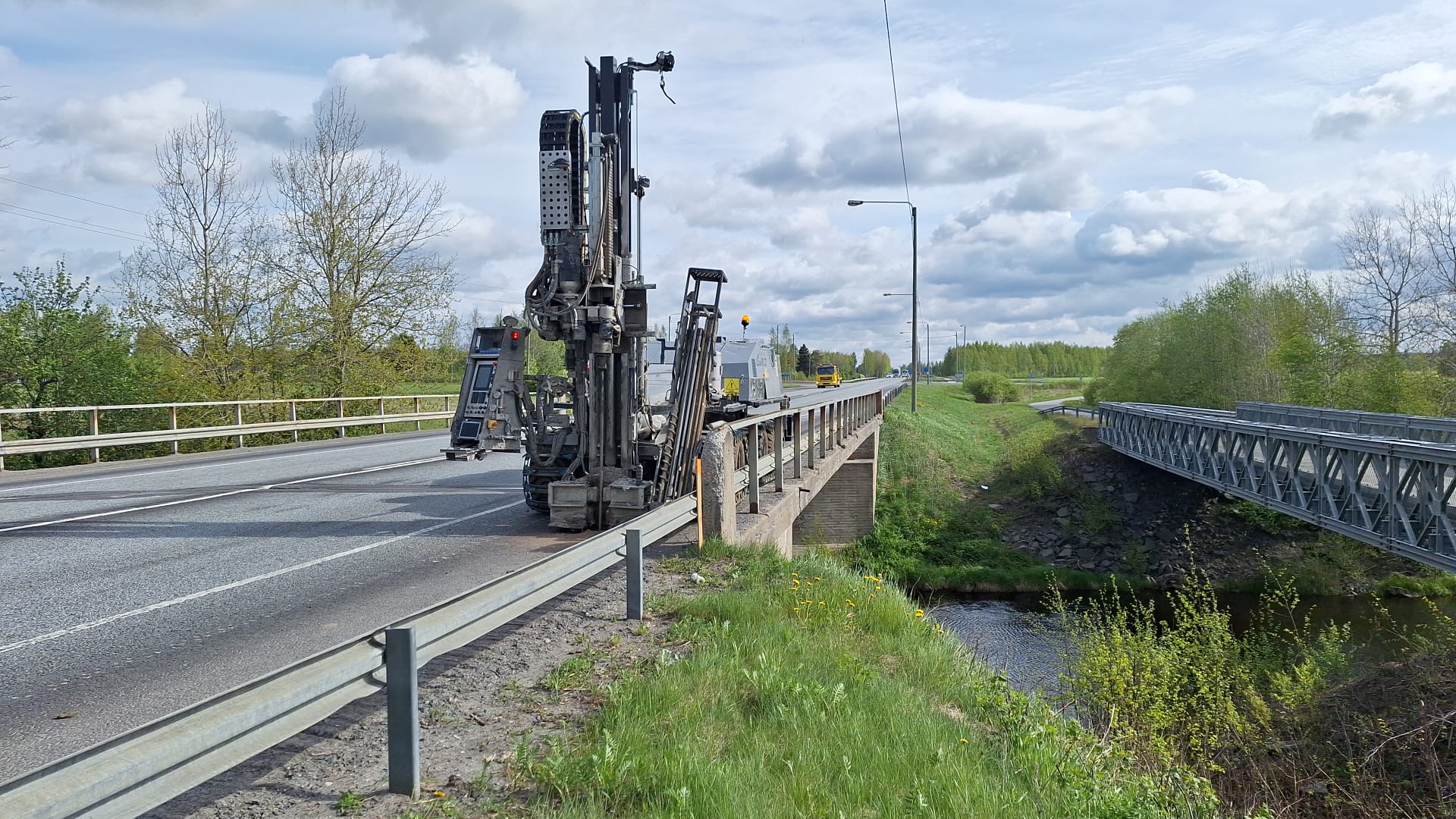
Geomachine Oy
Renting a machine is a good option, for example, when a company experiences a sudden increase in orders, project deadlines are approaching, or a new rig is still on the production line but investigations need to start immediately.
Geomachine currently rents ground investigation rigs primarily to Finland, the Nordic countries, and Estonia. In Finland, rentals are handled through Geomachine’s Tuusula office, while in other Nordic countries, machines can be rented from local distributors.
Geomachine’s spare parts sales manager Jouni Ketola explains that there are currently three versatile multi-purpose rigs available for rent. “Our models GM75, GM85 and GM100 are suitable for a variety of investigation methods and work well as multi-purpose machines. That’s why they are also in high demand as rental units.”
Rental agreements can be made for a fixed term or on a rolling basis. “A fixed-term contract is a good choice when the duration of the project is clearly defined. However, at the start of a project, it’s not always clear how much additional investigation will be needed. In such cases, a rolling rental agreement might be the smarter choice. The notice period for a rolling contract is two weeks, so ending the agreement is also simple if needed.”
The minimum rental period is one month. On average, customers rent rigs for one to two months, but much longer rental periods are also possible if necessary.
Many reasons to rent
There are many reasons why renting a machine may become necessary. “For example, if there’s a sudden machine failure, work must continue in order to stay on schedule. Penalties for delays are unpleasant, and no one wants to pay them. In these urgent situations, machine rental has often been a lifesaver.”
Perhaps the most positive reason for renting is a sudden growth in demand. “A rental machine is an excellent way to supplement a company’s own fleet when there’s more work than current resources can handle. It also increases the chances of success in tendering processes if you can confidently promise that investigations will be completed on time.”
Renting is also a smart move when a company is waiting for its own new machine to be delivered. “With a rental rig, you can make the most of the waiting period. You can continue to take on projects and start covering the cost of the new machine before it’s even delivered.”
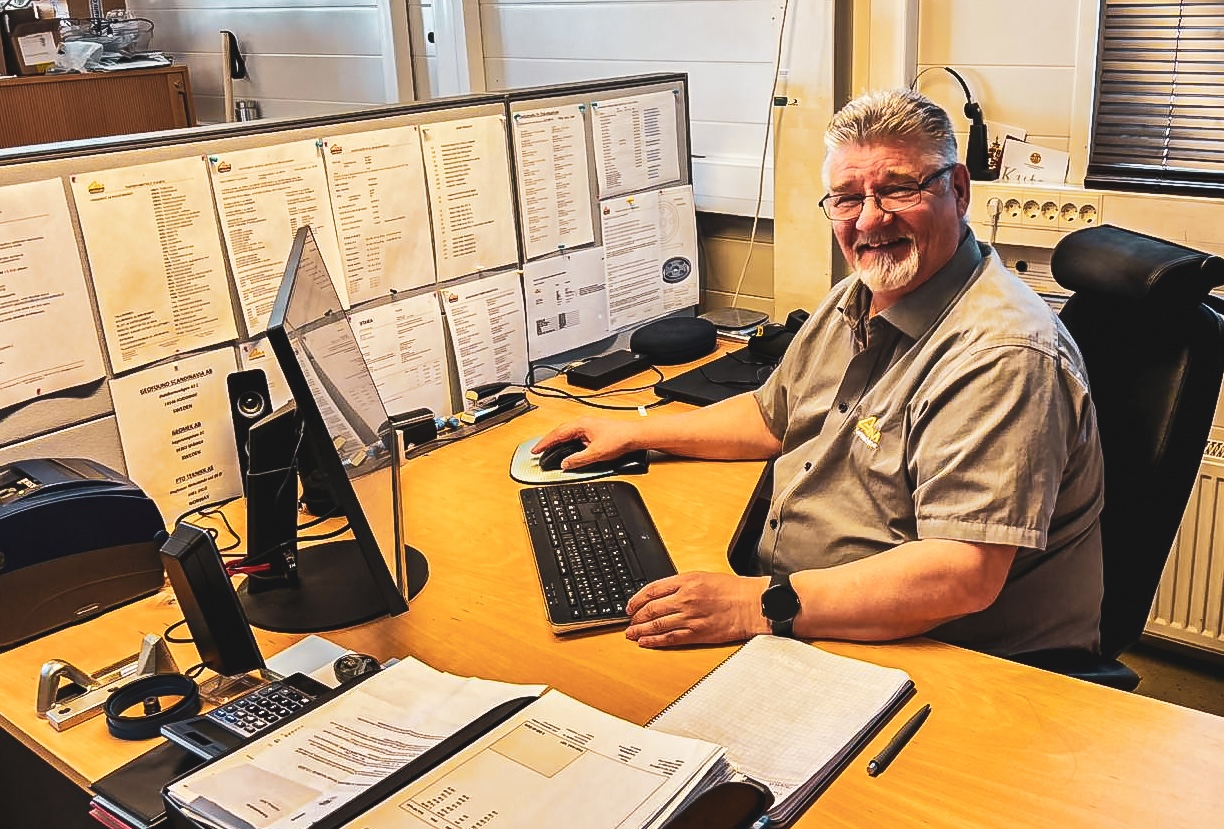
Always compatible, regardless of brand
According to Jouni Ketola, the equipment used by customers varies, but compatibility with the rental rig is not something to worry about. “We equip the rental rigs with drilling or hammering heads that match the customer’s existing equipment. This ensures compatibility regardless of the thread model used.”
If the customer doesn’t yet have their own equipment, that’s not a problem either. “A start-up company, for instance, might still be waiting for their machine to be built and hasn’t acquired equipment yet. In that case, we can sell the necessary gear, so they can begin ground investigations immediately if they wish.”
A rental partner that knows its machines
So why rent a ground investigation rig specifically from Geomachine? “We manufacture all the rigs we rent out, so we know them thoroughly. The machines are always serviced before being delivered to the customer. And if any issues arise during use, we can solve them quickly. We keep spare parts in stock and, whenever possible, the issue can be fixed with field service directly at the customer’s worksite.”
And what kind of company should consider renting? “If you want to serve your customers reliably in any situation, having access to rental machines is a great safety net. Renting is also a smart option for companies looking to expand their fleet organically. You can use a rental machine for individual projects and only invest in expanding your own fleet once your customer base and order flow are more established.”
Rental rigs can be made available very quickly if needed. “At most, the delivery time is a week—but quite often you’ll have the machine even sooner. Just give our rental service a call or send an email, and we’ll get the process started.”
Interested? Contact Geomachine!
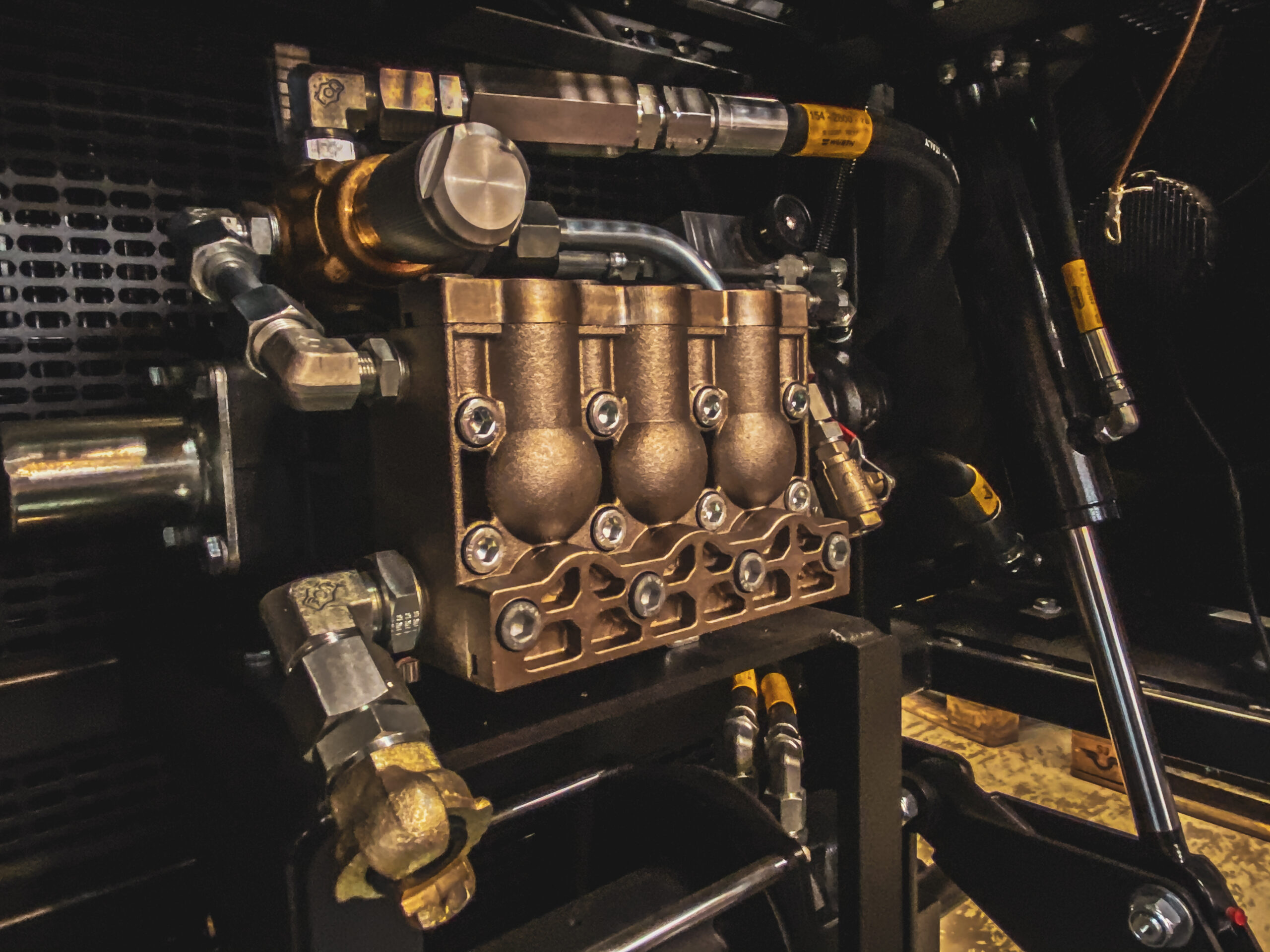
Geomachine Oy
Any company involved in geotechnical investigations knows that the uptime of drill rigs is directly linked to operational productivity. Geomachine’s maintenance services ensure that machine uptime can be maximised and downtime kept to a minimum.
“At Geomachine, we understand that only a working machine is a productive one,” begins Camilla Ojapalo, Geomachine’s service manager. “That’s why we’ve designed our maintenance services to ensure help is always available—regardless of the scale of the issue or the urgency of the repair.”
In Finland, machine maintenance is primarily carried out at Geomachine’s Tuusula site, while in other Nordic countries, local partners provide the service. For acute problems, fast assistance is available through the service points’ drop-in service. Minor maintenance work can usually be performed on-site within the same day or the next. Emergency care can also be provided on-site to transfer a completely inoperable machine to maintenance.
In addition to repairs, modifications and routine maintenance of drill rigs, service points also modernise older machines. They also handle the calibration of data logging systems and peripherals, and perform software updates on radio control systems installed in rigs.
Prevention is the best maintenance
From the perspective of maximising machine utilisation, the best approach is to care for the equipment proactively and in accordance with a maintenance schedule.
“The best way to solve a problem is to prevent it in the first place. Drill rigs are powerful machines. This means that if a component fails and the issue isn’t fixed quickly, it will likely escalate. If you want to be productive, it makes sense to ensure continuous operation. Productivity is also affected by how much is spent on urgent repairs—the size of the maintenance bill depends directly on the scale of the problem.”
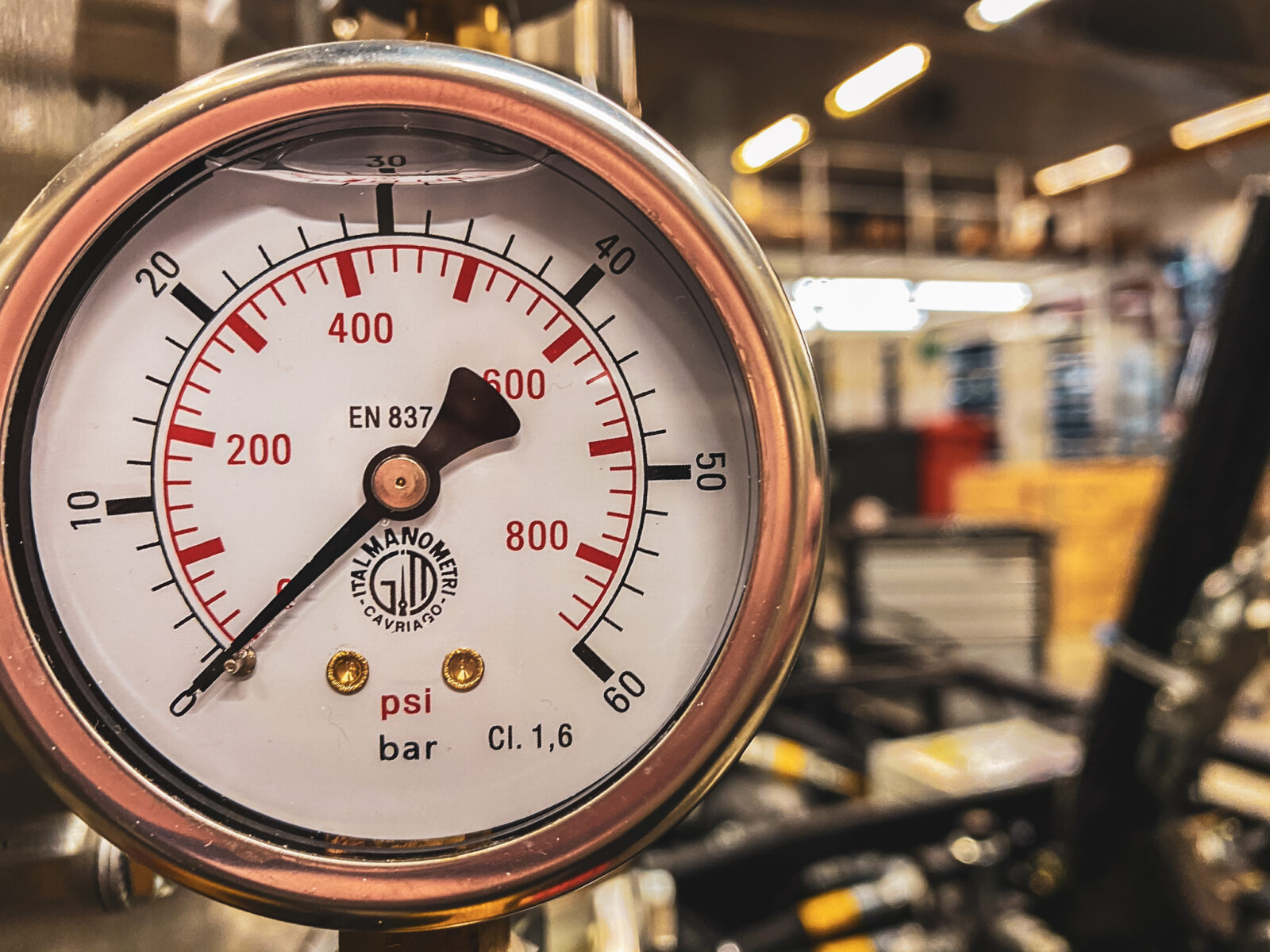
More intelligence and higher utilisation
Part of Geomachine’s digital product family, the GMCare maintenance service is designed to bring more predictability and efficiency to machine upkeep. Customers using this service are less likely to experience unexpected machine failures. “GMCare is an extremely smart maintenance platform. It uses machine learning to build a growing knowledge base, allowing for increasingly individualized and predictive maintenance in the future. If the machine is repaired before it fully breaks down, the length of downtime—and its impact on the project schedule—is minimised.”
GMCare users also recover from existing problems faster. “The service establishes a two-way, real-time connection between the worksite and those responsible for maintenance. The machine is added to the service queue immediately, and repairs can begin without delay. Some issues can be solved remotely through diagnostics, which naturally saves both time and money.”
GMCare is available to all Geomachine customers using the GMTracker logger with cloud connectivity. If GMTracker has not yet been installed, this can be done easily. “Installation takes one to three working days, so it can be up and running very quickly if needed.”
The hallmark of expert service
Geomachine’s maintenance services have been widely praised by customers, and the reason is clear. “Geomachine builds the machines it services, which of course means we know them inside and out. Our service centre is located under the same roof as production, so any questions that arise during servicing can be answered quickly. Our Nordic partners also maintain strong communication with us—so any issues raised on their end can also be solved without delays.”
In addition to in-depth machine knowledge, another key strength of Geomachine’s service is its speed. “Our spare parts inventory is also located on-site alongside manufacturing and servicing. This means we usually have the parts we need immediately available—no waiting for deliveries. Our customers appreciate this, as machine downtime is costly for any business.”
According to Camilla Ojapalo, there’s ultimately a very simple reason to make full use of Geomachine’s maintenance services. “If machine longevity is important to you, it makes sense to take full advantage of everything Geomachine’s maintenance offering includes.”
Interested? Contact Geomachine!
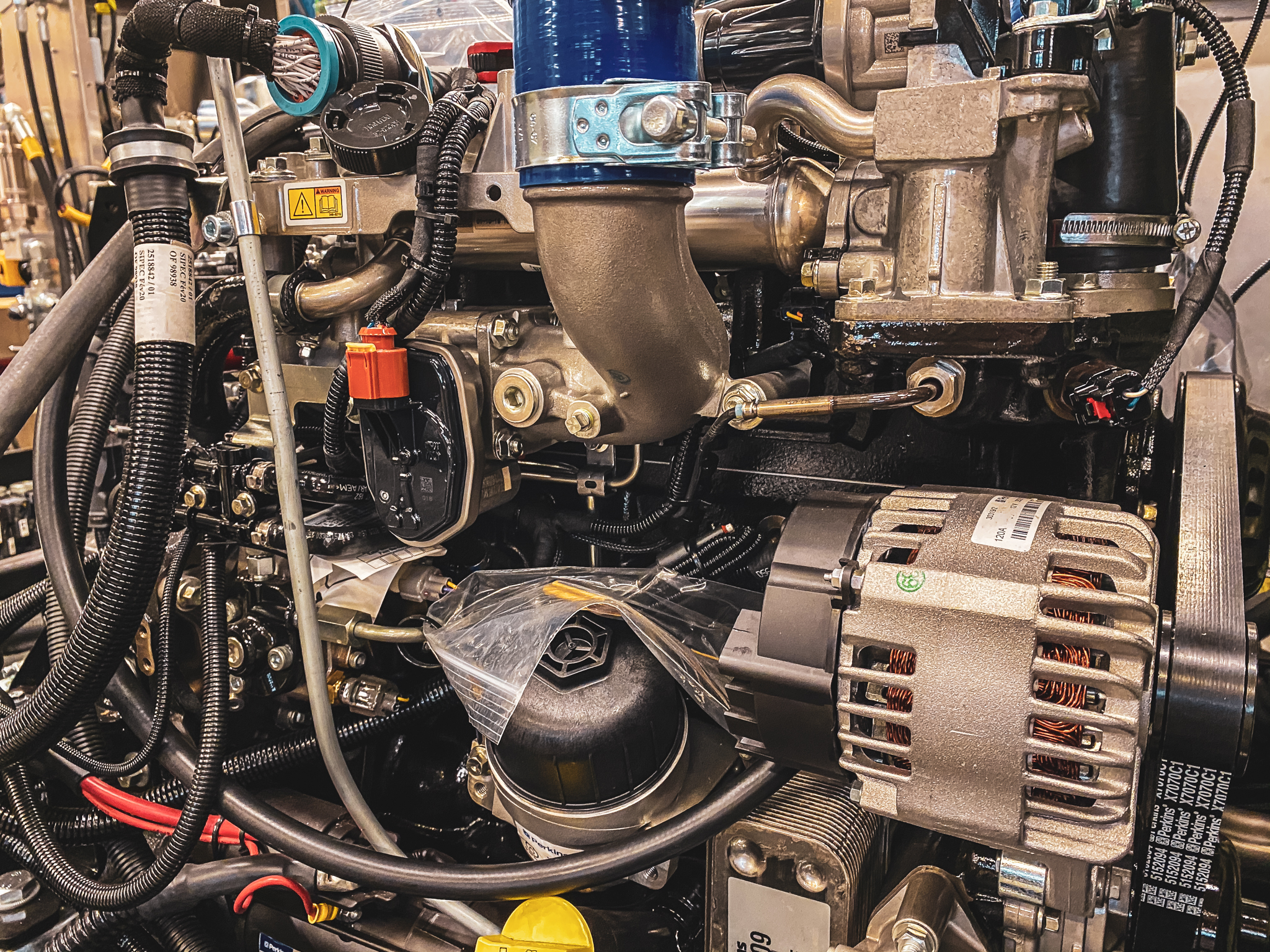
Geomachine Oy
Geomachine’s spare parts inventory holds tens of thousands of items, with several thousand in active circulation. Most spare part needs can be met directly from our own warehouse, enabling rapid resolution and minimal downtime.
Fast and knowledgeable spare parts service is key to maximising equipment uptime. When an unexpected breakdown occurs or a component reaches the end of its life cycle, it’s vital to replace parts without delay.
“Machine downtime is expensive for businesses, so we do everything we can to prevent it,” says Markus Ikonen, Spare Parts Salesperson at Geomachine. “Our Tuusula warehouse stocks most of the machine’s consumable components on the shelf, and we supply spare parts for every component attached to our drill rigs. We can usually deliver parts the same or the next day after the order. For more specialised items that need to be ordered from a supplier, delivery times are naturally a bit longer – but even in those cases, we do our utmost to ensure the quickest possible delivery to the customer.”
In addition to the spare parts warehouse, Geomachine’s Tuusula site also includes a manufacturing unit. “We produce some of the components used in our drill rigs ourselves, which naturally helps ensure their availability.”
On demand or on contract
Customers can order the spare parts they need as required, or ensure faster availability with an annual service agreement based on their maintenance plan.
The best way to resolve a problem is to avoid it in the first place. The more systematically and proactively a machine is maintained, the lower the risk of unexpected breakdowns. “However, when breakdowns do happen or scheduled maintenance is due, an annual contract is the smoothest solution. We keep a stock reserve of consumables for our contract customers, ensuring they get what they need without delay.”
Setting up an annual agreement with Geomachine is easy. “Just let our spare parts service know you’re interested. We’ll then review your part usage history – or make an estimate for new clients – and tailor a proposal accordingly. The service is activated immediately after signing.”
An annual contract offers more than guaranteed availability. “It also helps with budget planning – clients can allocate costs for spare parts based on actual consumption forecasts for the year.”

Support across key markets
Most of Geomachine’s spare parts customers operate in Finland, but the service also extends beyond its borders. “We are active also in Sweden, Norway, Iceland, and Estonia, where the service is available through our local partners.”
The Nordic region is relatively homogenous in terms of ground investigation conditions, so the demand for spare parts doesn’t vary significantly between countries. “Regardless of the market, the most commonly required parts are wear components like moving parts of the boom, drill rods, adapters, various undercarriage components and bearings.”
Delivery times are fast across all regions. “We work closely with local partners and maintain constant communication with them. When an order is placed, we can usually dispatch the parts from our own shelves quickly.”
GMFleet keeps you in control
In ground investigation, managing the lifecycle of equipment has traditionally been a challenge. Technical documents related to machines and parts have not been stored in one centralised place. Keeping data up to date has required manual work, leading to outdated information.
“By adopting our GMFleet equipment register tool, customers can ensure that all essential information about their machines and spare parts is always up to date. GMFleet includes all machine-related data, technical documentation, and lifecycle information. It also provides easy access to details on the technical capabilities of each machine.”
Centralised documentation of spare parts data in GMFleet helps get machines back in action quickly after maintenance or repairs. “Service partners and project managers can retrieve all needed equipment data from the register in an up-to-date and structured format. This speeds up both spare parts deliveries and the overall maintenance process.”
Want higher uptime?
As a machine manufacturer, Geomachine knows exactly what spare parts ground investigation rigs need – and how consumption varies per item. “Our expertise in this field is exceptional. For customers, this means help is always available and delivered without delay. In Tuusula, spare parts service operates under the same roof as sales, design, manufacturing, maintenance and machining. That means we can provide answers to any question quickly and reliably.”
According to Markus Ikonen, Geomachine’s spare parts services are ideal for any ground investigation company aiming for maximum uptime. “When the need for spare parts appears, we take immediate action. We know how costly downtime is – not only in direct expenses but also due to late penalties and revenue loss. That’s why we do everything we can to minimise it for our customers.”
Interested? Contact Geomachine!
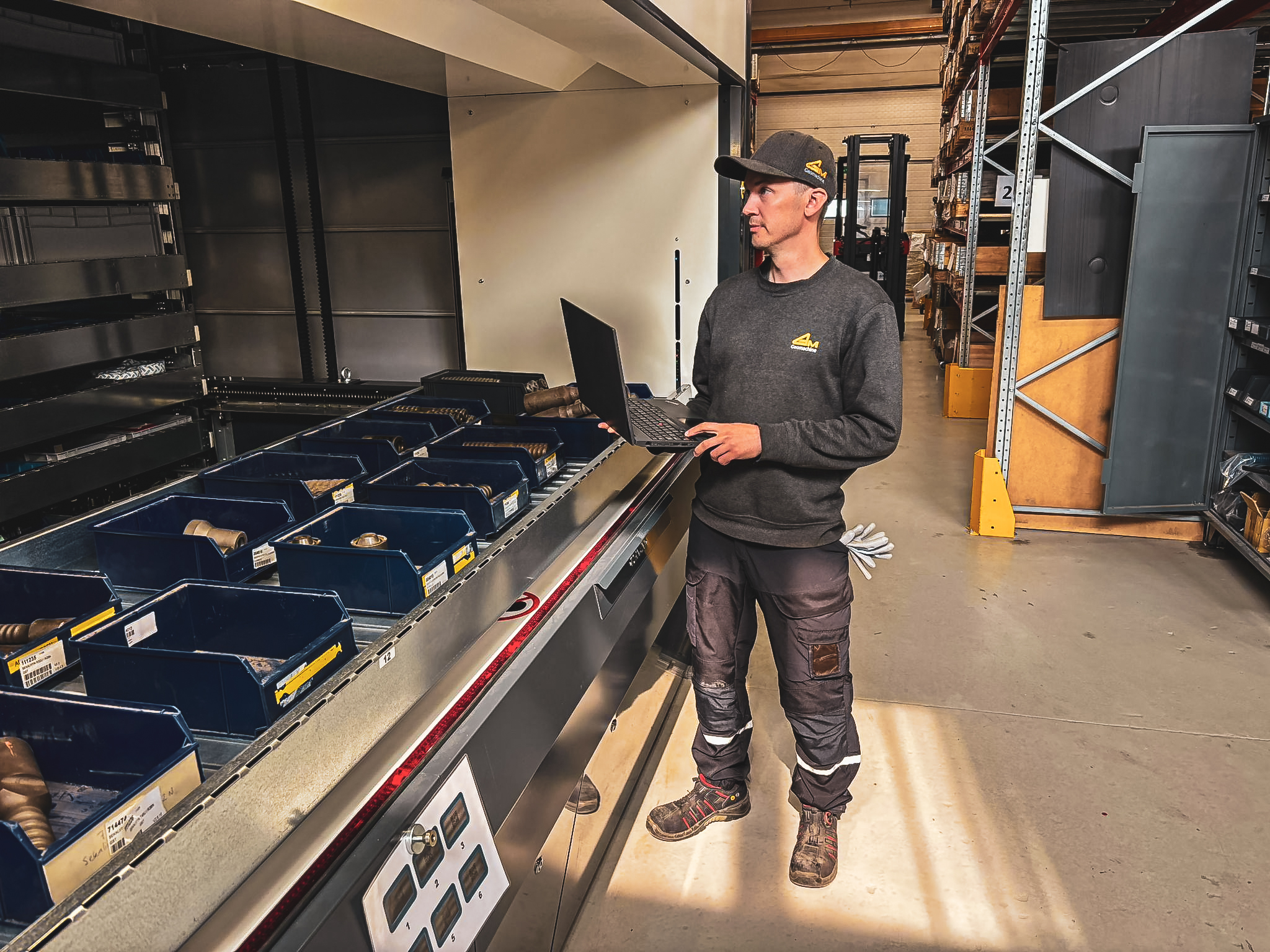
Taratest Oy
Taratest Oy, a Finnish expert in geotechnical and environmental research, has relied on Geomachine’s drilling rigs for nearly two decades. This article explores Taratest’s experience collaborating with Geomachine.
With over 40 years of history, Taratest employs more than 100 geotechnical professionals and operates offices in Pirkkala, Turku, and Vantaa. “Our mission is to deliver genuinely beneficial, technologically modern, innovative, and cost-effective solutions for construction,” says CEO Tero Mäkinen. “We focus on service quality to foster long-term client relationships, and environmental values are also important to us.”
Taratest’s turnover is approximately €21 million, offering a diverse range of ground and bedrock investigations, geotechnical design, and foundation construction consulting. Additionally, the company conducts environmental studies and assessments serving construction and industry.
A partnership spanning nearly two decades
Taratest ordered its first drilling rig from Geomachine in 2008. “We wanted to replace our outdated machines with equipment from a higher-quality manufacturer. We chose Geomachine because their machines’ advanced features convinced us. In our field, the community is relatively small, and Geomachine had a strong reputation among industry professionals.”
Today, Taratest operates around twenty Geomachine drilling rigs. “We use all Geomachine rig models except the GM8,” Mäkinen notes. “We initially acquired the GM65 rig for its versatility. As our projects became more demanding, we needed larger machines. Now, we have Finland’s most extensive fleet, focusing on larger machines like the GM100, which serves as an excellent heavy-duty multipurpose rig. We were also the first in Finland to acquire the GM100 Hybrid version.”
In the future, Taratest may expand its fleet with the fully electric GMe100 drilling rig. “Most of our projects are public sector works, where environmental friendliness is increasingly emphasized. We aim to be at the forefront of ground investigation, and as electrification is the future in our field, we’re exploring the possibility of adopting this method more extensively.”
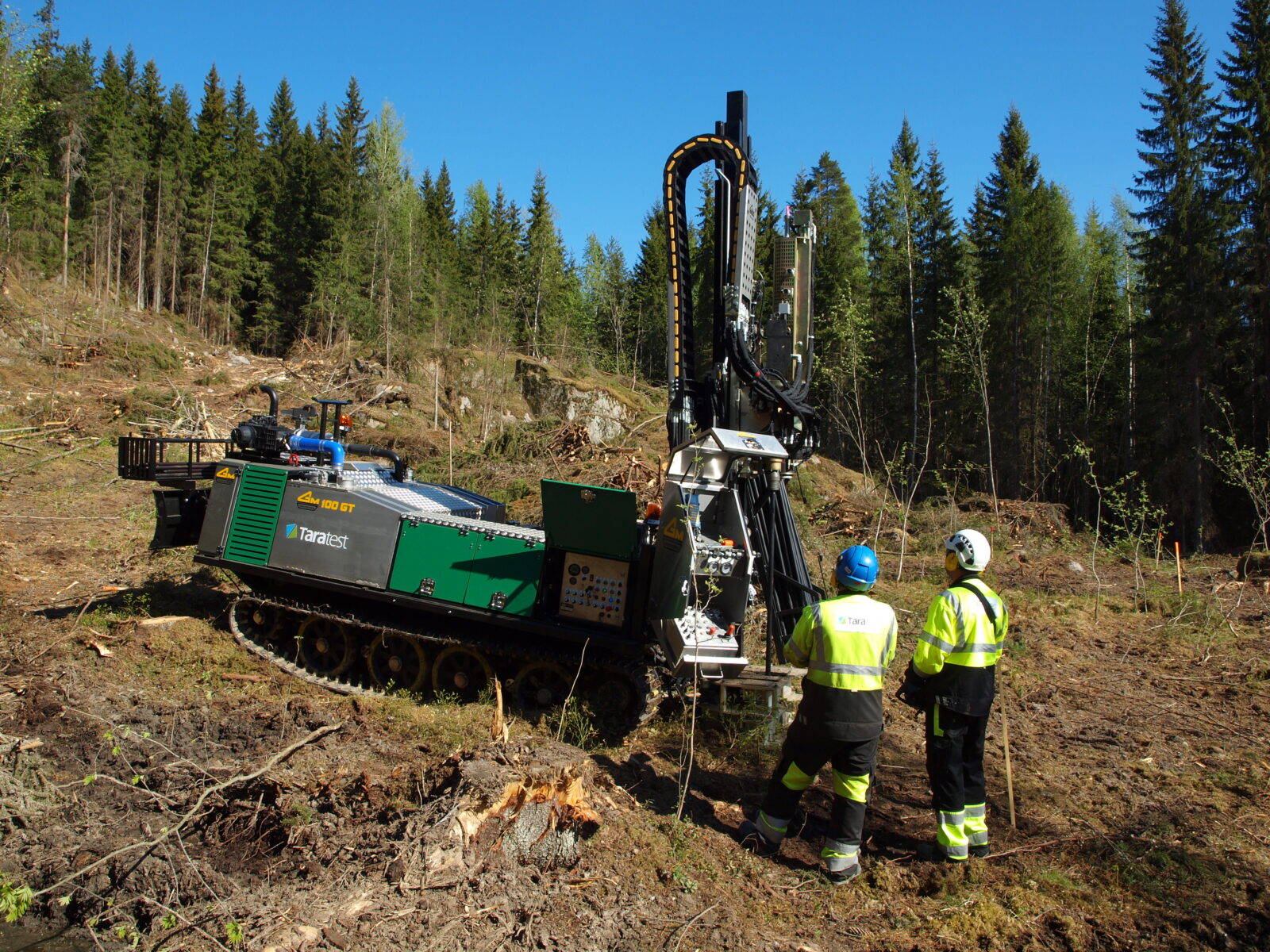
Features at the core
Mäkinen highlights that even at the beginning of their collaboration, Geomachine was ahead of competitors in developing features crucial for work efficiency. “Safety has always been our top priority. Even twenty years ago, Geomachine’s machines had advanced protections against rotating parts and crush hazards, surpassing other suppliers.”
Beyond safety features, Geomachine’s rigs offer other strengths. “Their off-road capability is exceptional, which is vital for us as we often work in challenging environments. The machines are also equipped for various research methods, which we highly value. Overall, their usability and reliability are excellent. It’s also beneficial that different models now have similar operational functions, reducing the time operators need to learn new machines.”
In ground investigation, data is the product, and Mäkinen praises Geomachine’s digital capabilities. “The GMTracker data-logger is an incredibly useful tool. Previously, our data-loggers only provided numerical data. In contrast, Geomachine’s data-logger offers a clear graphical interface showing drilling progress, which is highly beneficial. GMTracker automatically records ground properties and machine performance data, reducing manual work for the operator. Operators can also easily add their observations during the investigation. This not only improves data quality but also simplifies quality control of work processes.”
For those seeking the best tools
Mäkinen believes that successful collaboration results from multiple factors. “As a Finnish company, it’s important for us to work with high-quality domestic tools. Geomachine’s expertise in ground investigation methods used in the Nordic countries is exceptional.”
People matter as much as products. “We appreciate that, in addition to reliable machines, we can count on maintenance and support services when needed. It’s also pleasant to work with familiar people, whether considering new equipment purchases or matters related to our current fleet.”
The field of ground investigation is rapidly evolving. “Investigations are becoming more demanding and diverse, increasing expectations for machine performance and intelligence. The importance of data production and quality will continue to grow. Therefore, when acquiring equipment, it’s essential to ensure the supplier can offer digital services that enhance work efficiency alongside traditional drilling rigs.”
Mäkinen concludes that Geomachine is the right choice when aiming to conduct ground investigation with the best available tools. “I believe Geomachine’s drilling rigs and digital products are suitable for all geotechnical companies operating in the Nordic countries. Such that prioritize working with high-quality and reliable rigs—even in extremely challenging conditions.”
Interested? Contact Geomachine!
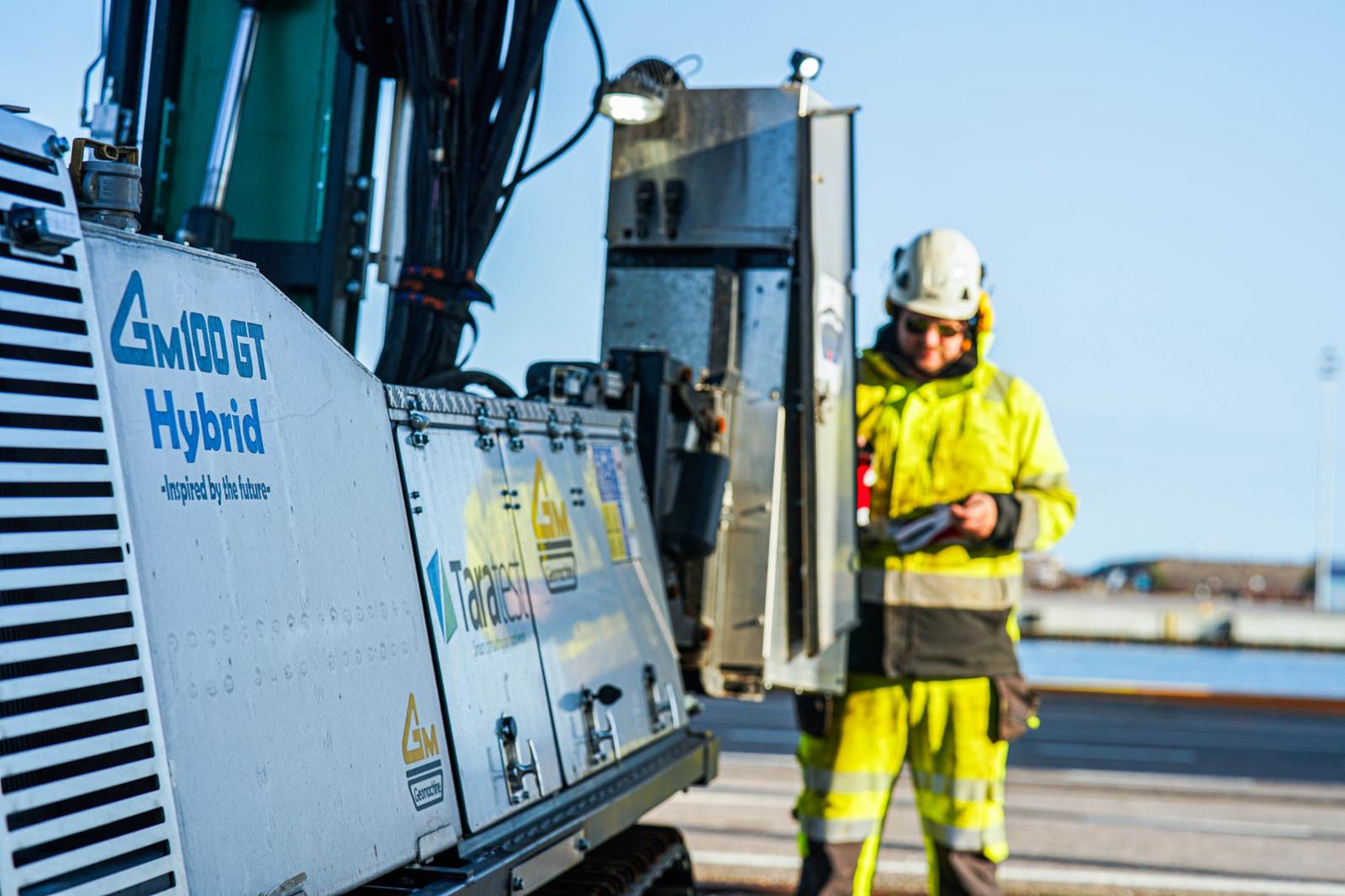
Geomachine
Geomachine has been designing and building ground investigation rigs for the world’s most challenging conditions for over four decades. Today, its product family includes seven different rig models to meet all ground investigation needs.
Geomachine began developing ground investigation rigs in 1984. Until then, investigations in Finnish conditions were conducted manually, and Geomachine sought to explore whether the process could be automated using machinery.
Today, the machine lineup comprises seven rig models capable of performing all investigation methods required for challenging Scandinavian conditions. To meet future demands for zero emissions, Geomachine has also developed the fully electric heavy-duty GMe100 investigation rig, which is suitable for all the same methods as its diesel-powered twin.
Significant advancements have occurred in rig development over recent decades. In the future, development will continue robustly, but its focus areas will evolve.
Cornerstones of rig development
Developing ground investigation rigs is an iterative process. There’s no need to reinvent the wheel each time; instead, new products are often built upon existing foundations. Proven and functional elements are retained, while areas identified through customer feedback are further developed.
According to Geomachine’s Sales Manager, Alexander Packalén, customer feedback is often very concrete. “For example, our GM85 rig model was developed because its predecessor, the GM75, couldn’t accommodate a compressor large enough to meet the customer’s power requirements. Our product family’s giant, the eight-wheeled GM8, came into being because a customer needed to work in rocky and challenging terrains inaccessible to tracked machines. Thanks to its off-road capabilities, the GM8 is in a class of its own and is now used on wind power construction sites, which are often located in remote areas.”
In addition to customer feedback, new product development is guided by legislation, environmental requirements, and the ongoing need for safer and more efficient operations. “In the ground investigation industry, as in other sectors, the pressure for environmental friendliness is continually increasing. Moreover, safety remains a crucial theme today, just as it was decades ago. As investigations become increasingly demanding and diverse, the need for larger machines and additional equipment, such as more powerful compressors, grows.”
When discussing ground investigation, one aspect stands above all. “Data must be collected from the ground with high quality. If this isn’t achieved, nothing else matters. That’s why our most significant focus in product development is currently on enhancing machine intelligence. The heart of our digital product family, the GMTracker data-logger, increases the automation level, efficiency, and data quality of investigation work. In addition to the data-logger, we offer innovative tools for planning and managing investigation projects, maintaining and servicing machines, and managing equipment registers. By adopting these tools, it’s possible to create a seamless value chain for the entire ground investigation process, significantly boosting productivity.”
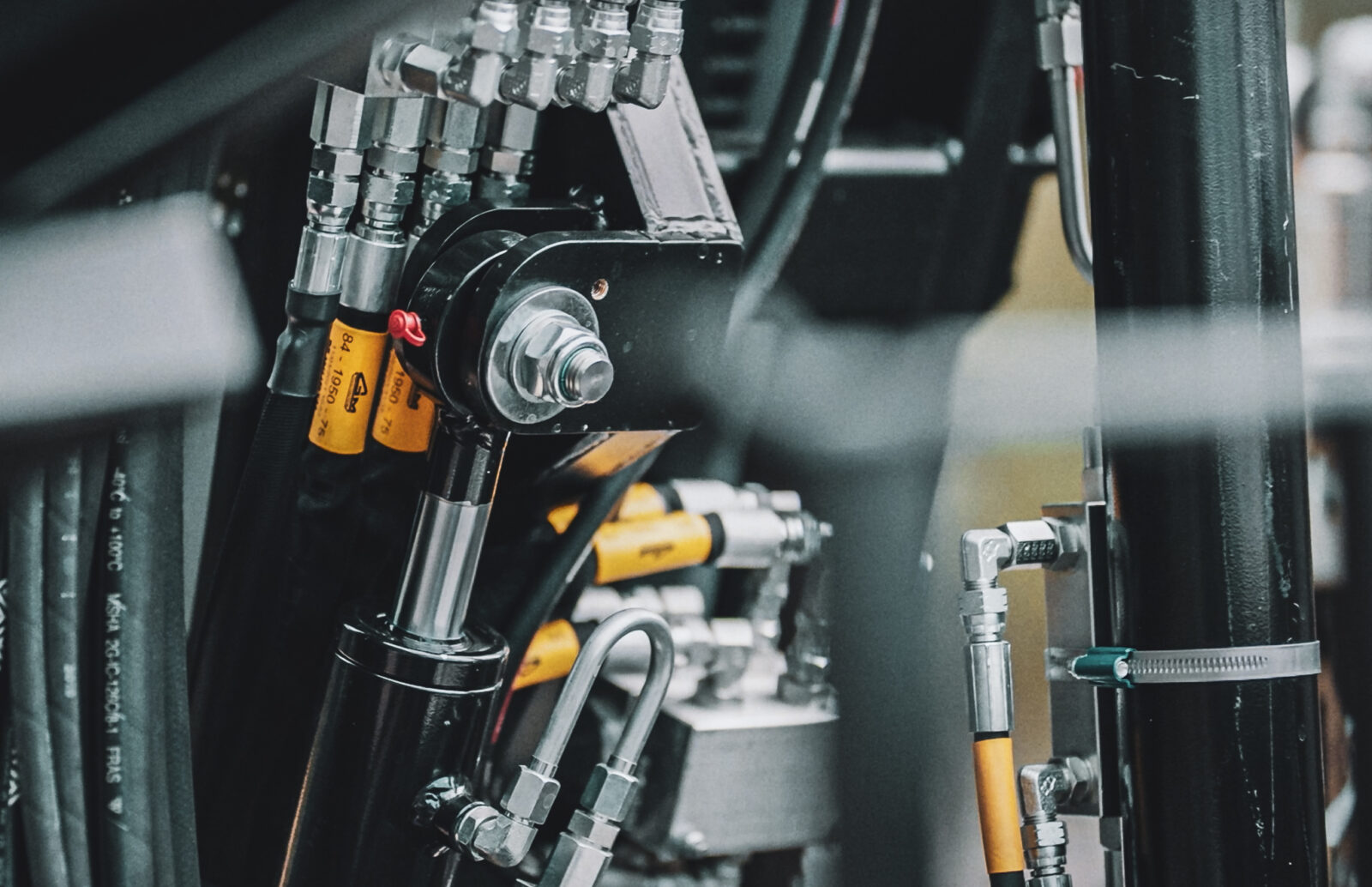
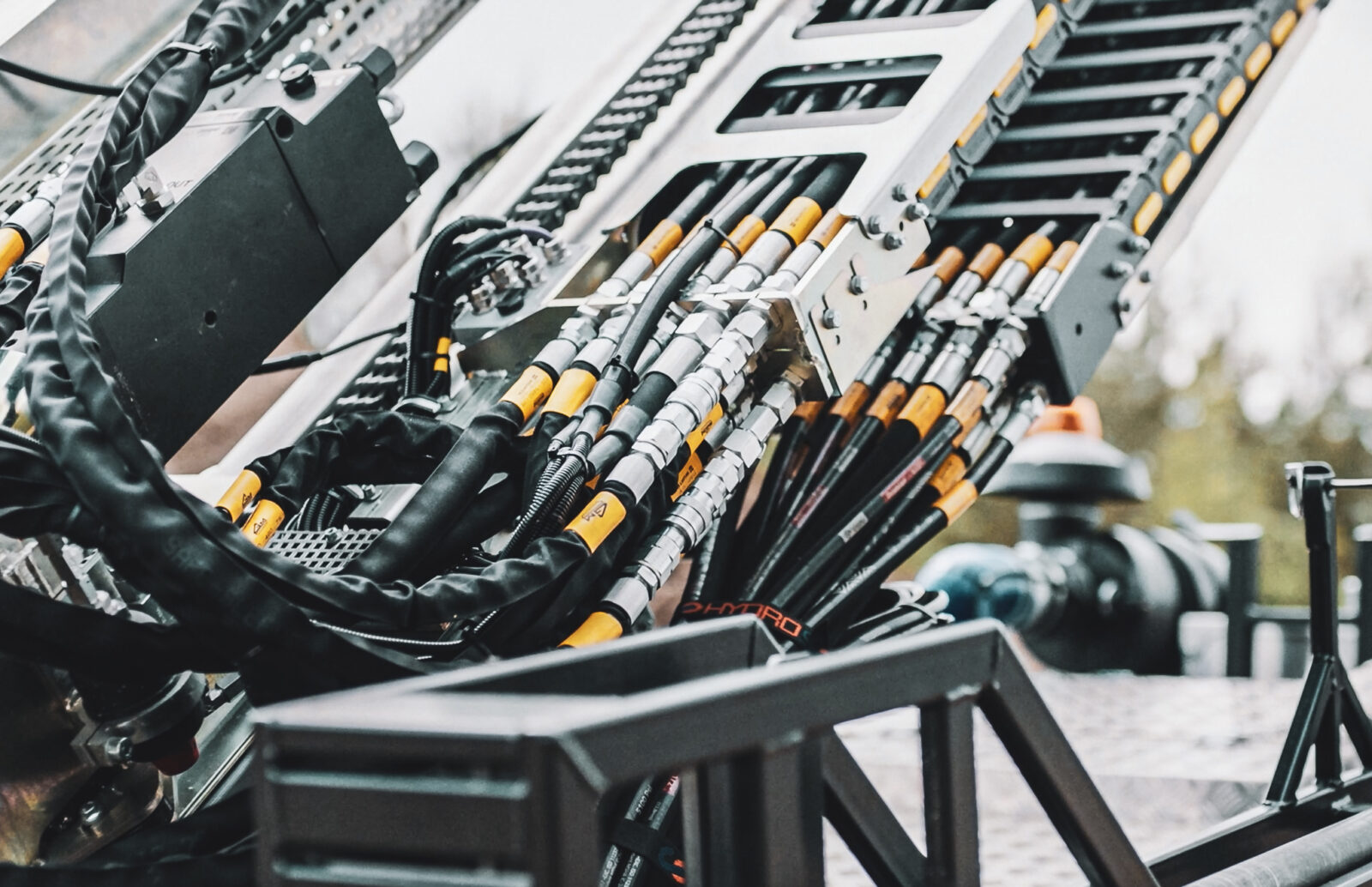
Smarter, more efficient, and environmentally friendly in the future
Geomachine’s Head of Engineering, Juha Sandholm, notes that there hasn’t been much development in the actual investigation methods in recent years, meaning that the rigs’ basic functions will remain relatively similar. “Where there’s still significant room for improvement is in increasing the intelligence of operations and, consequently, their productivity. We started developing our digital products about four years ago, and this development will continue strongly. Thanks to machine learning, our rigs will become even more analytical and predictive. Unnecessary manual workflows will be eliminated, and machine downtime will be minimized. Information will flow in real-time throughout the value chain, improving project turnaround times and profitability.”
The importance of digitalization will also be emphasized in the future because a new generation of drillers is entering the ground investigation industry. “Fresh, younger professionals are continually joining the field. They naturally live in the digital age, and therefore, a high level of intelligence in tools is an expected standard for them, not just a nice addition. We aim to be the most attractive partner in the market for future ground investigation professionals.”
Electrification is another main theme in future product development. “Our rig models have been available as hybrids since 2021. Recently, we also launched the fully electric GMe100 rig, which is expected to meet the increasingly stringent zero-emission requirements in ground investigation. However, customers’ equipment purchases are often strongly influenced by cost, which currently somewhat slows the transition to electrification. We anticipate that the world will evolve in a direction where manufacturing fully electric investigation rigs more affordably becomes possible in the future.”
A satisfied customer is the foundation of everything
Geomachine’s strong foothold in the ground investigation industry is primarily thanks to its customers. “Without satisfied customers, we wouldn’t exist. The ground investigation industry is relatively small, and word-of-mouth travels far. Customers share a lot of information with each other and pass on their experiences about how well our products and services have met their needs.”
According to Juha Sandholm, the main reason for customer satisfaction is that Geomachine understands the primary goal of its customers’ operations. “Each of our customers wants to conduct their business in the most productive, profitable, and smart way possible. They feel that our products and services together form a package that enables this.”
Interested? Contact Geomachine!
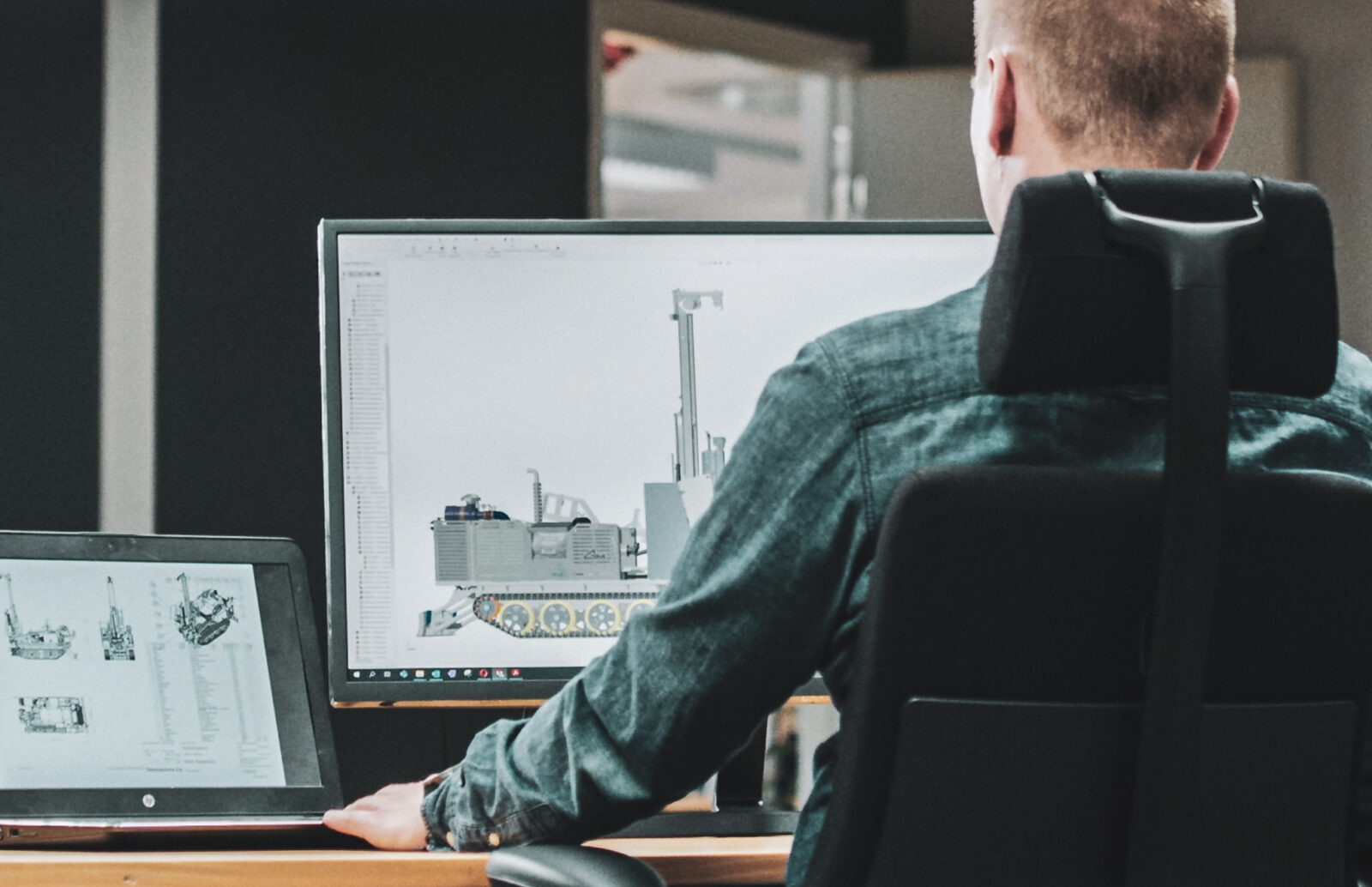
Geomachine
Geomachine’s range of drilling rigs covers all the needs of ground investigation. The fleet currently includes seven versatile rigs designed for various levels of challenging investigations. Each rig is packed with superior technical features, usability, and intelligence.
The smallest rig in Geomachine’s product family is the two-ton GM50, which can be transported on a car trailer. The flagship model is the eight-wheeled GM8 mammoth, capable of traversing even the most difficult terrains with low ground pressure. The core of the machine lineup consists of the GM75, GM85, and GM100, multi-purpose machines highly valued by ground investigation professionals.
All Geomachine drilling rigs are designed and manufactured in Finland. Each rig operates flawlessly in varying soil conditions, challenging terrains, as well as in snowy and harsh weather. The largest geotechnical drilling rigs are also excellently suited for geological investigations when equipped with diamond drilling equipment.
Modularity brings customization
All Geomachine drilling rigs are modular. This ensures that customers always have access to the most suitable tool without expensive customization costs or long delivery times.
In practice, modularity means that the machine base can be equipped with the most suitable boom. The boom range includes several innovative and durable options and can be categorized based on their operating principles into direct feed, chain feed, and dual mast booms. All boom types can also be installed on platforms other than Geomachine’s own, provided they have sufficient hydraulic output. In addition to drilling rigs, they are also suitable for tractors, excavators, and barges.
An essential part of the machines’ modularity is the dual drill table in Geomachine’s booms, which can be equipped with drilling and investigation equipment tailored to the user’s needs.
The power source of the machine can also be selected according to needs. For those prioritizing zero emissions and quiet operation, an electric motor package is the right choice. The diesel engines used in Geomachine’s drilling rigs meet the strictest Stage 5 emission standards and can be operated with renewable diesel.
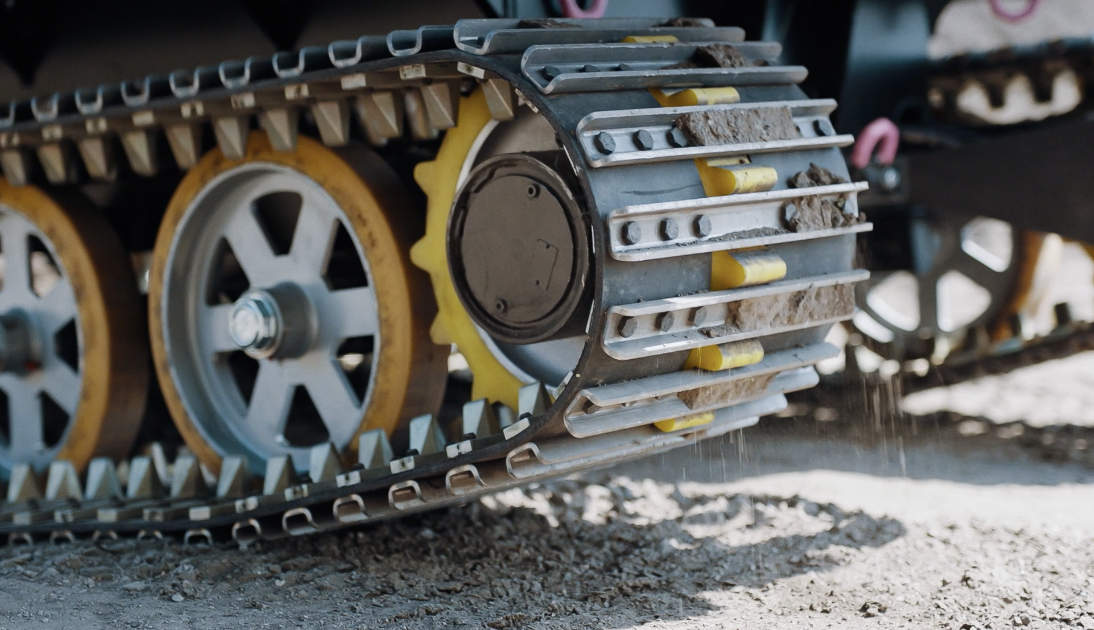
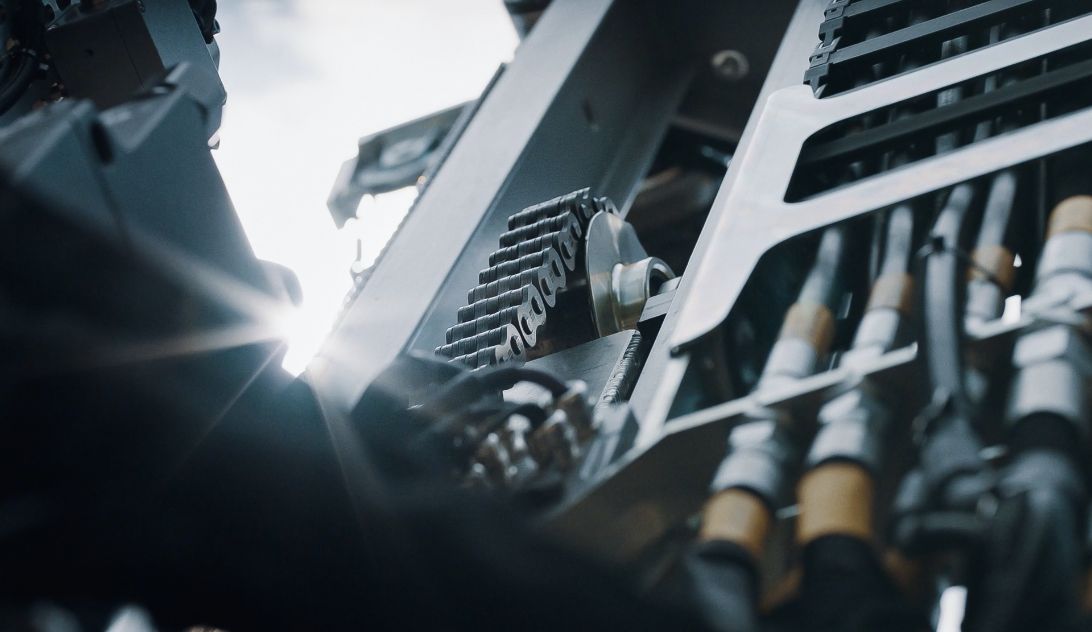
Most valued features
Geomachine’s products are always developed to serve genuine customer needs. Year after year, customers highly value ergonomics, usability, and safety in operations. Therefore, these features are always standard in all Geomachine ground investigation rigs.
A crucial factor affecting work ergonomics is the control panel positioned at the right height. Geomachine’s machine control panels have multi-directional adjustability, allowing the panel to be set at an optimal height even on uneven terrain.
Usability is further enhanced by the fact that all machine models today have very similar operational functions. This means that once the operating principle of a tool is learned, it doesn’t need to be relearned when switching machine models.
Safety features in Geomachine’s machines are also at a high level. Work safety is improved by features such as remote control enabled by the electronic IQAN control system and a separate rod-changing area.
Intelligent working
The ground investigation business follows the same principles as business in general. The ultimate goal is always to operate as qualitatively, productively, and profitably as possible. The investigation process itself is quite standardized today. The most productive detail for the entire process is how qualitatively the investigation data can be captured and how diversely it can be utilized.
Geomachine stands out from its competitors with the intelligence of its products. When all of Geomachine’s digital services are activated, the operator is equipped to efficiently and data-drivenly perform the most critical key tasks of all investigation projects.
Project profitability improves immediately as supply chains become transparent, equipment downtime decreases, equipment management improves, and unnecessary manual work becomes a thing of the past for all members in the project’s value chain. In the long term, project productivity further increases because, thanks to machine learning, investigation work as well as machine maintenance and servicing become more predictive. As the knowledge base on operations and equipment performance diversifies, it helps make the overall operation increasingly profitable.
Uncompromising quality for frontline professionals
Geomachine’s products and services are the right choice for industry operators who are not satisfied with merely completing the work but aim to conduct investigations more intelligently and with higher quality continuously. This means that only top-class tools are acceptable, and they must also be ready to meet future challenges. In the future, those who understand the importance of seamlessness in the project members’ value chain will also succeed.
Geomachine aims to help all its customers excel in their work in the best possible way. This is achieved by taking the ground investigation industry to a new, smarter, and more productive era.
Interested? Contact Geomachine!
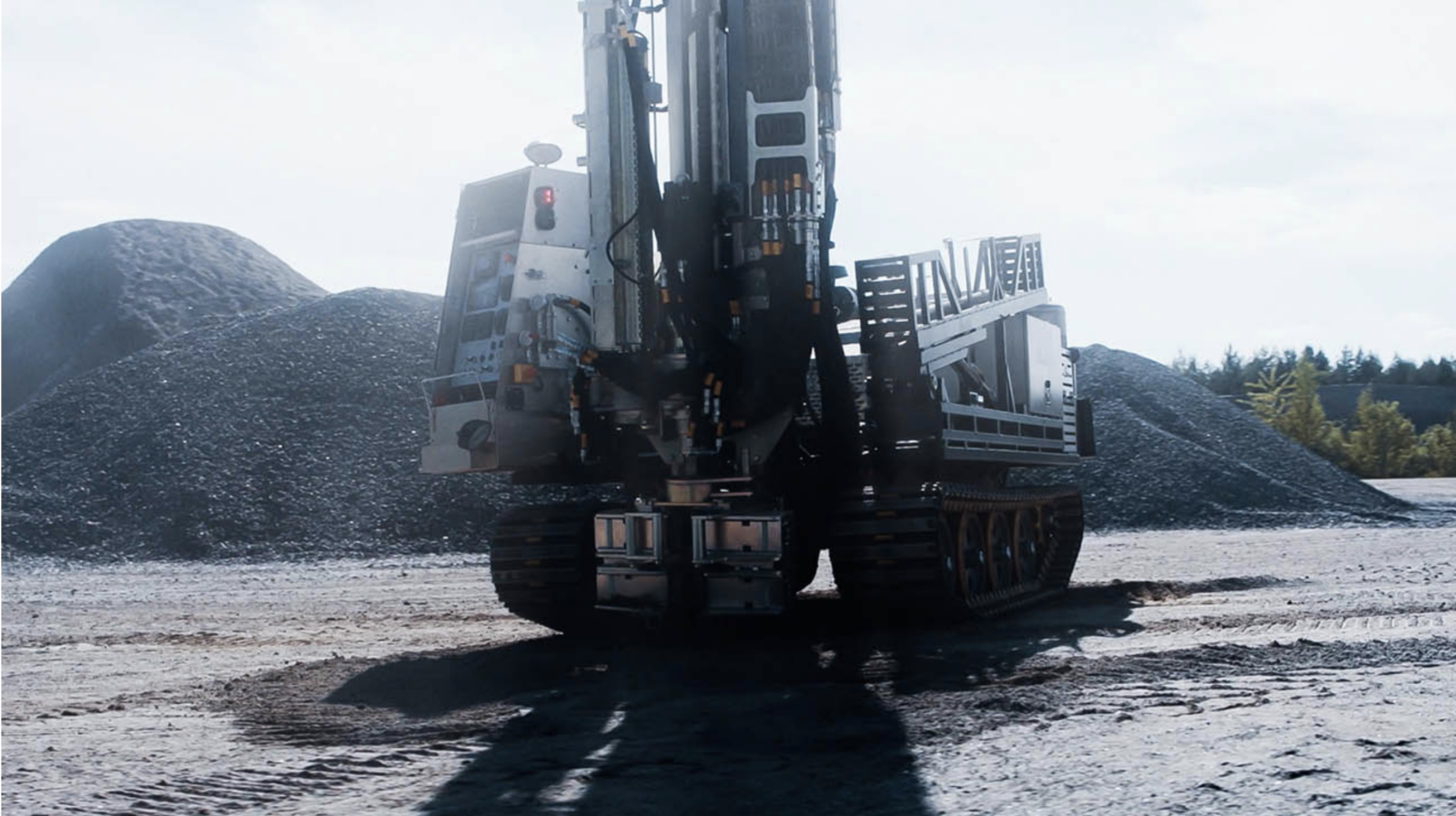
Geomachine
Updating the equipment used in geotechnical investigations becomes relevant for every industry player from time to time. Whether it’s a facelift or a complete renewal, the process is clear and seamless under Geomachine’s guidance.
“The geotechnical investigation industry in the Nordic region is relatively small,” begins Alexander Packalén, Geomachine’s Chief Operating Officer. “It’s a highly specialized field where industry professionals often know each other. That’s why the companies reaching out to us for their equipment needs are frequently already familiar to us.”
Regardless of whether the customer is a long-time partner or a new acquaintance, the discussion always starts by aligning with their needs. “Most of our customers are well-informed and have a clear idea—down to the model—of the machine that best suits their requirements. However, sometimes they only have a general idea of the intended use. In such cases, we explore the situation in more detail, and based on these discussions, we determine the best approach for moving forward with the procurement process.”
The needs of all stakeholders are considered
When a customer first contacts Geomachine about acquiring a machine, their primary concern is usually the cost. “When the time comes to make a purchase, it’s naturally important to understand the budget scale. Once the investment range is clear, the customer can proceed with internal decision-making within their organization.”
The next step involves diving into the details. “We arrange a meeting for a thorough needs assessment. In addition to the decision-maker, we also welcome the machine operators to this discussion. A skilled driller typically has a strong opinion on the features their tool must have. By mapping out these requirements during the design phase, we can ensure a cost-effective production process, avoiding unnecessary modifications later when the machine is already nearing completion.”
Should you upgrade or replace?
According to Alexander Packalén, the goal is always to find the best solution tailored to each customer’s needs. “We provide calculations for our customers to assess whether upgrading their existing equipment or investing in a new machine would be more cost-effective in their specific case. This analysis is especially crucial for companies continuously striving for better profitability.
Sometimes, an upgrade isn’t enough. Companies positioning themselves as industry pioneers and preparing for future changes in their business environment often choose to acquire an entirely new machine. “The geotechnical investigation industry is subject to increasingly stringent regulations, particularly regarding emissions standards. If a company aims to operate in densely built urban areas or participate in public tenders, acquiring a new machine is often the smartest choice. Even if an old machine has been upgraded with smart technology, a new boom, or other modern features, it won’t be competitive if its diesel engine exceeds emission limits.”
The geotechnical investigation sector is constantly evolving. “We closely monitor industry developments and regulatory changes. While no one can predict the future with certainty, we can at least provide well-informed insights based on our expertise.”
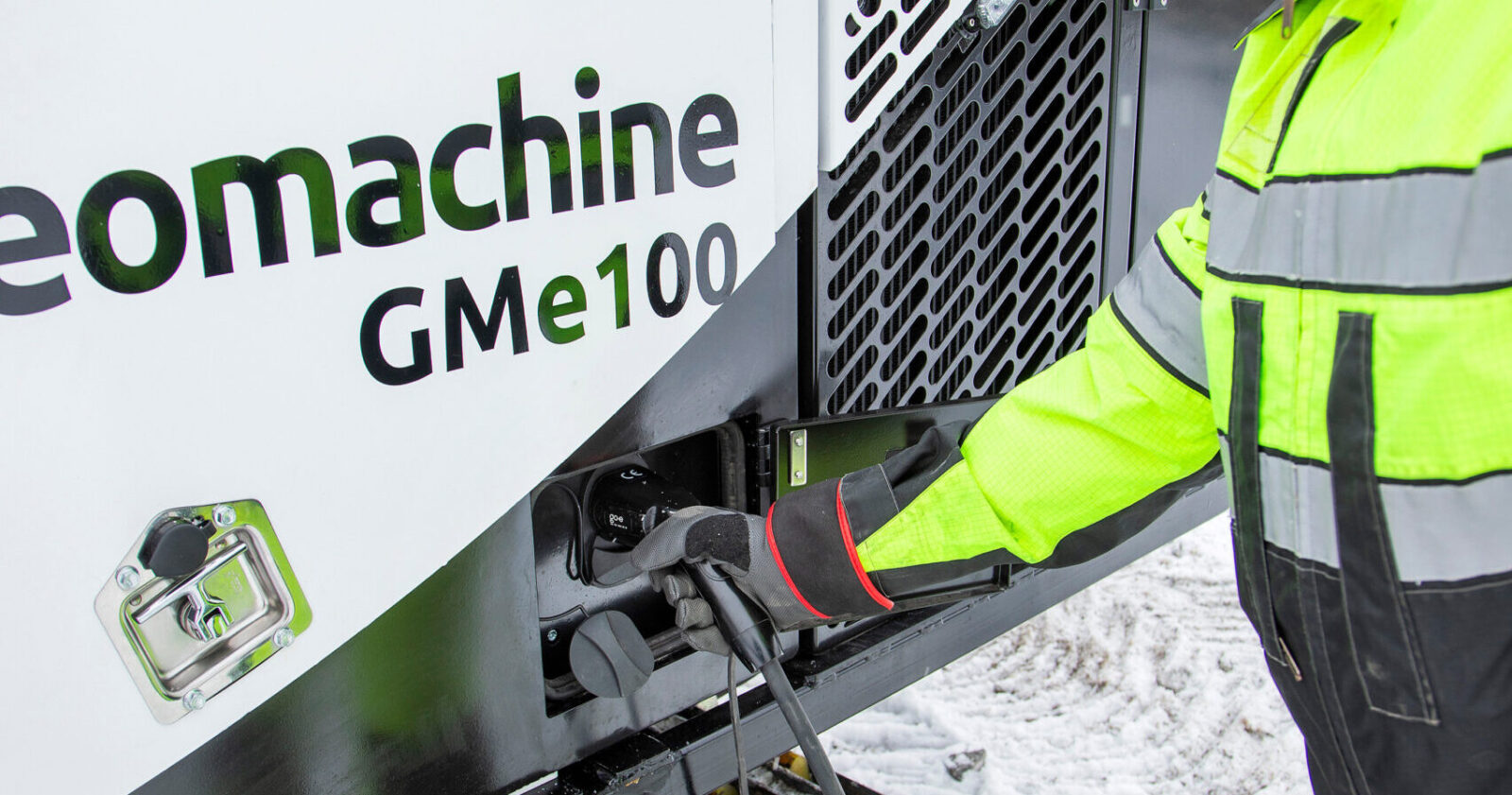
Start the conversation when the need arises
When it’s time to update or renew equipment, Alexander Packalén encourages reaching out to Geomachine without hesitation. “Our Sales Manager, Alex Lindholm, is the right person to contact by phone or email. He initiates the discussions and assembles the Geomachine team to drive the procurement process forward. Depending on the case, machine production times range from a few months to a year. That’s why it’s best to start the conversation as soon as a new purchase is on the horizon—ensuring that the machine is ready for use exactly when needed.”
Regardless of the level of preparedness or prior knowledge about equipment procurement, Geomachine is always a valuable partner. “We have been in the geotechnical investigation field for several decades and have learned to listen closely to our customers’ needs. We guide the procurement process in close collaboration with our clients, from the initial needs assessment to the moment the machine rolls off our production line. Customer satisfaction is always our priority, and we are known for this in the industry. That’s why we are the right partner for professionals who want to work with the best tools on the market and continuously improve their business success.”
Interested? Contact Geomachine!
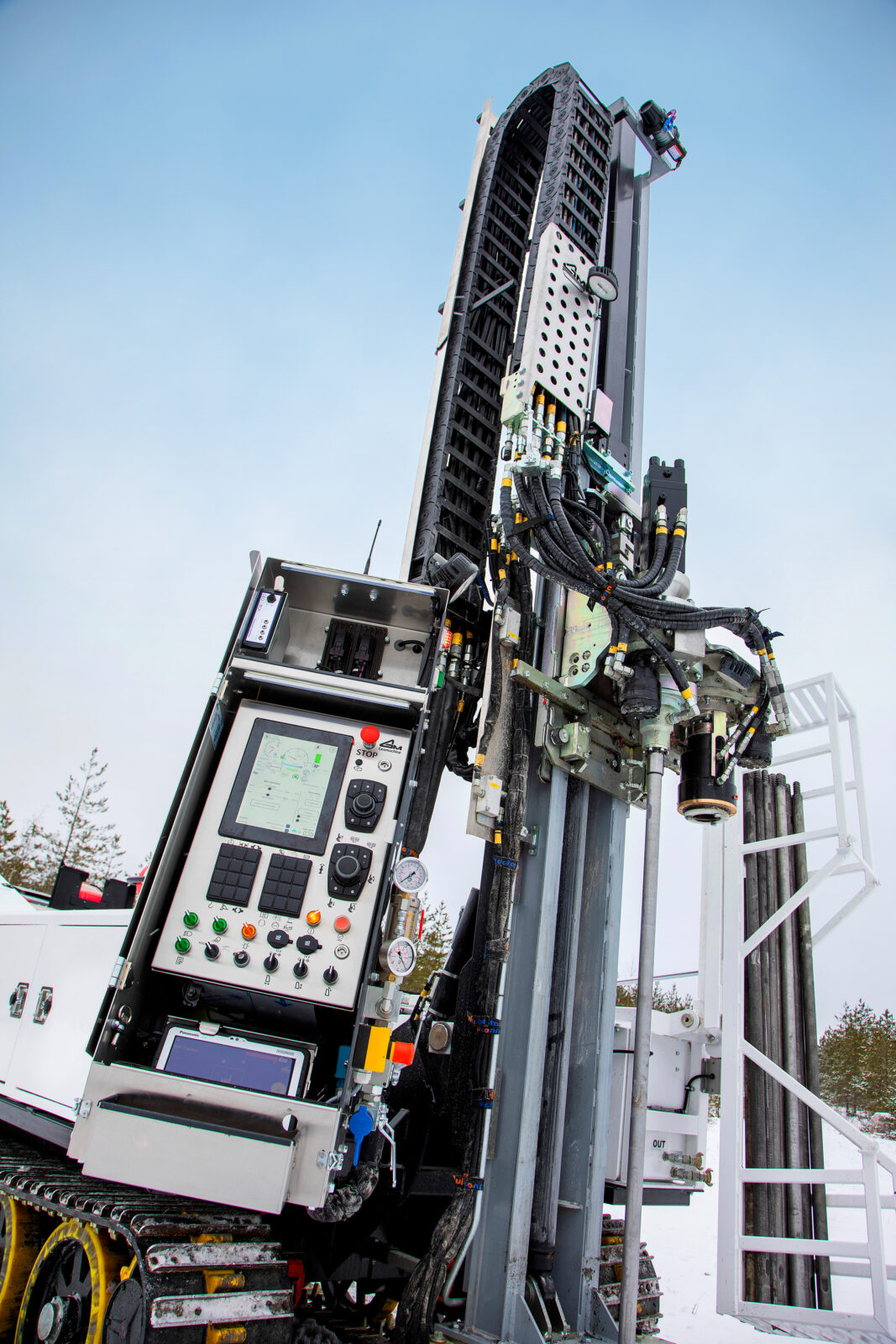
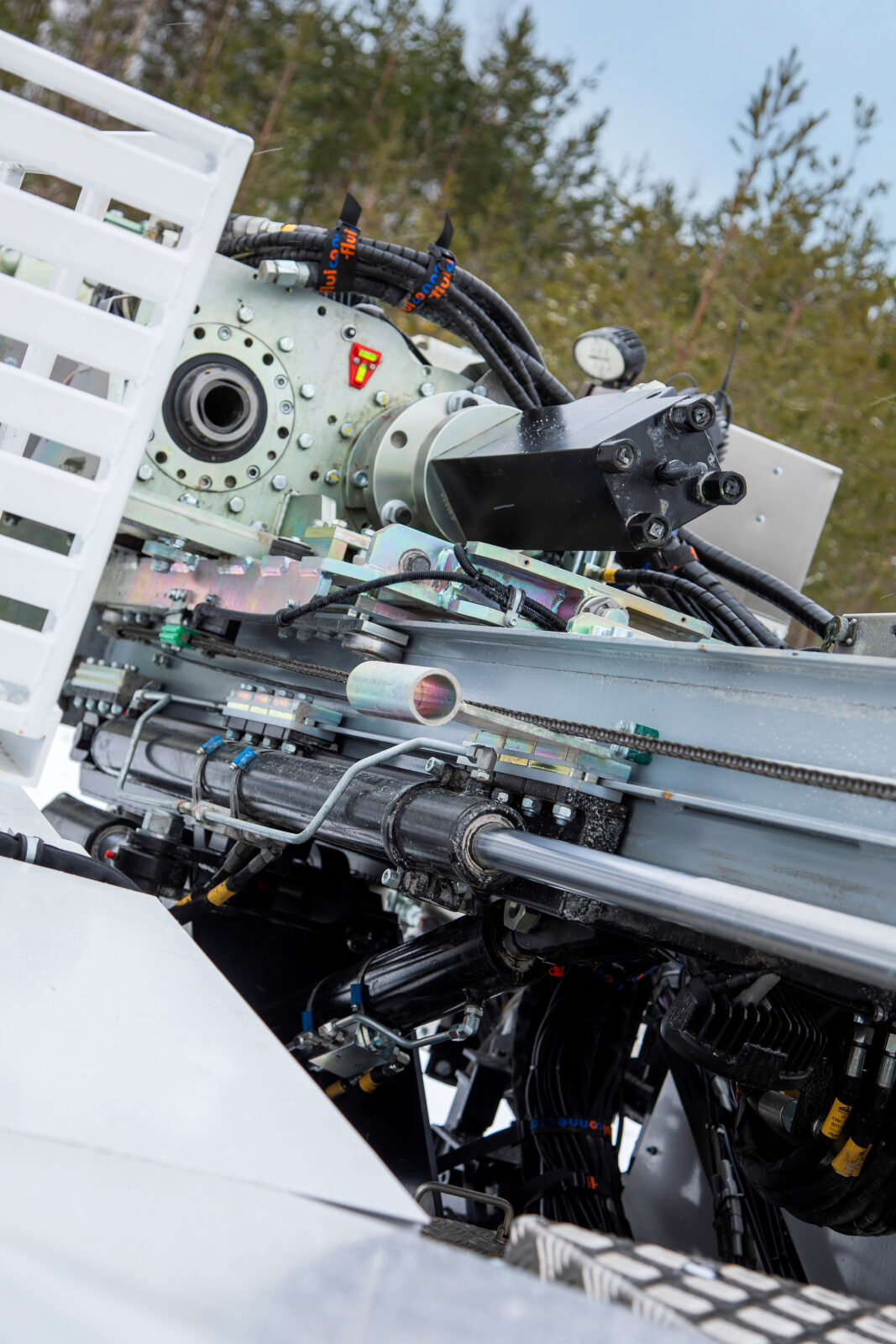
Geomachine
The emission class requirements for machines used in ground investigation are becoming increasingly stringent, and the pressure to work in an environmentally friendly manner is growing. Geomachine’s response to this challenge is the fully electric GMe100 drill rig.
The emissions of diesel-powered work machines have begun to be restricted, especially in densely built urban areas. For example, in Oslo, their use is no longer permitted. Efforts to reduce emissions are also evident in public tenders organized by cities, where emission class requirements are stricter than before, even if emissions are not yet legally regulated in the tendering area.
In the world of ground investigation, just like in technological development in general today, the trend is towards electrification. New product innovations are continually being introduced under this theme. Geomachine is also actively developing products to meet changes and expectations in its operating environment. The latest example of this is the fully electric GMe100 ground investigation rig.
New product innovations are created in collaboration with customers
Geomachine’s Chief Technology Officer, Vesa-Matti Salminen, explains that the GMe100 ground investigation rig was developed based on market needs. “When the requirement for zero-emission operation was enforced in Oslo, Norway, our distributor operating there contacted us. Following discussions and market research, we began developing an electrically powered drill rig in 2023.”
The GMe100 drill rig was built on the existing diesel-powered GM100 platform. It retains the same functionalities and usability as its diesel-powered twin. The machine’s operations remain hydraulic, but power generation in this rig is fully electric.
The length of Geomachine’s product development process varies depending on whether it involves a completely new product innovation or the further development of an existing product. The journey of the GMe100 drill rig from the drawing board to machine delivery took about two years.
When developing a completely new innovation, the product development process does not end at the time of delivery. “Although the machine is ready at delivery, close collaboration with the customer continues in the support phase,” says Geomachine’s Head of Engineering, Juha Sandholm. “We collect customer feedback on the real-world functionality of the machine to make further refinements if needed. Customers who invest in new innovations are industry pioneers. They understand that a finished product can still be refined after deployment and are keen to participate in this stage of product development.”
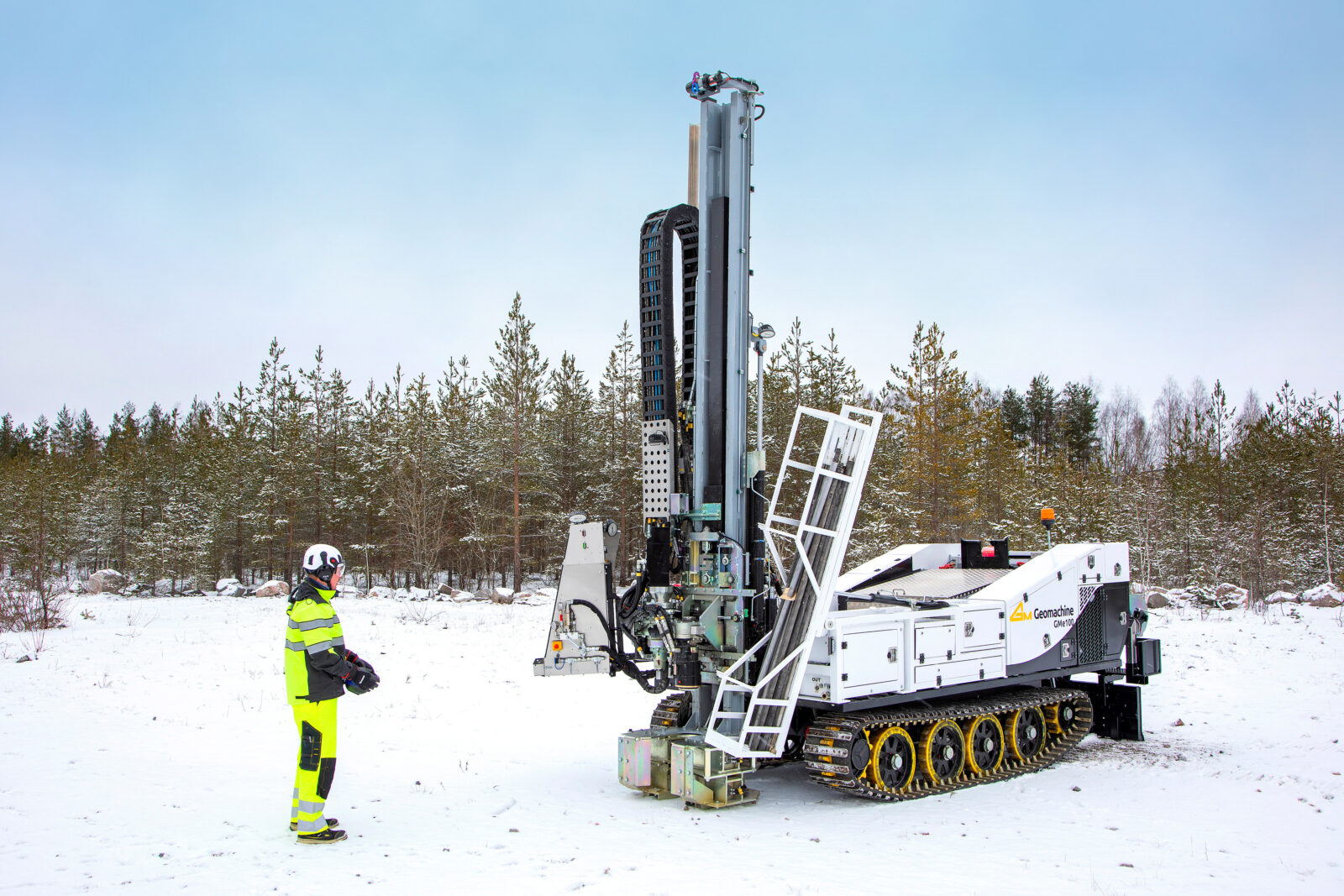
An electrically powered option for ground investigation
The GMe100 ground investigation rig is suitable for all the same investigation methods as its diesel-powered twin. These include dynamic probing, weight sounding, percussion drilling, casing drilling, spt and dspt testing, cpt and cpt-u testing, and pore pressure drilling. Additionally, it is suitable for groundwater pipe installation and sampling from both hard and soft grounds.
The GMe100 rig is powered by a battery-operated electric motor. Compressed air is supplied via an electric compressor. “During product development, we realized that using an electric compressor improves the efficiency of the fully electric machine, allowing for longer operation on a single battery charge,” says Juha Sandholm. “With a dedicated motor for the compressor, we were able to reduce the size of the machine’s main powertrain motor.”
The battery life of the rig varies depending on the investigation method used, and its capacity can be increased with an additional battery pack if necessary.
Like Geomachine’s equipment in general, the GMe100 is highly intelligent. It features an IQAN control system and GMTracker data logging software. A Cloud version of the logging software is also available, enhancing workflow efficiency, machine maintenance, and project management by connecting all stakeholders in the project’s value chain in real time.
Usability was another key focus in designing the GMe100 rig. This machine includes more storage space than before for the operator’s tools and essential liquids.
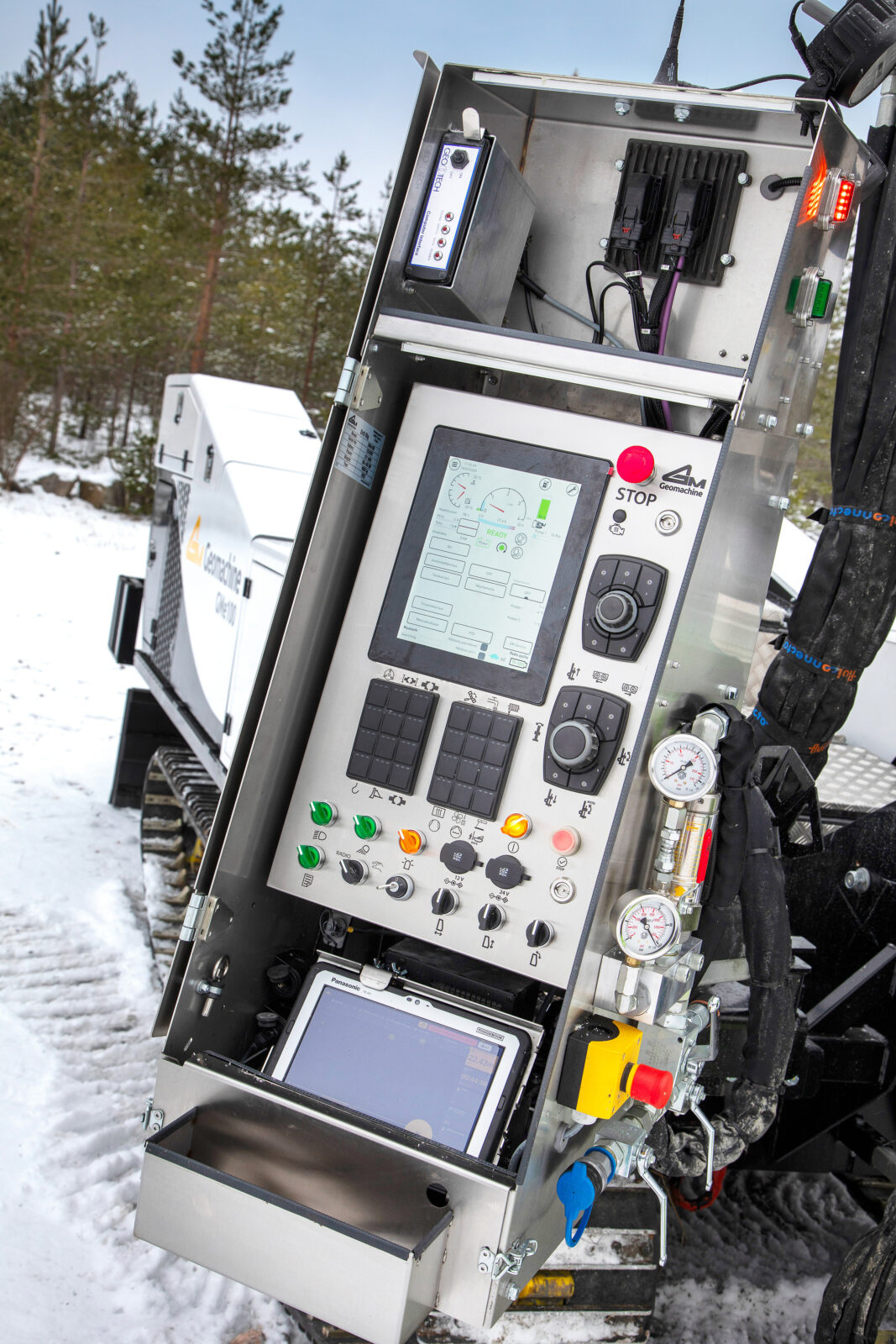
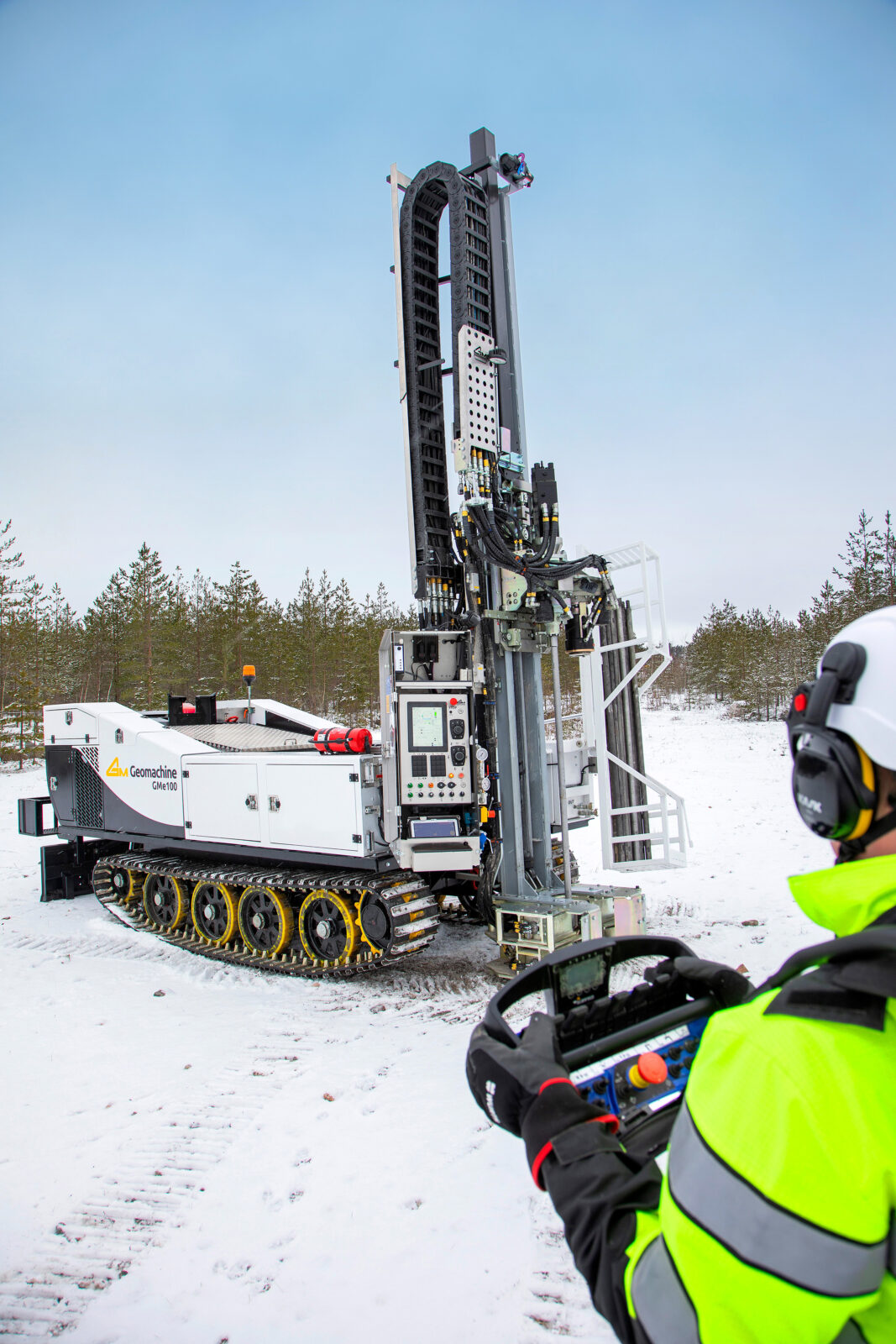
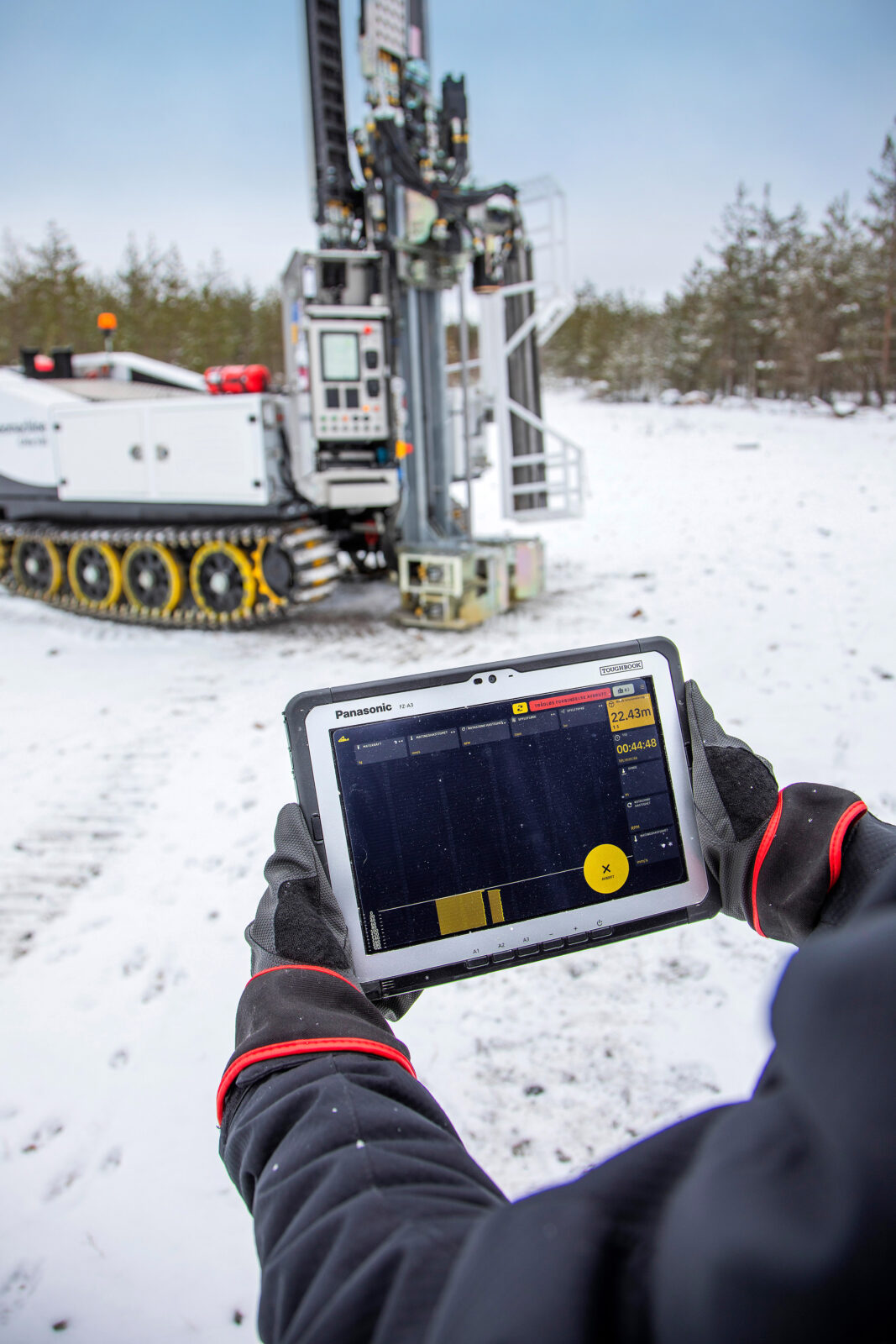
Key principles of product development
Vesa-Matti Salminen explains that Geomachine adheres to specific requirements in product development, ensuring that every product meets the highest standards. “We strive for quality in everything we do; our machines must be durable and perform at their best. Our products must also be easy to use. That’s why we aim for minimal differences in usability between models. Workplace safety is another crucial factor, and we continuously develop new solutions to enhance it.”
Geomachine’s customers share a commitment to working with the most reliable and user-friendly machines on the market. But that’s not all. “Our customers also highly value efficient and high-quality customer support. It’s important for them to get assistance from a familiar service representative who knows the machine’s history and features inside out.”
The GMe100 is a product innovation that Geomachine is extremely proud of. “Drawing on our extensive experience, we have successfully built a machine that enables ground investigation with exceptional quality and efficiency—now also in a more environmentally friendly and emission-free manner, meeting today’s demands.”
Interested? Contact Geomachine!
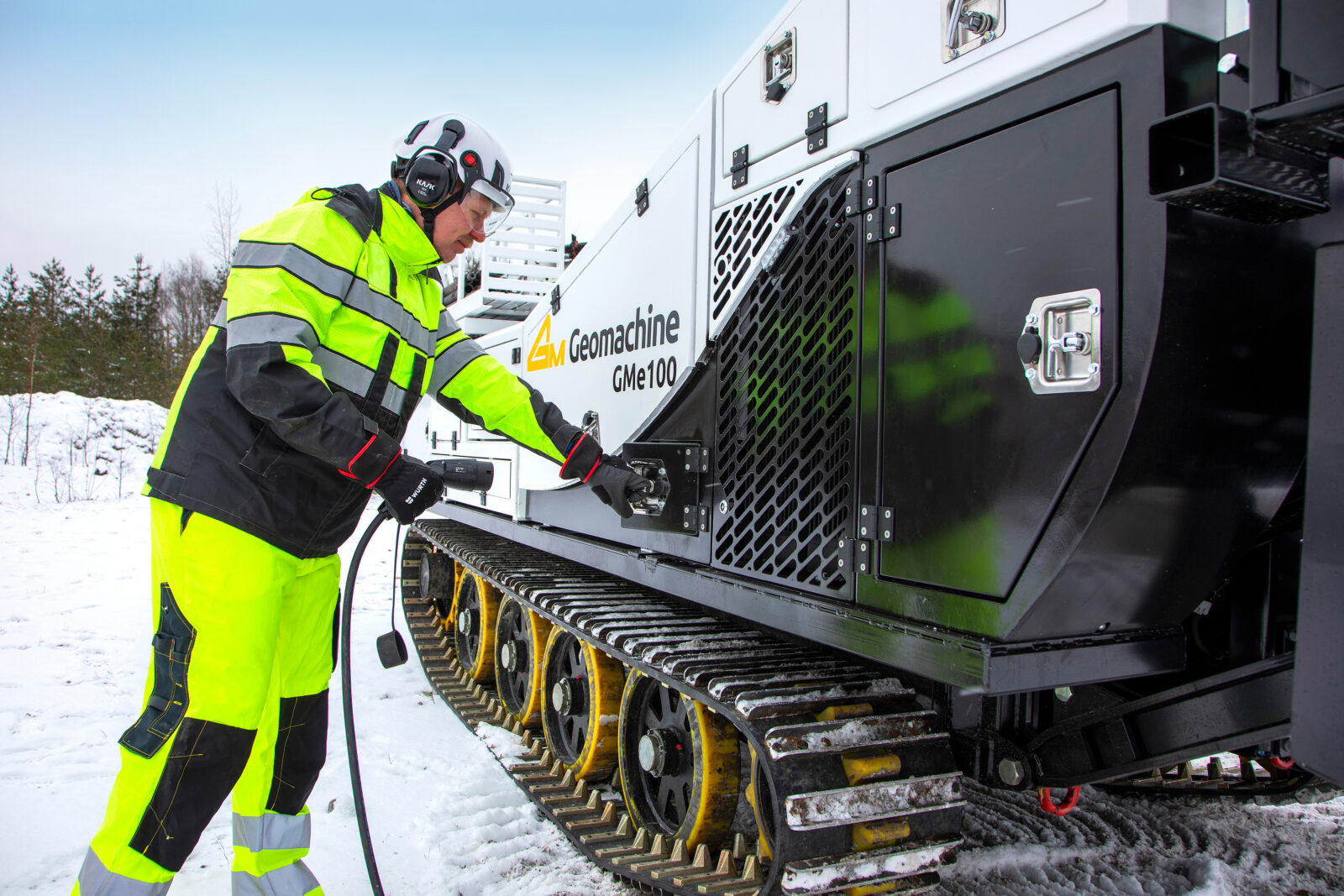
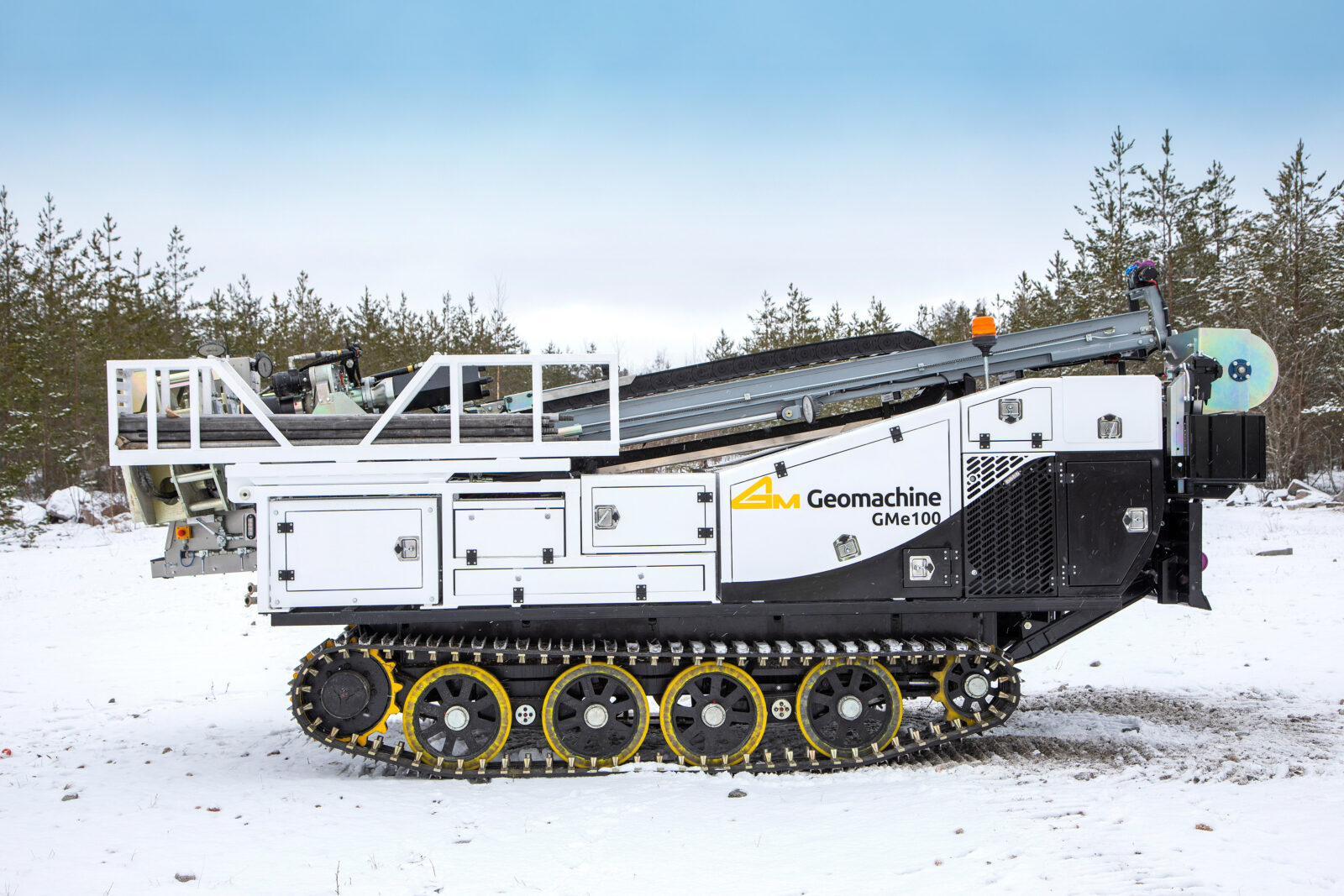
GMTracker
Information about the geotechnical field equipment used in ground investigations must be documented in the investigation report. Thanks to a new feature in the GMTracker data-logger, data on equipment is now transferred to the investigation report without manual effort.
The equipment required for ground investigations include, for example, CPT cones, vane shear devices, and sampling tools. These details must also be recorded in the work report for the investigation.
The new feature added to the GMTracker data-logger enables the maintenance and automatic adding of equipment data in work reports. The equipment registry contains information on the device’s identifier, model, type, and calibration, depending on the device. GMTracker is the only data-logger on the market whose registry also includes sampling tubes. Thanks to this new feature, equipment data is always accurately recorded in reports.
In the future, equipment management will also be integrated into the Cloud version of the GMTracker data-logger. Once data can be stored in the cloud, all stakeholders requiring equipment information will gain a comprehensive view of the devices used by the investigation company, their age, condition, and calibration status.
Managing specialized equipment through GMTrackerCloud will not only enhance reporting but also streamline the execution of investigation projects. It will help project management allocate sampling tasks to specific investigation vehicles without needing to transfer equipment from other sites. In the future, calibration values for equipment will also be manageable via GMTrackerCloud.
Interested? Take contact!
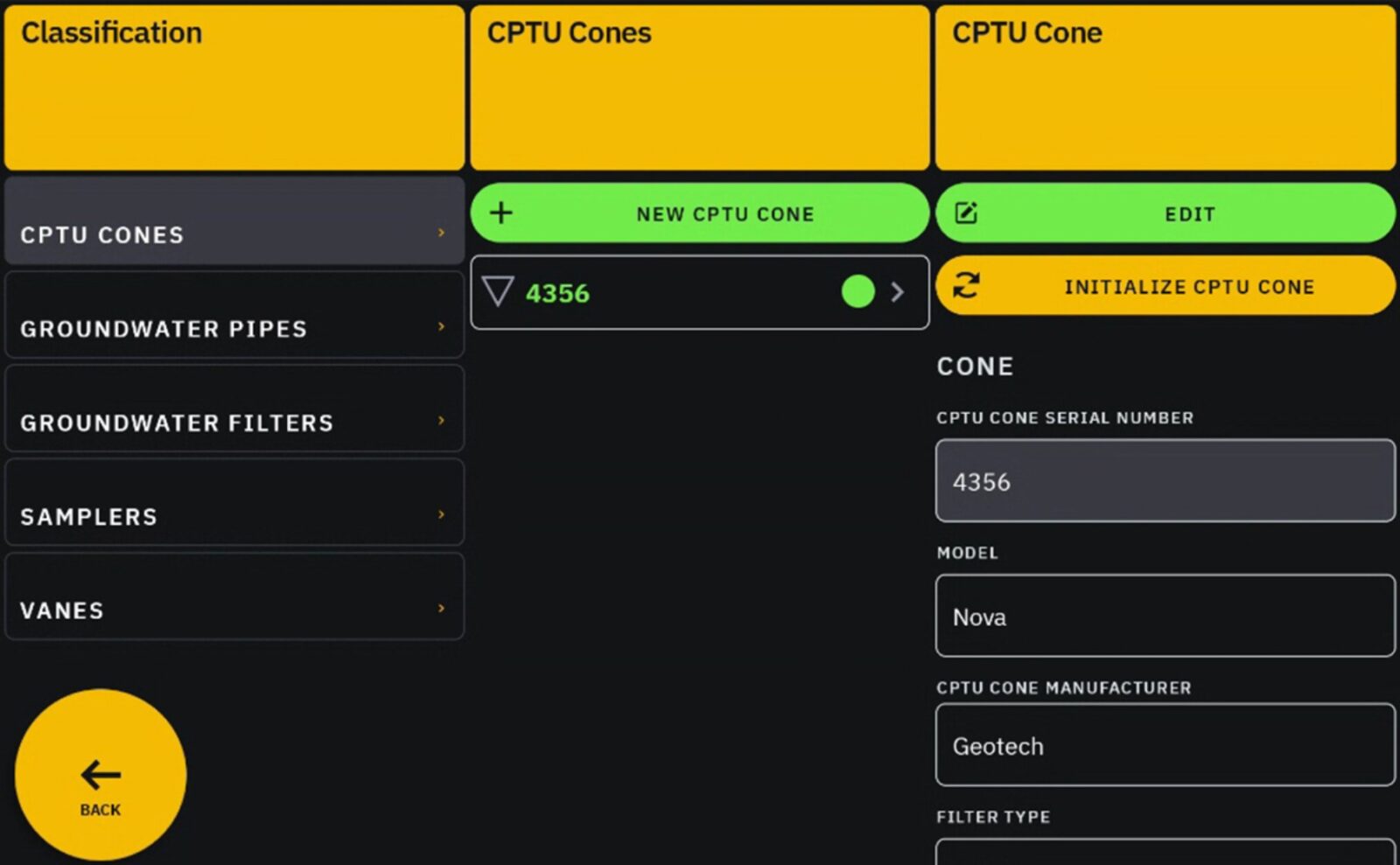
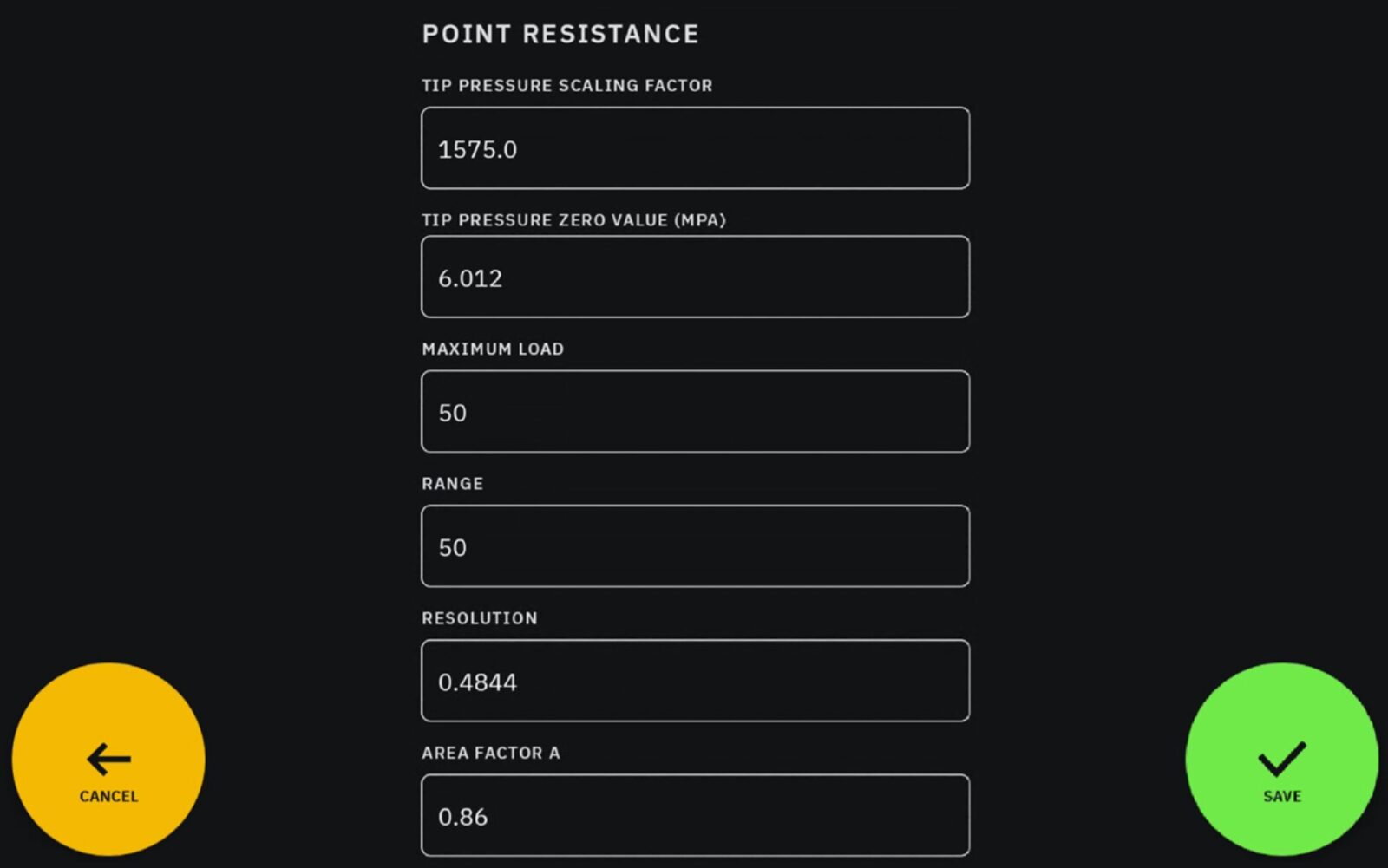
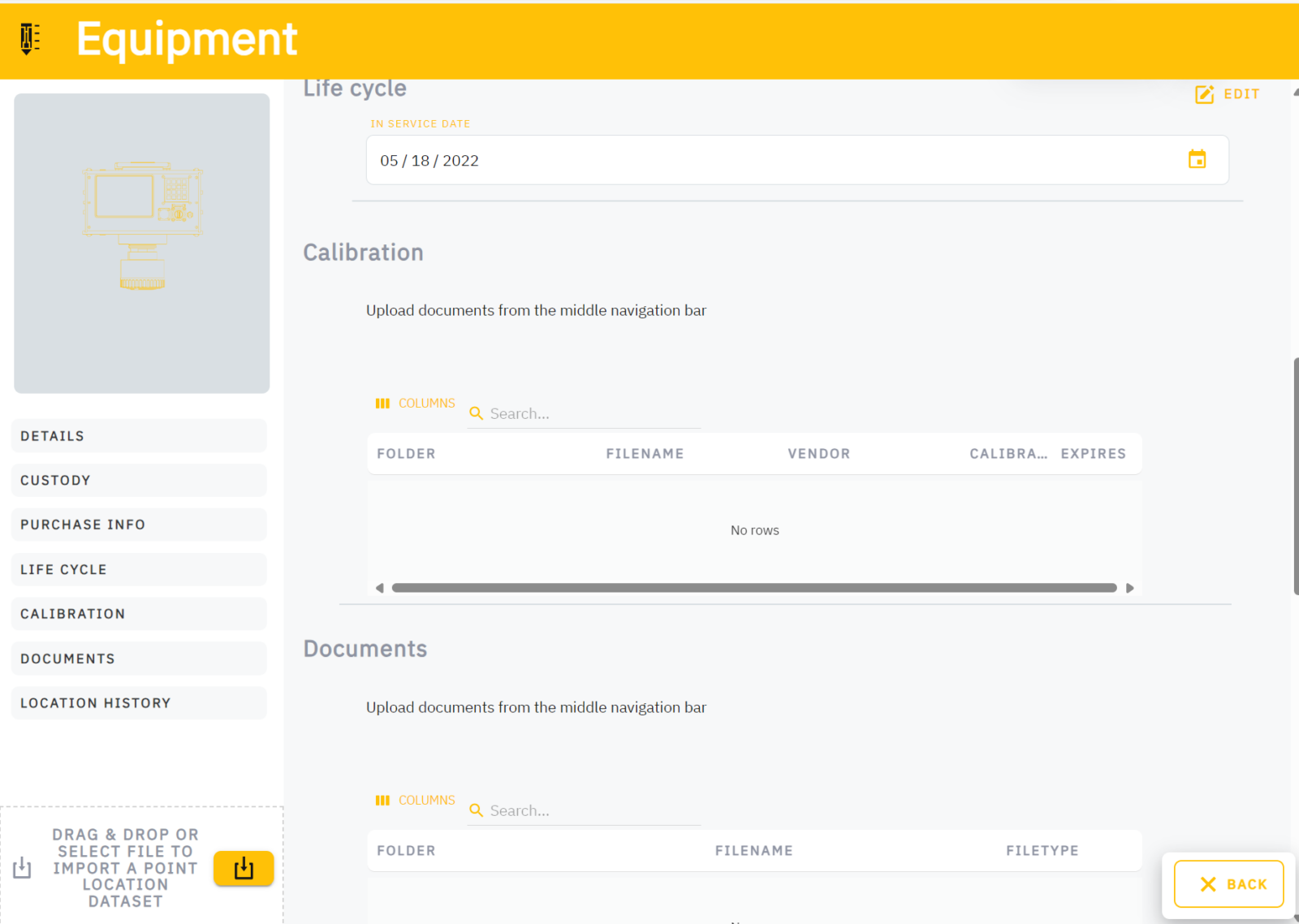